What is Wave Soldering?
Wave soldering is a soldering technique that involves passing a PCB over a molten solder wave to create electrical connections between components and the board. The process begins by applying a layer of flux to the bottom side of the PCB, which helps to remove oxides and improve solder wettability. The board is then placed on a conveyor belt that carries it over a tank of molten solder. As the board passes over the solder wave, the molten solder adheres to the exposed metal surfaces, creating a strong and reliable connection.
Advantages of Wave Soldering
- High throughput: Wave soldering is a fast process that can handle large volumes of PCBs, making it ideal for high-volume production runs.
- Versatility: Wave soldering can accommodate a wide range of component types, including through-hole components and some surface mount devices (SMDs).
- Cost-effective: Wave soldering is generally less expensive than reflow soldering, as it requires fewer specialized equipment and materials.
Disadvantages of Wave Soldering
- Limited compatibility with SMDs: While wave soldering can handle some SMDs, it is not well-suited for smaller or more delicate components, which can be damaged by the solder wave.
- Thermal shock: The high temperature of the molten solder can cause thermal shock to sensitive components, potentially leading to damage or failure.
- Solder bridging: Wave soldering can sometimes result in solder bridging, where excess solder creates unintended connections between adjacent pins or pads.
What is Reflow Soldering?
Reflow soldering is a soldering technique that involves applying solder paste to the PCB, placing components onto the paste, and then heating the entire assembly in a reflow oven to melt the solder and create a strong bond between the components and the board. The solder paste used in reflow soldering is a mixture of tiny solder particles suspended in a flux medium, which helps to remove oxides and improve solder wettability.
Advantages of Reflow Soldering
- Compatibility with SMDs: Reflow soldering is the preferred method for soldering SMDs, as it can handle smaller and more delicate components without causing damage.
- Precision: Reflow soldering allows for precise control over the amount of solder applied to each connection, reducing the risk of solder bridging or insufficient solder joints.
- Automation: Reflow soldering is a highly automated process, with pick-and-place machines for component placement and conveyor-based reflow ovens for heating the assembly.
Disadvantages of Reflow Soldering
- Higher equipment costs: Reflow soldering requires specialized equipment, such as solder paste printers, pick-and-place machines, and reflow ovens, which can be more expensive than wave soldering equipment.
- Limited compatibility with through-hole components: Reflow soldering is not well-suited for through-hole components, which require a separate wave soldering process or manual soldering.
- Thermal profiling: Reflow soldering requires careful thermal profiling to ensure that the solder paste is heated to the correct temperature and for the right duration to create a strong bond without damaging the components.
Comparing Wave Soldering and Reflow Soldering
To better understand the differences between wave soldering and reflow soldering, let’s compare them side by side:
Characteristic | Wave Soldering | Reflow Soldering |
---|---|---|
Solder application | Molten solder wave | Solder paste |
Component compatibility | Through-hole and some SMDs | SMDs |
Process speed | High throughput | Slower than wave soldering |
Equipment cost | Lower | Higher |
Precision | Lower | Higher |
Thermal shock risk | Higher | Lower |
Solder bridging risk | Higher | Lower |
Automation | Partially automated | Highly automated |
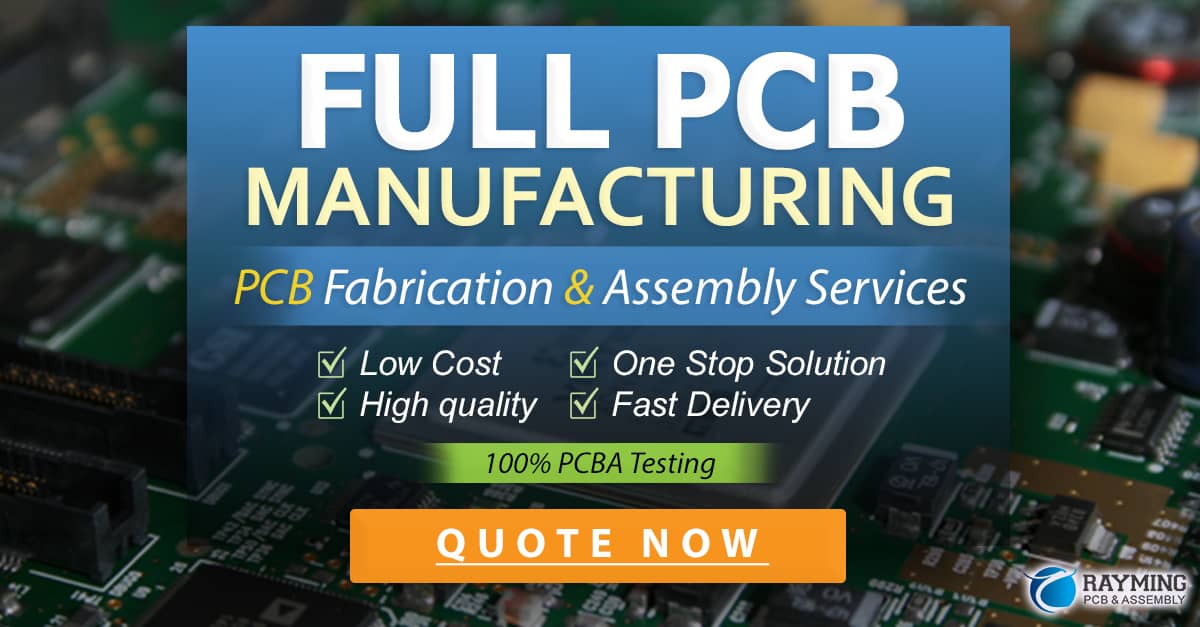
When to Use Wave Soldering or Reflow Soldering
The choice between wave soldering and reflow soldering depends on several factors, including the types of components being used, the production volume, and the available budget. Here are some general guidelines for when to use each method:
Use Wave Soldering When:
- The PCB contains primarily through-hole components.
- The production volume is high, and speed is a priority.
- The budget for equipment is limited.
- The PCB design can accommodate the limitations of wave soldering, such as larger component spacing and solder mask design.
Use Reflow Soldering When:
- The PCB contains primarily SMDs.
- The components are small, delicate, or have fine pitch leads.
- Precision and consistency are critical for the application.
- The production volume is lower, or the budget allows for the higher equipment costs.
- The PCB design is optimized for reflow soldering, with appropriate solder mask and pad designs.
Frequently Asked Questions (FAQ)
-
Can wave soldering and reflow soldering be used together on the same PCB?
Yes, it is possible to use both wave soldering and reflow soldering on the same PCB. This is known as a mixed-technology assembly, where through-hole components are wave soldered, and SMDs are reflow soldered. However, this requires careful planning and design to ensure compatibility between the two processes. -
What is selective soldering, and how does it relate to wave soldering?
Selective soldering is a variation of wave soldering that targets specific areas of the PCB, rather than the entire board. This is achieved using a miniature solder wave or a laser soldering system. Selective soldering is useful for PCBs with a mix of through-hole and SMDs, where the SMDs are reflow soldered, and the through-hole components are selectively soldered to avoid damage. -
What is the role of flux in wave soldering and reflow soldering?
Flux plays a critical role in both wave soldering and reflow soldering by removing oxides from the metal surfaces and improving solder wettability. In wave soldering, liquid flux is applied to the bottom side of the PCB before it passes over the solder wave. In reflow soldering, the flux is already mixed into the solder paste applied to the PCB before component placement. -
How does the solder joint quality differ between wave soldering and reflow soldering?
Reflow soldering generally produces higher-quality solder joints compared to wave soldering, as it allows for more precise control over the amount of solder applied and the heating process. Wave soldering can sometimes result in solder bridging or insufficient solder joints due to the nature of the solder wave and the limited control over the process. -
Can reflow soldering be used for rework or repair of PCBs?
Yes, reflow soldering can be used for rework or repair of PCBs, but it requires specialized equipment and techniques. Localized heating methods, such as hot air pencils or focused infrared systems, can be used to reflow specific components without affecting the rest of the board. However, rework and repair using reflow soldering can be more challenging and time-consuming compared to manual soldering methods.
Conclusion
Wave soldering and reflow soldering are two essential techniques used in the electronic manufacturing industry for creating reliable and durable connections between components and PCBs. While both methods have their advantages and disadvantages, the choice between them depends on factors such as the types of components being used, the production volume, and the available budget.
Wave soldering is better suited for high-volume production of PCBs with primarily through-hole components, while reflow soldering is the preferred method for boards with SMDs and where precision and consistency are critical. Understanding the differences between these two soldering techniques can help electronic manufacturers make informed decisions when designing and assembling PCBs, ultimately leading to higher-quality products and more efficient production processes.
0 Comments