Miniaturization and High-Density Interconnect (HDI) PCBs
One of the most significant PCB Trends is the ongoing miniaturization of electronic components and devices. As consumers demand smaller and more portable devices, manufacturers are turning to High-Density Interconnect (HDI) PCBs to meet these requirements. HDI PCBs feature finer trace widths, smaller vias, and higher component density compared to traditional PCBs.
Benefits of HDI PCBs
- Reduced board size and weight
- Improved signal integrity and performance
- Enhanced thermal management
- Lower power consumption
Challenges in HDI PCB Manufacturing
- Increased complexity in design and fabrication
- Higher manufacturing costs
- Specialized equipment and skilled labor requirements
Despite these challenges, the demand for HDI PCBs continues to grow, particularly in industries such as consumer electronics, automotive, and medical devices.
Flexible and Rigid-Flex PCBs
Another major trend in the PCB industry is the increasing adoption of flexible and rigid-flex PCBs. These versatile boards offer several advantages over traditional rigid PCBs, making them ideal for applications that require flexibility, durability, and space savings.
Advantages of Flexible and Rigid-Flex PCBs
- Increased design freedom and form factor flexibility
- Improved reliability and shock resistance
- Reduced assembly time and costs
- Lightweight and space-saving
Applications of Flexible and Rigid-Flex PCBs
- Wearable devices
- Medical implants and devices
- Automotive electronics
- Aerospace and military equipment
As the demand for compact and reliable electronic devices continues to rise, the use of flexible and rigid-flex PCBs is expected to grow significantly in the coming years.
Advanced Materials and Substrates
The development of advanced materials and substrates is another key trend in the PCB industry. These innovative materials offer improved performance, reliability, and environmental sustainability compared to traditional PCB materials.
Examples of Advanced Materials and Substrates
- Low-loss materials for high-frequency applications
- Thermally conductive materials for better heat dissipation
- Eco-friendly materials, such as halogen-free and recyclable substrates
- High-temperature materials for harsh environment applications
The use of advanced materials and substrates enables PCB manufacturers to create boards that can withstand extreme conditions, support high-speed data transmission, and minimize environmental impact.
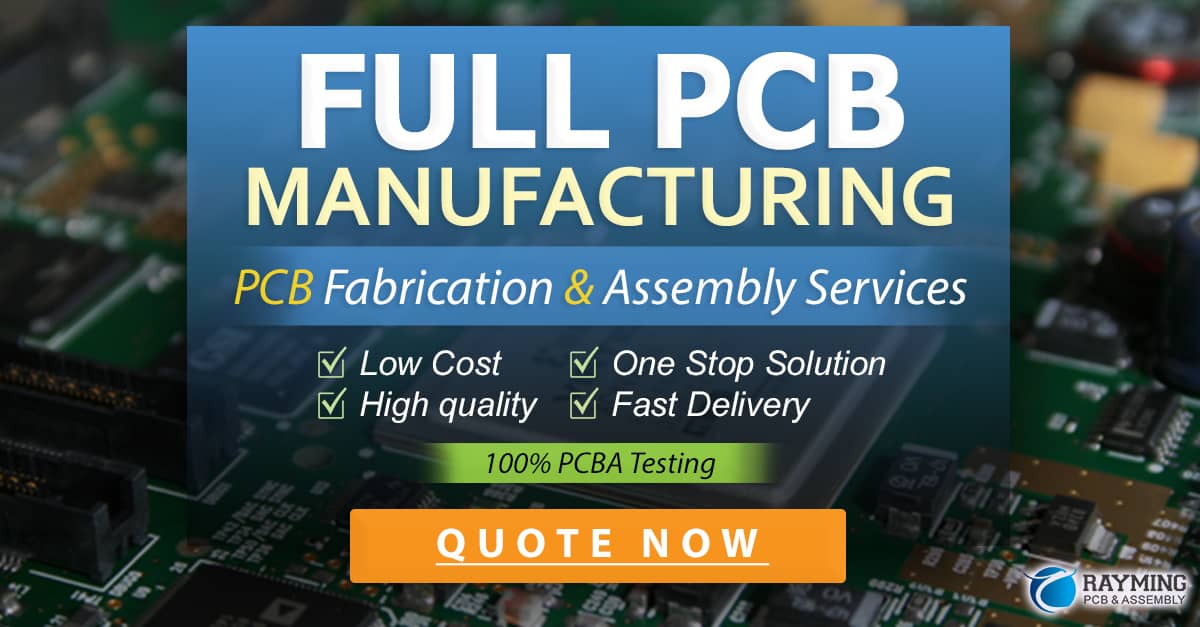
Embedded Components and 3D PCBs
Embedded components and 3D PCBs represent another significant trend in the PCB industry. By integrating components within the PCB layers or stacking multiple PCB layers, manufacturers can create highly compact and efficient electronic assemblies.
Benefits of Embedded Components and 3D PCBs
- Reduced board size and thickness
- Improved signal integrity and reduced noise
- Enhanced thermal management
- Increased reliability and durability
Challenges in Implementing Embedded Components and 3D PCBs
- Complex design and manufacturing processes
- Higher costs compared to traditional PCBs
- Limited repairability and serviceability
Despite these challenges, the adoption of embedded components and 3D PCBs is expected to increase, particularly in applications that require high-density packaging and advanced functionality.
Additive Manufacturing and 3D Printing
Additive manufacturing, also known as 3D printing, is an emerging trend in the PCB industry. This technology enables the rapid prototyping and production of PCBs without the need for traditional tooling and fabrication processes.
Advantages of Additive Manufacturing in PCB Production
- Faster prototyping and shorter lead times
- Reduced waste and environmental impact
- Increased design flexibility and customization
- Lower costs for low-volume production
Limitations of Additive Manufacturing in PCB Production
- Limited material options compared to traditional manufacturing
- Lower production speeds for high-volume manufacturing
- Challenges in achieving high-precision and fine-pitch features
As additive manufacturing technology advances, it is expected to play a growing role in PCB production, particularly for rapid prototyping, low-volume production, and custom designs.
Artificial Intelligence and Machine Learning in PCB Design and Manufacturing
Artificial Intelligence (AI) and Machine Learning (ML) are transforming various aspects of the PCB industry, from design automation to quality control and predictive maintenance.
Applications of AI and ML in PCB Design and Manufacturing
- Automated design rule checks (DRC) and design for manufacturability (DFM) analysis
- Intelligent component placement and routing optimization
- Automated visual inspection and defect detection
- Predictive maintenance and process optimization
By leveraging AI and ML technologies, PCB manufacturers can improve design efficiency, reduce errors, and optimize production processes, ultimately leading to higher quality products and faster time-to-market.
FAQ
1. What is the most significant trend in the PCB industry?
The most significant trend in the PCB industry is the ongoing miniaturization of electronic components and devices, which is driving the adoption of High-Density Interconnect (HDI) PCBs.
2. What are the benefits of using flexible and rigid-flex PCBs?
Flexible and rigid-flex PCBs offer increased design freedom, improved reliability, reduced assembly time and costs, and space savings compared to traditional rigid PCBs.
3. How are advanced materials and substrates improving PCB performance?
Advanced materials and substrates, such as low-loss materials, thermally conductive materials, and eco-friendly substrates, offer improved performance, reliability, and environmental sustainability compared to traditional PCB materials.
4. What are the challenges in implementing embedded components and 3D PCBs?
The challenges in implementing embedded components and 3D PCBs include complex design and manufacturing processes, higher costs, and limited repairability and serviceability compared to traditional PCBs.
5. How are AI and ML technologies being applied in the PCB industry?
AI and ML technologies are being applied in various aspects of the PCB industry, including automated design rule checks, intelligent component placement and routing optimization, automated visual inspection, and predictive maintenance.
PCB Trend | Key Benefits | Challenges |
---|---|---|
HDI PCBs | Reduced size and weight, improved performance | Increased complexity and costs |
Flexible and Rigid-Flex PCBs | Design freedom, reliability, space savings | Higher costs, specialized manufacturing |
Advanced Materials and Substrates | Improved performance, reliability, sustainability | Higher costs, limited availability |
Embedded Components and 3D PCBs | Compact and efficient assemblies | Complex manufacturing, limited repairability |
Additive Manufacturing | Rapid prototyping, reduced waste | Limited materials, lower production speeds |
The PCB industry is undergoing significant changes driven by these top technology trends. As manufacturers continue to innovate and adopt new technologies, we can expect to see more compact, efficient, and reliable electronic devices in the future. By staying informed about these trends and their potential impact, companies can make informed decisions and stay competitive in the rapidly evolving PCB market.
0 Comments