Introduction to Bluetooth PCB Design
Bluetooth technology has become ubiquitous in modern electronic devices, enabling wireless communication between devices over short distances. To ensure optimal performance and reliability of Bluetooth-enabled devices, it is crucial to follow best practices when designing Bluetooth printed circuit boards (PCBs). This comprehensive guide will dive into the key considerations and guidelines for creating high-quality Bluetooth PCBs.
Understanding Bluetooth Technology
What is Bluetooth?
Bluetooth is a wireless communication standard that allows devices to exchange data over short distances using radio waves in the 2.4 GHz frequency band. It was developed by Ericsson in 1994 and has since become widely adopted in various applications, such as wireless headphones, smart home devices, and industrial automation systems.
Bluetooth Versions and Features
Over the years, Bluetooth has evolved through several versions, each offering improved performance, power efficiency, and security features. The most recent version, Bluetooth 5.2, introduced in 2020, offers the following key features:
- Increased data transfer speed (up to 2 Mbps)
- Longer range (up to 240 meters in open areas)
- Improved power efficiency
- Enhanced security with LE Secure Connections
- Bluetooth mesh networking support
Bluetooth PCB Design Considerations
Antenna Design and Placement
The antenna is a critical component of any Bluetooth PCB, as it determines the range and quality of the wireless connection. When designing a Bluetooth antenna, consider the following factors:
- Antenna type (e.g., chip antenna, PCB trace antenna, or external antenna)
- Antenna size and shape
- Antenna placement on the PCB (away from other components and ground planes)
- Impedance matching between the antenna and the Bluetooth module
Proper antenna design and placement can significantly improve the performance and reliability of your Bluetooth device.
RF Layout and Grounding
To minimize electromagnetic interference (EMI) and ensure optimal signal integrity, follow these guidelines when designing the RF layout and grounding of your Bluetooth PCB:
- Keep RF traces as short as possible and avoid sharp bends
- Use controlled impedance traces for RF signals
- Provide adequate ground planes and use via stitching to minimize ground impedance
- Separate analog and digital ground planes and connect them at a single point
- Use RF shielding (e.g., metal cans or conformal shielding) to minimize interference
Power Supply and Decoupling
Bluetooth modules require a clean and stable power supply to function correctly. To achieve this, consider the following:
- Use low-dropout (LDO) voltage regulators to provide a stable voltage supply
- Place decoupling capacitors close to the Bluetooth module’s power pins
- Use ferrite beads or inductors to filter high-frequency noise
- Separate power supplies for analog and digital circuits
Component Selection and Placement
When selecting components for your Bluetooth PCB, choose parts that are compatible with the Bluetooth module and meet the performance requirements of your application. Consider the following factors:
- Component size and package type (e.g., surface-mount or through-hole)
- Component tolerance and temperature rating
- Placement of components to minimize signal path lengths and interference
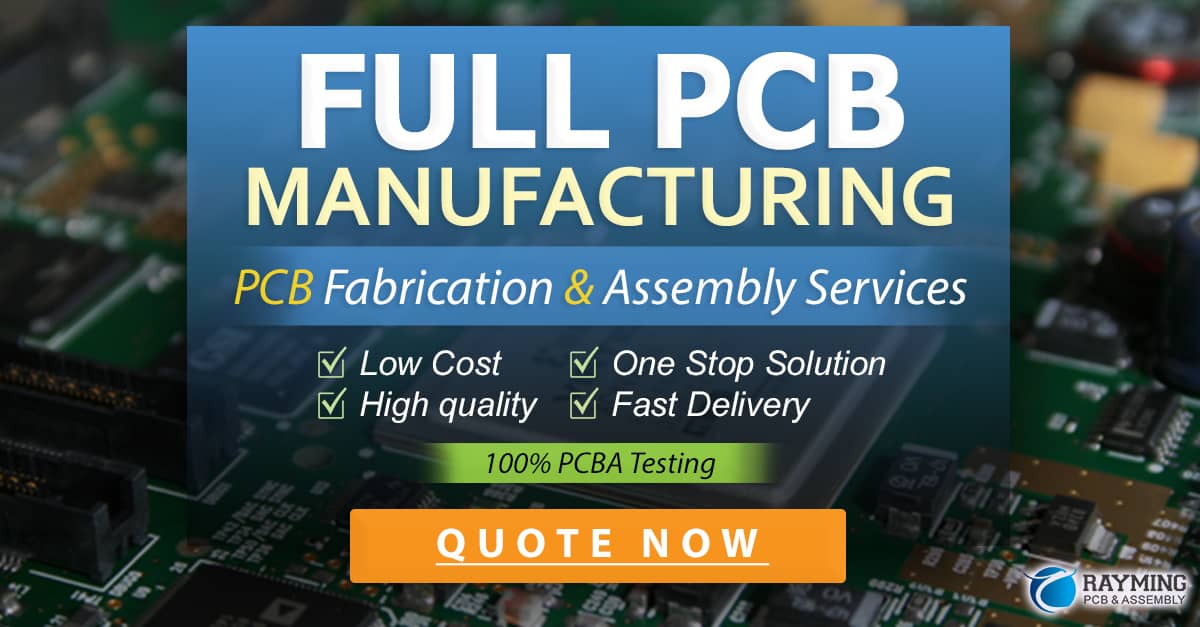
Bluetooth PCB Layout Guidelines
Layer Stack-up
A well-designed layer stack-up is essential for maintaining signal integrity and minimizing crosstalk between layers. A typical Bluetooth PCB layer stack-up may include the following layers:
Layer | Description |
---|---|
Top Layer | RF traces, components, and antenna |
Ground Plane | Solid ground plane for shielding and reference |
Power Plane | Solid power plane for distributing power to components |
Bottom Layer | Additional components and traces |
Trace Width and Spacing
When routing traces on your Bluetooth PCB, follow these guidelines to minimize signal loss and crosstalk:
- Use appropriate trace widths based on the current requirements and PCB manufacturing capabilities
- Maintain adequate spacing between traces to minimize crosstalk
- Use serpentine routing for longer traces to match trace lengths
Via Design and Placement
Vias are used to connect traces between layers on a PCB. When designing vias for your Bluetooth PCB, consider the following:
- Use the smallest via size possible to minimize signal loss and inductance
- Place vias strategically to minimize signal path lengths
- Use via stitching to connect ground planes and minimize ground impedance
Bluetooth PCB Testing and Validation
Signal Integrity Analysis
Before manufacturing your Bluetooth PCB, perform signal integrity analysis to ensure that the design meets the performance requirements. Use simulation tools to analyze the following:
- Impedance matching between the antenna and the Bluetooth module
- Signal reflections and losses in RF traces
- Crosstalk between signals
EMC Testing
Electromagnetic compatibility (EMC) testing is essential to ensure that your Bluetooth device does not interfere with other electronic devices and meets regulatory requirements. Perform the following EMC tests:
- Radiated emissions testing
- Conducted emissions testing
- Immunity testing
Functional Testing
After manufacturing your Bluetooth PCB, perform functional testing to validate its performance and reliability. Test the following aspects:
- Wireless range and connection quality
- Data transfer speed and throughput
- Power consumption and battery life
- Compatibility with other Bluetooth devices
Frequently Asked Questions (FAQ)
1. What is the maximum range of Bluetooth 5.2?
Bluetooth 5.2 offers a maximum range of up to 240 meters in open areas, depending on the transmit power and antenna design.
2. Can I use a PCB trace antenna for my Bluetooth design?
Yes, PCB trace antennas can be used for Bluetooth designs, provided they are properly designed and matched to the Bluetooth module’s impedance.
3. How can I minimize electromagnetic interference in my Bluetooth PCB?
To minimize EMI, use proper grounding techniques, RF shielding, and separate power supplies for analog and digital circuits.
4. What is the recommended layer stack-up for a Bluetooth PCB?
A typical Bluetooth PCB layer stack-up includes a top layer for RF traces and components, a ground plane, a power plane, and a bottom layer for additional components and traces.
5. How important is functional testing for Bluetooth PCBs?
Functional testing is crucial to validate the performance and reliability of your Bluetooth PCB, ensuring that it meets the desired specifications and is compatible with other Bluetooth devices.
Conclusion
Designing a high-quality Bluetooth PCB requires careful consideration of various factors, including antenna design, RF layout, power supply, component selection, and PCB layout. By following the guidelines outlined in this comprehensive guide, you can create Bluetooth PCBs that offer optimal performance, reliability, and compatibility with other devices. Remember to perform thorough testing and validation to ensure that your Bluetooth PCB meets the desired specifications and regulatory requirements.
0 Comments