What is Gold Plating?
Gold plating is a process where a thin layer of gold is deposited onto the surface of a PCB. The gold layer is typically applied to the exposed copper areas of the PCB, such as the contact fingers, connector pads, and test points. The purpose of gold plating is to enhance the electrical and mechanical properties of the PCB, making it more reliable and long-lasting.
Advantages of Gold Plating PCBs
There are several advantages to gold plating PCBs, including:
-
Excellent Electrical Conductivity: Gold is an excellent conductor of electricity, which makes it ideal for use in PCBs. Gold-plated contact fingers and connector pads provide a low-resistance path for electrical signals, minimizing signal loss and ensuring reliable connections.
-
Corrosion Resistance: Gold is highly resistant to corrosion, even in harsh environments. This makes gold-plated PCBs suitable for use in applications where the PCB may be exposed to moisture, chemicals, or other corrosive agents.
-
Durability: Gold is a soft metal, but it is also very durable. Gold-plated PCBs can withstand repeated insertions and removals of connectors without wearing out or losing their electrical properties.
-
Solderability: Gold is easily solderable, which makes it easy to attach components to gold-plated PCBs using standard soldering techniques.
-
Improved Aesthetics: Gold-plated PCBs have a bright, shiny appearance that can enhance the overall look of the finished product.
Common Gold Plating Methods for PCBs
There are several methods used for gold plating PCBs, each with its own advantages and disadvantages. The most common methods are:
Electroplating
Electroplating is the most common method used for gold plating PCBs. In this process, the PCB is immersed in a gold-containing electrolyte solution, and an electric current is applied. The electric current causes the gold ions in the solution to be attracted to the exposed copper areas of the PCB, forming a thin layer of gold on the surface.
Advantages of electroplating include:
- Uniform coating thickness
- Good adhesion to the base metal
- Suitable for high-volume production
Disadvantages of electroplating include:
- Requires specialized equipment and chemicals
- Can be expensive for small-volume production
- May require additional processing steps, such as cleaning and activation
Immersion Gold Plating
Immersion gold plating is a simpler and less expensive alternative to electroplating. In this process, the PCB is immersed in a gold-containing solution, and the gold ions in the solution spontaneously deposit onto the exposed copper areas of the PCB.
Advantages of immersion gold plating include:
- Simple process that does not require specialized equipment
- Less expensive than electroplating
- Suitable for small-volume production
Disadvantages of immersion gold plating include:
- Thin coating thickness (typically 0.05-0.2 microns)
- May not provide sufficient corrosion protection in harsh environments
- Limited shelf life of the plated PCBs
Electroless Nickel Immersion Gold (ENIG)
ENIG is a two-step process that combines electroless nickel plating with immersion gold plating. In the first step, a thin layer of nickel is deposited onto the exposed copper areas of the PCB using an electroless plating process. In the second step, a thin layer of gold is deposited onto the nickel layer using an immersion plating process.
Advantages of ENIG include:
- Excellent corrosion resistance
- Good solderability
- Suitable for fine-pitch components
Disadvantages of ENIG include:
- More expensive than other gold plating methods
- Requires strict process control to ensure consistent results
- May be prone to “black pad” defects if not properly controlled
Comparison of Gold Plating Methods
Method | Thickness | Adhesion | Cost | Suitability |
---|---|---|---|---|
Electroplating | 0.5-2.0 microns | Excellent | High | High-volume production |
Immersion Gold | 0.05-0.2 microns | Good | Low | Small-volume production |
ENIG | 0.05-0.2 microns (Au) / 3-6 microns (Ni) | Excellent | High | Fine-pitch components |
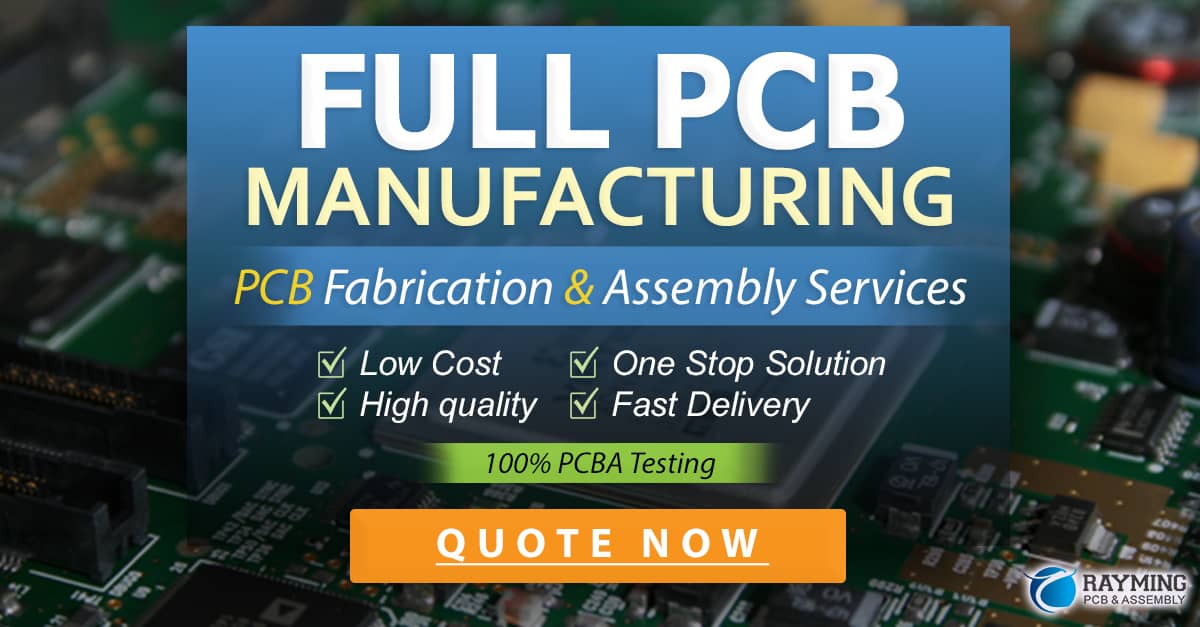
Gold Plating Process Steps
The gold plating process for PCBs typically involves the following steps:
-
Cleaning: The PCB is cleaned to remove any contaminants or oxides from the surface. This is typically done using a chemical cleaning process, such as acid cleaning or alkaline cleaning.
-
Activation: The exposed copper areas of the PCB are activated to improve the adhesion of the gold plating. This is typically done using a mild acid solution, such as sulfuric acid or hydrochloric acid.
-
Plating: The PCB is immersed in the gold plating solution, and the gold is deposited onto the exposed copper areas using one of the methods described above.
-
Rinsing: The PCB is rinsed with deionized water to remove any remaining plating solution.
-
Drying: The PCB is dried using hot air or a vacuum dryer to remove any remaining moisture.
-
Inspection: The PCB is inspected for defects, such as voids, nodules, or inconsistent plating thickness.
Factors Affecting Gold Plating Quality
Several factors can affect the quality of gold plating on PCBs, including:
-
Surface Preparation: Proper surface preparation is essential for achieving good adhesion and uniform plating thickness. Any contaminants or oxides on the surface can prevent the gold from adhering properly, leading to defects such as voids or peeling.
-
Plating Solution Composition: The composition of the gold plating solution must be carefully controlled to ensure consistent results. Factors such as the gold concentration, pH, and temperature can all affect the plating quality.
-
Current Density: In electroplating, the current density must be carefully controlled to achieve the desired plating thickness and uniformity. Too high a current density can lead to nodules or burning, while too low a current density can result in thin or uneven plating.
-
Plating Time: The plating time must be carefully controlled to achieve the desired plating thickness. Too short a plating time can result in thin or incomplete plating, while too long a plating time can lead to excessive thickness or waste of gold.
-
Rinsing and Drying: Proper rinsing and drying are essential for removing any remaining plating solution and preventing contamination or corrosion of the plated surface.
Frequently Asked Questions (FAQ)
-
What is the typical thickness of gold plating on PCBs?
The typical thickness of gold plating on PCBs ranges from 0.05 to 2.0 microns, depending on the plating method used and the specific application requirements. -
Is gold plating necessary for all PCBs?
No, gold plating is not necessary for all PCBs. It is typically used in applications where high reliability, corrosion resistance, or solderability are required, such as in aerospace, military, or medical electronics. -
Can gold plating be applied to other metals besides copper?
Yes, gold plating can be applied to other metals besides copper, such as nickel, silver, or palladium. However, copper is the most common base metal used for PCBs. -
How does gold plating affect the cost of PCBs?
Gold plating can significantly increase the cost of PCBs, especially if a thick layer of gold is required. The cost of gold plating depends on factors such as the plating method, the thickness of the gold layer, and the size of the PCB. -
Can gold-plated PCBs be recycled?
Yes, gold-plated PCBs can be recycled to recover the gold and other valuable metals. However, the recycling process is complex and requires specialized equipment and expertise.
Conclusion
Gold plating is a common finishing process for PCBs that provides excellent electrical conductivity, corrosion resistance, and durability. There are several methods used for gold plating PCBs, including electroplating, immersion gold plating, and ENIG. The choice of plating method depends on factors such as the specific application requirements, the desired plating thickness, and the production volume.
To achieve high-quality gold plating on PCBs, careful attention must be paid to factors such as surface preparation, plating solution composition, current density, plating time, and rinsing and drying. By understanding these factors and following best practices for gold plating, manufacturers can produce reliable, long-lasting PCBs for a wide range of applications.
0 Comments