Introduction
In today’s fast-paced technological world, the efficiency of the supply chain is crucial for the success of any electronics manufacturing company. One of the key factors that can significantly impact the speed and effectiveness of the supply chain is the choice of Printed Circuit Board (PCB) assembly. PCB Assembly is the process of attaching electronic components to a PCB, which is a fundamental step in the production of electronic devices. The right choice of PCB assembly can streamline the manufacturing process, reduce lead times, and improve overall supply chain performance. On the other hand, a poorly chosen PCB assembly method can lead to delays, increased costs, and potential quality issues.
This article will explore the various aspects of PCB assembly and how they relate to the supply chain. We will discuss the different types of PCB assembly, the factors to consider when choosing an assembly method, and the impact of PCB assembly on the overall supply chain performance. Additionally, we will provide insights into best practices for optimizing PCB assembly to ensure a smooth and efficient supply chain.
Types of PCB Assembly
There are three main types of PCB assembly: through-hole, surface-mount, and mixed assembly. Each method has its own advantages and disadvantages, and the choice of assembly type depends on various factors such as the complexity of the design, the required level of automation, and the production volume.
Through-Hole Assembly
Through-hole assembly is the traditional method of PCB assembly, where electronic components have long leads that are inserted into drilled holes on the PCB and soldered onto the other side. This method is suitable for larger components and provides a strong mechanical connection. However, through-hole assembly is slower and less automated compared to surface-mount assembly, which can impact the overall speed of the supply chain.
Surface-Mount Assembly
Surface-mount assembly (SMT) is a more modern and widely used method of PCB assembly. In this process, electronic components are placed directly onto the surface of the PCB and soldered in place. SMT allows for smaller components, higher component density, and increased automation, resulting in faster assembly times and improved production efficiency. The use of SMT can significantly speed up the supply chain by reducing lead times and increasing throughput.
Mixed Assembly
Mixed assembly combines both through-hole and surface-mount components on a single PCB. This method is used when a design requires components that are not available in surface-mount packages or when certain components need the added mechanical strength provided by through-hole mounting. Mixed assembly can be more complex and time-consuming than pure SMT assembly, which may impact the speed of the supply chain.
Factors to Consider When Choosing PCB Assembly
When selecting the appropriate PCB assembly method for a particular project, several factors must be taken into account to ensure optimal supply chain performance.
Design Complexity
The complexity of the PCB design is a significant factor in determining the choice of assembly method. Designs with high component density, fine pitch components, or complex routing may require the use of SMT assembly to achieve the necessary precision and reliability. On the other hand, simpler designs with larger components may be suitable for through-hole assembly.
Production Volume
The expected production volume plays a crucial role in selecting the PCB assembly method. For high-volume production, SMT assembly is generally the preferred choice due to its higher level of automation and faster assembly times. Through-hole assembly may be more suitable for low-volume or prototype production, where the added costs of SMT setup may not be justified.
Component Availability
The availability of components in specific package types can influence the choice of assembly method. Some components may only be available in through-hole packages, while others may be exclusively surface-mount. The selection of components and their package types should be considered early in the design process to ensure compatibility with the chosen assembly method.
Cost Considerations
The cost of PCB assembly is another important factor to consider. SMT assembly generally has higher initial setup costs due to the need for specialized equipment and tooling. However, for high-volume production, SMT can offer lower per-unit costs due to increased automation and faster assembly times. Through-hole assembly may be more cost-effective for low-volume or prototype production.
Quality and Reliability Requirements
The required level of quality and reliability for the end product should also be considered when choosing a PCB assembly method. SMT assembly typically offers higher reliability due to the smaller size of components and the reduced number of solder joints. Through-hole assembly may be preferred in applications where mechanical strength is a priority or where the PCB will be subjected to high levels of stress or vibration.
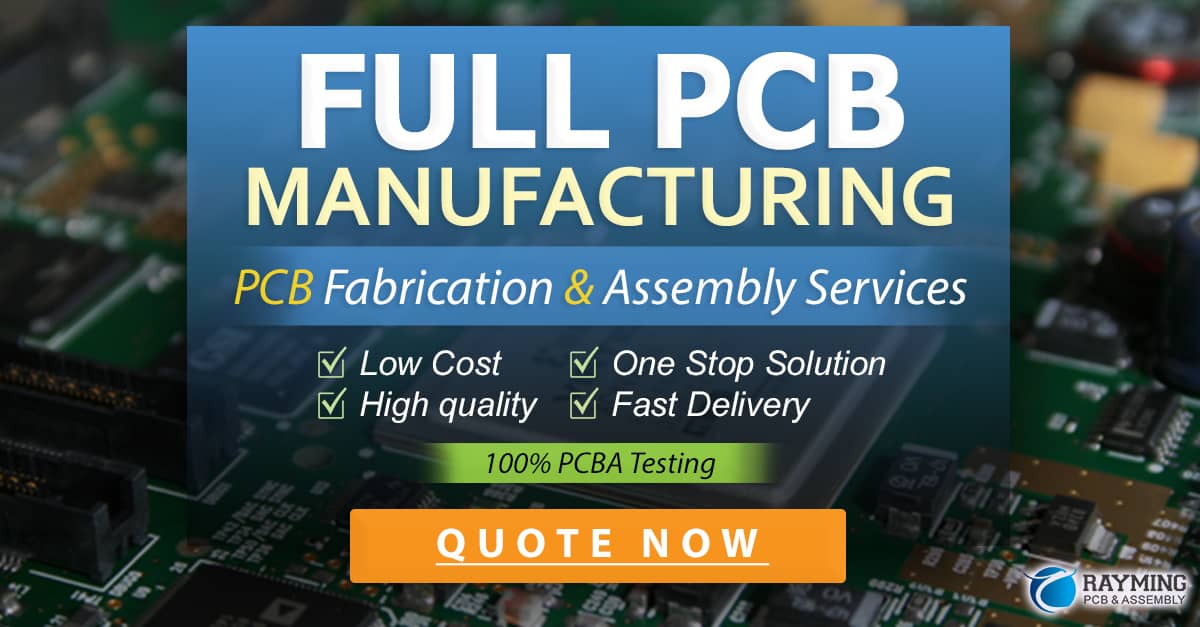
Impact of PCB Assembly on Supply Chain Performance
The choice of PCB assembly method can have a significant impact on various aspects of supply chain performance, including lead times, inventory management, and overall production efficiency.
Lead Times
The assembly method chosen can greatly influence lead times, which is the time between the placement of an order and the delivery of the finished product. SMT assembly generally offers shorter lead times compared to through-hole assembly due to its higher level of automation and faster assembly speeds. Shorter lead times can help companies respond more quickly to market demands and reduce the risk of obsolete inventory.
Inventory Management
PCB assembly choice can also impact inventory management. SMT assembly allows for smaller component sizes and higher component density, which can reduce the amount of raw material inventory required. Additionally, the faster assembly times associated with SMT can help reduce work-in-progress (WIP) inventory, freeing up valuable resources and improving cash flow.
Production Efficiency
The choice of assembly method can significantly affect overall production efficiency. SMT assembly offers higher throughput and lower per-unit costs for high-volume production, enabling companies to optimize their production processes and improve overall efficiency. Through-hole assembly may be less efficient for high-volume production but can still be the preferred choice for low-volume or prototype runs.
Best Practices for Optimizing PCB Assembly in the Supply Chain
To ensure a smooth and efficient supply chain, companies should consider the following best practices when optimizing their PCB assembly processes:
-
Early collaboration between design and manufacturing teams to ensure design for manufacturability (DFM) and design for assembly (DFA) principles are incorporated from the start.
-
Careful selection of components and their package types to ensure compatibility with the chosen assembly method and to minimize the risk of supply chain disruptions.
-
Investment in automated assembly equipment and processes to improve throughput, reduce human error, and increase overall production efficiency.
-
Implementation of lean manufacturing principles, such as just-in-time (JIT) inventory management and continuous improvement initiatives, to streamline the supply chain and reduce waste.
-
Regular monitoring and analysis of key performance indicators (KPIs) related to PCB assembly, such as lead times, yield rates, and inventory turns, to identify areas for improvement and optimize supply chain performance.
FAQs
-
Q: What is the difference between through-hole and surface-mount PCB assembly?
A: Through-hole assembly involves inserting component leads into drilled holes on the PCB and soldering them in place, while surface-mount assembly places components directly onto the surface of the PCB and solders them in place. SMT assembly allows for smaller components, higher component density, and increased automation compared to through-hole assembly. -
Q: Which PCB assembly method is best for high-volume production?
A: Surface-mount assembly (SMT) is generally the preferred choice for high-volume production due to its higher level of automation, faster assembly times, and lower per-unit costs. SMT allows for higher throughput and improved production efficiency compared to through-hole assembly. -
Q: Can mixed assembly, using both through-hole and surface-mount components, affect the speed of the supply chain?
A: Yes, mixed assembly can be more complex and time-consuming than pure SMT assembly, which may impact the speed of the supply chain. The added complexity of handling both through-hole and surface-mount components can increase assembly times and reduce overall production efficiency. -
Q: How can the choice of PCB assembly impact inventory management in the supply chain?
A: The choice of PCB assembly can impact inventory management in several ways. SMT assembly allows for smaller component sizes and higher component density, which can reduce the amount of raw material inventory required. Additionally, the faster assembly times associated with SMT can help reduce work-in-progress (WIP) inventory, freeing up valuable resources and improving cash flow. -
Q: What are some best practices for optimizing PCB assembly in the supply chain?
A: Some best practices for optimizing PCB assembly in the supply chain include early collaboration between design and manufacturing teams, careful selection of components and their package types, investment in automated assembly equipment and processes, implementation of lean manufacturing principles, and regular monitoring and analysis of key performance indicators (KPIs) related to PCB assembly.
Conclusion
The choice of PCB assembly method plays a critical role in the efficiency and speed of the electronics manufacturing supply chain. Surface-mount assembly (SMT) has emerged as the preferred choice for high-volume production due to its increased automation, faster assembly times, and improved production efficiency. However, through-hole assembly and mixed assembly still have their place in certain applications, such as those requiring stronger mechanical connections or the use of components not available in surface-mount packages.
When selecting the appropriate PCB assembly method, companies must consider factors such as design complexity, production volume, component availability, cost, and quality requirements. By carefully evaluating these factors and implementing best practices for optimizing PCB assembly, companies can streamline their supply chain, reduce lead times, improve inventory management, and increase overall production efficiency.
As technology continues to advance and the demand for electronics grows, the importance of efficient PCB assembly in the supply chain will only increase. By staying informed about the latest developments in PCB assembly methods and best practices, electronics manufacturers can position themselves for success in an increasingly competitive market.
0 Comments