What is a PCB BOM?
A Bill of Materials (BOM) is a comprehensive list of all the components, parts, and materials required to manufacture a product. In the context of Printed Circuit Board (PCB) design, a BOM is a crucial document that lists all the electronic components needed to assemble a PCB. It serves as a bridge between the design and manufacturing processes, ensuring that the right components are procured and assembled correctly.
A well-organized and accurate PCB BOM is essential for several reasons:
- It helps in procuring the correct components from suppliers
- It assists in planning the manufacturing process
- It helps in estimating the cost of the PCB
- It serves as a reference for future revisions and repairs
Key Elements of a PCB BOM
A comprehensive PCB BOM should include the following information for each component:
Element | Description |
---|---|
Reference Designator | A unique identifier for each component on the PCB, such as R1, C2, U3, etc. |
Quantity | The number of each component required for one PCB |
Manufacturer Part Number | The unique part number assigned by the manufacturer |
Description | A brief description of the component, including its value, tolerance, and package type |
Manufacturer | The name of the component manufacturer |
Supplier | The name of the supplier from whom the component will be procured |
Supplier Part Number | The unique part number assigned by the supplier |
Here’s an example of a PCB BOM table:
Ref Des | Qty | Manufacturer Part Number | Description | Manufacturer | Supplier | Supplier Part Number |
---|---|---|---|---|---|---|
C1, C2 | 2 | 0805YC105KAT2A | 1μF 10% 16V X5R 0805 | AVX | Digi-Key | 478-1395-1-ND |
R1 | 1 | ERJ-6ENF1002V | 10kΩ 1% 1/8W 0805 | Panasonic | Mouser | 667-ERJ-6ENF1002V |
U1 | 1 | ATTINY85-20SU | MCU 8-bit ATtiny AVR RISC 8KB Flash 2.7 to 5.5V 8-SOIC | Microchip | Arrow | ATTINY85-20SU |
Best Practices for Creating a PCB BOM
1. Start Early and Update Regularly
Begin creating the BOM early in the design process and update it regularly as the design evolves. This helps in identifying any component issues or availability constraints early on, reducing the risk of delays later in the manufacturing process.
2. Use a Consistent Format
Establish a consistent format for the BOM and stick to it across all projects. This makes it easier for team members and suppliers to understand and work with the BOM.
3. Include All Necessary Information
Ensure that the BOM includes all the necessary information for each component, as listed in the “Key Elements of a PCB BOM” section. Missing or incomplete information can lead to procurement and assembly issues.
4. Use Unique Reference Designators
Assign unique reference designators to each component on the PCB. This helps in clearly identifying components both in the BOM and on the physical PCB.
5. Specify the Correct Quantity
Double-check the quantity of each component required for one PCB. Incorrect quantities can lead to shortages or excess inventory.
6. Use Approved Manufacturers and Suppliers
Source components from approved manufacturers and suppliers to ensure quality and reliability. Using unauthorized or counterfeit components can lead to performance issues and reliability problems.
7. Consider Alternate Components
Include alternate components in the BOM, especially for critical or hard-to-find components. This helps in mitigating the risk of component obsolescence or supply chain disruptions.
8. Perform a BOM Validation
Conduct a thorough BOM validation before releasing it for procurement and manufacturing. This includes:
- Checking for missing or duplicate components
- Verifying component values, tolerances, and package types
- Ensuring that the BOM matches the schematic and PCB layout
- Confirming component availability and lead times with suppliers
9. Use a BOM Management Tool
Consider using a BOM management tool to streamline the creation, updates, and sharing of BOMs. These tools often integrate with PCB design software and provide features like component libraries, supplier integration, and change tracking.
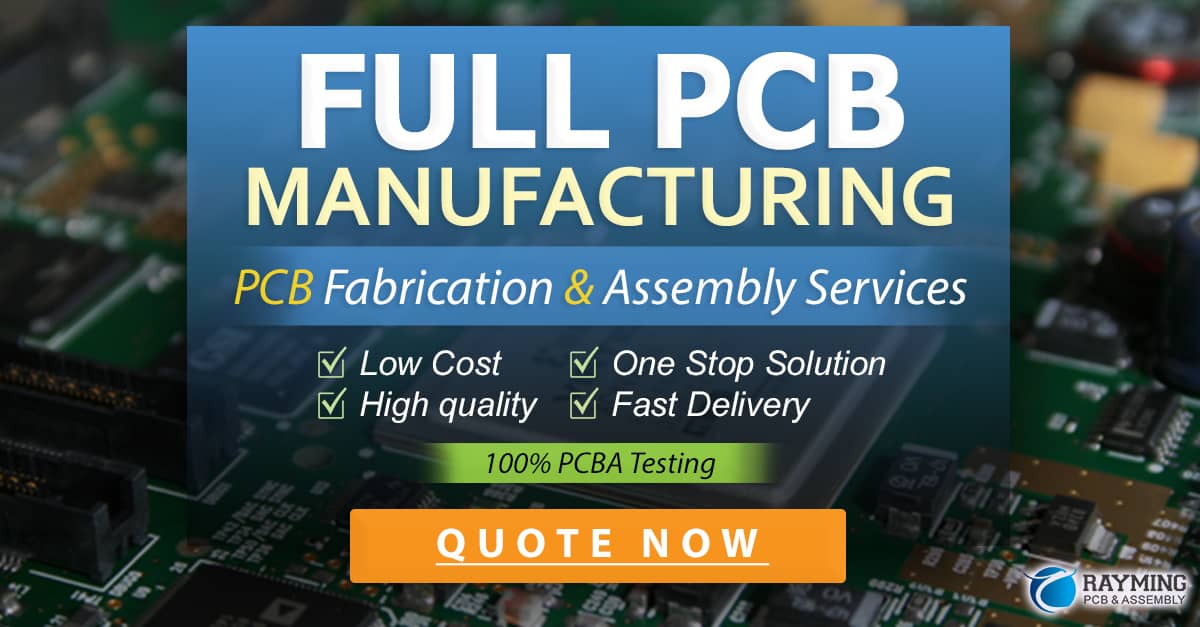
Common PCB BOM Mistakes and How to Avoid Them
1. Incomplete or Inconsistent Component Information
Mistake: Incomplete or inconsistent component information in the BOM can lead to procurement and assembly issues.
Solution: Establish a consistent format for the BOM and ensure that all necessary information is included for each component.
2. Using Unapproved or Counterfeit Components
Mistake: Using unapproved or counterfeit components to save costs can lead to quality and reliability issues.
Solution: Source components only from approved manufacturers and suppliers. Establish a clear component approval process and maintain an approved vendor list (AVL).
3. Not Considering Component Availability and Lead Times
Mistake: Not considering component availability and lead times can lead to delays in the manufacturing process.
Solution: Check component availability and lead times with suppliers before finalizing the BOM. Consider alternate components for critical or hard-to-find parts.
4. Not Updating the BOM Throughout the Design Process
Mistake: Not updating the BOM as the design evolves can lead to discrepancies between the design and the manufactured product.
Solution: Update the BOM regularly throughout the design process. Perform a final BOM validation before releasing it for procurement and manufacturing.
5. Not Collaborating with the Manufacturing Team
Mistake: Not collaborating with the manufacturing team can lead to design-for-manufacturing (DFM) issues and assembly problems.
Solution: Involve the manufacturing team early in the design process and seek their input on component selection, placement, and assembly considerations.
The Role of BOM in Design for Manufacturing (DFM)
Design for Manufacturing (DFM) is the process of designing products that are easy to manufacture, assemble, and test. A well-structured and accurate BOM plays a crucial role in DFM by:
-
Enabling Component Standardization: By using standardized components across multiple designs, you can reduce inventory costs, improve procurement efficiency, and simplify the assembly process.
-
Facilitating Design Reviews: The BOM serves as a key document during design reviews, allowing the manufacturing team to provide input on component selection, placement, and assembly considerations.
-
Supporting Manufacturing Planning: The BOM helps in planning the manufacturing process, including component procurement, assembly line setup, and testing procedures.
-
Enabling Cost Optimization: By analyzing the BOM, you can identify opportunities for cost optimization, such as using alternate components, negotiating better pricing with suppliers, or redesigning the PCB for easier assembly.
Managing BOM Changes and Revisions
As the PCB design evolves, it’s essential to manage changes and revisions to the BOM effectively. Here are some best practices for managing BOM changes and revisions:
-
Establish a Change Control Process: Define a clear process for requesting, reviewing, and approving changes to the BOM. This should include a change request form, a review committee, and a version control system.
-
Use Version Control: Assign unique version numbers to each revision of the BOM. This helps in tracking changes and ensuring that all stakeholders are working with the latest version.
-
Communicate Changes: Clearly communicate BOM changes to all relevant stakeholders, including the design team, manufacturing team, suppliers, and customers.
-
Document Change History: Maintain a change history log that records all changes made to the BOM, including the date, version number, and a brief description of the change.
-
Perform Impact Analysis: Before implementing a change, perform an impact analysis to assess the potential effects on the design, manufacturing process, and cost. This helps in making informed decisions and minimizing unintended consequences.
Integrating BOM with Other Tools and Processes
To streamline the PCB design and manufacturing process, it’s important to integrate the BOM with other tools and processes, such as:
-
PCB Design Software: Many PCB design software packages include BOM generation and management features. By integrating the BOM with the design software, you can ensure that the BOM stays in sync with the schematic and PCB layout.
-
Enterprise Resource Planning (ERP) Systems: Integrating the BOM with your ERP system helps in streamlining component procurement, inventory management, and production planning.
-
Supply Chain Management (SCM) Systems: Integrating the BOM with SCM systems enables real-time visibility into component availability, pricing, and lead times, helping you make informed decisions and avoid supply chain disruptions.
-
Product Lifecycle Management (PLM) Systems: Integrating the BOM with PLM systems helps in managing the entire product lifecycle, from design to manufacturing, sales, and support. This enables better collaboration, version control, and change management.
Frequently Asked Questions (FAQ)
1. What is the difference between a parts list and a BOM?
A parts list is a simplified version of a BOM that typically includes only the reference designators, quantities, and descriptions of the components. A BOM, on the other hand, is a more comprehensive document that includes additional information such as manufacturer part numbers, supplier information, and alternate components.
2. How do I handle components that are not in the BOM?
If you encounter a component that is not in the BOM, first check if it is a valid component that was accidentally omitted. If it is, add it to the BOM and update the version number. If it is not a valid component, remove it from the design and update the BOM accordingly.
3. What should I do if a component in the BOM becomes obsolete?
If a component in the BOM becomes obsolete, you should:
- Identify a suitable alternate component
- Update the BOM with the new component information
- Verify the compatibility of the new component with the design
- Communicate the change to all relevant stakeholders
4. How often should I update the BOM?
The BOM should be updated regularly throughout the design process, whenever there are changes to the components or the design. It is also good practice to perform a final BOM validation before releasing it for procurement and manufacturing.
5. Can I use the same BOM for multiple PCB designs?
While it is possible to use the same BOM for multiple PCB designs, it is generally not recommended. Each PCB design should have its own unique BOM to ensure accuracy and avoid confusion. However, you can standardize components across multiple designs to simplify procurement and inventory management.
Conclusion
A well-structured and accurate BOM is essential for successful PCB design and manufacturing. By following the best practices outlined in this article, you can create BOMs that help streamline the procurement process, reduce manufacturing errors, and ensure the long-term success of your PCB projects. Remember to start early, update regularly, and collaborate with all stakeholders to create a robust and reliable BOM that serves as the foundation for your PCB design and manufacturing process.
0 Comments