Understanding BOM and CPL
What is a BOM?
A Bill of Materials (BOM) is a comprehensive list of raw materials, components, and instructions required to manufacture, assemble, or repair a product or service. It serves as a centralized source of information that details every item needed for production, including quantities, descriptions, and sometimes even costs. The BOM is an essential tool for managing production processes, ensuring that all necessary components are available when needed, and keeping track of inventory levels.
What is a CPL?
A Component Part List (CPL) is a document that lists all the individual parts or components that make up a larger assembly or system. The CPL typically includes detailed information about each component, such as its unique identifier, description, quantity, manufacturer, and part number. In some cases, the CPL may also include additional information like the component’s dimensions, weight, material composition, or other relevant specifications.
The primary purpose of a CPL is to provide a clear and concise reference for all the parts used in a particular product or system. This information is crucial for various departments within an organization, including engineering, procurement, manufacturing, and maintenance teams.
Differences between BOM and CPL
While BOM and CPL are often used interchangeably, there are some key differences between the two:
Aspect | BOM | CPL |
---|---|---|
Scope | Comprehensive list of all materials, components, and instructions needed to create a product | Detailed list of individual parts or components that make up a larger assembly or system |
Level of Detail | May include subassemblies, raw materials, and process instructions | Focused on individual components and their specifications |
Purpose | Used for managing production processes, ensuring availability of components, and tracking inventory | Serves as a reference for all parts used in a product or system, useful for various departments |
Hierarchy | Often structured in a hierarchical manner, with top-level items broken down into subassemblies and components | Typically a flat list of components without a hierarchical structure |
Creating Effective BOM and CPL
Best Practices for BOM Creation
-
Use a consistent naming convention: Establish a standardized naming convention for all components and materials in the BOM to avoid confusion and ensure clarity across teams.
-
Include detailed descriptions: Provide clear and concise descriptions for each item in the BOM, including any relevant specifications, dimensions, or material composition.
-
Specify quantities: Clearly state the required quantity for each component or material in the BOM to ensure accurate inventory management and procurement.
-
Organize in a hierarchical structure: Structure the BOM in a hierarchical manner, with top-level items broken down into subassemblies and components, to provide a clear overview of the product’s structure.
-
Regularly review and update: Continuously review and update the BOM to reflect any changes in the product design, components, or suppliers to maintain accuracy and relevance.
Best Practices for CPL Creation
-
Use unique identifiers: Assign each component a unique identifier, such as a part number, to avoid confusion and ensure precise reference throughout the organization.
-
Provide detailed specifications: Include all relevant specifications for each component, such as dimensions, weight, material composition, and performance characteristics.
-
Include manufacturer information: Specify the manufacturer and their part number for each component to ensure consistency in sourcing and procurement.
-
Organize by system or assembly: Group components in the CPL according to the system or assembly they belong to for easier reference and navigation.
-
Maintain version control: Implement version control for the CPL to track changes and ensure that all teams are working with the most up-to-date information.
Managing BOM and CPL Data
Integration with ERP and PLM Systems
Integrating BOM and CPL data with Enterprise Resource Planning (ERP) and Product Lifecycle Management (PLM) systems can greatly enhance the efficiency and accuracy of product development and manufacturing processes.
ERP systems can utilize BOM data to:
– Plan and schedule production
– Manage inventory levels
– Generate work orders
– Calculate material costs
PLM systems can leverage both BOM and CPL data to:
– Manage product development processes
– Control product versions and revisions
– Facilitate collaboration among teams
– Streamline change management
By integrating BOM and CPL data with these systems, organizations can ensure that all teams have access to the most up-to-date and accurate product information, reducing errors, and improving overall efficiency.
Data Maintenance and Updates
Regularly maintaining and updating BOM and CPL data is crucial for ensuring the accuracy and relevance of product information. Some key considerations for data maintenance include:
-
Establish ownership: Assign clear ownership and responsibilities for maintaining and updating BOM and CPL data to ensure accountability and regular updates.
-
Define update processes: Establish well-defined processes for updating BOM and CPL data, including workflows for reviewing, approving, and implementing changes.
-
Conduct periodic audits: Regularly audit BOM and CPL data to identify and correct any discrepancies, errors, or outdated information.
-
Collaborate with suppliers: Work closely with suppliers to ensure that component information in the CPL is accurate and up-to-date, particularly for externally sourced parts.
-
Utilize automation: Implement automated tools and systems to streamline data maintenance, such as automatically updating BOM and CPL data when changes are made in CAD or PLM systems.
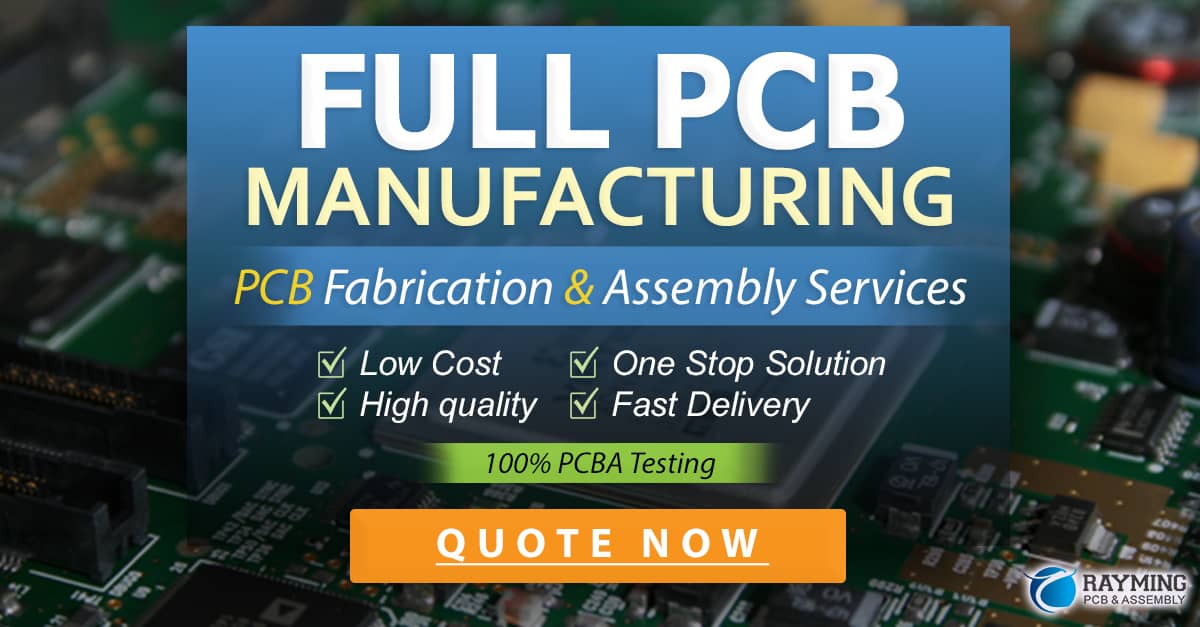
Leveraging BOM and CPL Data for Improved Outcomes
Enhancing Supply Chain Management
BOM and CPL data can be leveraged to optimize supply chain management in several ways:
-
Demand planning: Use BOM data to accurately forecast material requirements and ensure that the necessary components are available when needed for production.
-
Supplier consolidation: Analyze CPL data to identify opportunities for supplier consolidation, reducing complexity and potentially lowering costs.
-
Strategic sourcing: Utilize BOM and CPL data to identify critical components and develop strategic sourcing strategies to mitigate supply chain risks.
-
Inventory optimization: Leverage BOM data to determine optimal inventory levels for raw materials and components, reducing holding costs and minimizing stockouts.
Improving Product Quality and Compliance
Accurate and well-maintained BOM and CPL data can contribute to improved product quality and compliance by:
-
Ensuring consistent components: Using CPL data to specify and source consistent, high-quality components across all products and batches.
-
Facilitating traceability: Maintaining detailed BOM and CPL records to enable traceability of components and materials throughout the supply chain, which is crucial for compliance with regulations and quality standards.
-
Enabling root cause analysis: Leveraging BOM and CPL data to quickly identify the source of quality issues or defects, facilitating root cause analysis and corrective actions.
-
Supporting product lifecycle management: Utilizing BOM and CPL data to manage product changes, updates, and obsolescence throughout the product lifecycle, ensuring ongoing quality and compliance.
Frequently Asked Questions (FAQ)
- What is the difference between an Engineering BOM (eBOM) and a Manufacturing BOM (mBOM)?
-
An Engineering BOM (eBOM) is created by the design team and focuses on the product’s design, including all the parts, materials, and components needed to create the product. In contrast, a Manufacturing BOM (mBOM) is derived from the eBOM and adapted for the manufacturing process, considering factors such as assembly instructions, packaging, and manufacturing-specific components.
-
How do I handle component obsolescence in my CPL?
-
To manage component obsolescence in your CPL, regularly review and update the list to identify components nearing the end of their lifecycle. Work with suppliers to find suitable replacement parts, and update the CPL accordingly. Implement a proactive obsolescence management strategy, which may include lifetime buys, redesigns, or alternative sourcing options.
-
What role does BOM play in cost estimation and budgeting?
-
The BOM serves as a critical tool for cost estimation and budgeting by providing a detailed list of all materials, components, and quantities required for a product. By assigning costs to each item in the BOM, organizations can accurately estimate the total material cost of a product, which forms the basis for pricing decisions, budgeting, and cost control measures.
-
How can I ensure data consistency between my BOM and CPL?
-
To maintain data consistency between your BOM and CPL, establish clear data governance policies and procedures. Define a single source of truth for component information, and ensure that all teams work from the same, up-to-date data. Implement automated data synchronization between systems, and conduct regular audits to identify and resolve any discrepancies.
-
What are the benefits of using a multi-level BOM structure?
- A multi-level BOM structure offers several benefits, including:
- Providing a clear, hierarchical overview of the product structure
- Enabling better organization and management of complex products
- Facilitating more accurate cost roll-ups and analysis
- Supporting more efficient product development and change management processes
- Allowing for easier reuse of subassemblies and components across multiple products
By leveraging the tips, best practices, and strategies outlined in this article, organizations can effectively create, manage, and utilize BOM and CPL data to drive improvements in product development, manufacturing, supply chain management, and overall operational efficiency.
0 Comments