Introduction to Teflon PCB
Teflon PCB, also known as PTFE (Polytetrafluoroethylene) PCB, is a type of printed circuit board that utilizes Teflon as the base material. Teflon is a synthetic fluoropolymer known for its exceptional properties, including high thermal stability, low dielectric constant, and excellent chemical resistance. These characteristics make Teflon PCBs ideal for various applications in industries such as aerospace, military, telecommunications, and medical devices.
Key Features of Teflon PCB
- High thermal stability
- Low dielectric constant
- Excellent chemical resistance
- Low moisture absorption
- High-frequency performance
Advantages of Using Teflon PCB
1. Superior Electrical Properties
Teflon PCBs offer superior electrical properties compared to traditional PCB materials. The low dielectric constant of Teflon allows for faster signal transmission and reduced signal loss, making it suitable for high-frequency applications. Additionally, Teflon PCBs have low dissipation factors, which minimize power loss and improve overall circuit efficiency.
2. Excellent Thermal Stability
One of the most significant advantages of Teflon PCBs is their exceptional thermal stability. Teflon can withstand temperatures ranging from -200°C to +260°C without significant degradation in its properties. This thermal stability ensures reliable performance in extreme temperature conditions, making Teflon PCBs ideal for applications in harsh environments.
3. Chemical Resistance
Teflon is highly resistant to various chemicals, including acids, bases, and solvents. This chemical resistance prevents corrosion and degradation of the PCB, ensuring long-term reliability and durability. Teflon PCBs are particularly suitable for applications in industries where exposure to harsh chemicals is common, such as the chemical processing industry.
4. Low Moisture Absorption
Teflon has a very low moisture absorption rate, which is crucial for maintaining the integrity of the PCB. High moisture absorption can lead to delamination, warping, and other defects that compromise the performance and reliability of the circuit board. Teflon PCBs are less susceptible to moisture-related issues, making them suitable for applications in humid environments.
5. High-Frequency Performance
The low dielectric constant and low dissipation factor of Teflon make it an excellent choice for high-frequency applications. Teflon PCBs can maintain signal integrity even at high frequencies, reducing signal distortion and ensuring reliable performance. This characteristic is particularly important in applications such as radar systems, wireless communications, and high-speed digital circuits.
Applications of Teflon PCB
1. Aerospace and Military
Teflon PCBs are widely used in the aerospace and military industries due to their ability to withstand extreme temperatures, harsh chemicals, and high-frequency signals. These industries require reliable and durable electronic components that can operate in challenging environments. Teflon PCBs are used in various applications, such as radar systems, satellite communications, and avionics.
2. Telecommunications
The telecommunications industry relies on high-frequency signals for data transmission. Teflon PCBs are ideal for this industry because of their low dielectric constant and low dissipation factor, which enable faster signal transmission and reduced signal loss. Teflon PCBs are used in applications such as base stations, antennas, and microwave devices.
3. Medical Devices
Teflon PCBs are also used in medical devices due to their biocompatibility and chemical resistance. Medical devices often require reliable and durable electronic components that can withstand sterilization processes and exposure to bodily fluids. Teflon PCBs are used in various medical applications, such as implantable devices, diagnostic equipment, and surgical instruments.
4. Industrial Equipment
Industrial equipment often operates in harsh environments with exposure to high temperatures, chemicals, and moisture. Teflon PCBs are suitable for these applications because of their thermal stability, chemical resistance, and low moisture absorption. Teflon PCBs are used in various industrial applications, such as oil and gas exploration, power generation, and chemical processing.
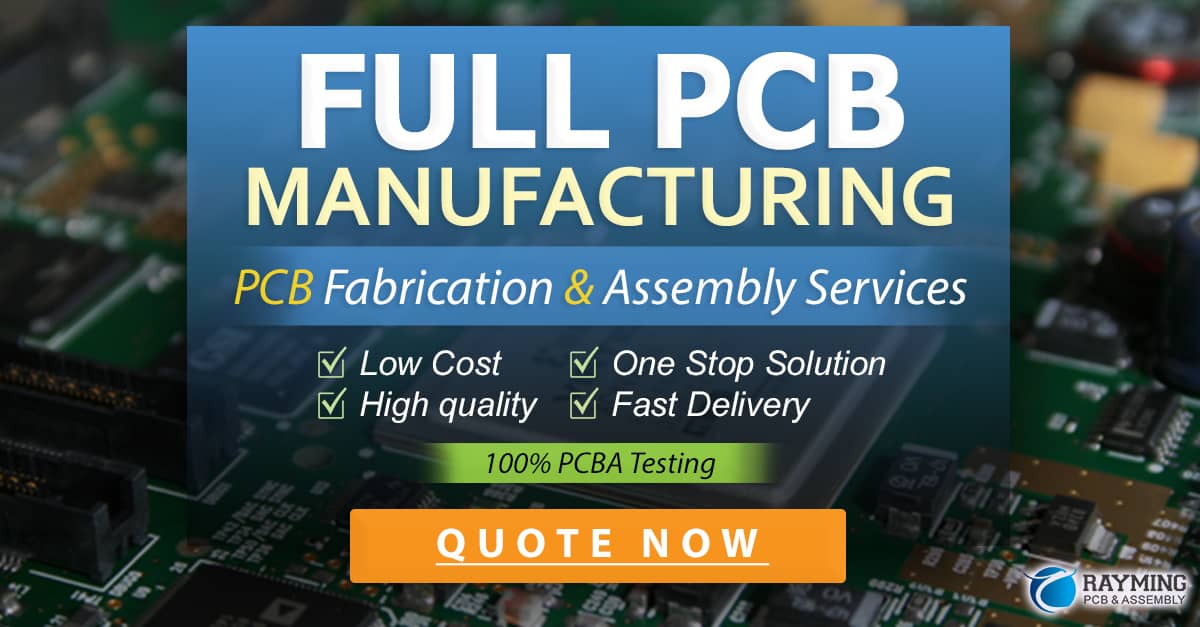
Teflon PCB Manufacturing Process
The manufacturing process for Teflon PCBs is similar to that of traditional PCBs, with a few additional considerations due to the unique properties of Teflon.
1. Material Selection
The first step in the manufacturing process is selecting the appropriate Teflon material. There are various grades of Teflon available, each with slightly different properties. The most commonly used Teflon materials for PCBs are PTFE and FEP (Fluorinated Ethylene Propylene).
2. Lamination
The selected Teflon material is laminated with copper foil using heat and pressure. The lamination process ensures a strong bond between the Teflon and the copper, creating a stable base for the PCB.
3. Drilling
After lamination, the PCB is drilled to create holes for components and vias. Drilling Teflon PCBs requires special considerations due to the material’s softness and tendency to deform. Specialized drill bits and parameters are used to ensure clean and accurate holes.
4. Plating
The drilled holes are then plated with copper to create electrical connections between the layers of the PCB. Electroless copper plating is commonly used for Teflon PCBs, as it provides a uniform and reliable coating.
5. Patterning
The desired circuit pattern is then created on the PCB using photolithography and etching processes. A photoresist is applied to the copper surface, exposed to UV light through a patterned mask, and developed to create the desired pattern. The exposed copper is then etched away, leaving the circuit pattern intact.
6. Solder Mask and Silkscreen
A solder mask is applied to the PCB to protect the copper traces and prevent short circuits. The solder mask also provides insulation and improves the PCB’s appearance. A silkscreen layer is then added to the PCB to provide component labels and other markings.
7. Surface Finish
Finally, a surface finish is applied to the exposed copper areas to prevent oxidation and improve solderability. Common surface finishes for Teflon PCBs include HASL (Hot Air Solder Leveling), ENIG (Electroless Nickel Immersion Gold), and OSP (Organic Solderability Preservative).
Choosing the Right Teflon PCB Manufacturer
When selecting a Teflon PCB manufacturer, there are several factors to consider to ensure high-quality products and reliable service.
1. Experience and Expertise
Choose a manufacturer with extensive experience in producing Teflon PCBs. Teflon PCBs require specialized knowledge and manufacturing processes, and an experienced manufacturer will be better equipped to handle the unique challenges associated with this material.
2. Quality Control
Ensure that the manufacturer has a robust quality control system in place. This should include inspections at various stages of the manufacturing process, as well as thorough testing of the finished products. Look for manufacturers with certifications such as ISO 9001 and UL to ensure they meet industry standards.
3. Technical Support
Select a manufacturer that offers comprehensive technical support. This includes assistance with design, material selection, and troubleshooting. A knowledgeable technical support team can help you optimize your Teflon PCB design and resolve any issues that may arise during the manufacturing process.
4. Lead Time and Pricing
Consider the manufacturer’s lead time and pricing when making your selection. While cost is an important factor, it should not be the sole determining factor. Ensure that the manufacturer can deliver high-quality Teflon PCBs within your required timeframe and budget.
5. Reputation and Customer Feedback
Research the manufacturer’s reputation and seek feedback from their previous customers. Look for reviews and testimonials to gauge the level of customer satisfaction and the quality of their products and services. A reputable manufacturer will have a track record of delivering high-quality Teflon PCBs and exceptional customer service.
Top Teflon PCB Manufacturers
Manufacturer | Location | Website |
---|---|---|
Rogers Corporation | USA | www.rogerscorp.com |
Arlon Electronic Materials | USA | www.arlonemd.com |
Taconic | USA | www.4taconic.com |
Chukoh Chemical Industries | Japan | www.chukoh.co.jp/en/ |
Shengyi Technology | China | www.syst.com.cn/en/ |
FAQ
1. What is the difference between PTFE and FEP Teflon PCBs?
PTFE (Polytetrafluoroethylene) and FEP (Fluorinated Ethylene Propylene) are both types of Teflon used in PCB manufacturing. PTFE has a slightly lower dielectric constant and is more commonly used for high-frequency applications. FEP has a lower melting point and is easier to process, making it suitable for multilayer PCBs.
2. Can Teflon PCBs be used for flexible circuits?
Yes, Teflon PCBs can be used for flexible circuits. Teflon’s flexibility and resistance to creasing make it an excellent choice for applications requiring flexible PCBs, such as wearable devices and aerospace systems.
3. How do Teflon PCBs compare to other high-frequency PCB materials?
Teflon PCBs offer several advantages over other high-frequency PCB materials, such as lower dielectric constant, lower dissipation factor, and higher thermal stability. However, Teflon PCBs are generally more expensive and require specialized manufacturing processes compared to other materials like FR-4.
4. What are the challenges in soldering Teflon PCBs?
Soldering Teflon PCBs can be challenging due to the material’s low surface energy and non-stick properties. To overcome these challenges, special surface treatments, such as sodium etching or plasma treatment, are often used to improve the wettability of the Teflon surface and ensure reliable solder joints.
5. How do I choose the right thickness for my Teflon PCB?
The choice of Teflon PCB thickness depends on various factors, including the application, signal frequency, and component requirements. Thinner Teflon PCBs are generally preferred for high-frequency applications to minimize signal loss and improve impedance control. However, thicker Teflon PCBs may be necessary for applications requiring higher mechanical strength or thermal dissipation. Consult with your Teflon PCB manufacturer to determine the optimal thickness for your specific application.
Conclusion
Teflon PCBs offer unique properties that make them ideal for various applications in industries such as aerospace, military, telecommunications, and medical devices. Their exceptional thermal stability, low dielectric constant, and excellent chemical resistance enable reliable performance in challenging environments and high-frequency applications.
When selecting a Teflon PCB manufacturer, it is essential to consider factors such as experience, quality control, technical support, lead time, pricing, and reputation. By choosing the right manufacturer, you can ensure high-quality Teflon PCBs that meet your specific requirements and exceed your expectations.
As technology continues to advance, the demand for high-performance PCBs like Teflon will only increase. By understanding the advantages and applications of Teflon PCBs, and partnering with a reliable manufacturer, you can unlock the full potential of this innovative material and stay ahead of the curve in your industry.
0 Comments