Mistake 1: Failing to Provide Complete and Accurate Documentation
One of the most critical aspects of placing a successful PCB assembly order is providing complete and accurate documentation. This includes:
- Bill of Materials (BOM)
- Gerber files
- Assembly drawings
- Schematics
- Test specifications
The Importance of a Comprehensive Bill of Materials (BOM)
A Bill of Materials (BOM) is a detailed list of all the components required for the PCB assembly process. It should include the following information for each component:
- Part number
- Quantity
- Description
- Manufacturer
- Supplier
Failing to provide a comprehensive and accurate BOM can lead to:
- Incorrect components being used
- Delays in the assembly process
- Increased costs due to last-minute changes
To avoid these issues, ensure that your BOM is complete, accurate, and up-to-date before submitting your PCB assembly order.
The Role of Gerber Files in PCB Assembly
Gerber files are the industry standard for conveying PCB design information to manufacturers. These files contain critical data about the PCB layout, including:
- Copper layers
- Solder mask
- Silkscreen
- Drill holes
Providing incomplete or incorrect Gerber files can result in:
- Manufacturing errors
- Delays in the assembly process
- Increased costs due to rework
To prevent these problems, double-check your Gerber files for accuracy and completeness before submitting your PCB assembly order.
Document Type | Purpose | Consequences of Inaccuracies |
---|---|---|
Bill of Materials (BOM) | Detailed list of required components | Incorrect components, delays, increased costs |
Gerber Files | Conveys PCB design information | Manufacturing errors, delays, increased costs |
Assembly Drawings | Provides visual representation of component placement | Misplaced components, assembly errors |
Schematics | Shows electrical connections and component relationships | Incorrect functionality, troubleshooting difficulties |
Test Specifications | Defines testing requirements and procedures | Inadequate quality control, product failures |
Mistake 2: Neglecting Design for Manufacturability (DFM)
Design for Manufacturability (DFM) is the practice of designing PCBs in a way that optimizes the manufacturing process. Neglecting DFM principles can lead to various issues, such as:
- Increased manufacturing costs
- Lower yields
- Longer lead times
- Reduced reliability
Key DFM Considerations
To ensure that your PCB design is optimized for manufacturability, consider the following factors:
- Component selection and placement
- Trace width and spacing
- Via size and placement
- Solder mask and silkscreen design
- Panelization and routing
By incorporating DFM principles into your PCB design, you can:
- Reduce manufacturing costs
- Improve yields
- Shorten lead times
- Enhance product reliability
Collaborating with Your PCB Assembly Partner
To maximize the benefits of DFM, it is essential to collaborate with your PCB assembly partner early in the design process. They can provide valuable insights and recommendations based on their manufacturing capabilities and experience, helping you optimize your design for their specific processes.
Mistake 3: Ignoring the Importance of Component Availability
Component availability is a critical factor in the success of your PCB assembly project. Ignoring this aspect can lead to:
- Delays in the assembly process
- Increased costs due to last-minute component sourcing
- Redesigns to accommodate alternative components
Strategies for Ensuring Component Availability
To mitigate the risks associated with component availability, consider the following strategies:
- Select components with multiple sourcing options
- Verify component availability and lead times early in the design process
- Maintain open communication with your PCB assembly partner regarding component status
- Consider using alternative components with similar specifications when necessary
By proactively addressing component availability, you can minimize delays, control costs, and ensure a smooth PCB assembly process.
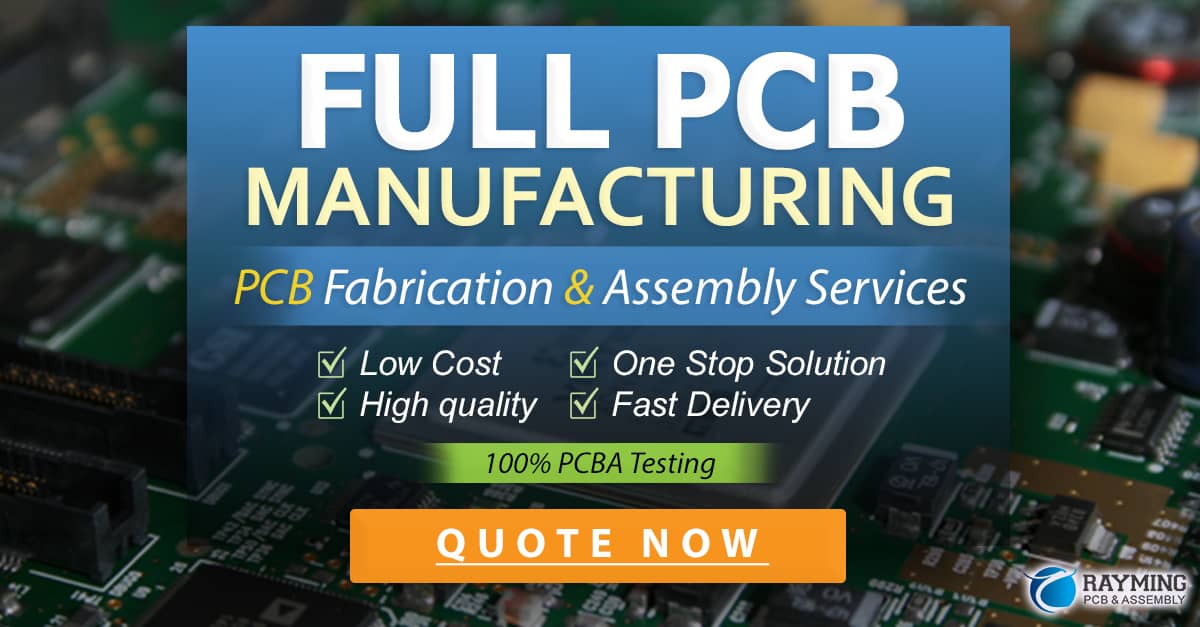
Mistake 4: Failing to Consider Testing and Quality Control
Testing and quality control are essential aspects of the PCB assembly process, ensuring that your products meet the required specifications and performance standards. Failing to consider these factors can result in:
- Increased product failures
- Higher warranty costs
- Damage to your brand reputation
Defining Testing Requirements
To avoid these issues, clearly define your testing requirements and communicate them to your PCB assembly partner. This may include:
- In-circuit testing (ICT)
- Functional testing
- Boundary scan testing
- X-ray inspection
- Thermal cycling
By specifying your testing requirements upfront, you can ensure that your PCB assembly partner has the necessary capabilities and resources to meet your quality control needs.
The Benefits of a Robust Quality Control Process
Implementing a robust quality control process offers several benefits, such as:
- Early detection and correction of defects
- Reduced product failures and warranty costs
- Improved customer satisfaction
- Enhanced brand reputation
Work closely with your PCB assembly partner to develop a comprehensive quality control plan that addresses your specific product requirements and industry standards.
Mistake 5: Overlooking the Importance of Communication and Collaboration
Effective communication and collaboration between you and your PCB assembly partner are crucial for the success of your project. Overlooking this aspect can lead to:
- Misunderstandings about project requirements
- Delays due to incomplete or inaccurate information
- Increased costs due to rework or redesigns
Best Practices for Communication and Collaboration
To foster a strong working relationship with your PCB assembly partner, consider the following best practices:
- Establish clear lines of communication and designate key points of contact
- Provide comprehensive and accurate project documentation
- Regularly update your PCB assembly partner on project status and changes
- Be responsive to questions and requests for information
- Collaborate on problem-solving and continuous improvement initiatives
By prioritizing communication and collaboration, you can build a strong partnership with your PCB assembly provider, resulting in improved project outcomes and long-term success.
Frequently Asked Questions (FAQ)
-
Q: What are the most critical documents to provide when placing a PCB assembly order?
A: The most critical documents include the Bill of Materials (BOM), Gerber files, assembly drawings, schematics, and test specifications. Ensuring that these documents are complete, accurate, and up-to-date is essential for a smooth and successful PCB assembly process. -
Q: How can I optimize my PCB design for manufacturability?
A: To optimize your PCB design for manufacturability, consider factors such as component selection and placement, trace width and spacing, via size and placement, solder mask and silkscreen design, and panelization and routing. Collaborating with your PCB assembly partner early in the design process can help you incorporate Design for Manufacturability (DFM) principles effectively. -
Q: What should I do if a component becomes unavailable during the PCB assembly process?
A: If a component becomes unavailable, first communicate the issue to your PCB assembly partner. They may have alternative sourcing options or be able to recommend a suitable replacement component. In some cases, a redesign may be necessary to accommodate alternative components with similar specifications. -
Q: How can I ensure that my PCB assembly meets the required quality standards?
A: To ensure that your PCB assembly meets the required quality standards, clearly define your testing requirements and communicate them to your PCB assembly partner. This may include in-circuit testing (ICT), functional testing, boundary scan testing, X-ray inspection, and thermal cycling. Work closely with your PCB assembly partner to develop a comprehensive quality control plan that addresses your specific product requirements and industry standards. -
Q: What are the benefits of effective communication and collaboration with my PCB assembly partner?
A: Effective communication and collaboration with your PCB assembly partner can lead to improved project outcomes, reduced misunderstandings, minimized delays, and lower costs. By establishing clear lines of communication, providing comprehensive project documentation, and regularly updating your partner on project status and changes, you can build a strong working relationship that fosters long-term success.
In conclusion, avoiding these top common mistakes while placing a PCB assembly order is essential for ensuring the success of your electronics manufacturing project. By providing complete and accurate documentation, considering Design for Manufacturability (DFM), addressing component availability, defining testing and quality control requirements, and prioritizing communication and collaboration, you can minimize risks, reduce costs, and achieve high-quality results. Partnering with an experienced and reliable PCB assembly provider who understands these critical factors can help you navigate the complexities of the process and deliver a successful product to market.
0 Comments