What is a Stepper Motor?
A stepper motor is a brushless DC electric motor that divides a full rotation into a number of equal steps. It moves in discrete steps when electrical command pulses are applied to it in the proper sequence. The motor’s position can be precisely controlled without any feedback mechanism, as long as the motor is carefully sized to the application in respect to torque and speed.
How does a Stepper Motor work?
Stepper motors operate on the principle of electromagnetism. They consist of a rotor (the rotating part) and a stator (the stationary part). The stator has multiple windings that can be energized in a specific sequence to create a rotating magnetic field. The rotor, which is a permanent magnet or a ferromagnetic core with salient poles, aligns itself with the magnetic field created by the stator, causing the motor to rotate in steps.
Types of Stepper Motors
There are three main types of stepper motors:
-
Permanent Magnet (PM) Stepper Motors: These motors have a permanent magnet rotor and operate on the attraction and repulsion between the rotor poles and the electromagnets in the stator.
-
Variable Reluctance (VR) Stepper Motors: These motors have a toothed iron rotor and operate on the principle of magnetic reluctance. The stator windings are energized to create a magnetic field that attracts the rotor teeth.
-
Hybrid Stepper Motors: These motors combine the features of both PM and VR stepper motors. They have a toothed rotor with a permanent magnet embedded in it, offering high torque and precision.
Advantages of Stepper Motors
- Precise positioning and repeatability
- Excellent low-speed torque
- No need for feedback mechanisms
- Reliable and long lifespan
- Simple and cost-effective control
Disadvantages of Stepper Motors
- Limited high-speed performance
- Can experience resonance and vibration
- Requires a dedicated control circuit
- Can generate more heat compared to DC motors
Applications of Stepper Motors
Stepper motors are commonly used in applications that require precise positioning, such as:
- 3D printers
- CNC machines
- Robotics
- Automotive gauges and instruments
- Medical equipment
- Surveillance cameras
What is a DC Motor?
A DC motor is an electric motor that runs on direct current (DC) electricity. It converts electrical energy into mechanical energy through the interaction between the motor’s magnetic field and the electric current in the windings.
How does a DC Motor work?
DC motors consist of a stator, rotor, brushes, and a commutator. The stator is a stationary part that provides a permanent magnetic field, while the rotor is the rotating part that contains the armature windings. The brushes are conductive components that make contact with the commutator, which is a segmented ring on the rotor.
When a DC voltage is applied to the motor, current flows through the armature windings, creating a magnetic field. The interaction between this magnetic field and the permanent magnetic field of the stator generates torque, causing the rotor to rotate.
Types of DC Motors
There are several types of DC motors, including:
-
Brushed DC Motors: These motors have brushes that make physical contact with the commutator to supply current to the armature windings.
-
Brushless DC (BLDC) Motors: These motors use electronic commutation instead of brushes, offering higher efficiency and longer lifespan.
-
Coreless DC Motors: These motors have a rotor without an iron core, resulting in lower inertia and faster response times.
-
Shunt, Series, and Compound DC Motors: These motors are classified based on how the field windings are connected to the armature.
Advantages of DC Motors
- High starting torque
- Smooth operation
- Simple speed control
- Wide range of speeds
- Compact size
Disadvantages of DC Motors
- Brushed DC motors require regular maintenance
- Limited lifespan of brushes
- Electromagnetic interference (EMI) from brush commutation
- Higher cost compared to AC motors
Applications of DC Motors
DC motors are used in a wide range of applications, such as:
- Automotive systems (e.g., power windows, seats)
- Robotics and automation
- Household appliances
- Power tools
- Toys and models
- Wheelchairs and mobility devices
Comparison: Stepper Motors vs. DC Motors
Now that we have a basic understanding of stepper motors and DC motors, let’s compare their key characteristics and performance aspects.
Characteristic | Stepper Motors | DC Motors |
---|---|---|
Positioning Accuracy | High | Low to moderate |
Speed Range | Low to moderate | Wide range |
Torque at Low Speeds | High | Moderate to high |
Efficiency | Moderate | High |
Control Complexity | Simple | Simple to complex |
Feedback Requirement | Not necessary | Optional |
Smoothness of Rotation | Stepped | Smooth |
Noise Level | Moderate to high | Low to moderate |
Cost | Moderate | Low to high |
Positioning Accuracy
Stepper motors excel in applications that require precise positioning. They can achieve a high degree of accuracy without the need for a feedback mechanism. DC motors, on the other hand, have lower inherent positioning accuracy and often require encoders or other feedback devices to achieve precise positioning.
Speed Range
DC motors offer a wide range of operating speeds, from very low to very high, depending on the motor design and power supply. Stepper motors, however, have a more limited speed range and are typically used in low to moderate speed applications.
Torque at Low Speeds
Stepper motors provide excellent torque at low speeds, making them suitable for applications that require high holding torque or precise low-speed movement. DC motors can also provide good torque at low speeds, but their performance may vary depending on the motor type and design.
Efficiency
DC motors generally have higher efficiency than stepper motors, particularly at high speeds. Stepper motors can generate more heat due to the constant current flow in the windings, even when the motor is not moving.
Control Complexity
Stepper motors are relatively simple to control, as they require only a sequence of pulses to achieve precise positioning. DC motors can also be simple to control for basic applications, but more advanced speed or position control may require complex control algorithms and feedback mechanisms.
Feedback Requirement
Stepper motors do not require feedback for positioning, as long as the motor is properly sized for the application. DC motors may or may not require feedback, depending on the application requirements and the desired level of control accuracy.
Smoothness of Rotation
DC motors provide smooth and continuous rotation, while stepper motors move in discrete steps, which can result in vibration and resonance at certain frequencies.
Noise Level
Stepper motors can produce more noise compared to DC motors, particularly at low speeds or when the motor experiences resonance. DC motors generally operate with lower noise levels.
Cost
The cost of stepper motors and DC motors can vary depending on the size, power rating, and features. In general, stepper motors tend to be more expensive than comparable DC motors due to their more complex construction and control requirements.
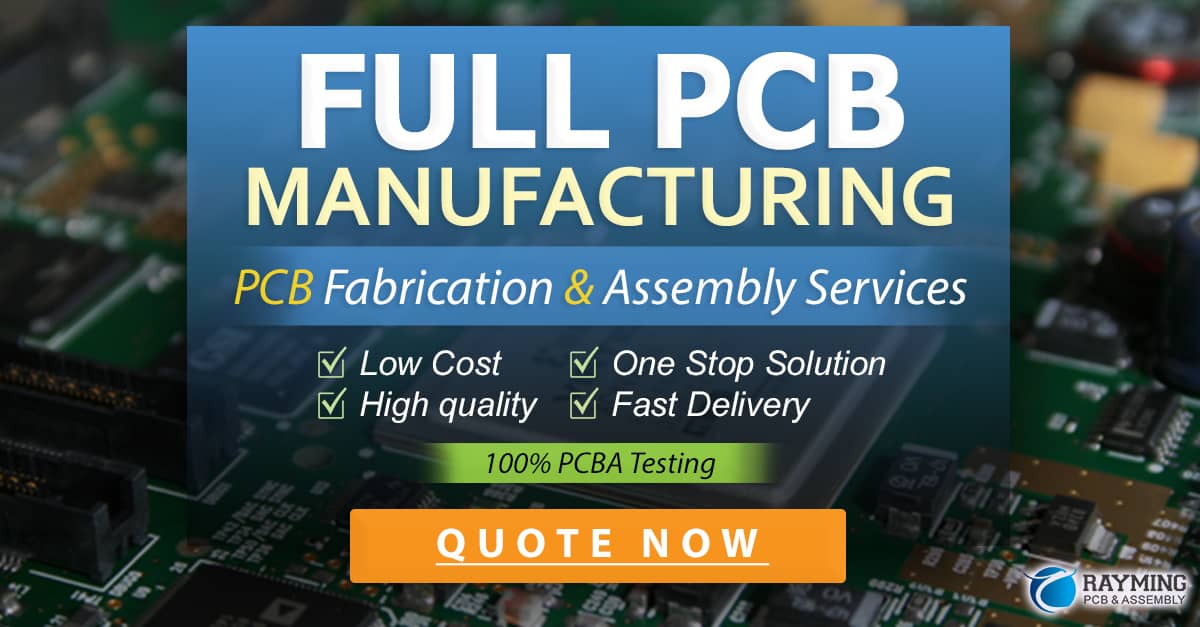
Choosing Between Stepper Motors and DC Motors
When deciding between a stepper motor and a DC motor for a particular application, consider the following factors:
- Positioning accuracy requirements
- Speed range and torque requirements
- Smoothness of rotation
- Control complexity and feedback requirements
- Efficiency and heat generation
- Noise level
- Cost and availability
In applications that prioritize precise positioning and low-speed torque, stepper motors are often the preferred choice. For applications that require high-speed operation, smooth rotation, and high efficiency, DC motors are generally more suitable.
Frequently Asked Questions (FAQ)
-
Can a stepper motor be used in place of a DC motor?
In some cases, yes, but it depends on the specific application requirements. Stepper motors are best suited for applications that require precise positioning and high torque at low speeds, while DC motors are better for applications that require high-speed operation and smooth rotation. -
How do I control the speed of a stepper motor?
The speed of a stepper motor is controlled by the frequency of the pulses sent to the motor. Higher frequencies result in faster rotation, while lower frequencies result in slower rotation. The speed can be adjusted by changing the pulse frequency using a microcontroller or a dedicated stepper motor driver. -
What is the main advantage of using a brushless DC motor over a brushed DC motor?
Brushless DC motors offer several advantages over brushed DC motors, including higher efficiency, longer lifespan, less maintenance, and reduced electromagnetic interference (EMI). They also typically provide better heat dissipation and can operate at higher speeds. -
Can a DC motor be used for precise positioning?
Yes, a DC motor can be used for precise positioning when combined with an encoder or other feedback device. The encoder provides information about the motor’s position, which can be used by a control system to adjust the motor’s position as needed. -
What is the difference between a unipolar and bipolar stepper motor?
Unipolar Stepper motors have two windings per phase, with a center tap on each winding, allowing the current to flow in only one direction. Bipolar stepper motors have a single winding per phase, and the current must be reversed to change the direction of the magnetic field. Bipolar stepper motors typically offer higher torque and efficiency, while unipolar stepper motors are simpler to control.
Conclusion
Stepper motors and DC motors are both widely used in various applications, each with its own strengths and weaknesses. Stepper motors are ideal for applications that require precise positioning, high torque at low speeds, and simple control. DC motors, on the other hand, are better suited for applications that demand high-speed operation, smooth rotation, and high efficiency.
When selecting between a stepper motor and a DC motor, it is essential to carefully consider the specific requirements of the application, such as positioning accuracy, speed range, torque, control complexity, and cost. By understanding the unique characteristics and capabilities of each motor type, engineers and designers can make informed decisions and choose the most appropriate motor for their projects.
As technology continues to advance, both stepper motors and DC motors will likely see further improvements in performance, efficiency, and cost-effectiveness. Regardless of the specific application, these two types of electric motors will undoubtedly continue to play a crucial role in driving innovation and automation across various industries.
0 Comments