What is an FPGA?
An FPGA is a type of integrated circuit that can be programmed and reprogrammed after manufacturing to implement various digital logic functions. FPGAs consist of an array of programmable logic blocks, interconnected through a hierarchy of reconfigurable interconnects. These logic blocks can be configured to perform combinational functions (e.g., AND, OR, XOR) or sequential functions (e.g., flip-flops, latches) by loading a configuration bitstream into the FPGA.
The key features of FPGAs include:
- Programmability: FPGAs can be programmed using hardware description languages (HDLs) like VHDL or Verilog.
- Reconfigurability: The functionality of an FPGA can be modified by loading a new configuration bitstream, allowing for design changes and updates.
- Parallel processing: FPGAs can exploit parallelism by executing multiple operations simultaneously.
- Rapid prototyping: FPGAs enable fast iterative development and testing of hardware designs.
What is an ASIC?
An ASIC is a customized integrated circuit designed for a specific application or purpose. Unlike FPGAs, ASICs are manufactured with a fixed functionality that cannot be altered after fabrication. ASICs are designed using HDLs and then go through a complex manufacturing process involving multiple steps such as synthesis, placement, routing, and fabrication.
The key features of ASICs include:
- High performance: ASICs offer superior performance compared to FPGAs due to their customized and optimized design.
- Low power consumption: ASICs consume less power than FPGAs as they are tailored for a specific function.
- Small form factor: ASICs can be designed to have a smaller footprint compared to FPGAs.
- High upfront costs: The design and manufacturing process of ASICs is expensive and time-consuming.
FPGA vs ASIC: Key Differences
1. Architecture
The architecture of FPGAs and ASICs differs significantly. FPGAs consist of a matrix of programmable logic blocks and interconnects that can be configured to implement various digital functions. The programmable nature of FPGAs allows for flexibility and reconfigurability.
On the other hand, ASICs have a fixed architecture that is custom-designed for a specific application. The logic gates, interconnects, and other components in an ASIC are optimized and hardwired during the manufacturing process. This fixed architecture provides high performance and power efficiency but lacks the flexibility of FPGAs.
2. Design Process
The design process for FPGAs and ASICs varies in terms of complexity, time, and cost.
Designing an FPGA involves the following steps:
1. HDL design entry: The desired functionality is described using HDLs like VHDL or Verilog.
2. Synthesis: The HDL code is synthesized into a netlist representing the logic gates and their connections.
3. Place and route: The synthesized design is mapped onto the FPGA’s programmable logic blocks and interconnects.
4. Bitstream generation: A configuration bitstream is generated to program the FPGA.
The FPGA design process is relatively fast and iterative, allowing for quick prototyping and design modifications.
In contrast, the ASIC design process is more complex and involves the following steps:
1. HDL design entry: Similar to FPGAs, the functionality is described using HDLs.
2. Synthesis: The HDL code is synthesized into a gate-level netlist.
3. Physical design: The netlist undergoes floorplanning, placement, and routing to create a physical layout.
4. Verification: The design is thoroughly verified through simulations and formal verification techniques.
5. Fabrication: The verified design is sent for manufacturing, which involves mask generation and wafer fabrication.
The ASIC design process is time-consuming and expensive due to the custom manufacturing steps involved.
3. Cost
The cost structure of FPGAs and ASICs differs significantly. FPGAs have lower upfront costs as they are off-the-shelf components that can be purchased and programmed by the user. The cost of an FPGA depends on factors such as the number of logic elements, memory resources, and I/O pins. However, for high-volume production, the per-unit cost of FPGAs can be higher compared to ASICs.
ASICs, on the other hand, have high upfront costs associated with custom design and manufacturing. The non-recurring engineering (NRE) costs for ASICs, which include mask generation and fabrication setup, can run into millions of dollars. However, for high-volume production, the per-unit cost of ASICs becomes significantly lower than FPGAs.
The following table compares the cost aspects of FPGAs and ASICs:
Cost Aspect | FPGA | ASIC |
---|---|---|
Upfront Costs | Lower | High (NRE costs) |
Per-unit Cost | Higher for high-volume production | Lower for high-volume production |
Design Cost | Lower (faster design cycle) | Higher (complex design process) |
Time-to-Market | Faster | Slower |
Economies of Scale | Not significant | Significant for high volumes |
4. Performance
Performance is a critical factor when choosing between FPGAs and ASICs. ASICs offer superior performance compared to FPGAs due to their custom-designed and optimized architecture. ASICs can achieve higher clock speeds, lower latency, and higher throughput because the logic gates and interconnects are hardwired for a specific function.
FPGAs, while offering flexibility, have lower performance compared to ASICs. The programmable nature of FPGAs introduces additional delays and overhead due to the configuration logic and interconnects. However, modern high-end FPGAs have made significant strides in terms of performance, narrowing the gap with ASICs.
The following table compares the performance aspects of FPGAs and ASICs:
Performance Aspect | FPGA | ASIC |
---|---|---|
Clock Speed | Lower | Higher |
Latency | Higher | Lower |
Throughput | Lower | Higher |
Power Efficiency | Lower | Higher |
Parallel Processing | Exploits parallelism | Exploits parallelism |
5. Flexibility
Flexibility is a key differentiator between FPGAs and ASICs. FPGAs offer high flexibility as they can be reprogrammed and reconfigured after manufacturing. This allows for design changes, bug fixes, and feature upgrades without the need for hardware modifications. FPGAs are ideal for applications that require adaptability, rapid prototyping, or frequent design iterations.
ASICs, on the other hand, have fixed functionality once they are manufactured. Any changes to the design require a new manufacturing cycle, which is costly and time-consuming. ASICs are suitable for applications with stable requirements and high-volume production, where the functionality is unlikely to change.
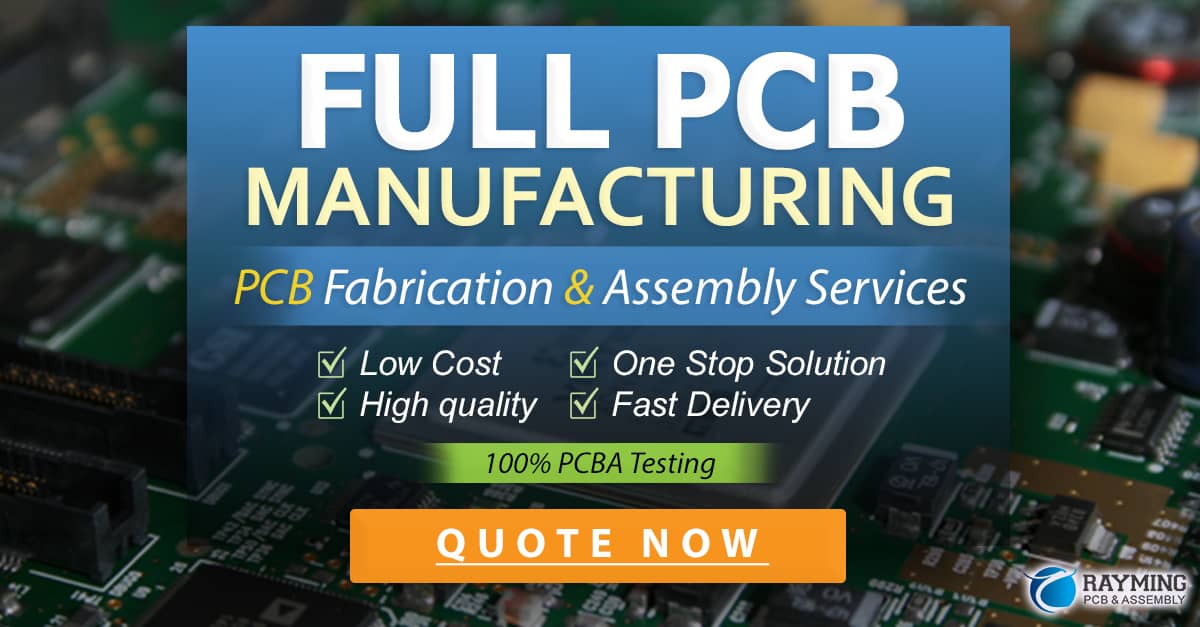
Applications of FPGAs and ASICs
FPGAs and ASICs find applications in various domains, each leveraging their unique characteristics. Some common applications include:
FPGA Applications
- Prototyping and proof-of-concept designs
- Digital signal processing (DSP) systems
- Software-defined radio (SDR)
- Automotive and aerospace systems
- Industrial control and automation
- Network switches and routers
- Cryptography and security applications
ASIC Applications
- High-volume consumer electronics (e.g., smartphones, gaming consoles)
- Application-specific processors (e.g., GPUs, AI accelerators)
- Wireless communication devices (e.g., baseband processors)
- Sensors and IoT devices
- Cryptographic hardware wallets
- Medical devices and implantable systems
Frequently Asked Questions (FAQ)
1. Can an FPGA be converted to an ASIC?
Yes, it is possible to convert an FPGA design to an ASIC. This process is known as FPGA-to-ASIC conversion or ASIC prototyping. It involves optimizing the FPGA design, synthesizing it for ASIC technology, and going through the ASIC manufacturing process. However, the conversion process requires additional effort and expertise to ensure the ASIC meets the required performance, power, and area constraints.
2. Are FPGAs cheaper than ASICs?
The cost comparison between FPGAs and ASICs depends on the production volume and the specific application. For low to medium volumes, FPGAs are generally cheaper due to their lower upfront costs and faster time-to-market. However, for high-volume production, ASICs become more cost-effective as the per-unit cost decreases significantly, offsetting the high NRE costs.
3. Can FPGAs be used for high-performance computing?
Yes, FPGAs can be used for high-performance computing applications. Modern high-end FPGAs offer significant computational power and can be used as accelerators for complex algorithms, such as machine learning, data analytics, and scientific simulations. FPGAs can provide high parallelism and energy efficiency compared to general-purpose processors.
4. What is the typical design cycle for FPGAs and ASICs?
The design cycle for FPGAs is typically faster compared to ASICs. FPGA designs can be developed, simulated, and verified within a few weeks to months, depending on the complexity of the design. The ability to reprogram FPGAs allows for quick iterations and modifications.
In contrast, the design cycle for ASICs is longer and can take several months to a year or more. The ASIC design process involves complex steps such as synthesis, physical design, verification, and fabrication, which contribute to the longer design cycle.
5. Can ASICs be reprogrammed like FPGAs?
No, ASICs cannot be reprogrammed like FPGAs. Once an ASIC is manufactured, its functionality is fixed and cannot be modified. If changes are required, a new ASIC design must be developed, and the manufacturing process must be repeated. This inflexibility is one of the main drawbacks of ASICs compared to FPGAs.
Conclusion
FPGAs and ASICs are two distinct approaches to implementing digital logic circuits, each with its own strengths and weaknesses. FPGAs offer flexibility, reconfigurability, and faster time-to-market, making them suitable for prototyping, low-volume production, and applications that require adaptability. On the other hand, ASICs provide superior performance, power efficiency, and lower per-unit costs for high-volume production, but at the expense of higher upfront costs and longer design cycles.
Choosing between an FPGA and an ASIC depends on various factors such as the application requirements, production volume, development time, and budget constraints. In some cases, a combination of both technologies can be used, where an FPGA is employed for prototyping and initial development, followed by an ASIC implementation for mass production.
As technology advances, the boundaries between FPGAs and ASICs continue to blur. Modern FPGAs are becoming more powerful and efficient, while advancements in ASIC design tools and methodologies are reducing the development time and costs. Ultimately, understanding the differences between FPGAs and ASICs and carefully evaluating the project requirements will help in making an informed decision and selecting the most appropriate solution.
0 Comments