What is PCB Soldermask?
PCB soldermask, also known as solder resist or solder mask, is a thin layer of polymer applied to the copper traces of a printed circuit board (PCB). Its primary purpose is to protect the copper traces from oxidation, prevent solder bridges from forming between closely spaced pads, and provide electrical insulation. Soldermask also serves as a barrier against environmental contaminants and improves the overall durability of the PCB.
Types of PCB Soldermask
There are two main types of soldermask used in PCB manufacturing:
-
Liquid PhotoImageable (LPI) Soldermask: This type of soldermask is applied as a liquid and then exposed to UV light through a photomask, hardening the exposed areas. LPI soldermask offers excellent resolution and is suitable for fine-pitch components.
-
Dry Film Soldermask: Dry film soldermask is a solid film that is laminated onto the PCB surface using heat and pressure. It is then exposed to UV light and developed, similar to the LPI process. Dry film soldermask is more durable and provides better chemical resistance compared to LPI.
Common Problems with PCB Soldermask
Despite its essential role in PCB manufacturing, soldermask can present several challenges and issues. Here are some of the most common problems encountered with PCB soldermask:
1. Soldermask Cracking
Soldermask cracking occurs when the soldermask layer becomes brittle and develops cracks, exposing the underlying copper traces. This can happen due to various factors, such as:
- Excessive thickness of the soldermask layer
- Improper curing of the soldermask
- Mechanical stress during the assembly process
- Thermal stress during soldering or operation
To prevent soldermask cracking, it is essential to:
- Control the Soldermask Thickness to the recommended range (typically 0.8-1.2 mils)
- Ensure proper curing of the soldermask by following the manufacturer’s guidelines
- Use a flexible soldermask material that can withstand mechanical and thermal stress
- Avoid excessive handling or bending of the PCB during assembly
2. Soldermask Adhesion Issues
Poor adhesion between the soldermask and the copper surface can lead to delamination, exposing the copper traces to oxidation and contamination. Factors that contribute to soldermask adhesion issues include:
- Inadequate surface cleaning before applying soldermask
- Incompatibility between the soldermask and the surface finish (e.g., ENIG, HASL)
- Insufficient curing of the soldermask
- Contamination of the copper surface
To improve soldermask adhesion:
- Thoroughly clean the copper surface using a micro-etch or plasma treatment before applying soldermask
- Select a soldermask that is compatible with the chosen surface finish
- Follow the manufacturer’s recommendations for curing time and temperature
- Maintain a clean and contamination-free environment during PCB manufacturing
3. Soldermask Peeling
Soldermask peeling refers to the lifting or separation of the soldermask layer from the copper surface, usually along the edges of pads or traces. This can be caused by:
- Poor adhesion between the soldermask and copper
- Mechanical stress during the assembly process
- Thermal shock during soldering
- Incompatibility with certain cleaning agents or solvents
To minimize soldermask peeling:
- Ensure good adhesion between the soldermask and copper surface
- Use a soldermask with high peel strength and flexibility
- Avoid excessive mechanical stress during assembly
- Control the soldering temperature and duration to prevent thermal shock
- Select cleaning agents and solvents that are compatible with the soldermask material
4. Soldermask Discoloration
Soldermask discoloration is a cosmetic issue that can occur over time due to exposure to UV light, high temperatures, or certain chemicals. While it does not directly affect the functionality of the PCB, it can be a concern for some applications where appearance is critical.
To prevent soldermask discoloration:
- Choose a soldermask with good UV and thermal stability
- Avoid prolonged exposure to high temperatures during storage or operation
- Use UV-resistant additives in the soldermask formulation
- Select cleaning agents and solvents that do not cause discoloration
5. Soldermask Voids
Soldermask voids are small holes or gaps in the soldermask layer that expose the underlying copper. These voids can be caused by:
- Air bubbles trapped during the soldermask application process
- Contamination on the copper surface preventing proper adhesion
- Insufficient soldermask coverage in certain areas
To minimize soldermask voids:
- Ensure proper mixing and degassing of the soldermask before application
- Maintain a clean and contamination-free copper surface
- Use a soldermask with good flow properties to achieve uniform coverage
- Optimize the soldermask application process to minimize air entrapment
Solutions for PCB Soldermask Problems
To address the common problems associated with PCB soldermask, manufacturers can implement various solutions:
1. Material Selection
Choosing the right soldermask material is crucial for preventing issues like cracking, peeling, and discoloration. Consider the following factors when selecting a soldermask:
- Compatibility with the surface finish and other materials used in the PCB
- Flexibility and peel strength to withstand mechanical and thermal stress
- UV and thermal stability for long-term durability
- Recommended thickness range for optimal performance
Some of the most common soldermask materials include:
Material | Description | Key Properties |
---|---|---|
LPI Soldermask | Liquid photoimageable soldermask applied as a liquid and cured with UV light | Excellent resolution, suitable for fine-pitch components |
Dry Film Soldermask | Solid film soldermask laminated onto the PCB surface and cured with UV light | High durability, good chemical resistance |
Epoxy Soldermask | Two-part epoxy system that cures through a chemical reaction | Excellent adhesion, high chemical resistance |
Acrylic Soldermask | UV-curable acrylic-based soldermask with good flexibility | Good thermal stability, suitable for high-temperature applications |
2. Process Optimization
Optimizing the soldermask application and curing process can help minimize issues like voids, poor adhesion, and insufficient coverage. Key process parameters to control include:
- Soldermask thickness: Maintain the recommended thickness range (0.8-1.2 mils) for optimal performance
- Curing conditions: Follow the manufacturer’s guidelines for curing time, temperature, and UV exposure
- Surface preparation: Ensure proper cleaning and treatment of the copper surface before applying soldermask
- Application method: Use a consistent and controlled method for applying soldermask, such as screen printing or spray coating
3. Quality Control
Implementing strict quality control measures throughout the PCB manufacturing process can help identify and prevent soldermask issues. Some essential quality control steps include:
- Incoming material inspection: Verify the quality and consistency of the soldermask material before use
- Process monitoring: Regularly monitor and document key process parameters, such as soldermask thickness, curing conditions, and surface cleanliness
- Visual inspection: Conduct visual inspections of the soldermask layer for defects like cracks, voids, peeling, or discoloration
- Adhesion testing: Perform peel strength tests to ensure adequate adhesion between the soldermask and copper surface
- Thermal cycling: Subject PCBs to thermal cycling tests to evaluate the soldermask’s ability to withstand temperature fluctuations
4. Design Considerations
Incorporating certain design considerations can help minimize the risk of soldermask issues:
- Pad and trace spacing: Ensure adequate spacing between pads and traces to prevent solder bridging and allow for proper soldermask coverage
- Soldermask expansion: Account for soldermask expansion during the design phase to avoid issues like soldermask cracking or peeling
- Soldermask relief: Provide sufficient soldermask relief around pads and vias to ensure proper solder wetting and prevent soldermask from interfering with the soldering process
- Component placement: Consider the placement of components to minimize mechanical stress on the soldermask layer during assembly
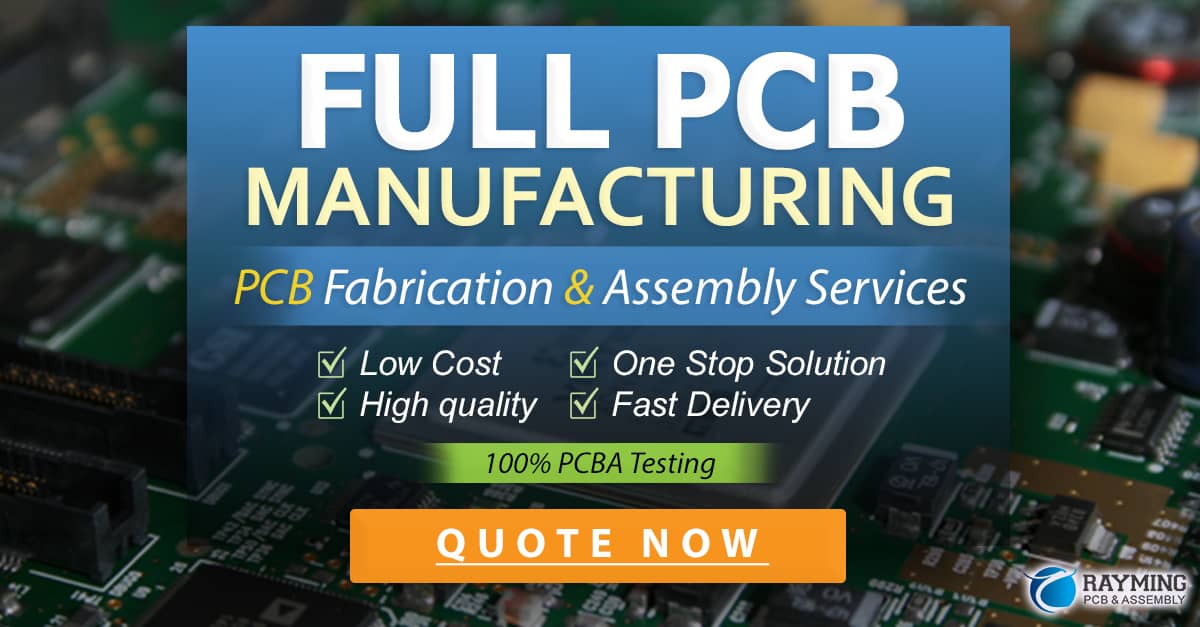
Frequently Asked Questions (FAQ)
1. What is the purpose of soldermask on a PCB?
Soldermask serves several purposes on a PCB, including:
– Protecting the copper traces from oxidation and contamination
– Preventing solder bridges from forming between closely spaced pads
– Providing electrical insulation between conductive areas
– Improving the overall durability and reliability of the PCB
2. What are the most common types of soldermask used in PCB manufacturing?
The two most common types of soldermask used in PCB manufacturing are:
1. Liquid PhotoImageable (LPI) Soldermask: Applied as a liquid and cured with UV light, offering excellent resolution for fine-pitch components.
2. Dry Film Soldermask: A solid film laminated onto the PCB surface and cured with UV light, providing high durability and chemical resistance.
3. How can I prevent soldermask cracking on my PCBs?
To prevent soldermask cracking, you can:
– Control the soldermask thickness to the recommended range (0.8-1.2 mils)
– Ensure proper curing of the soldermask by following the manufacturer’s guidelines
– Use a flexible soldermask material that can withstand mechanical and thermal stress
– Avoid excessive handling or bending of the PCB during assembly
4. What causes soldermask peeling, and how can it be minimized?
Soldermask peeling can be caused by poor adhesion, mechanical stress, thermal shock, or incompatibility with certain cleaning agents or solvents. To minimize peeling:
– Ensure good adhesion between the soldermask and copper surface
– Use a soldermask with high peel strength and flexibility
– Avoid excessive mechanical stress during assembly
– Control the soldering temperature and duration to prevent thermal shock
– Select cleaning agents and solvents that are compatible with the soldermask material
5. How can I choose the right soldermask material for my PCB?
When choosing a soldermask material, consider the following factors:
– Compatibility with the surface finish and other materials used in the PCB
– Flexibility and peel strength to withstand mechanical and thermal stress
– UV and thermal stability for long-term durability
– Recommended thickness range for optimal performance
– Specific requirements of your application, such as fine-pitch components or high-temperature operation
By understanding the common problems and solutions associated with PCB soldermask, manufacturers can take proactive steps to ensure the quality, reliability, and longevity of their PCBs. Proper material selection, process optimization, quality control, and design considerations all play crucial roles in minimizing soldermask issues and producing high-quality PCBs that meet the demands of today’s electronics industry.
0 Comments