What is a PCB and Why Are They Used?
A printed circuit board (PCB) is a thin board made of fiberglass, composite epoxy, or other laminate material that is used to mechanically support and electrically connect electronic components using conductive pathways, tracks or signal traces etched from copper sheets laminated onto a non-conductive substrate.
PCBs are used in virtually all commercial electronic products, providing a means to mechanically support and electrically connect electronic components using conductive pathways. They allow manufacturers to automate much of the assembly process, solder components to the board, and produce electronic products much more efficiently than with other wiring methods.
Some of the key benefits of using PCBs include:
- Compact size and low weight
- Low electronic noise
- Highly reliable
- Inexpensive mass production
- Easily repaired or replaced
The Six Main Types of PCB Applications
While PCBs are used in a wide variety of industries, there are six main categories of PCB applications:
- Consumer Electronics
- Medical Devices
- Aerospace & Defense
- Automotive
- Telecommunications
- Industrial Equipment
Let’s take a closer look at each of these PCB application categories in more detail.
1. Consumer Electronics
Consumer electronics is one of the largest markets for PCBs. This category includes devices such as:
- Smartphones and tablets
- Laptops and desktop computers
- Televisions and home theater systems
- Gaming consoles and controllers
- Wearable devices like smartwatches and fitness trackers
- Smart home devices and IoT products
PCBs used in consumer electronics must be designed to handle high-speed digital signals while minimizing electronic noise and interference. They also need to be as compact and lightweight as possible to fit into increasingly small form factors.
Common materials used for PCBs in consumer electronics include:
Material | Typical Applications |
---|---|
FR-4 | Computers, TVs, general purpose |
Polyimide | Flexible circuits, wearables |
High Tg FR-4 | Smartphones, tablets |
Metal Core | LED lighting, power electronics |
Consumer electronics PCBs also often require advanced features such as:
- High density interconnect (HDI)
- Blind and buried vias
- Embedded components
- Rigid-flex construction
2. Medical Devices
PCBs play a critical role in a wide range of medical devices, including:
- Diagnostic imaging equipment like X-ray, CT, and MRI machines
- Patient monitoring systems
- Surgical robotics and equipment
- Wearable health monitors and drug delivery devices
- Lab analysis and testing equipment
Reliability and signal integrity are paramount for PCBs used in medical devices. They must be able to operate continuously for long periods of time without failure. Miniaturization is also increasingly important to enable smaller, less invasive devices.
Standards and certifications required for Medical PCBs may include:
- ISO 13485
- IPC 6012 Class 3
- REACH and RoHS compliance
- FDA approval
3. Aerospace & Defense
PCBs used in aerospace and defense applications must be able to withstand extreme environmental conditions, including:
- Wide temperature ranges
- High altitudes
- Shock and vibration
- Exposure to water, chemicals, and abrasion
Common aerospace and defense PCB applications include:
- Avionics and flight control systems
- Radar and surveillance
- Satellite and spacecraft components
- Military communications and imaging
Materials used in aerospace and defense PCBs must have high heat resistance, mechanical strength, and low outgassing properties. Typical laminates include:
Material | Characteristics |
---|---|
Polyimide | Flexible, lightweight, thermal resistant |
PTFE/Teflon | Low dielectric constant, thermal resistant |
Kevlar | High strength-to-weight ratio |
Ceramics | High thermal conductivity, hermetic |
Stringent quality standards for aerospace and defense PCBs include:
- IPC 6012 Class 3A
- MIL-PRF-31032
- AS9100 certification
4. Automotive
The automotive industry is a rapidly growing market for PCBs. Modern vehicles incorporate dozens of electronic systems and components that rely on PCBs, such as:
- Engine control units
- Infotainment and navigation systems
- ADAS (advanced driver assistance systems)
- Instrumentation and dashboards
- Lighting and electronic mirrors
- EV battery management systems
Automotive PCBs need to reliably operate in harsh conditions like extreme temperatures, vibration, and exposure to moisture, oils, and corrosive chemicals. They also require long lifecycles of 10-15 years or more.
Standards that apply to automotive PCBs include:
- IATF 16949
- AEC-Q100
- LV 214
- IPC 6012 Class 2
High-temperature laminates are commonly used in automotive PCBs:
Material | Maximum Temp | Applications |
---|---|---|
FR-4 | 130°C | General purpose |
Polyimide | 225°C | Under-hood, lighting |
Copper-clad aluminum | 180°C | Power electronics |
PTFE | 200°C+ | High-frequency, microwave |
5. Telecommunications
PCBs are essential for the operation of telecommunications networks and equipment, including:
- 5G infrastructure
- Fiber optic networks
- Cellular base stations
- Routers and switches
- Satellite communications
High-frequency materials are used to fabricate PCBs for telecom applications operating in the RF and microwave ranges. These laminates have low dielectric loss and precisely controlled dielectric constants. Examples include:
Material | Dk @ 10 GHz | Characteristics |
---|---|---|
PTFE/ceramic | 3.0 – 10.2 | Ultra-low loss, high Temperature |
Hydrocarbon/ceramic | 3.2 – 3.6 | Low loss, low CTE |
BT/epoxy | 3.8 – 4.2 | Low-cost, high Tg |
PCBs for 5G and IoT applications use HDI designs and ultra-fine BGA components. They also increasingly integrate antennas and radios into the board design.
6. Industrial Equipment
PCBs are found in a variety of industrial equipment and systems, such as:
- Factory automation and process control
- Power generation and distribution
- HVAC and building controls
- Instrumentation and measurement devices
- Robotics and CNC machines
Industrial PCBs must withstand harsh operating conditions like extreme temperatures, shock, vibration, and exposure to dust, oil, and chemicals. Reliability and long service life are critical.
Industrial PCBs use materials such as:
Material | Characteristics |
---|---|
High Tg/Td FR-4 | Improved thermal performance |
Epoxy | Chemical resistance |
Aluminum | Thermal dissipation for heatsinks |
Ceramics | High voltage isolation |
Relevant standards for industrial PCBs include:
- UL 508
- UL 840
- UL 94 V-0 flammability
- IPC 6012 Class 3
FAQ
What is the most common type of PCB?
FR-4 glass epoxy laminate is the most widely used material for making PCBs. It is a composite of woven fiberglass cloth and an epoxy resin binder that offers good mechanical and electrical properties at a relatively low cost. FR-4 is used in a wide variety of general purpose applications across all industries.
What are the differences between PCBs for prototyping vs. production?
Prototype PCBs are typically made in small quantities to test and validate a design before moving to high volume production. They may be fabricated using different processes and materials than production boards in order to reduce costs and turnaround times. For example, prototypes may use larger trace widths and clearances or lower-grade laminates.
Production PCBs are manufactured in large quantities once the design is finalized. The focus is on optimizing the design for high yields, reliability, and low cost. High-volume production may use more advanced fabrication technologies and materials, such as HDI processes, copper filled vias, and higher-grade laminates.
What is the most demanding PCB application?
Aerospace and defense applications are typically considered the most demanding for PCBs due to the extreme environmental conditions and high reliability requirements involved. PCBs used in aircraft, spacecraft, and military systems must withstand wide temperature ranges, high altitudes, shock, vibration, and exposure to moisture and chemicals. They also require extensive qualification testing and documentation to meet stringent quality standards.
Medical devices are another demanding application that requires a high degree of reliability and traceability. PCBs used in life-critical medical equipment must provide many years of failure-free operation and meet strict certification standards.
What are the current challenges facing PCB manufacturing?
Some of the main challenges for PCB Manufacturers include:
-
Miniaturization: The trend towards smaller, more compact electronic devices is driving the need for finer pitch components, smaller vias, and thinner PCBs. This requires more advanced manufacturing processes and equipment.
-
High-speed designs: As data rates continue to increase, PCBs must be designed to handle higher frequencies while maintaining signal integrity. This requires careful selection of materials, layout techniques, and design rules.
-
Supply chain disruptions: The COVID-19 pandemic and trade tensions have disrupted the global supply chains for PCB raw materials and components. This has led to longer lead times and higher costs for some PCB manufacturers.
-
Environmental regulations: PCB manufacturers face increasingly strict regulations on the use of hazardous substances like lead, as well as requirements for recycling and disposal of waste products. Complying with these regulations adds costs and complexity to the manufacturing process.
What is the future outlook for the PCB industry?
The global PCB market is expected to continue growing in the coming years, driven by increasing demand for electronic products and the adoption of new technologies. Some key growth areas include:
-
5G and IoT: The rollout of 5G networks and the proliferation of connected devices is driving demand for high-frequency, high-density PCBs.
-
Automotive: The shift towards electric and autonomous vehicles is increasing the electronic content in cars, creating opportunities for automotive PCB manufacturers.
-
Healthcare: The aging population and the demand for smaller, more portable medical devices is driving growth in medical PCBs.
-
Industry 4.0: The adoption of smart factory technologies and industrial IoT is creating demand for more advanced industrial PCBs.
However, the industry also faces challenges such as rising material costs, supply chain disruptions, and increased competition from low-cost manufacturers in Asia. To remain competitive, PCB manufacturers will need to invest in advanced manufacturing technologies, develop new materials and processes, and focus on high-value applications.
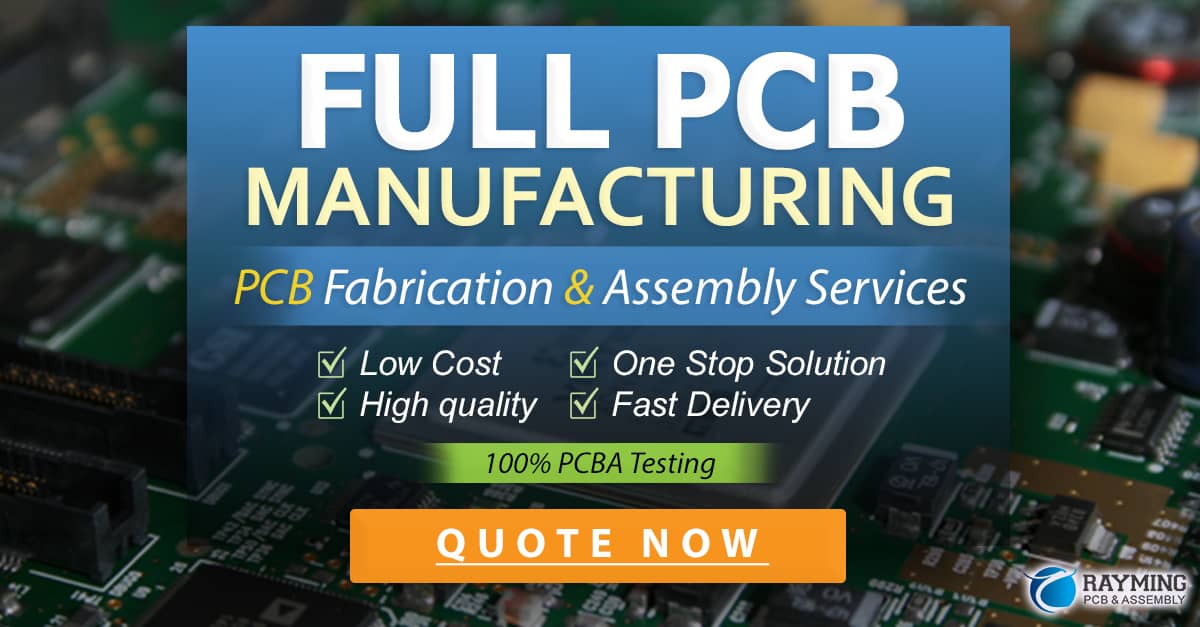
0 Comments