What are IPC Standards and Why Do They Matter for PCBs?
IPC, formerly known as the Institute for Printed Circuits, is a global trade association that develops standards for the electronic interconnection industry. IPC standards cover nearly every aspect of printed circuit board (PCB) design and manufacturing.
IPC standards are voluntary consensus standards that are developed by committees of industry experts. They provide guidelines and requirements for various processes involved in PCB manufacturing, such as design, fabrication, assembly, and testing.
The primary purpose of IPC standards is to ensure the quality, reliability, and consistency of PCBs. By adhering to these standards, PCB manufacturers can produce boards that meet the specific requirements of their customers and are suitable for their intended applications.
Some of the key benefits of using IPC standards in PCB manufacturing include:
- Improved quality and reliability
- Increased consistency and uniformity
- Enhanced communication between designers, manufacturers, and customers
- Reduced costs and time-to-market
- Compliance with industry regulations and requirements
Overview of Key IPC Standards for PCB Manufacturing
There are numerous IPC standards that cover different aspects of PCB manufacturing. Some of the most important ones include:
IPC-2221: Generic Standard on Printed Board Design
IPC-2221 is a generic standard that provides guidelines for the design of printed boards and assemblies. It covers various aspects of PCB design, such as:
- Board layout and routing
- Component placement and spacing
- Hole and via design
- Electrical clearances and creepage distances
- Thermal management
- Manufacturability and testability
IPC-6012: Qualification and Performance Specification for Rigid Printed Boards
IPC-6012 is a specification that defines the requirements for the qualification and performance of rigid printed boards. It covers the following aspects:
- Material requirements
- Dimensional tolerances
- Conductor definition and spacing
- Hole and via requirements
- Surface finish and coating
- Electrical testing
- Visual and mechanical inspection
IPC-A-600: Acceptability of Printed Boards
IPC-A-600 is a pictorial standard that provides visual illustrations and acceptance criteria for various PCB defects and conditions. It is used by PCB manufacturers and customers to determine the acceptability of printed boards based on their visual appearance.
IPC-J-STD-001: Requirements for Soldered Electrical and Electronic Assemblies
IPC-J-STD-001 is a standard that defines the requirements for soldering processes and materials used in the assembly of electronic components on PCBs. It covers the following aspects:
- Soldering processes and techniques
- Solder materials and fluxes
- Component placement and alignment
- Cleanliness and contamination control
- Inspection and testing
The Benefits of Using IPC Standards in PCB Manufacturing
Using IPC standards in PCB manufacturing offers several benefits for both manufacturers and customers. Some of the key benefits include:
1. Improved Quality and Reliability
By adhering to IPC standards, PCB manufacturers can ensure that their products meet the highest quality and reliability requirements. IPC standards provide guidelines for various processes and materials used in PCB manufacturing, which helps to minimize defects and failures.
For example, IPC-A-600 provides visual acceptance criteria for PCBs, which helps manufacturers to identify and correct defects before the boards are shipped to customers. Similarly, IPC-J-STD-001 provides guidelines for soldering processes and materials, which helps to ensure reliable and consistent solder joints.
2. Increased Consistency and Uniformity
IPC standards help to ensure consistency and uniformity across different PCB manufacturers and designs. By following the same guidelines and requirements, manufacturers can produce PCBs that are compatible and interchangeable with each other.
This is particularly important for customers who require PCBs from multiple sources or who need to replace boards in the field. By using IPC standards, they can be assured that the replacement boards will meet the same specifications and performance requirements as the original ones.
3. Enhanced Communication and Collaboration
IPC standards provide a common language and framework for communication between PCB designers, manufacturers, and customers. By using the same terminology and definitions, all parties can easily understand each other’s requirements and expectations.
This helps to reduce misunderstandings and errors, and facilitates collaboration between different teams and organizations. For example, a PCB designer can use IPC-2221 to communicate their design intent to the manufacturer, who can then use IPC-6012 to ensure that the finished product meets the specified requirements.
4. Reduced Costs and Time-to-Market
Using IPC standards can help to reduce costs and time-to-market for PCB manufacturing. By following established guidelines and best practices, manufacturers can optimize their processes and avoid costly mistakes and rework.
For example, by using IPC-2221 to design for manufacturability, designers can avoid potential issues that could delay production or increase costs. Similarly, by using IPC-J-STD-001 to ensure reliable soldering processes, manufacturers can reduce the risk of board failures and returns.
5. Compliance with Industry Regulations and Requirements
Many industries have specific regulations and requirements for PCBs used in their products. For example, the automotive industry requires PCBs to meet strict reliability and environmental standards, while the aerospace industry has specific requirements for materials and processes used in PCB manufacturing.
By using IPC standards, PCB manufacturers can ensure that their products comply with these industry-specific requirements. This can help them to access new markets and customers, and avoid potential legal and financial liabilities.
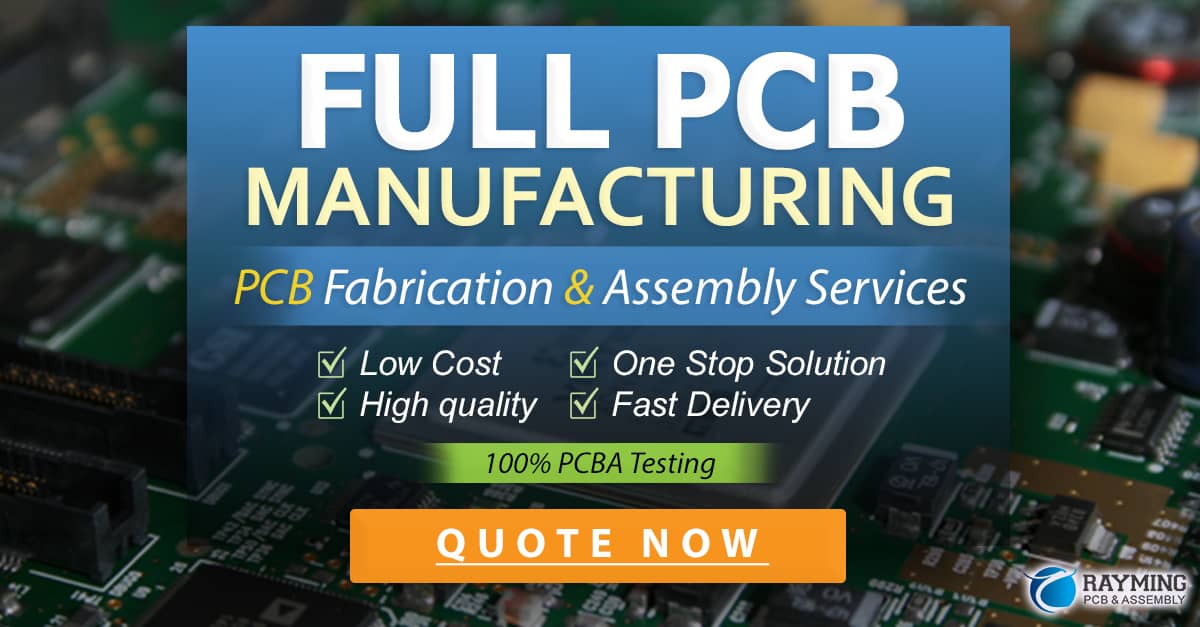
Common Challenges in Implementing IPC Standards
While using IPC standards offers many benefits for PCB manufacturing, there are also some challenges that manufacturers may face in implementing them. Some of the common challenges include:
1. Cost and Resource Constraints
Implementing IPC standards can require significant investments in equipment, materials, and training. For example, meeting the requirements of IPC-6012 may require specialized testing equipment and trained personnel to perform the necessary inspections and tests.
Small and medium-sized manufacturers may struggle to justify these costs, especially if they are not seeing immediate returns on their investments. However, the long-term benefits of using IPC standards, such as improved quality and reliability, can often outweigh the initial costs.
2. Resistance to Change
Some manufacturers may be resistant to changing their existing processes and practices to meet IPC standards. This can be particularly challenging for those who have been using their own internal standards or have long-established relationships with customers who may not require IPC compliance.
To overcome this resistance, manufacturers may need to educate their employees and customers about the benefits of using IPC standards, and demonstrate how they can improve quality, reliability, and customer satisfaction in the long run.
3. Lack of Understanding or Expertise
Implementing IPC standards requires a deep understanding of the various requirements and guidelines involved. Some manufacturers may lack the necessary expertise or resources to properly interpret and apply these standards to their processes.
This can lead to inconsistencies or errors in the finished products, which can negatively impact quality and reliability. To address this challenge, manufacturers may need to invest in training and education for their employees, or seek guidance from IPC-certified experts or consultants.
FAQ
1. What is the difference between IPC and other PCB standards?
IPC standards are widely recognized and accepted in the electronics industry, and cover a broad range of topics related to PCB design, fabrication, assembly, and testing. Other standards, such as those developed by individual companies or industry groups, may be more specific to certain applications or regions.
2. Do all PCB manufacturers need to follow IPC standards?
While IPC standards are voluntary, many customers and industries require PCBs to be manufactured in accordance with these standards. Manufacturers who do not follow IPC standards may face challenges in winning new business or meeting customer requirements.
3. How can PCB designers ensure their designs meet IPC standards?
PCB designers can use IPC-2221 as a guideline for their designs, and work closely with their manufacturing partners to ensure that their designs are compatible with the specific processes and capabilities of the manufacturer. They can also use design for manufacturability (DFM) tools and techniques to optimize their designs for reliability and manufacturability.
4. What happens if a PCB does not meet IPC standards?
If a PCB does not meet the specified IPC standards, it may be rejected by the customer or fail to perform as intended in the field. This can lead to costly rework, delays, and potential liability issues for the manufacturer. In some cases, non-compliant PCBs may also violate industry regulations or safety requirements.
5. How can PCB manufacturers ensure consistent compliance with IPC standards?
PCB manufacturers can ensure consistent compliance with IPC standards by implementing robust quality management systems, training their employees on the specific requirements and best practices, and regularly auditing their processes and products against the relevant standards. They can also seek IPC certification to demonstrate their commitment to quality and reliability.
In conclusion, IPC standards play a critical role in ensuring the quality, reliability, and consistency of PCBs used in a wide range of applications. By adhering to these standards, PCB manufacturers can improve their processes, reduce costs and time-to-market, and meet the specific requirements of their customers and industries.
While implementing IPC standards can present some challenges, the benefits of using these standards far outweigh the costs and efforts involved. As the electronics industry continues to evolve and become more complex, the importance of IPC standards will only continue to grow, making them an essential tool for PCB manufacturers who want to stay competitive and succeed in the global marketplace.
0 Comments