What is FCT Testing?
FCT (Functional Circuit Testing) is a crucial step in the PCB (Printed Circuit Board) manufacturing and assembly process. It involves testing the functionality of the assembled PCB to ensure that it meets the required specifications and performs as intended. FCT testing is typically performed after the PCB has been assembled and before it is shipped to the customer.
Types of FCT Testing
There are several types of FCT testing that can be performed, depending on the complexity of the PCB and the specific requirements of the customer. Some of the most common types of FCT testing include:
Test Type | Description |
---|---|
In-Circuit Testing (ICT) | Involves testing individual components on the PCB to ensure that they are functioning correctly and are properly connected. |
Flying Probe Testing | Uses mobile probes to test specific points on the PCB for continuity, resistance, and other parameters. |
Boundary Scan Testing | Uses a special test access port (TAP) to test the interconnections between components on the PCB. |
Functional Testing | Involves testing the overall functionality of the PCB to ensure that it meets the required specifications. |
Benefits of FCT Testing
FCT testing offers several benefits to PCB manufacturers and their customers, including:
-
Early detection of defects: FCT testing allows manufacturers to detect defects early in the manufacturing process, before the PCB is shipped to the customer. This can help to reduce the cost and time associated with rework and repairs.
-
Improved quality: By ensuring that each PCB meets the required specifications and performs as intended, FCT testing helps to improve the overall quality of the finished product.
-
Reduced warranty claims: By catching defects before the PCB is shipped, FCT testing can help to reduce the number of warranty claims and returns from customers.
-
Increased customer satisfaction: By delivering high-quality PCBs that meet the required specifications and perform as intended, manufacturers can increase customer satisfaction and build long-term relationships with their clients.
The FCT Testing Process
The FCT testing process typically involves several steps, including:
1. Test Planning
The first step in the FCT testing process is to plan the tests that will be performed on the PCB. This involves reviewing the PCB design, identifying the critical components and functions that need to be tested, and determining the appropriate test methods and equipment.
2. Test Fixture Design
Once the test plan has been developed, the next step is to design the test fixture that will be used to hold the PCB during testing. The test fixture must be designed to provide access to all of the test points on the PCB and to ensure that the PCB is held securely in place during testing.
3. Test Program Development
The test program is the software that controls the test equipment and executes the tests on the PCB. The test program must be developed to match the specific requirements of the PCB and the test plan.
4. Test Execution
Once the test fixture and test program have been developed, the next step is to execute the tests on the PCB. This involves placing the PCB in the test fixture, connecting the test equipment, and running the test program.
5. Results Analysis
After the tests have been executed, the results must be analyzed to determine whether the PCB has passed or failed. If the PCB fails the tests, the manufacturer must determine the root cause of the failure and take corrective action to fix the problem.
Common FCT Testing Challenges
While FCT testing is an essential part of the PCB manufacturing process, it can also present several challenges, including:
1. Complex PCB Designs
As PCBs become more complex and include more components and functions, FCT testing becomes more challenging. Manufacturers must develop more sophisticated test fixtures and programs to accommodate these complex designs.
2. High-Density PCBs
High-density PCBs, which include a large number of components in a small area, can be difficult to test using traditional methods. Manufacturers may need to use specialized equipment, such as flying probe testers, to access the test points on these boards.
3. Customized Test Requirements
Some customers may have specific test requirements that are not covered by standard FCT testing methods. In these cases, manufacturers may need to develop custom test fixtures and programs to meet the customer’s needs.
4. Time and Cost Constraints
FCT testing can be a time-consuming and expensive process, particularly for complex PCBs or high-volume production runs. Manufacturers must balance the need for thorough testing with the need to meet production schedules and control costs.
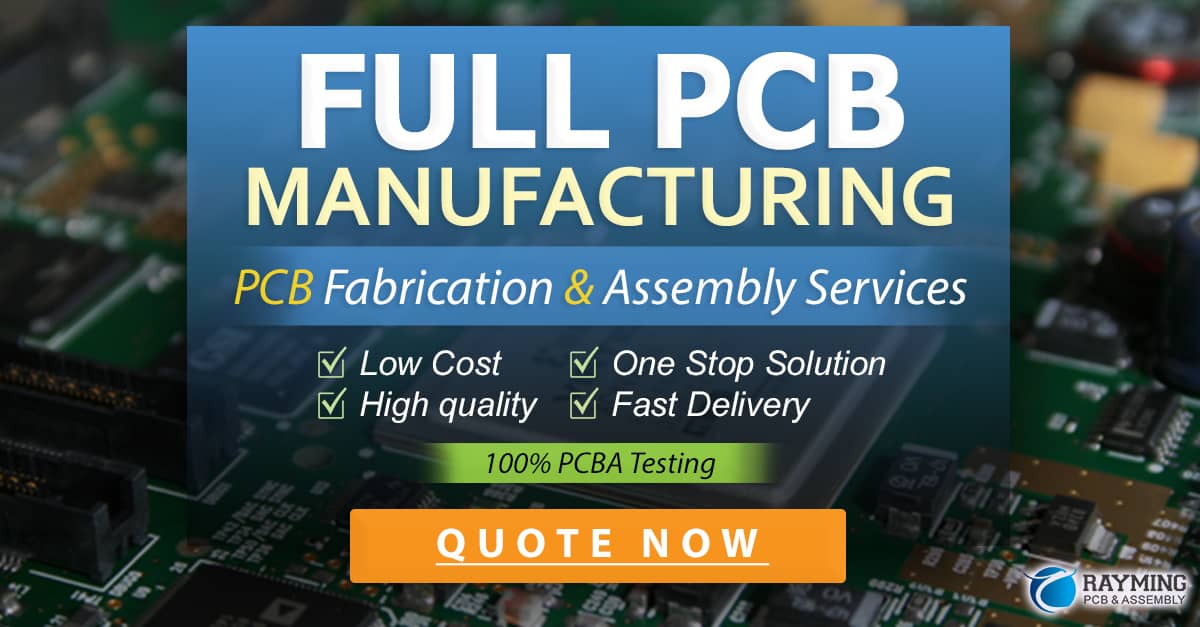
Best Practices for FCT Testing
To ensure effective and efficient FCT testing, manufacturers should follow these best practices:
-
Develop a comprehensive test plan: The test plan should cover all of the critical components and functions of the PCB and should be based on the specific requirements of the customer.
-
Use appropriate test methods and equipment: Manufacturers should select the appropriate test methods and equipment based on the complexity of the PCB and the specific test requirements.
-
Design for testability: PCB designers should consider testability when developing the board layout and component selection. This can help to reduce the complexity and cost of FCT testing.
-
Implement quality control measures: Manufacturers should implement quality control measures throughout the FCT testing process to ensure that the tests are performed consistently and accurately.
-
Continuously improve the process: Manufacturers should continuously monitor and analyze the FCT testing process to identify opportunities for improvement and to ensure that the process remains effective and efficient.
Frequently Asked Questions (FAQ)
1. What is the difference between FCT testing and other types of PCB testing?
FCT testing focuses on the functionality of the assembled PCB, while other types of testing, such as in-circuit testing (ICT) and flying probe testing, focus on individual components or specific points on the PCB.
2. How long does FCT testing typically take?
The duration of FCT testing depends on the complexity of the PCB and the specific test requirements. Simple PCBs may only require a few minutes of testing, while more complex boards may require several hours or even days.
3. Can FCT testing be performed on prototype PCBs?
Yes, FCT testing can be performed on prototype PCBs to verify the design and functionality of the board before moving to full production.
4. What happens if a PCB fails FCT testing?
If a PCB fails FCT testing, the manufacturer must determine the root cause of the failure and take corrective action to fix the problem. This may involve reworking the PCB, replacing components, or modifying the manufacturing process.
5. How much does FCT testing cost?
The cost of FCT testing varies depending on the complexity of the PCB, the specific test requirements, and the volume of boards being tested. Manufacturers should work with their customers to develop a cost-effective testing strategy that meets the customer’s needs while controlling costs.
Conclusion
FCT testing is a critical step in the PCB manufacturing and assembly process that helps to ensure the functionality and quality of the finished product. By detecting defects early in the process, reducing warranty claims, and improving customer satisfaction, FCT testing provides significant benefits to both manufacturers and their customers.
To ensure effective and efficient FCT testing, manufacturers should develop a comprehensive test plan, use appropriate test methods and equipment, design for testability, implement quality control measures, and continuously improve the process. By following these best practices, manufacturers can deliver high-quality PCBs that meet the required specifications and perform as intended.
0 Comments