Introduction to Wire Harness and Cable Assembly
Wire harnesses and cable assemblies are essential components in various industries, including automotive, aerospace, and electronics. They are responsible for transmitting power and signals between different parts of a system, ensuring proper functionality and performance. However, like any other component, wire harnesses and cable assemblies can experience issues that require troubleshooting. In this comprehensive guide, we will explore common problems, their causes, and effective solutions to help you maintain and repair your wire harnesses and cable assemblies.
Common Issues in Wire Harness and Cable Assembly
1. Poor Connectivity
One of the most prevalent issues in wire harnesses and cable assemblies is poor connectivity. This can manifest as intermittent signals, power loss, or complete failure of the connected components. Poor connectivity can be caused by several factors, including:
- Loose or damaged connectors
- Corroded contacts
- Improper crimping or soldering
- Damaged wires or insulation
Troubleshooting Steps for Poor Connectivity
- Visually inspect the connectors and contacts for any signs of damage, corrosion, or contamination.
- Check the crimping or soldering points to ensure they are secure and properly executed.
- Test the continuity of the wires using a multimeter to identify any breaks or high resistance points.
- If necessary, clean the contacts using a suitable solvent and apply a contact enhancer to improve connectivity.
2. Short Circuits
Short circuits occur when two or more wires come into contact with each other, causing an unintended path for electrical current. This can lead to system malfunctions, component damage, or even fire hazards. Short circuits can be caused by:
- Damaged wire insulation
- Improper routing or bundling of wires
- Excessive bending or stretching of the harness or cable
- Exposure to harsh environmental conditions
Troubleshooting Steps for Short Circuits
- Disconnect the power source to the affected harness or cable assembly.
- Use a multimeter to test for continuity between the wires and ground. A short circuit will show a low resistance reading.
- Carefully inspect the wires for any signs of damage or exposed conductors.
- If a short circuit is found, isolate the affected section and repair or replace the damaged wires.
3. Open Circuits
Open circuits occur when there is a break in the electrical path, preventing current from flowing through the wire harness or cable assembly. This can cause a complete loss of power or signal to the connected components. Open circuits can be caused by:
- Broken or severed wires
- Faulty connectors or terminals
- Excessive strain on the harness or cable
- Corrosion or oxidation of the conductors
Troubleshooting Steps for Open Circuits
- Use a multimeter to test for continuity between the two ends of the suspected open circuit. An open circuit will show no continuity or an infinite resistance reading.
- Visually inspect the wires, connectors, and terminals for any signs of damage or corrosion.
- If an open circuit is found, locate the break and repair or replace the affected section of the wire harness or cable assembly.
4. Electromagnetic Interference (EMI)
Electromagnetic interference (EMI) is a disturbance that affects the performance of electrical circuits due to electromagnetic radiation emitted by other devices. EMI can cause signal degradation, data corruption, or even system failures. Common sources of EMI include:
- Power lines
- Electric motors
- Wireless communication devices
- Improperly shielded cables
Troubleshooting Steps for EMI
- Identify potential sources of EMI near the affected wire harness or cable assembly.
- Ensure proper shielding and grounding of the cables to minimize the effects of EMI.
- Use ferrite cores or other EMI suppression techniques to reduce the impact of electromagnetic radiation.
- Reroute the cables away from known sources of EMI, if possible.
5. Mechanical Damage
Wire harnesses and cable assemblies are often subjected to various mechanical stresses during installation and operation. Mechanical damage can compromise the integrity of the wires and lead to failures. Common causes of mechanical damage include:
- Improper handling or installation
- Abrasion against sharp edges or surfaces
- Excessive bending, twisting, or stretching
- Exposure to extreme temperatures or chemicals
Troubleshooting Steps for Mechanical Damage
- Visually inspect the wire harness or cable assembly for any signs of mechanical damage, such as cuts, abrasions, or deformations.
- Check for proper routing and support of the cables to minimize mechanical stress.
- Use protective sleeves, conduits, or grommets to prevent abrasion and damage in high-risk areas.
- Replace damaged sections of the wire harness or cable assembly, ensuring proper splicing and insulation techniques.
Preventive Maintenance for Wire Harness and Cable Assembly
Regular preventive maintenance is crucial to ensure the longevity and reliability of wire harnesses and cable assemblies. Some key preventive maintenance practices include:
-
Visual Inspection: Regularly inspect the wire harnesses and cable assemblies for any signs of damage, wear, or contamination. Look for frayed wires, cracked insulation, or corroded contacts.
-
Cleaning: Clean the connectors and contacts using a suitable solvent to remove dirt, dust, or oxidation. Apply a contact enhancer to improve connectivity and protect against corrosion.
-
Proper Routing and Support: Ensure that the wire harnesses and cable assemblies are properly routed and supported to minimize mechanical stress and prevent damage. Use cable ties, clamps, or other appropriate fasteners to secure the cables.
-
Environmental Protection: Protect the wire harnesses and cable assemblies from harsh environmental conditions, such as extreme temperatures, moisture, or chemical exposure. Use appropriate insulation, shielding, and sealing techniques to prevent damage.
-
Testing and Monitoring: Regularly test the continuity, resistance, and insulation resistance of the wire harnesses and cable assemblies to identify potential issues early. Use monitoring systems to detect and alert operators of any abnormalities in the system.
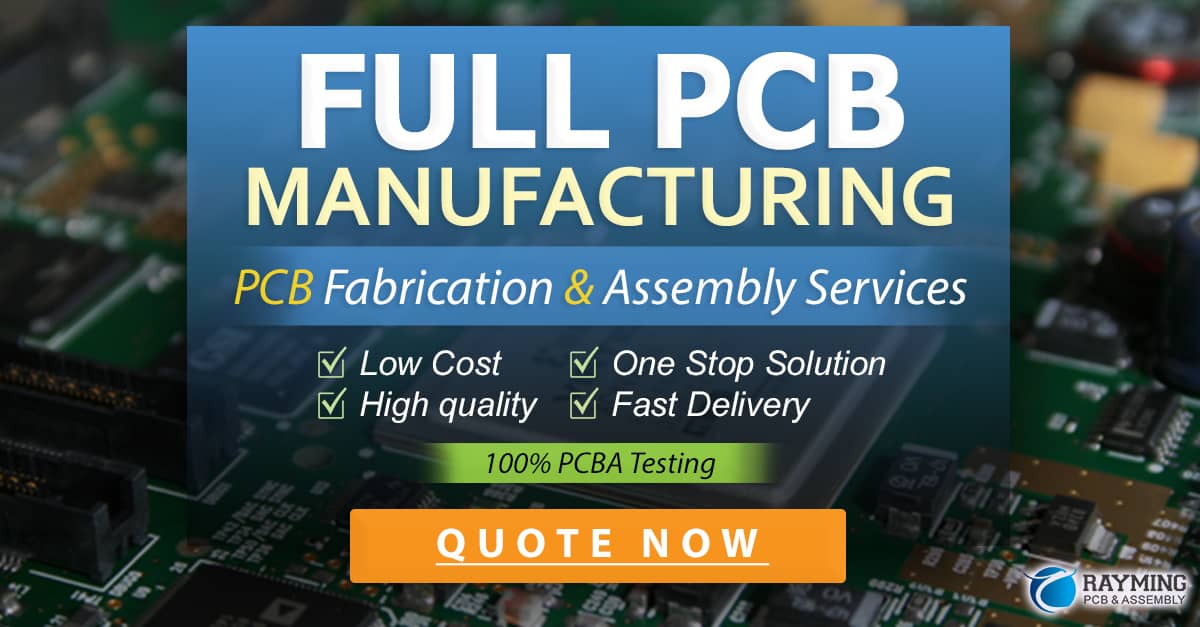
Troubleshooting Tools and Techniques
To effectively troubleshoot wire harness and cable assembly issues, it is essential to have the right tools and techniques at your disposal. Some of the most common troubleshooting tools and techniques include:
1. Multimeter
A multimeter is a versatile tool that can measure voltage, current, resistance, and continuity. It is an essential tool for troubleshooting electrical issues in wire harnesses and cable assemblies.
Function | Description |
---|---|
Voltage | Measures the potential difference between two points in an electrical circuit |
Current | Measures the flow of electrons through a conductor |
Resistance | Measures the opposition to current flow in an electrical circuit |
Continuity | Checks for a complete electrical path between two points |
2. Oscilloscope
An oscilloscope is a powerful tool that allows you to visualize and analyze electrical signals in real-time. It is particularly useful for troubleshooting signal integrity issues and identifying EMI problems.
3. Insulation Resistance Tester
An insulation resistance tester, also known as a megohmmeter, is used to measure the resistance of the insulation between conductors or between a conductor and ground. It helps identify degraded or damaged insulation that can lead to leakage currents or short circuits.
4. Time-Domain Reflectometer (TDR)
A time-domain reflectometer (TDR) is a specialized tool that uses high-frequency electrical pulses to locate faults in cables, such as open circuits, short circuits, or impedance mismatches. It is particularly useful for troubleshooting long cable runs or buried cables.
5. Thermal Imaging Camera
A thermal imaging camera is a non-contact tool that detects infrared radiation and creates a visual representation of the temperature distribution. It can be used to identify hot spots or overheating components in wire harnesses and cable assemblies, which may indicate potential failure points.
FAQ
-
Q: What are the most common causes of wire harness and cable assembly failures?
A: The most common causes of wire harness and cable assembly failures include poor connectivity, short circuits, open circuits, electromagnetic interference (EMI), and mechanical damage. -
Q: How can I prevent short circuits in my wire harness?
A: To prevent short circuits in your wire harness, ensure proper insulation and routing of the wires, avoid excessive bending or stretching, and protect the harness from harsh environmental conditions. Regularly inspect the wires for any signs of damage or exposed conductors. -
Q: What should I do if I suspect an open circuit in my cable assembly?
A: If you suspect an open circuit in your cable assembly, use a multimeter to test for continuity between the two ends of the suspected open circuit. If an open circuit is confirmed, visually inspect the wires, connectors, and terminals for any signs of damage or corrosion. Locate the break and repair or replace the affected section of the cable assembly. -
Q: How can I protect my wire harness from electromagnetic interference (EMI)?
A: To protect your wire harness from EMI, ensure proper shielding and grounding of the cables, use ferrite cores or other EMI suppression techniques, and route the cables away from known sources of EMI whenever possible. -
Q: What are some key preventive maintenance practices for wire harnesses and cable assemblies?
A: Key preventive maintenance practices for wire harnesses and cable assemblies include regular visual inspections, cleaning of connectors and contacts, proper routing and support, protection from harsh environmental conditions, and regular testing and monitoring of the system.
Conclusion
Troubleshooting wire harness and cable assembly issues can be a complex and challenging task. However, by understanding the common problems, their causes, and effective troubleshooting techniques, you can minimize downtime and ensure the reliable performance of your systems. Regular preventive maintenance, combined with the use of appropriate troubleshooting tools, can help you identify and resolve issues quickly and efficiently.
Remember to always prioritize safety when working with electrical systems, and consult professional assistance if you are unsure about any aspect of the troubleshooting process. By following the guidelines and best practices outlined in this comprehensive Troubleshooting Guide, you can keep your wire harnesses and cable assemblies in top condition and avoid costly failures.
0 Comments