What is Etching in PCB Manufacturing?
Etching is a critical process in the manufacturing of printed circuit boards (PCBs), especially multilayer PCBs. It involves selectively removing copper from the surface of the PCB substrate to create the desired circuit pattern. The etching process is typically performed using chemical etchants, such as ferric chloride or ammonium persulfate, which dissolve the exposed copper while leaving the protected areas intact.
In multilayer PCB manufacturing, etching plays a crucial role in creating the intricate network of conductive traces and vias that connect the different layers of the board. However, the etching process can be complex and prone to various issues that can affect the quality and reliability of the final product.
Issue 1: Over-Etching
What is Over-Etching?
Over-etching occurs when the etchant removes more copper than intended, resulting in the widening of traces and the reduction of spacing between them. This can lead to several problems, such as:
- Reduced electrical performance due to increased resistance and capacitance
- Increased risk of short circuits and signal crosstalk
- Difficulty in meeting tight tolerance requirements
Causes of Over-Etching
Over-etching can be caused by various factors, including:
- Excessive etching time
- High etchant concentration or temperature
- Inadequate protection of the desired copper areas
- Inconsistent or uneven application of the photoresist
Prevention and Mitigation Strategies
To prevent or mitigate over-etching, PCB manufacturers can employ several strategies:
- Optimize the etching process parameters, such as time, temperature, and etchant concentration
- Use high-quality photoresists and ensure proper application and development
- Implement strict process control and monitoring systems
- Utilize advanced etching techniques, such as spray etching or laser-assisted etching
Parameter | Optimum Range |
---|---|
Etching Time | 60-90 seconds |
Etchant Temperature | 45-55°C |
Etchant Concentration | 30-40% |
Issue 2: Under-Etching
What is Under-Etching?
Under-etching occurs when the etchant fails to remove enough copper, resulting in the incomplete formation of traces and vias. This can lead to several problems, such as:
- Open circuits and disconnected traces
- Increased risk of short circuits due to remaining copper bridges
- Poor electrical performance due to inconsistent trace widths and thicknesses
Causes of Under-Etching
Under-etching can be caused by various factors, including:
- Insufficient etching time
- Low etchant concentration or temperature
- Excessive protection of the copper areas
- Contamination or degradation of the etchant solution
Prevention and Mitigation Strategies
To prevent or mitigate under-etching, PCB manufacturers can employ several strategies:
- Optimize the etching process parameters, such as time, temperature, and etchant concentration
- Regularly monitor and maintain the etchant solution to ensure consistent performance
- Use high-quality photoresists and ensure proper exposure and development
- Implement post-etching inspection and rework processes to identify and correct under-etched areas
Inspection Method | Defect Detection Capability |
---|---|
Automated Optical Inspection (AOI) | High |
Manual Visual Inspection | Medium |
Electrical Testing | High |
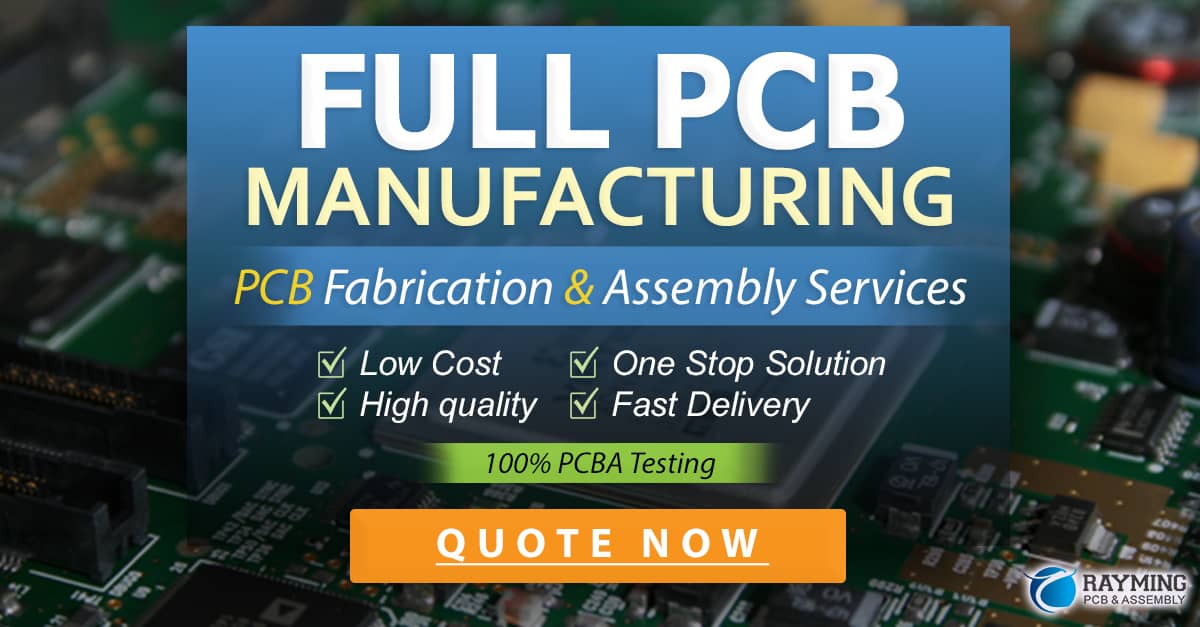
Issue 3: Etchant Compatibility
What is Etchant Compatibility?
Etchant compatibility refers to the ability of the etching solution to selectively remove copper without damaging other materials present in the multilayer PCB, such as the substrate, soldermask, or other metal layers. Incompatibility between the etchant and these materials can lead to several problems, such as:
- Delamination or warping of the PCB substrate
- Degradation or discoloration of the soldermask
- Corrosion or oxidation of other metal layers, such as gold or nickel
Causes of Etchant Incompatibility
Etchant incompatibility can be caused by various factors, including:
- Improper selection of etchant for the specific PCB materials and requirements
- Contamination or degradation of the etchant solution
- Inadequate control of the etching process parameters
- Insufficient cleaning and neutralization of the PCB after etching
Prevention and Mitigation Strategies
To prevent or mitigate etchant incompatibility, PCB manufacturers can employ several strategies:
- Carefully select the appropriate etchant for the specific PCB materials and requirements
- Regularly monitor and maintain the etchant solution to ensure consistent composition and performance
- Implement strict process control and monitoring systems to ensure optimal etching conditions
- Thoroughly clean and neutralize the PCB after etching to remove any residual etchant or byproducts
PCB Material | Compatible Etchant |
---|---|
FR-4 | Cupric Chloride, Ammonium Persulfate |
Polyimide | Alkaline Etchant, Cupric Chloride |
Teflon | Alkaline Etchant, Plasma Etching |
FAQ
-
Q: What are the most common etchants used in PCB manufacturing?
A: The most common etchants used in PCB manufacturing are ferric chloride, ammonium persulfate, and cupric chloride. The choice of etchant depends on factors such as the PCB material, desired etching speed, and environmental considerations. -
Q: How can I ensure consistent etching results in my multilayer PCB production?
A: To ensure consistent etching results, it is essential to implement strict process control and monitoring systems. This includes regularly monitoring and maintaining the etchant solution, optimizing the etching process parameters, and using high-quality photoresists and imaging techniques. Additionally, post-etching inspection and rework processes can help identify and correct any issues. -
Q: What are the environmental concerns associated with PCB etching?
A: PCB etching can have significant environmental impacts due to the use of hazardous chemicals and the generation of waste products. Common concerns include the disposal of spent etchant solutions, the release of toxic fumes, and the potential for groundwater contamination. To mitigate these concerns, PCB manufacturers must adhere to strict environmental regulations and implement proper waste management and treatment systems. -
Q: Are there any alternatives to chemical etching in PCB manufacturing?
A: Yes, there are several alternatives to chemical etching, such as plasma etching, laser etching, and mechanical milling. These methods offer advantages such as higher precision, reduced environmental impact, and compatibility with a wider range of materials. However, they may also have limitations in terms of cost, throughput, and the ability to handle complex PCB designs. -
Q: How can I troubleshoot Etching Issues in my multilayer PCB production?
A: Troubleshooting etching issues requires a systematic approach that involves analyzing the symptoms, identifying potential causes, and implementing corrective actions. Key steps include: - Visually inspecting the etched PCBs for signs of over-etching, under-etching, or incompatibility
- Reviewing the etching process parameters and comparing them to the optimal ranges
- Testing the etchant solution for composition, concentration, and contamination
- Evaluating the quality and application of the photoresist and imaging processes
- Conducting electrical testing to identify any open or short circuits
By following these steps and consulting with experienced PCB manufacturing professionals, you can effectively troubleshoot and resolve etching issues in your multilayer PCB production.
0 Comments