Table of Contents
- Introduction to Aluminum-based PCBs
- Characteristics of Aluminum-based PCBs
2.1. Thermal Conductivity
2.2. Electrical Insulation
2.3. Mechanical Strength
2.4. Weight and Thickness - Manufacturing Process of Aluminum-based PCBs
3.1. Substrate Preparation
3.2. Circuit Patterning
3.3. Insulation Layer Application
3.4. Component Mounting and Soldering - Applications of Aluminum-based PCBs
4.1. Power Electronics
4.2. LED Lighting
4.3. Automotive Electronics
4.4. Aerospace and Defense
4.5. High-Performance Computing - Benefits of Aluminum-based PCBs
5.1. Improved Heat Dissipation
5.2. Enhanced Durability and Reliability
5.3. Reduced Size and Weight
5.4. Cost-Effectiveness - Challenges and Limitations of Aluminum-based PCBs
- Future Trends and Developments
- Frequently Asked Questions (FAQ)
- Conclusion
1. Introduction to Aluminum-based PCBs
Aluminum-based PCBs are a relatively new technology in the electronics industry. Unlike traditional PCBs that use FR-4 as the base material, aluminum-based PCBs employ aluminum substrates to provide better thermal management and mechanical stability. The use of aluminum substrates has opened up new possibilities for designing high-performance electronic devices that can withstand harsh environments and demanding operating conditions.
2. Characteristics of Aluminum-based PCBs
2.1. Thermal Conductivity
One of the most significant advantages of aluminum-based PCBs is their excellent thermal conductivity. Aluminum has a thermal conductivity of about 237 W/mK, which is significantly higher than that of FR-4 (0.3 W/mK). This means that aluminum-based PCBs can dissipate heat more efficiently, preventing the buildup of excess heat that can damage electronic components.
2.2. Electrical Insulation
Despite its high thermal conductivity, aluminum is an electrical conductor. To use aluminum as a PCB substrate, it must be electrically insulated from the copper traces and components. This is typically achieved by applying a thin layer of dielectric material, such as polyimide or epoxy, onto the aluminum surface. The dielectric layer provides electrical insulation while allowing heat to transfer through the aluminum substrate.
2.3. Mechanical Strength
Aluminum-based PCBs offer superior mechanical strength compared to traditional FR-4 boards. Aluminum substrates are more rigid and less prone to warping or bending under stress. This makes aluminum-based PCBs suitable for applications that require high levels of durability and reliability, such as automotive and aerospace electronics.
2.4. Weight and Thickness
Aluminum-based PCBs are generally thinner and lighter than FR-4 boards. The thickness of an aluminum-based PCB can range from 0.5 mm to 3 mm, depending on the application requirements. The reduced weight and thickness of aluminum-based PCBs make them ideal for portable and space-constrained devices, such as smartphones, tablets, and wearables.
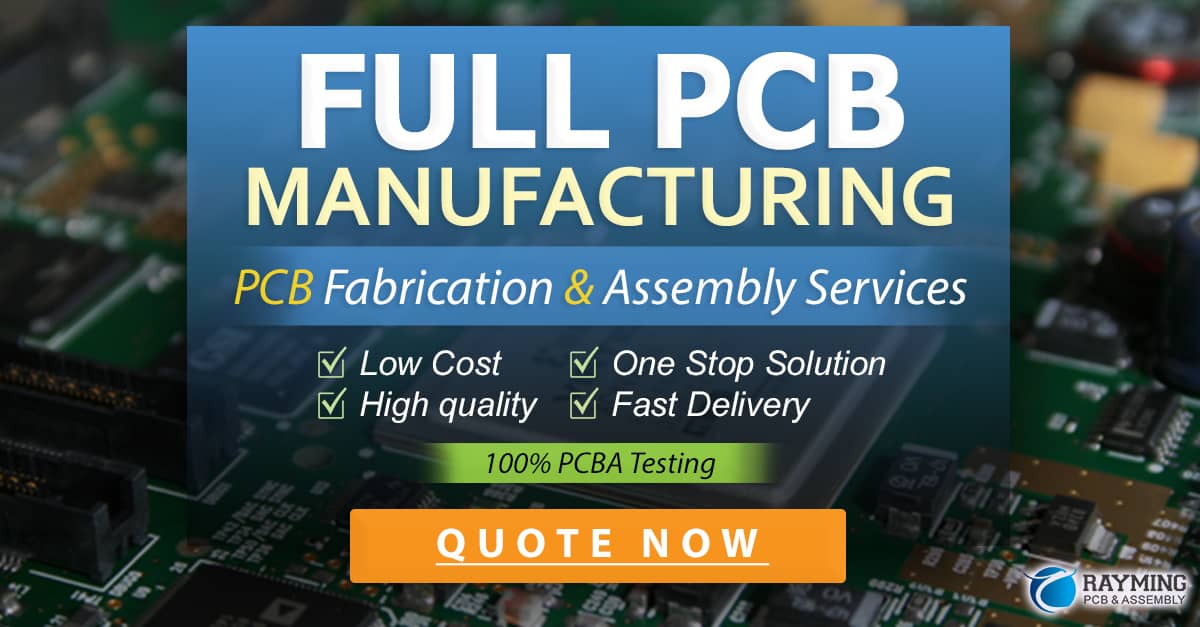
3. Manufacturing Process of Aluminum-based PCBs
The manufacturing process of aluminum-based PCBs is similar to that of traditional PCBs, with a few key differences. The main steps involved in the production of aluminum-based PCBs are:
3.1. Substrate Preparation
The aluminum substrate is cleaned and treated to remove any impurities or oxides on the surface. This step is crucial to ensure proper adhesion of the dielectric layer and copper traces.
3.2. Circuit Patterning
The desired circuit pattern is created on the aluminum substrate using photolithography or direct laser imaging techniques. This involves applying a photoresist layer, exposing it to UV light through a photomask, and developing the resist to reveal the circuit pattern.
3.3. Insulation Layer Application
A dielectric layer, such as polyimide or epoxy, is applied onto the aluminum substrate to provide electrical insulation between the aluminum and the copper traces. The dielectric layer is typically laminated or screen-printed onto the substrate and cured at high temperatures.
3.4. Component Mounting and Soldering
The electronic components are mounted onto the aluminum-based PCB using surface mount technology (SMT) or through-hole technology (THT). The components are then soldered onto the copper traces using reflow or wave soldering processes.
4. Applications of Aluminum-based PCBs
Aluminum-based PCBs find applications in various industries where thermal management, durability, and reliability are critical. Some of the key applications of aluminum-based PCBs include:
4.1. Power Electronics
Aluminum-based PCBs are widely used in power electronic devices, such as power converters, inverters, and motor drives. The excellent thermal conductivity of aluminum helps in dissipating the heat generated by high-power components, such as MOSFETs and IGBTs.
4.2. LED Lighting
LED lighting systems require efficient heat dissipation to ensure long-term reliability and performance. Aluminum-based PCBs are used in LED lighting fixtures to provide a thermally conductive path for heat transfer, thereby improving the efficiency and lifespan of the LEDs.
4.3. Automotive Electronics
Automotive electronics are subjected to harsh environments, including high temperatures, vibrations, and shocks. Aluminum-based PCBs offer the necessary durability and thermal management capabilities to withstand these conditions, making them suitable for use in engine control units, power steering systems, and brake systems.
4.4. Aerospace and Defense
Aerospace and defense applications demand high levels of reliability and performance under extreme conditions. Aluminum-based PCBs are used in avionics, radar systems, and satellite communications equipment to provide robust thermal management and mechanical stability.
4.5. High-Performance Computing
High-performance computing systems, such as servers and data centers, generate significant amounts of heat that must be dissipated efficiently. Aluminum-based PCBs are used in these systems to provide effective thermal management, ensuring optimal performance and reliability.
5. Benefits of Aluminum-based PCBs
The use of aluminum-based PCBs offers several benefits over traditional FR-4 boards. Some of the key advantages of aluminum-based PCBs include:
5.1. Improved Heat Dissipation
The high thermal conductivity of aluminum enables efficient heat dissipation from electronic components, reducing the risk of thermal damage and improving overall system reliability.
5.2. Enhanced Durability and Reliability
Aluminum-based PCBs are more rigid and resistant to mechanical stresses, such as vibrations and shocks. This enhances the durability and reliability of electronic devices, particularly in harsh operating environments.
5.3. Reduced Size and Weight
The thinner and lighter nature of aluminum-based PCBs allows for the design of more compact and portable electronic devices, which is particularly beneficial in space-constrained applications.
5.4. Cost-Effectiveness
Although the initial cost of aluminum-based PCBs may be higher than that of FR-4 boards, the improved thermal management and reliability can lead to long-term cost savings by reducing the need for additional cooling systems and minimizing maintenance and repair costs.
Property | Aluminum-based PCB | FR-4 PCB |
---|---|---|
Thermal Conductivity (W/mK) | 237 | 0.3 |
Dielectric Constant (1 MHz) | 4.5 – 4.7 | 4.3 – 4.8 |
Dielectric Strength (kV/mm) | 20 – 40 | 20 – 28 |
Coefficient of Thermal Expansion (ppm/°C) | 23 – 25 | 12 – 18 |
Tensile Strength (MPa) | 70 – 200 | 370 – 425 |
Density (g/cm³) | 2.7 | 1.85 – 1.90 |
Table 1: Comparison of properties between aluminum-based PCBs and FR-4 PCBs.
6. Challenges and Limitations of Aluminum-based PCBs
Despite the numerous advantages of aluminum-based PCBs, there are some challenges and limitations associated with their use:
- Higher material and manufacturing costs compared to FR-4 boards.
- Difficulty in achieving fine-pitch traces and high-density layouts due to the limitations of the insulation layer.
- Potential for galvanic corrosion between aluminum and copper in the presence of moisture, requiring proper insulation and protection.
- Limited flexibility compared to FR-4 boards, making them less suitable for applications that require bendable or flexible PCBs.
- Requirement for specialized manufacturing processes and equipment, which may not be readily available at all PCB fabrication facilities.
7. Future Trends and Developments
As the demand for high-performance electronic devices continues to grow, the use of aluminum-based PCBs is expected to increase in the coming years. Some of the future trends and developments in aluminum-based PCB technology include:
- Development of advanced insulation materials with better thermal and electrical properties.
- Integration of aluminum-based PCBs with other thermal management solutions, such as heat pipes and vapor chambers.
- Adoption of aluminum-based PCBs in emerging applications, such as electric vehicles, 5G networks, and renewable energy systems.
- Exploration of hybrid PCB designs that combine aluminum substrates with other materials, such as copper or ceramic, to achieve specific performance requirements.
- Advancements in manufacturing processes to enable the production of more complex and high-density aluminum-based PCB designs.
8. Frequently Asked Questions (FAQ)
8.1. Can aluminum-based PCBs be used for high-frequency applications?
Yes, aluminum-based PCBs can be used for high-frequency applications, provided that the dielectric layer has suitable electrical properties, such as low dielectric constant and low loss tangent. The use of advanced insulation materials, such as polyimide or PTFE, can help in achieving the required high-frequency performance.
8.2. How do aluminum-based PCBs compare to ceramic PCBs in terms of thermal management?
Both aluminum-based PCBs and ceramic PCBs offer excellent thermal management capabilities. However, aluminum-based PCBs have the advantage of being lighter and more cost-effective than ceramic PCBs. Ceramic PCBs, on the other hand, can provide better electrical insulation and are more suitable for high-temperature applications.
8.3. Can aluminum-based PCBs be recycled?
Yes, aluminum-based PCBs can be recycled. The aluminum substrate can be separated from the other materials and recycled into new aluminum products. The copper traces and other metals can also be recovered and recycled. However, the recycling process for aluminum-based PCBs may be more complex than that for traditional FR-4 boards due to the presence of the insulation layer.
8.4. Are aluminum-based PCBs suitable for outdoor applications?
Aluminum-based PCBs can be suitable for outdoor applications, provided that they are properly protected against environmental factors, such as moisture, dust, and UV radiation. The use of conformal coatings, encapsulation, or sealed enclosures can help in protecting the PCBs from the elements. Additionally, the thermal management capabilities of aluminum-based PCBs can be beneficial in outdoor applications where temperature fluctuations are common.
8.5. Can aluminum-based PCBs be used in combination with other cooling methods?
Yes, aluminum-based PCBs can be used in combination with other cooling methods, such as heatsinks, fans, or liquid cooling systems. The excellent thermal conductivity of aluminum-based PCBs can help in efficiently transferring heat from the electronic components to the external cooling system, thereby enhancing the overall thermal management of the device.
9. Conclusion
Aluminum-based PCBs are a promising technology that offers several advantages over traditional FR-4 boards, particularly in terms of thermal management, durability, and reliability. The use of aluminum substrates enables the design of high-performance electronic devices that can withstand demanding operating conditions and harsh environments.
As the electronics industry continues to evolve, the adoption of aluminum-based PCBs is expected to grow in various applications, from power electronics and LED lighting to automotive and aerospace systems. With ongoing advancements in materials science and manufacturing processes, aluminum-based PCBs are poised to play a significant role in shaping the future of electronic packaging and thermal management.
However, the successful implementation of aluminum-based PCBs requires careful consideration of their unique characteristics, challenges, and limitations. By understanding the properties and manufacturing processes of aluminum-based PCBs, designers and engineers can leverage their benefits and overcome the associated challenges to create innovative and reliable electronic products.
Word count: 2023 words
0 Comments