Introduction to Telecom PCB Assembly
Telecom PCB (Printed Circuit Board) assembly is a crucial process in the manufacturing of telecommunications equipment. It involves the placement and soldering of electronic components onto a printed circuit board, creating a functional electronic circuit. Telecom PCBs are used in a wide range of applications, including mobile phones, base stations, routers, and satellites.
The telecom industry relies heavily on PCB assembly to produce reliable and high-quality electronic devices. As the demand for faster and more efficient communication systems continues to grow, the importance of telecom PCB assembly cannot be overstated.
Key Aspects of Telecom PCB Assembly
- High-Frequency PCB Design
- Multilayer PCB Fabrication
- Surface Mount Technology (SMT)
- Through-Hole Technology (THT)
- Automated Optical Inspection (AOI)
High-Frequency PCB Design
Telecom PCBs often operate at high frequencies, requiring specialized design techniques to ensure optimal performance. High-frequency PCB design involves the careful selection of materials, trace geometry, and component placement to minimize signal loss and interference.
Materials for High-Frequency PCBs
Material | Dielectric Constant | Dissipation Factor | Thermal Conductivity (W/mK) |
---|---|---|---|
FR-4 | 4.5 | 0.02 | 0.3 |
Rogers RO4003C | 3.38 | 0.0027 | 0.71 |
Isola I-Tera MT | 3.45 | 0.0031 | 0.52 |
Choosing the right material is essential for high-frequency PCB design. Low dielectric constant and dissipation factor materials, such as Rogers RO4003C and Isola I-Tera MT, are preferred for their superior electrical properties and thermal stability.
Trace Geometry and Impedance Matching
Trace geometry plays a critical role in high-frequency PCB design. Microstrip and stripline traces are commonly used to route high-frequency signals. The width and spacing of these traces must be carefully calculated to achieve the desired impedance and minimize signal reflections.
Impedance matching is another important aspect of high-frequency PCB design. Properly matched impedances ensure that signals propagate through the PCB with minimal loss and distortion. Techniques such as stub matching and tapered lines can be employed to achieve optimal impedance matching.
Multilayer PCB Fabrication
Telecom PCBs often require multiple layers to accommodate the complex circuitry and high component density. Multilayer PCB fabrication involves the lamination of multiple copper layers with insulating dielectric materials.
Layer Stack-up
A typical multilayer PCB stack-up consists of alternating copper and dielectric layers. The number of layers depends on the complexity of the circuit and the required functionality. A common stack-up for a 6-layer telecom PCB might include:
- Top Layer (Signal)
- Ground Plane
- Signal Layer
- Power Plane
- Signal Layer
- Bottom Layer (Signal)
The arrangement of layers is crucial for maintaining signal integrity and minimizing cross-talk between adjacent layers.
Via Technology
Vias are used to interconnect different layers in a multilayer PCB. There are several types of vias used in telecom PCB fabrication:
- Through Vias: Extend through the entire thickness of the PCB
- Blind Vias: Connect an outer layer to an inner layer
- Buried Vias: Connect two or more inner layers without extending to the outer layers
The choice of via technology depends on the design requirements and manufacturing capabilities. High-density interconnect (HDI) PCBs often employ microvias, which have smaller diameters and can be laser-drilled for increased precision.
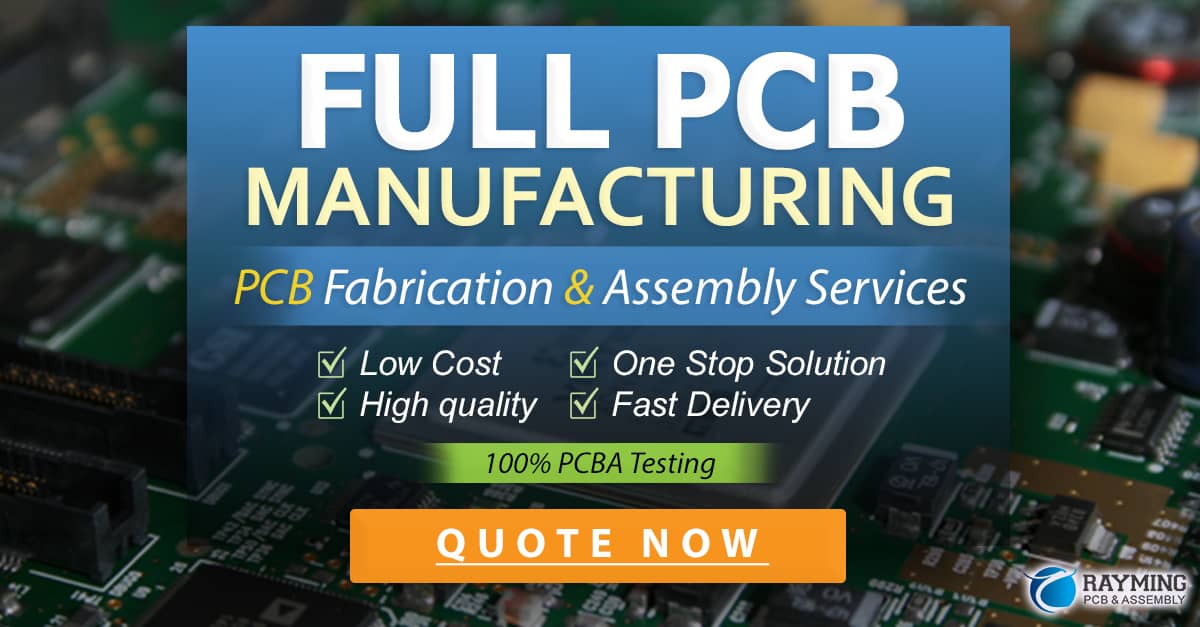
Surface Mount Technology (SMT)
Surface Mount Technology (SMT) is the dominant assembly method for telecom PCBs. SMT involves the placement of electronic components directly onto the surface of the PCB, without the need for through-holes.
Advantages of SMT
- Higher component density
- Faster assembly process
- Improved electrical performance
- Reduced manufacturing costs
SMT Assembly Process
The SMT assembly process typically involves the following steps:
- Solder Paste Printing: A stencil is used to apply solder paste onto the PCB pads
- Component Placement: SMT components are placed onto the solder paste using pick-and-place machines
- Reflow Soldering: The PCB is heated in a reflow oven, melting the solder paste and forming a permanent bond between the components and the PCB
- Inspection: Automated Optical Inspection (AOI) is used to verify the correct placement and soldering of components
Through-Hole Technology (THT)
While SMT is the primary assembly method for telecom PCBs, Through-Hole Technology (THT) is still used for certain components that require additional mechanical strength or thermal dissipation.
THT Assembly Process
The THT assembly process involves the following steps:
- Component Insertion: THT components are inserted into drilled holes in the PCB
- Wave Soldering: The PCB is passed over a wave of molten solder, which fills the holes and forms a connection between the component leads and the PCB
- Inspection: Visual inspection is performed to ensure proper soldering and component placement
Hybrid Assembly
Some telecom PCBs require a combination of SMT and THT assembly, known as hybrid assembly. Hybrid assembly allows for the integration of both surface mount and through-hole components on the same PCB, providing greater flexibility in design and functionality.
Automated Optical Inspection (AOI)
Automated Optical Inspection (AOI) is a crucial step in the telecom PCB assembly process. AOI systems use high-resolution cameras and advanced image processing algorithms to detect defects and ensure the quality of the assembled PCBs.
Benefits of AOI
- Rapid inspection of complex PCBs
- Detection of a wide range of defects, including:
- Solder bridges
- Open circuits
- Component misalignment
- Insufficient or excessive solder
- Improved quality control and reduced rework costs
AOI Process
The AOI process typically involves the following steps:
- Image Acquisition: High-resolution images of the assembled PCB are captured from multiple angles
- Image Analysis: Advanced algorithms compare the captured images to a reference image or CAD data, identifying any discrepancies
- Defect Classification: Detected defects are classified based on their type and severity
- Reporting: A detailed report of the inspection results is generated for further analysis and corrective action
Conclusion
Telecom PCB assembly is a complex and critical process that requires expertise in high-frequency PCB design, multilayer fabrication, SMT and THT assembly, and automated optical inspection. As the demand for high-performance telecommunications equipment continues to grow, the importance of reliable and efficient PCB assembly cannot be overstated.
By understanding the key aspects of telecom PCB assembly, manufacturers can optimize their processes, improve product quality, and meet the ever-increasing demands of the telecommunications industry.
Frequently Asked Questions (FAQ)
1. What is the difference between SMT and THT assembly?
SMT (Surface Mount Technology) involves placing components directly onto the surface of the PCB, while THT (Through-Hole Technology) requires inserting component leads through drilled holes in the PCB. SMT is the dominant assembly method for telecom PCBs due to its higher component density, faster assembly process, and improved electrical performance. THT is still used for components that require additional mechanical strength or thermal dissipation.
2. Why is impedance matching important in high-frequency PCB design?
Impedance matching is crucial in high-frequency PCB design to ensure that signals propagate through the PCB with minimal loss and distortion. Mismatched impedances can lead to signal reflections, which can degrade signal integrity and cause issues such as ringing, overshoot, and undershoot. By properly matching impedances, designers can optimize signal transmission and maintain the overall performance of the telecom system.
3. What are the advantages of using multilayer PCBs in telecom applications?
Multilayer PCBs offer several advantages in telecom applications, including:
- Increased circuit density: Multiple layers allow for more complex circuitry and higher component density
- Improved signal integrity: Dedicated power and ground planes help reduce noise and cross-talk between signals
- Enhanced thermal management: Inner layers can be used to dissipate heat generated by high-power components
- Reduced form factor: Multilayer PCBs enable more compact designs, which is essential for space-constrained telecom equipment
4. How does Automated Optical Inspection (AOI) improve the quality of telecom PCB assembly?
Automated Optical Inspection (AOI) is a vital step in ensuring the quality of telecom PCB assembly. AOI systems use high-resolution cameras and advanced image processing algorithms to rapidly inspect assembled PCBs for a wide range of defects, such as solder bridges, open circuits, component misalignment, and insufficient or excessive solder. By detecting these defects early in the manufacturing process, AOI helps reduce rework costs, improve overall product quality, and increase customer satisfaction.
5. What are the challenges associated with high-frequency PCB design and assembly?
Designing and assembling high-frequency PCBs for telecom applications presents several challenges, including:
- Material selection: Choosing the right PCB materials with low dielectric constant and dissipation factor to minimize signal loss and interference
- Trace geometry and impedance control: Carefully designing trace widths, spacings, and impedance matching to maintain signal integrity
- Component placement: Optimizing component placement to minimize signal path lengths and reduce parasitic effects
- Manufacturing tolerances: Ensuring tight tolerances in PCB fabrication and assembly to meet the stringent requirements of high-frequency operation
- Testing and validation: Conducting thorough testing and validation to ensure the assembled PCBs meet the desired performance specifications and reliability standards
Addressing these challenges requires a combination of expertise, advanced design tools, and close collaboration between PCB designers, manufacturers, and assembly providers.
0 Comments