Introduction
Launching new products successfully requires creating high-quality prototypes to test concepts and refine designs. However, building prototypes can be time-consuming and expensive without the right approach. Turnkey prototype assembly provides a streamlined solution for creating prototypes efficiently.
With turnkey assembly, companies can outsource the prototype build process to an experienced partner. This allows product developers to focus their efforts on design and validation while leveraging the specialized skills and equipment of an assembly partner. The result is faster prototyping, lower costs, and decreased development risk.
In this guide, we will explore the key benefits of turnkey prototype assembly and provide tips for partnering with the right assembly provider. Whether you are seeking faster iteration, lower costs, or reduced risk, turnkey assembly can accelerate your path to launching innovative new products.
Benefits of Turnkey Prototype Assembly
Turnkey prototype assembly provides the following advantages compared to in-house build processes:
Faster Build Speed
Specialized assembly partners have dedicated tools, jigs, and expertise for rapid prototyping across a wide range of product categories. By leveraging their scale and experience, turnkey assembly can shrink prototyping lead times from weeks to days.
Flexible Scaling
In-house prototype shops have limited capacity thresholds. But turnkey assemblers can easily scale up or down to match variable demand. This on-demand flexibility prevents backlogs during peak prototype activity.
Specialized Expertise
Experienced prototype assemblers have expertise across multiple production methods including CNC machining, 3D printing, sheet metal fabrication, and more. This avoids the need to invest in diverse in-house capabilities.
Economy of Scale
Dedicated prototype assemblers purchase materials in bulk and reuse tools/jigs across customers. This results in lower per-unit costs compared to small batch in-house builds.
Reduced Risk
Relying on an established assembly partner reduces the risk of mistakes, rework, and delays compared to managing the process internally. Their expertise improves quality and adherence to specifications.
Choosing the Right Prototype Assembly Partner
To maximize the benefits of turnkey assembly, it is critical to select the right partner. Key factors to evaluate include:
Range of Capabilities
Look for partners with expertise across different prototyping methods including machining, 3D printing, sheet metal, molding, and casting. This enables flexible sourcing for each project.
Material Experience
Choose assemblers with experience working with the materials specific to your prototypes including metals, plastics, elastomers, composites, and more. Material-specific process knowledge is critical.
Quality Systems
Rigorous quality control and documentation ensures accurate execution according to the design specifications. Ask about testing, inspection, and certification processes.
Prototyping Experience
Prefer partners with a track record building prototypes for complex, high-precision products similar to yours. Related experience translates to faster problem solving.
Engineering Collaboration
The ability to collaborate with in-house engineers and designers enables optimization of the assembly process. Evaluate technical interfaces and design review procedures.
Scalability
Look for capacity to scale up or down flexibly so lead times stay short even with variable demand. Understanding capacity thresholds ensures reliable delivery.
Security
For products involving intellectual property risks, prioritize assemblers with strong controls and proven processes for security. NDAs and IT controls are key.
By carefully selecting partners against these criteria, companies can maximize quality, speed, flexibility, and security through turnkey prototyping.
The Prototype Assembly Process
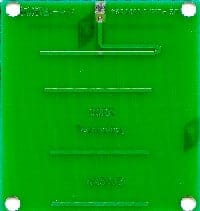
Executing a turnkey prototype build involves close coordination through the following typical process:
Step 1 – Design Review
The assembly partner reviews prototype designs to identify potential areas for DFM optimization and select the best assembly methods. Early collaboration enables design tweaks to improve manufacturability.
Step 2 – Sourcing
Based on the bill of materials, the assembler sources necessary parts and materials from trusted suppliers and inserts. They leverage bulk purchasing power to minimize per-unit cost.
Step 3 – Program Generation
For operations involving CNC machining or other automated equipment, assembly programming is completed based on 3D models and drawings. Jigs and fixtures may also be created.
Step 4 – Assembly
The prototype is assembled by trained technicians following strict protocols. Inspection and testing validates execution according to specifications.
Step 5 – Design Review
If needed, additional design reviews are conducted to resolve any assembly issues and implement improvements for the next iteration.
Step 6 – Delivery
The finished prototype is packaged along with documentation of materials, quality reports, and any other accompanying information.
Close coordination throughout this process is critical to achieving high quality and accelerating turnaround times. Regular design reviews and progress updates help keep assembly on track.
Table: Comparison of In-House vs. Turnkey Prototype Assembly
Factor | In-House | Turnkey Assembly |
---|---|---|
Build Speed | Slow, depends on capacity | Fast, dedicated resources |
Cost | High per-unit cost | Low due to economy of scale |
Quality | Variable, higher risk | Consistent based on process expertise |
Overhead | Tools, equipment, hiring, training | Minimal, outsourced activities |
Scalability | Limited by capacity | Flexible, scales on-demand |
Iteration Speed | Slower process adjustment | Faster learning curve |
Key Takeaways
Turnkey prototype assembly provides an efficient path to high-quality prototypes. By leveraging specialized partners, companies can:
- Accelerate build speeds through dedicated expertise and capacity
- Reduce per-unit costs through economy of scale
- Improve quality with mature processes and quality control
- Minimize overhead of tools, equipment, and training
- Scale on demand through flexible capacity
- Iterate faster through collaboration and continuous improvement
Carefully selecting capable assembly partners enables a faster and lower-risk path to driving new product innovation and getting to market quickly.
Frequently Asked Questions
Q: When does it make sense to use turnkey vs. in-house assembly?
A: Turnkey assembly is preferable when prototyping complexity, quality requirements, or capacity constraints exceed in-house capabilities. It enables focus on design rather than production logistics.
Q: How can we protect our intellectual property with an outside assembler?
A: Require NDAs, limit data sharing only to what is essential, and work only with assemblers that have strong controls around data security. On-site assembly can also limit risk.
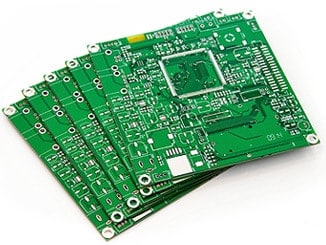
Q: What if our prototypes involve new materials or processes?
A: Look for assemblers experienced with process development and material trials. The best can co-develop new methods tailored to your needs.
Q: How much design freedom do we have to change if we use turnkey?
A: There is flexibility to modify designs via the build-test-learn cycle as long as assembler feedback is incorporated. Design for manufacturability.
Q: Can turnkey scale all the way from low to high volume production?
A: Turnkey partners are optimized for prototyping and low rate initial production. For scaled production, a full contract manufacturer is recommended.
0 Comments