Introduction to Thermal Relief BGA Pads
Ball Grid Array (BGA) packages are a popular choice for high pin count integrated circuits due to their compact size and ability to accommodate a large number of connections in a small footprint. However, the high density of connections in a BGA package presents challenges when it comes to soldering the package to a printed circuit board (PCB). One key challenge is managing the thermal stress that occurs during the soldering process.
Thermal relief BGA pads are a design technique used to mitigate thermal stress issues when soldering BGA packages. They provide a controlled thermal path between the BGA solder ball and the connecting copper pour or plane on the PCB. This article will dive into the details of thermal relief BGA pad design, including:
- The purpose and benefits of thermal relief
- Key design parameters and considerations
- Layout guidelines and best practices
- Analyzing thermal relief effectiveness
- Frequently asked questions about thermal relief BGA pads
By understanding and properly implementing thermal relief techniques, designers can improve manufacturing yield, reliability, and performance of PCB assemblies using BGA packages.
What is Thermal Relief and Why is it Needed?
Thermal relief is a PCB design technique that creates a controlled thermal connection between a pad (in this case a BGA pad) and the surrounding copper pour or plane. The basic structure of a thermal relief pad is a pad with a reduced copper connection (a “thermal spoke”) to the surrounding copper.
The main purposes of thermal relief are:
- Allow a sufficient temperature differential between pad and plane during soldering so the solder properly wets and flows onto the pad without being prematurely cooled by the plane
- Limit heat transfer from the pad into the plane which could cause thermal stress, warpage, or damage to nearby components during soldering
- Provide mechanical anchoring of the pad to prevent pad lifting or separation
Without thermal relief, the large copper area of a plane would act as a major heat sink, making it difficult to heat the pad to the necessary soldering temperature. The solder would tend to wick away and spread out over the plane rather than forming a proper fillet on the pad. Thermal relief creates a bottleneck that allows the pad to reach a higher temperature than the plane.
Thermal relief is especially important for BGA packages due to the large number of connections and small pitches involved. Proper design of thermal relief is critical to achieving good soldering results and long-term reliability of BGA solder joints.
Key Parameters for Thermal Relief Pad Design
There are several key parameters that define a thermal relief pad. Understanding these parameters and making appropriate design choices is essential for effective thermal relief performance.
Spoke Count
The number of thermal spokes connecting the pad to the plane. Typical spoke counts are 2, 3, or 4. Higher spoke counts provide more thermal connection and mechanical strength but reduce thermal relief effectiveness.
Spoke Count | Thermal Relief | Mechanical Strength |
---|---|---|
2 | High | Low |
3 | Medium | Medium |
4 | Low | High |
Spoke Width
The width of the thermal spoke connection. Narrower spokes provide more thermal relief but reduce mechanical strength. Typical spoke widths range from 0.15mm to 0.3mm.
Spoke Length
The length of the thermal spoke from pad to plane. Longer spokes provide more thermal relief. Spoke length is typically set to allow a minimum 0.15mm web between the pad and plane.
Inner Diameter
The diameter of the pad where it connects to the spokes. A larger inner diameter reduces the thermal connection to the plane. The inner diameter must be sized to accommodate solder mask expansion.
Outer Diameter
The diameter of the pad where it connects to the BGA solder ball. The outer diameter is typically defined by the size and pitch of the BGA package.
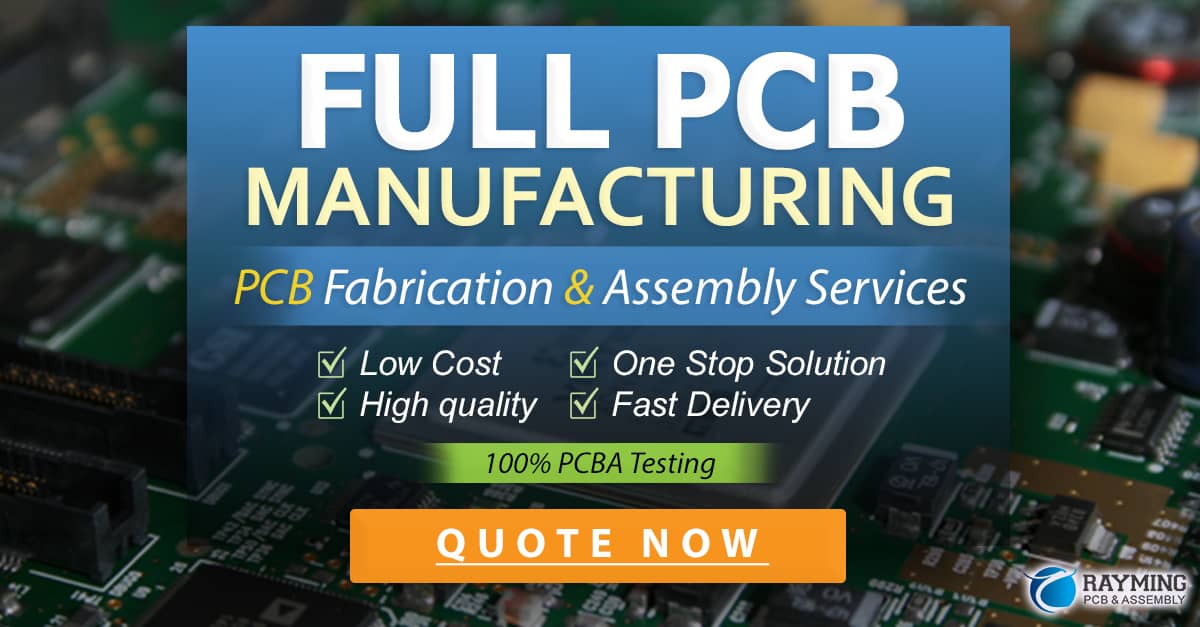
Thermal Relief Layout Guidelines
When laying out thermal relief BGA pads, there are several guidelines and best practices to follow:
-
Use a consistent spoke count for all pads in a BGA – mixing spoke counts can cause uneven heating and soldering defects
-
Orient spokes diagonally – this allows for the most spokes while minimizing plane copper loss
-
Ensure an adequate web of space between pad and plane – a 0.15mm minimum web is a typical rule
-
Size the pad inner diameter to account for solder mask expansion – typically 0.1mm larger than the copper pad diameter
-
Avoid acute angles in spoke or pad geometry – smooth, rounded connections are preferred
-
Provide a solderable surface on the outer pad – apply soldermask openings larger than the pad
-
Optimize spoke width for thermal and mechanical requirements – 0.15-0.2mm is typical for most designs but high-reliability applications may use wider spokes
-
Simulate or analyze complex designs – thermal and mechanical simulation can validate thermal relief performance prior to manufacturing
Analyzing Thermal Relief Effectiveness
The effectiveness of a thermal relief design can be analyzed through simulation or empirical testing. Thermal simulation tools can model the heat transfer from pad to plane during soldering and predict temperature gradients and thermal stress.
Key metrics for evaluating thermal relief include:
- Peak pad temperature during reflow soldering
- Thermal gradient between pad and plane
- Solder joint shape and volume
- Mechanical strength and reliability of solder joints
Empirical testing methods such as thermal imaging, cross-sectioning, and accelerated lifecycle testing can validate thermal relief performance in manufactured assemblies.
Proper thermal relief design should result in a well-formed solder joint with good wetting to the pad, minimal voids or defects, and a robust mechanical connection without thermal stress or damage to the PCB or components.
Thermal Relief BGA Design FAQ
Q: When is thermal relief needed for BGA pads?
A: Thermal relief is recommended for most BGA designs, especially those with large or high-density packages, small pad pitches, or thick power/ground planes. Thermal relief is critical when soldering BGA packages to multi-layer PCBs with large internal copper areas.
Q: What is the typical spoke count for BGA thermal relief pads?
A: 3 or 4 spokes are commonly used for BGA thermal relief. 2-spoke designs may be used in low-reliability consumer products. High-reliability or aerospace applications may use 5 or more spokes for added mechanical strength.
Q: How does the size of the BGA package affect thermal relief design?
A: Larger BGA packages have more thermal mass and may require longer or narrower thermal relief spokes to achieve adequate thermal isolation. Smaller BGA packages have less thermal mass but may have limited space for relief spokes due to tight pitches.
Q: Can thermal relief be used for non-BGA pads?
A: Yes, thermal relief can be applied to any surface mount or through-hole pad where a thermal connection to a copper pour or plane is needed. The same design principles of spoke count, width, and length apply.
Q: What are the trade-offs between thermal and mechanical performance in thermal relief design?
A: Thermal relief designs must balance the competing needs of thermal isolation and mechanical strength. More or wider thermal spokes will improve mechanical strength and reliability but reduce thermal isolation and make soldering more difficult. Narrower or fewer spokes have the opposite effect. The optimal design will depend on the specific requirements and reliability needs of the application.
Conclusion
Thermal relief BGA pad design is a critical aspect of PCB layout for assemblies using BGA packages. Proper implementation of thermal relief techniques can improve soldering quality, reduce thermal stress and defects, and enhance long-term reliability.
By understanding key design parameters such as spoke count, width, and length, and following layout best practices, designers can create robust thermal relief BGA pad designs. Analyzing thermal relief performance through simulation and testing validates the design and ensures manufacturing success.
As BGA packages continue to trend towards higher density and finer pitches, the importance of effective thermal relief design will only increase. Designers who master the principles and techniques of thermal relief will be well-equipped to tackle the challenges of modern BGA PCB design.
0 Comments