Introduction to Heat Dissipation in PCBs
Printed Circuit Boards (PCBs) are essential components in modern electronic devices, serving as the foundation for mounting and interconnecting various electronic components. As electronic systems become more complex and powerful, managing heat dissipation becomes a critical factor in ensuring optimal performance, reliability, and longevity of PCBs. Excessive heat generation can lead to component failure, reduced efficiency, and even complete system breakdown.
In this comprehensive article, we will explore the fundamental concepts of heat dissipation in PCBs, discuss the importance of effective thermal management, and delve into various techniques and strategies employed to mitigate heat-related issues. By understanding and implementing these heat dissipation techniques, designers and engineers can create robust and efficient PCBs that can withstand the thermal challenges posed by modern electronic systems.
The Importance of Heat Dissipation in PCBs
Heat dissipation is a crucial aspect of PCB design for several reasons:
-
Component Reliability: Excessive heat can cause components to operate beyond their specified temperature ranges, leading to reduced performance, accelerated aging, and eventual failure.
-
System Stability: High temperatures can affect the stability of electronic systems, causing signal integrity issues, clock skew, and other problems that can compromise the overall functionality of the device.
-
Product Lifespan: Proper heat dissipation helps to extend the lifespan of electronic products by preventing premature component failure and maintaining optimal operating conditions.
-
User Experience: Overheating can lead to uncomfortable user experiences, such as hot surfaces on handheld devices or noisy cooling fans in larger systems.
-
Compliance with Standards: Many industries have specific thermal management standards and regulations that must be met to ensure product safety and reliability.
Factors Affecting Heat Generation in PCBs
Several factors contribute to heat generation in PCBs:
-
Power Density: As electronic components become smaller and more powerful, the power density on PCBs increases, leading to higher heat generation per unit area.
-
Component Selection: Different components have varying power dissipation characteristics. High-power components, such as processors, power regulators, and RF modules, generate more heat compared to low-power components.
-
PCB Layout: The placement and routing of components on a PCB can significantly impact heat distribution. Improper layout can lead to hot spots and uneven heat dissipation.
-
Environmental Factors: The operating environment, including ambient temperature, humidity, and airflow, can influence the heat dissipation capabilities of a PCB.
Heat Dissipation Techniques for PCBs
To effectively manage heat in PCBs, various techniques can be employed. These techniques can be categorized into passive and active methods.
Passive Heat Dissipation Techniques
Passive heat dissipation techniques rely on natural heat transfer mechanisms, such as conduction, convection, and radiation, without the need for external power input.
Thermal Vias
Thermal vias are small, plated holes drilled through the PCB to transfer heat from one layer to another. They provide a low-resistance path for heat to flow from hot components to other layers or to the opposite side of the board, where it can be dissipated more effectively.
Thermal Via Parameter | Typical Value |
---|---|
Drill Diameter | 0.2 – 0.5 mm |
Copper Plating Thickness | 25 – 50 µm |
Via Pitch | 1.0 – 2.0 mm |
Copper Pours and Planes
Copper pours and planes are large areas of copper on the PCB that act as heat spreaders. By providing a large surface area for heat dissipation, copper pours and planes help to distribute heat more evenly across the board, reducing hot spots and improving overall thermal performance.
Copper Pour/Plane Parameter | Typical Value |
---|---|
Copper Thickness | 1 – 2 oz |
Copper Coverage | 50 – 100% |
Thermal Interface Materials (TIMs)
Thermal Interface Materials (TIMs) are used to enhance heat transfer between components and heat sinks or other cooling solutions. TIMs fill the air gaps and irregularities between mating surfaces, improving thermal conductivity and reducing thermal resistance.
TIM Type | Thermal Conductivity (W/mK) |
---|---|
Thermal Grease | 0.5 – 10 |
Thermal Pads | 1 – 15 |
Phase Change Materials | 1 – 10 |
Component Placement and Orientation
Strategic component placement and orientation can significantly improve heat dissipation. By placing high-power components away from each other and orienting them to maximize heat flow towards the edges of the board or cooling solutions, designers can minimize thermal interactions and promote better heat dissipation.
Active Heat Dissipation Techniques
Active heat dissipation techniques involve the use of external power-driven devices to enhance heat removal from the PCB.
Heatsinks
Heatsinks are metal structures designed to absorb and dissipate heat from components. They work by increasing the surface area available for heat dissipation and promoting convective heat transfer to the surrounding air. Heatsinks come in various shapes and sizes, including extruded, stamped, and forged types, and can be passive or actively cooled with fans.
Heatsink Material | Thermal Conductivity (W/mK) |
---|---|
Aluminum | 150 – 200 |
Copper | 350 – 400 |
Graphite | 100 – 1500 |
Fans and Blowers
Fans and blowers are used to actively move air across the PCB and its components, enhancing convective heat transfer. They can be mounted directly on the PCB or integrated into the enclosure of the electronic device. The choice between fans and blowers depends on factors such as the required airflow, static pressure, and noise constraints.
Liquid Cooling
In high-power applications, liquid cooling can be used to effectively remove heat from the PCB. Liquid cooling systems typically involve a closed loop of coolant that absorbs heat from the components and transfers it to a radiator or heat exchanger. This technique offers superior heat dissipation capabilities compared to air cooling, but it comes with added complexity and cost.
Peltier Coolers (Thermoelectric Coolers)
Peltier coolers, also known as thermoelectric coolers (TECs), are solid-state devices that use the Peltier effect to create a temperature difference between two surfaces. By applying a DC current, heat is absorbed from one surface and dissipated on the other, effectively cooling the target component. Peltier coolers are compact and have no moving parts, making them suitable for applications where reliability and precise temperature control are essential.
Thermal Management in PCB Design Process
Incorporating heat dissipation techniques into the PCB design process is crucial for achieving optimal thermal performance. The following steps outline a typical thermal management workflow:
-
Thermal Analysis: Perform thermal simulations and analyses to predict the temperature distribution on the PCB and identify potential hot spots. This helps in making informed decisions about component placement, copper pour distribution, and cooling solution requirements.
-
Component Selection: Choose components with suitable power dissipation characteristics and thermal ratings. Consider factors such as package type, thermal resistance, and maximum junction temperature.
-
PCB Layout Optimization: Optimize the PCB layout to promote heat dissipation. This includes strategic component placement, proper copper pour distribution, and the use of thermal vias where necessary.
-
Cooling Solution Selection: Based on the thermal analysis results and system requirements, select appropriate cooling solutions such as heatsinks, fans, or liquid cooling. Consider factors such as thermal performance, size constraints, and cost.
-
Prototyping and Testing: Fabricate prototype PCBs and conduct thermal testing to validate the design. Use thermal imaging cameras, thermocouples, or other temperature measurement techniques to assess the actual thermal performance of the PCB.
-
Iterative Refinement: Based on the testing results, refine the PCB design, component selection, and cooling solutions as needed to achieve the desired thermal performance.
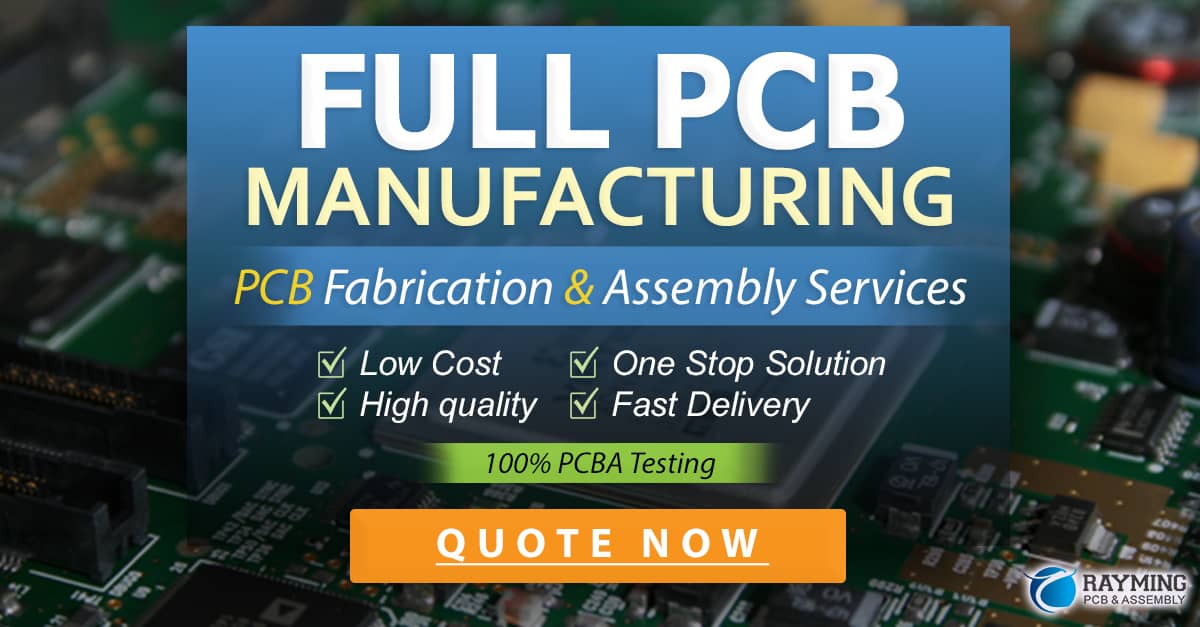
Thermal Management Standards and Guidelines
Several industry standards and guidelines provide recommendations and best practices for thermal management in PCBs. Some notable standards include:
- IPC-2221: Generic Standard on Printed Board Design
- IPC-7351: Generic Requirements for Surface Mount Design and Land Pattern Standard
- JESD51-1: Integrated Circuit Thermal Measurement Method – Electrical Test Method (Single Semiconductor Device)
- JESD51-2: Integrated Circuits Thermal Test Method Environment Conditions – Natural Convection (Still Air)
- JESD51-7: High Effective Thermal Conductivity Test Board for Leaded Surface Mount Packages
Adhering to these standards ensures that PCBs are designed with proper thermal considerations and can meet the required performance and reliability criteria.
Frequently Asked Questions (FAQ)
-
Q: What is the difference between passive and active heat dissipation techniques?
A: Passive heat dissipation techniques rely on natural heat transfer mechanisms, such as conduction, convection, and radiation, without the need for external power input. Examples include thermal vias, copper pours, and heatsinks. Active heat dissipation techniques involve the use of external power-driven devices, such as fans, blowers, and liquid cooling systems, to enhance heat removal from the PCB. -
Q: How do I determine the appropriate heatsink size for my PCB?
A: The appropriate heatsink size depends on factors such as the power dissipation of the components, the maximum allowable junction temperature, and the ambient temperature. Thermal simulations and calculations can help determine the required heatsink thermal resistance and size. Heatsink manufacturers often provide online tools and selection guides to assist in choosing the right heatsink for a given application. -
Q: Can I use thermal vias on multi-layer PCBs?
A: Yes, thermal vias can be used on multi-layer PCBs to transfer heat from inner layers to outer layers or to the opposite side of the board. By strategically placing thermal vias near high-power components and connecting them to copper pours or planes on other layers, heat can be effectively dissipated through the PCB stack. -
Q: What are the advantages of using liquid cooling in PCBs?
A: Liquid cooling offers several advantages over air cooling, including higher heat dissipation capacity, better temperature uniformity, and the ability to cool high-power components more effectively. Liquid cooling systems can also be more compact and quieter compared to air cooling solutions, making them suitable for applications with strict size and noise constraints. -
Q: How can I verify the thermal performance of my PCB design?
A: There are several methods to verify the thermal performance of a PCB design. Thermal simulations using specialized software can provide insights into the temperature distribution and identify potential hot spots. Physical testing using thermal imaging cameras, thermocouples, or other temperature measurement techniques can validate the actual thermal performance of the manufactured PCB. It is important to conduct both simulations and physical testing to ensure the design meets the required thermal specifications.
Conclusion
Heat dissipation is a critical aspect of PCB design that directly impacts the performance, reliability, and longevity of electronic systems. By understanding the principles of heat generation and employing various heat dissipation techniques, designers and engineers can create PCBs that can effectively manage thermal challenges.
Passive techniques such as thermal vias, copper pours, and heatsinks, along with active solutions like fans, blowers, and liquid cooling, provide a wide range of options to suit different applications and requirements. Incorporating thermal management considerations into the PCB design process, from component selection to layout optimization and cooling solution integration, is essential for achieving optimal results.
Adhering to industry standards and guidelines, performing thorough thermal analyses, and conducting rigorous testing and validation are key steps in ensuring the thermal performance of PCBs meets the desired targets.
By mastering the art of heat dissipation in PCBs, designers and engineers can push the boundaries of electronic system performance, enabling the development of more advanced, efficient, and reliable products across various industries.
0 Comments