Introduction
Printed Circuit Boards (PCBs) are an essential component in modern electronics. They provide a stable and efficient platform for mounting and connecting electronic components. However, the process of cutting PCBs can be challenging, especially for those who are new to the field. In this article, we will explore the best methods for cutting PCB boards, including the tools and techniques required for achieving clean and precise cuts.
Why Proper PCB Cutting Techniques Matter
Proper PCB cutting techniques are crucial for several reasons:
-
Functionality: Improper cutting can damage the PCB, leading to short circuits, broken traces, or other issues that can affect the functionality of the circuit.
-
Aesthetics: Clean and precise cuts give the PCB a professional appearance, which is important for commercial products or presentations.
-
Efficiency: Using the right tools and techniques can save time and minimize material waste, making the PCB fabrication process more efficient.
Tools for Cutting PCB Boards
There are several tools available for cutting PCBs, each with its own advantages and disadvantages. Here are some of the most common tools:
1. Shears
PCB shears are specialized tools designed for cutting PCBs. They have hardened steel blades that can cleanly cut through the board material without causing damage to the copper traces or components. Shears are available in various sizes and styles, including hand shears and bench-mounted shears.
Advantages | Disadvantages |
---|---|
Clean, precise cuts | Limited to straight cuts |
Easy to use | Not suitable for intricate shapes |
Affordable |
2. Saws
Various types of saws can be used for cutting PCBs, including band saws, table saws, and scroll saws. These tools allow for more flexibility in terms of cutting shapes and angles compared to shears.
Advantages | Disadvantages |
---|---|
Versatile cutting options | Higher risk of damaging the PCB |
Can cut intricate shapes | Requires more skill to use |
Generate dust and debris |
3. Routers
CNC routers are computer-controlled machines that can cut PCBs with high precision. They use spinning bits to remove material from the board, allowing for complex shapes and cutouts. Routers are commonly used in professional PCB fabrication settings.
Advantages | Disadvantages |
---|---|
High precision and accuracy | Expensive equipment |
Can cut complex shapes | Requires specialized software and skills |
Efficient for large-scale production | Overkill for small projects |
4. Laser Cutters
Laser cutters use a high-powered laser beam to vaporize the PCB material, resulting in clean and precise cuts. They are capable of cutting intricate shapes and patterns with minimal material waste.
Advantages | Disadvantages |
---|---|
Extremely precise cuts | High initial cost |
Can cut complex shapes | Requires specialized equipment and skills |
Minimal material waste | Limited material thickness |
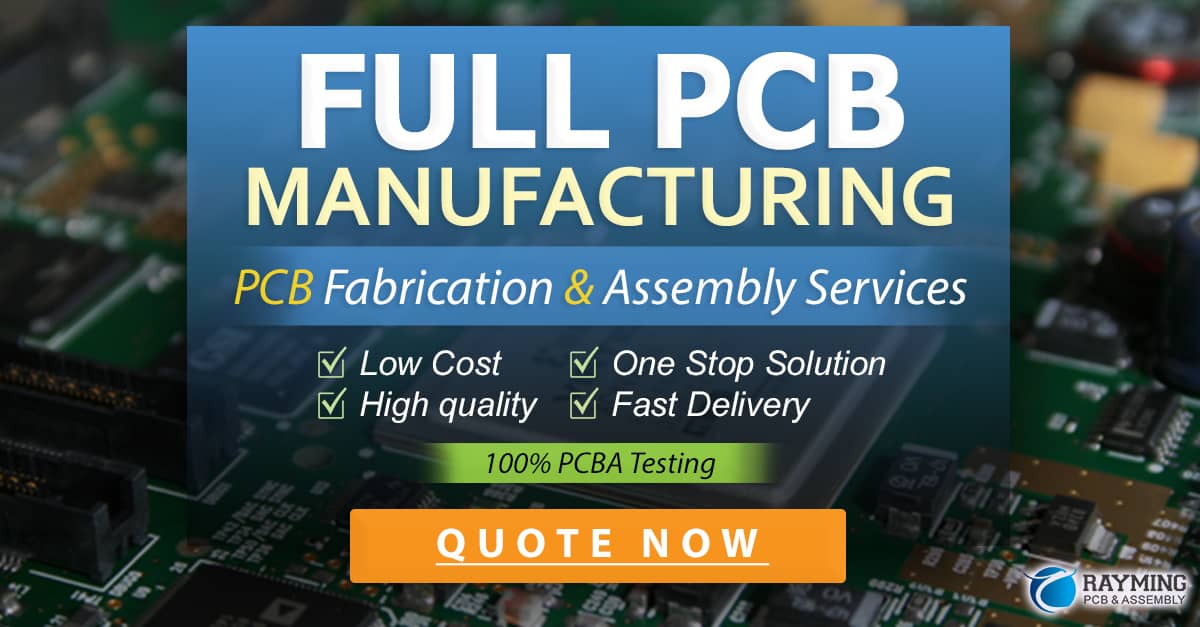
Techniques for Cutting PCB Boards
Regardless of the tool used, there are several techniques that can help ensure clean and precise cuts:
1. Scoring and Snapping
For straight cuts, scoring and snapping can be an effective method. This involves using a sharp blade or scoring tool to create a deep groove along the desired cut line. Then, the board is snapped along the score line, resulting in a clean break. This method works best for thin PCBs and requires a steady hand and practice to achieve consistent results.
2. Drilling and Routing
For more complex shapes or cutouts, drilling and routing techniques can be used. This involves drilling a series of small holes along the desired cut line, then using a router or saw to connect the holes and remove the excess material. This method allows for more flexibility in terms of shapes and angles but requires more skill and patience to execute properly.
3. V-Grooving
V-grooving is a technique used for creating fold lines in PCBs, allowing them to be bent into specific shapes or angles. This involves using a V-shaped blade to cut a groove along the desired fold line, leaving a thin strip of material that acts as a hinge. V-grooving is commonly used for creating enclosures or mounting brackets for PCBs.
Safety Considerations
When cutting PCBs, it’s important to prioritize safety to avoid injury or damage to the equipment. Here are some key safety considerations:
- Wear protective gear, such as safety glasses and gloves, to protect against flying debris and sharp edges.
- Secure the PCB properly to prevent slipping or shifting during cutting.
- Use the appropriate tool and blade for the material and thickness of the PCB.
- Work in a well-ventilated area to minimize exposure to dust and fumes.
- Follow the manufacturer’s instructions and safety guidelines for each tool and machine.
PCB Cutting Tips and Tricks
Here are some additional tips and tricks for achieving the best results when cutting PCBs:
- Use a sacrificial backing board to minimize tearout and support the PCB during cutting.
- Apply masking tape along the cut line to minimize chipping and improve the cut quality.
- Use a lubricant, such as WD-40 or mineral oil, to reduce friction and heat buildup during cutting.
- For intricate shapes or designs, consider using a stencil or template to guide the cutting process.
- Practice on scrap material or test boards before cutting the final PCB to ensure the desired results are achieved.
Frequently Asked Questions (FAQ)
1. What is the best tool for cutting PCBs?
The best tool for cutting PCBs depends on the specific requirements of the project, such as the size, shape, and complexity of the cuts. For straight cuts, PCB shears are often the most efficient and affordable option. For more complex shapes or designs, a CNC router or laser cutter may be necessary.
2. Can I use a regular saw to cut PCBs?
While it is possible to use a regular saw, such as a hacksaw or coping saw, to cut PCBs, it is not recommended. Regular saws may cause excessive chipping, burring, or damage to the copper traces and components. It’s best to use specialized tools designed for cutting PCBs to ensure clean and precise cuts.
3. How do I avoid damaging the PCB when cutting?
To avoid damaging the PCB when cutting, follow these tips:
– Use the appropriate tool and blade for the material and thickness of the PCB
– Secure the PCB properly to prevent slipping or shifting during cutting
– Apply masking tape along the cut line to minimize chipping
– Use a sacrificial backing board to support the PCB and minimize tearout
– Work slowly and carefully, applying steady pressure and maintaining control of the tool
4. Can I cut a PCB with a laser cutter?
Yes, laser cutters are an excellent option for cutting PCBs, especially for intricate shapes and designs. Laser cutters use a high-powered laser beam to vaporize the PCB material, resulting in clean and precise cuts with minimal material waste. However, laser cutters are expensive and require specialized equipment and skills to operate.
5. How do I ensure consistent and accurate cuts when cutting PCBs?
To ensure consistent and accurate cuts when cutting PCBs, follow these tips:
– Use a template, stencil, or guide to ensure consistent positioning and alignment of the cuts
– Measure and mark the cut lines carefully, using a ruler, caliper, or other precision measuring tool
– Practice on scrap material or test boards to refine your technique and ensure the desired results are achieved
– Use a consistent cutting speed, pressure, and angle to maintain control and accuracy
– Regularly maintain and calibrate your cutting tools to ensure optimal performance and precision
Conclusion
Cutting PCBs is a critical step in the PCB fabrication process, requiring the right tools, techniques, and safety considerations to achieve clean and precise results. Whether using shears, saws, routers, or laser cutters, it’s important to choose the appropriate method based on the specific requirements of the project, such as the size, shape, and complexity of the cuts.
By following the tips and techniques outlined in this article, you can improve your PCB cutting skills and achieve professional-quality results. Remember to prioritize safety, work carefully and methodically, and practice on scrap material or test boards to refine your technique.
With the right knowledge and tools, cutting PCBs can be a rewarding and efficient process that helps bring your electronic projects to life.
0 Comments