Why Component Arrangement Matters in Assembly Design
The arrangement of components is a critical aspect of assembly design that has a significant impact on the overall efficiency, reliability, and cost-effectiveness of the final product. Proper component arrangement can lead to faster assembly times, reduced material waste, and improved product quality. On the other hand, poor component arrangement can result in assembly errors, increased production costs, and lower customer satisfaction.
One of the primary goals of component arrangement in assembly design is to minimize the number of assembly steps required. By carefully considering the placement and orientation of each component, designers can streamline the assembly process and reduce the likelihood of errors. This not only saves time and money but also ensures that the final product meets the required quality standards.
Another important consideration in component arrangement is the accessibility of each component during the assembly process. Components that are difficult to reach or require special tools to install can slow down the assembly line and increase the risk of damage to the product. By designing for accessibility, manufacturers can improve the efficiency of their assembly processes and reduce the need for costly rework.
Key Principles of Component Arrangement
There are several key principles that designers should keep in mind when arranging components in an assembly:
-
Functionality: The primary consideration in component arrangement should be the functionality of the final product. Components should be placed in a way that allows them to perform their intended function without interference from other components.
-
Assembly Sequence: The arrangement of components should follow a logical assembly sequence that minimizes the number of steps required and reduces the likelihood of errors. This may involve grouping similar components together or placing them in a specific order based on their installation requirements.
-
Accessibility: Components should be placed in a way that allows for easy access during the assembly process. This may involve leaving sufficient space around each component or designing the assembly to allow for the use of standard tools and equipment.
-
Standardization: Wherever possible, designers should strive to use standardized components and assembly processes. This can help to reduce costs, improve quality, and simplify the supply chain.
-
Material Flow: The arrangement of components should take into account the flow of materials through the assembly process. This may involve placing components near the point of use or designing the assembly to minimize the distance that materials need to travel.
Common Techniques for Component Arrangement
There are several common techniques that designers use to optimize component arrangement in assembly design:
-
Modular Design: Modular design involves breaking down the assembly into smaller, self-contained modules that can be assembled separately and then combined to form the final product. This approach can help to simplify the assembly process and improve flexibility in the supply chain.
-
Platform Design: Platform design involves creating a common base or platform that can be used across multiple products or variations. This approach can help to reduce costs and improve efficiency by allowing for the reuse of components and assembly processes.
-
Design for Assembly (DFA): DFA is a systematic approach to designing products with the goal of simplifying the assembly process. This may involve reducing the number of parts, standardizing components, or designing for easy insertion and fastening.
-
Poka-Yoke: Poka-yoke is a Japanese term that refers to mistake-proofing. In the context of assembly design, poka-yoke involves designing components and assemblies in a way that prevents errors from occurring. This may involve using asymmetrical shapes, color-coding, or other visual cues to ensure that components are installed correctly.
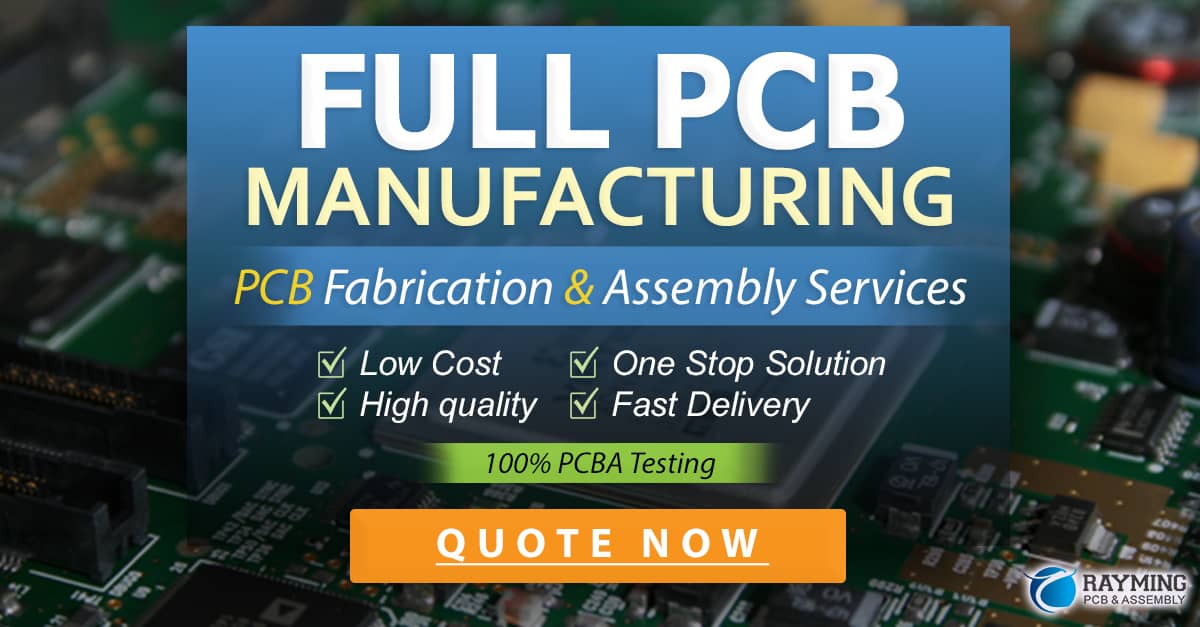
Case Studies
To illustrate the importance of component arrangement in assembly design, let’s look at a few real-world examples:
Case Study 1: Automotive Wiring Harness Assembly
In the automotive industry, wiring harnesses are a critical component that connect various electrical systems throughout the vehicle. The arrangement of wires and connectors within the harness can have a significant impact on the ease of assembly and the reliability of the final product.
One common technique for optimizing wiring harness assembly is to use a modular design approach. By breaking down the harness into smaller sub-assemblies, manufacturers can simplify the assembly process and improve flexibility in the supply chain. This approach also allows for the use of automated assembly processes, which can help to reduce costs and improve quality.
Another important consideration in wiring harness assembly is the use of color-coding and other visual cues to ensure that components are installed correctly. For example, using different colored connectors for different circuits can help to prevent errors during assembly and make it easier to troubleshoot issues later on.
Case Study 2: Medical Device Assembly
In the medical device industry, the arrangement of components is critical for ensuring the safety and effectiveness of the final product. Poor component arrangement can lead to assembly errors that could have serious consequences for patients.
One common challenge in medical device assembly is the need to maintain sterility throughout the process. This requires careful consideration of the placement and handling of components to avoid contamination.
Another important consideration is the need for precise alignment of components. Many medical devices require tight tolerances to ensure proper functionality, and even small misalignments can cause issues. Designers must carefully consider the placement and orientation of each component to ensure that they can be assembled accurately and consistently.
Case Study 3: Consumer Electronics Assembly
In the consumer electronics industry, the arrangement of components can have a significant impact on the overall design and functionality of the final product. Designers must balance the need for compact, lightweight designs with the requirements for performance and reliability.
One common technique for optimizing component arrangement in consumer electronics is the use of flexible printed circuit boards (PCBs). These PCBs can be bent and folded to fit into tight spaces, allowing for more compact designs.
Another important consideration is the placement of heat-generating components. Designers must carefully consider the thermal management requirements of each component and arrange them in a way that allows for adequate cooling.
Best Practices for Component Arrangement
Based on the principles and techniques discussed above, here are some best practices for optimizing component arrangement in assembly design:
-
Start with the end in mind: Before beginning the design process, clearly define the functionality and performance requirements of the final product. Use this information to guide decisions about component selection and placement.
-
Collaborate with stakeholders: Involve representatives from all relevant departments, including engineering, manufacturing, and supply chain, in the design process. This can help to ensure that the final design meets the needs of all stakeholders and avoids potential issues down the line.
-
Use 3D modeling and simulation: Modern CAD tools allow designers to create detailed 3D models of assemblies and simulate the assembly process. Use these tools to optimize component placement and identify potential issues before moving to production.
-
Design for automation: Wherever possible, design assemblies with automated assembly processes in mind. This may involve using standardized components, designing for easy insertion and fastening, and minimizing the need for manual intervention.
-
Continuously improve: Monitor the performance of assemblies in production and use this information to identify opportunities for improvement. Continuously refine the design and assembly processes to optimize efficiency, quality, and cost.
FAQ
-
What is component arrangement in assembly design?
Component arrangement refers to the placement and orientation of individual components within an assembly. It involves considering factors such as functionality, assembly sequence, accessibility, standardization, and material flow to optimize the overall efficiency and reliability of the final product. -
Why is component arrangement important in assembly design?
Proper component arrangement can lead to faster assembly times, reduced material waste, improved product quality, and lower production costs. Poor component arrangement, on the other hand, can result in assembly errors, increased costs, and lower customer satisfaction. -
What are some common techniques for optimizing component arrangement?
Some common techniques for optimizing component arrangement include modular design, platform design, design for assembly (DFA), and poka-yoke (mistake-proofing). These techniques involve breaking down assemblies into smaller sub-assemblies, standardizing components, designing for easy insertion and fastening, and using visual cues to prevent errors. -
How can 3D modeling and simulation tools help with component arrangement?
Modern CAD tools allow designers to create detailed 3D models of assemblies and simulate the assembly process. This can help to optimize component placement, identify potential issues, and refine the design before moving to production. -
What are some best practices for optimizing component arrangement in assembly design?
Some best practices for optimizing component arrangement include starting with the end in mind, collaborating with stakeholders, using 3D modeling and simulation tools, designing for automation, and continuously improving the design and assembly processes based on performance data.
0 Comments