Understand the Power Supply Design and Specifications
Before beginning PCB assembly, it’s essential to thoroughly review and understand the power supply design files and specifications:
- Schematic diagrams
- PCB layout files
- Bill of Materials (BOM)
- Assembly drawings
- Mechanical models
Carefully analyze these documents to get familiar with the power supply circuit topology, key components, physical layout, and mechanical form factor. Identify any special requirements, such as:
- High voltage or current handling areas
- Thermal management features like heatsinks or fans
- Safety critical isolation regions
- Grounding and shielding structures
- Connectors and cabling interfaces
Having a solid grasp of the complete power supply design is necessary to properly plan and execute the PCB assembly process.
Prepare the PCB for Component Placement
Step | Description |
---|---|
PCB Inspection | Visually examine the bare PCB for any obvious defects, contamination, or damage. Check hole sizes, pad conditions, soldermask, legend markings, etc. |
Tooling Holes | Verify that tooling holes are present and sized correctly for compatibility with your assembly fixtures and machines. |
Fiducials | Confirm that global and local fiducial marks are properly located on the PCB to enable machine vision alignment. |
Stencil | Obtain a laser-cut or electroformed solder paste stencil that matches the pad layout and sizes on the PCB. |
Solder Paste | Select a solder paste compatible with the surface finish on the PCB pads (e.g. lead-free vs leaded) and the reflow profile required. |
Thoroughly cleaning the bare PCB of any contaminants and residues prior to solder paste application is also recommended. Consult with your solder paste and cleaning chemistry suppliers for best practices.
Place Power Components with Precision
Power supply PCBs often incorporate through-hole (THT) power components like large capacitors, inductors, transformers and connectors in addition to surface mount devices (SMD). Special care must be taken during placement of these bulky and heavy parts:
THT Power Component Placement
- Manually place THT components per their polarity, orientation and body outline defined in the assembly drawing
- Fully seat component leads into their corresponding PTH locations, ensuring the component body rests flush against the PCB surface without gaps
- Secure power components to the PCB using adhesives or mounting hardware as specified to prevent shifting during wave soldering
- Clip or form component leads on the solder side of the PCB per instructions to optimize flow hole fill and top side protrusion
- Avoid placing THT parts too close to tall SMD components or other obstructions that could interfere with their placement or soldering
SMD Power Component Placement
- Use a pick-and-place machine with sufficient nozzle size, suction, and placement force capability to reliably handle larger SMD power components
- Ensure nozzle tips are appropriate for the component package dimensions and weight to avoid damage during pickup and placement
- Program the placement machine with the correct polarity, rotation, and XY coordinates for each power component per the centroid file
- Carefully monitor the placement process to check that power components are accurately placed on their PCB pads without misalignment or tombstoning
- Allow sufficient edge clearance around power components for solder fillet formation and visual inspection
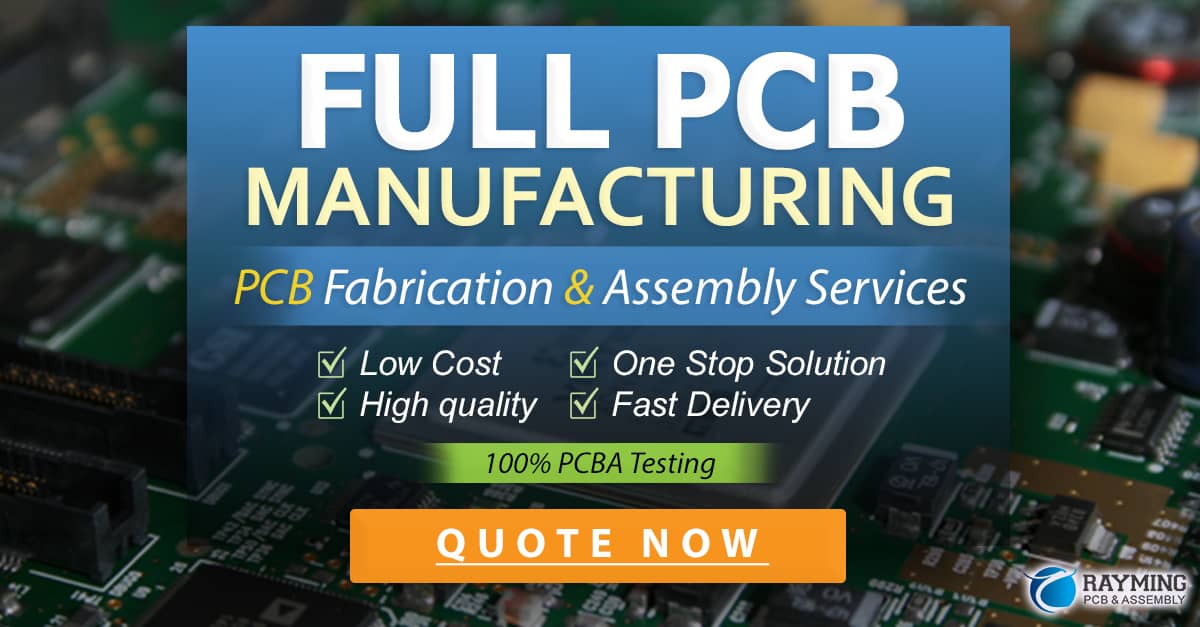
Optimize the Solder Paste Printing Process
Consistent solder paste printing is one of the most important factors in achieving high-quality solder joints on power supply PCBs. Follow these guidelines to optimize the stencil printing process:
Parameter | Guideline |
---|---|
Stencil Thickness | Select a stencil thickness that balances the need for sufficient paste volume and prevention of bridging, typically 0.1-0.15mm for power components |
Aperture Size | Modify aperture widths and lengths as needed to achieve the desired paste volume and accommodate any unique component geometries |
Aperture Shape | Use home plate or rounded rectangle aperture shapes for larger SMD pads to improve paste release |
Stencil Type | Consider a stepped stencil to print less paste on smaller SMD pads and more paste on power component pads |
Print Parameters | Set blade pressure, speed, separation speed, and snap-off distance to optimize paste transfer efficiency and prevent defects |
Understencil Cleaning | Regularly clean the understencil area to prevent paste bleed out and buildup that can cause smearing or poor print definition |
It’s also advisable to use SPI (solder paste inspection) equipment to analyze the paste deposits immediately after printing. This allows you to catch any print defects and make stencil or parameter adjustments before components are placed.
Reflow Soldering Power Supply PCBs
After all THT and SMD components are placed, the power supply PCB is ready for reflow soldering. A proper reflow profile is needed to form reliable solder joints without damaging components.
Reflow Oven Setup
- Use a reflow oven with good temperature accuracy, uniformity and control across the heated zones
- Select a nitrogen vs air atmosphere based on the solder paste flux type and power component thermal requirements
- Verify that the oven’s heated zone lengths and conveyor speed are compatible with the PCB size and thermal mass
- Install the necessary oven profiling equipment such as thermocouples and data loggers
Reflow Profile Development
- Obtain the reflow specifications for the solder paste and most sensitive power components being used
- Develop a baseline reflow profile with appropriate preheat, soak, reflow and cooling parameters
- Place thermocouples on the PCB at strategic locations including near large power components and ground planes
- Run the PCB through the reflow oven and analyze the logged temperature data
- Compare the actual PCB profile against the paste and component requirements
- Make adjustments to the oven zone temperatures and conveyor speed until an optimal profile is achieved
Profile Parameter | Typical Value |
---|---|
Preheat Ramp Rate | 0.5-2°C/sec |
Soak Temperature | 150-190°C |
Soak Time | 60-120 sec |
Reflow Peak Temperature | 235-245°C (lead-free) |
Time Above Liquidus (TAL) | 60-90 sec |
Cooling Rate | 1-6°C/sec |
Carefully review the post-reflow PCBs to verify good solder joint formation and identify any defects like bridging, tombstoning, or insufficient wetting that may require profile changes.
Wave Soldering THT Power Components
If the power supply PCB utilizes both SMD and THT components, an additional wave soldering process is needed after SMD reflow. Wave soldering allows the THT component leads to be soldered from the bottom side of the PCB.
Wave Solder Machine Setup
- Select a wave solder machine with a pot size and throughput capability suitable for the PCB panel dimensions
- Use a dual wave configuration consisting of a turbulent wave followed by a laminar wave to optimize hole fill and top side fillet formation
- Adjust the conveyor angle, width and speed to ensure the PCB panels are properly oriented and transported through the machine
- Control the solder pot temperature to maintain a consistent molten solder viscosity and minimize dross formation
- Choose an appropriate flux chemistry and application method (spray or foam) for the PCB surface finish and components
Wave Solder Process Control
- Verify that all THT component leads are properly trimmed and formed prior to wave soldering
- Apply temporary high temperature masking or kapton tape to any SMD connectors or components that could be damaged by the molten solder wave
- Monitor and maintain the flux density and solder pot temperature within acceptable ranges during production
- Regularly skim the solder pot surface to remove dross and maintain a clean and consistent wave
- Analyze the wave soldered PCBs for good hole fill, top side fillet coverage and absence of shorts or icicles
Test and Inspect Assembled Power Supply PCBs
Thorough testing and inspection of the assembled power supply PCBs is necessary to catch any defects and ensure functionality before further integration.
Automated Optical Inspection (AOI)
AOI equipment uses machine vision algorithms to rapidly scan the PCB and identify potential defects such as:
- Missing or misaligned components
- Solder joint defects (bridging, opens, insufficient solder)
- Reversed polarity or orientation
- Damaged component bodies
Comparing the actual assembled PCB images against the expected CAD data allows AOI to detect a wide range of defects. However, AOI is limited to inspecting visible surfaces and cannot directly verify electrical performance.
Electrical Testing
Electrical testing is needed to further validate that the power supply PCB operates per its specifications. Common electrical tests include:
- Power on self-test (POST)
- Voltage and current outputs under different loading conditions
- Ripple and noise measurements
- Efficiency and power factor
- Protection features (over-voltage, over-current, short circuit, etc.)
Performing comprehensive electrical testing, including extended burn-in periods, can help identify any marginal components or assembly issues before the power supply is integrated into the end product.
X-Ray Inspection
X-ray inspection is a specialized technique for examining solder joints and other features that are hidden from view, such as:
- BGA and QFN solder balls
- PTH solder fill in connectors or large components
- Voids or cracks within the PCB substrate
X-ray can be valuable for power supply PCBs that have high density SMD packages or critical PTH joints that are difficult to inspect optically. However, X-ray equipment is expensive and inspecting large PCBs can be time-consuming.
By incorporating a combination of AOI, electrical testing and X-ray inspection, you can achieve a high level of confidence in the assembled power supply PCBs before they leave the production facility.
Frequently Asked Questions (FAQ)
What are the most common defects encountered in power supply PCB assembly?
Some of the most frequent assembly defects seen on power supply PCBs include:
- Solder joint defects such as bridging, poor wetting, or insufficient solder volume
- Missing or incorrectly placed components
- Reversed polarity on electrolytic capacitors or diodes
- Poor hole fill or top side fillet formation on wave soldered THT joints
- Damaged component bodies due to excessive placement force or reflow temperatures
How can I prevent solder paste printing defects?
To minimize solder paste printing defects, consider the following:
- Use a high quality laser cut or electroformed stencil with optimal aperture sizes and shapes
- Regularly clean the understencil area to prevent paste buildup and smearing
- Monitor and adjust print parameters such as pressure, speed, and separation distance
- Perform periodic SPI to detect any print volume or registration issues
- Store solder paste at the proper temperature and use it within its shelf life to maintain good print performance
What are some tips for achieving good reflow solder joints on power components?
To optimize reflow soldering of power components, keep these points in mind:
- Select a solder paste that is compatible with the component metallization and PCB surface finish
- Develop a reflow profile that achieves good wetting and intermetallic formation without exceeding component temperature limits
- Use a nitrogen reflow atmosphere if needed to minimize oxidation and improve solder joint appearance
- Ensure power components are accurately placed and secured to the PCB prior to reflow
- Visually inspect solder joints after reflow for proper fillet formation and absence of defects
When is X-ray inspection needed for power supply PCBs?
X-ray inspection may be necessary for power supply PCBs in the following cases:
- High density SMD packages like BGAs or QFNs are used where solder balls are not visible optically
- PTH components have hidden solder joints that cannot be inspected from the top side
- Suspect voids, cracks or delamination within the PCB substrate itself
- Failure analysis is needed to examine internal features of components or solder joints
- Compliance with industry standards or customer requirements mandates X-ray inspection
How can I reduce the risk of ESD damage during power supply PCB assembly?
To protect sensitive components from ESD (electrostatic discharge) damage during PCB assembly, follow these guidelines:
- Establish an ESD-safe workspace with grounded mats, wrist straps, and dissipative flooring
- Train all personnel on proper ESD handling procedures and use of protective equipment
- Use ESD-safe packaging, transport carts and storage racks for PCBs and components
- Regularly test and maintain ESD protection equipment to ensure proper functionality
- Handle PCBs and components by their edges and avoid touching exposed leads or pins
By understanding and mitigating ESD risks, you can significantly reduce the occurrence of latent component failures and improve overall power supply reliability.
Conclusion
Assembling high-quality, reliable power supply PCBs requires careful planning, process control and adherence to best practices. By following the guidelines covered in this article, you can avoid common defects, optimize solder joint formation, and ensure consistent performance of your power supplies.
Remember to always start with a thorough understanding of the PCB design, use precision placement and soldering equipment, develop optimal reflow and wave solder profiles, and perform comprehensive inspection and testing.
With the right tools, techniques, and attention to detail, you can efficiently produce power supply PCBs that meet even the most demanding application requirements.
0 Comments