Introduction to Metal Core PCBs
Metal core printed circuit boards (MCPCBs) are a special type of PCB that has a metal base layer, usually made of aluminum, instead of the traditional FR4 material. The metal core serves as an effective heat sink, allowing for better thermal management and heat dissipation compared to standard PCBs. This makes metal core PCBs ideal for applications that generate a lot of heat, such as high-power LED lighting, automotive electronics, and power supplies.
Key Features of Metal Core PCBs
- Aluminum base layer for improved heat dissipation
- Thermal vias to conduct heat away from components
- Dielectric layer to insulate components from the metal core
- Copper circuit layer for electrical connections
Advantages of Using Metal Core PCBs
Superior Heat Dissipation
One of the primary advantages of using metal core PCBs is their excellent thermal management capabilities. The aluminum base layer acts as a built-in heat sink, effectively conducting heat away from the components and distributing it evenly across the board. This helps to prevent hot spots and thermal stress, which can lead to component failure and reduced reliability.
The thermal conductivity of aluminum is significantly higher than that of FR4, as shown in the table below:
Material | Thermal Conductivity (W/mK) |
---|---|
Aluminum | 205 |
FR4 | 0.3 |
This means that metal core PCBs can dissipate heat up to 10 times more effectively than standard FR4 boards.
Increased Power Density
With the improved thermal management provided by metal core PCBs, designers can increase the power density of their boards without compromising reliability. This means that more components can be packed onto a smaller board area, reducing the overall size and weight of the device.
In applications such as LED lighting, where high power densities are required, metal core PCBs are essential for ensuring optimal performance and longevity.
Enhanced Reliability
By effectively managing heat and preventing thermal stress, metal core PCBs offer enhanced reliability compared to standard PCBs. This is particularly important in applications where failure is not an option, such as automotive electronics and aerospace systems.
The improved reliability of metal core PCBs can be attributed to several factors:
- Reduced thermal stress on components
- Even heat distribution across the board
- Prevention of hot spots and thermal runaway
- Lower operating temperatures
Cost Savings
While metal core PCBs may have a higher initial cost compared to standard PCBs, they can offer significant cost savings in the long run. The improved thermal management and reliability of metal core PCBs can lead to:
- Reduced component failure rates
- Extended product lifespan
- Lower maintenance and repair costs
- Improved energy efficiency
In applications where reliability is critical, the cost savings associated with metal core PCBs can far outweigh the initial investment.
Applications of Metal Core PCBs
High-Power LED Lighting
Metal core PCBs are widely used in high-power LED lighting applications, such as street lights, automotive headlights, and industrial lighting. LEDs generate a significant amount of heat, which must be effectively dissipated to ensure optimal performance and longevity.
By using metal core PCBs, designers can create compact, high-power LED fixtures that offer superior thermal management and reliability.
Automotive Electronics
In the automotive industry, reliability and durability are paramount. Metal core PCBs are used in a variety of automotive electronics applications, such as:
- Engine control units (ECUs)
- Power steering systems
- Electric vehicle battery management systems
- Infotainment systems
The enhanced thermal management and reliability provided by metal core PCBs make them ideal for the harsh operating conditions encountered in automotive environments.
Power Supplies
Power supplies, particularly those with high power densities, can benefit greatly from the use of metal core PCBs. The improved heat dissipation and thermal management capabilities of metal core PCBs allow for more efficient and reliable power supply designs.
Some common power supply applications that utilize metal core PCBs include:
- Switching mode power supplies (SMPS)
- AC-DC Converters
- DC-DC converters
- Battery Chargers
Industrial Control Systems
Industrial control systems often require high reliability and the ability to operate in harsh environments. Metal core PCBs are well-suited for these applications, as they can withstand higher temperatures and provide improved thermal management.
Examples of industrial control systems that may utilize metal core PCBs include:
- Motor drives
- Programmable logic controllers (PLCs)
- Automation systems
- Process control equipment
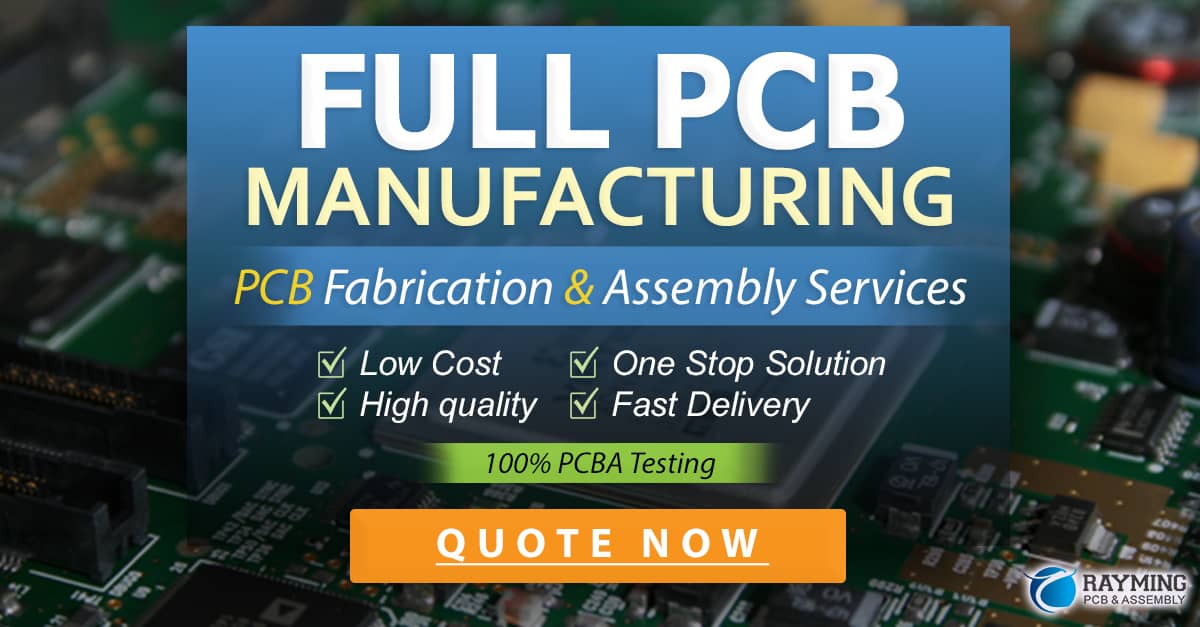
Designing with Metal Core PCBs
Thermal Management Considerations
When designing with metal core PCBs, it is essential to consider the thermal management requirements of the application. This includes:
- Identifying heat-generating components
- Calculating power dissipation requirements
- Determining the optimal placement of components
- Utilizing thermal vias for improved heat transfer
By carefully considering these factors, designers can ensure that their metal core PCB design provides optimal thermal performance and reliability.
Dielectric Layer Selection
The dielectric layer in a metal core PCB serves to insulate the components from the metal core while allowing for efficient heat transfer. The choice of dielectric material is critical for achieving the desired thermal and electrical performance.
Common dielectric materials used in metal core PCBs include:
- Aluminum oxide (Al2O3)
- Boron nitride (BN)
- Aluminum nitride (AlN)
- Epoxy-based polymers
Each material has its own set of properties, such as thermal conductivity, dielectric strength, and cost. Designers must carefully consider these properties when selecting a dielectric material for their metal core PCB.
Manufacturing Considerations
Manufacturing metal core PCBs requires specialized processes and equipment compared to standard PCBs. Some key manufacturing considerations include:
- Bonding the dielectric layer to the metal core
- Drilling and plating thermal vias
- Ensuring proper adhesion of the copper circuit layer
- Handling the increased weight and thickness of the board
Working closely with an experienced metal core PCB manufacturer can help ensure that the final product meets all design and performance requirements.
FAQ
1. What is the difference between a metal core PCB and a standard PCB?
A metal core PCB has a metal base layer, usually made of aluminum, instead of the FR4 material used in standard PCBs. This metal core provides improved heat dissipation and thermal management capabilities.
2. Can metal core PCBs be used for all applications?
While metal core PCBs offer many advantages, they are not suitable for all applications. They are best suited for applications that require high power densities, generate significant amounts of heat, or demand high reliability, such as LED lighting, automotive electronics, and power supplies.
3. Are metal core PCBs more expensive than standard PCBs?
Yes, metal core PCBs typically have a higher initial cost compared to standard PCBs due to the specialized materials and manufacturing processes required. However, the improved thermal management and reliability of metal core PCBs can lead to significant cost savings over the life of the product.
4. How do I choose the right dielectric material for my metal core PCB?
The choice of dielectric material depends on the specific requirements of your application, such as thermal conductivity, dielectric strength, and cost. Common dielectric materials include aluminum oxide, boron nitride, aluminum nitride, and epoxy-based polymers. Consult with your metal core PCB manufacturer to determine the best material for your needs.
5. Can I manufacture metal core PCBs using the same processes as standard PCBs?
Manufacturing metal core PCBs requires specialized processes and equipment compared to standard PCBs. This includes bonding the dielectric layer to the metal core, drilling and plating thermal vias, and ensuring proper adhesion of the copper circuit layer. It is essential to work with an experienced metal core PCB manufacturer to ensure the best results.
Conclusion
Metal core PCBs offer numerous advantages over standard PCBs, including superior heat dissipation, increased power density, enhanced reliability, and potential cost savings. These benefits make them ideal for applications that generate significant amounts of heat or require high reliability, such as LED lighting, automotive electronics, power supplies, and industrial control systems.
When designing with metal core PCBs, it is essential to consider thermal management requirements, dielectric layer selection, and manufacturing considerations. By working closely with an experienced metal core PCB manufacturer and carefully considering these factors, designers can create high-performance, reliable products that meet the demands of their specific applications.
As technology continues to advance and the demand for high-power, compact electronics grows, the use of metal core PCBs is likely to increase across a wide range of industries. By understanding the advantages and design considerations associated with metal core PCBs, engineers and manufacturers can stay at the forefront of this exciting technology and create innovative, reliable products that meet the needs of their customers.
0 Comments