What is Soldering Flux?
Soldering flux is a chemical cleaning agent used in soldering to help facilitate the soldering process. It is designed to remove oxidation from metals, prevent further oxidation during soldering, and help the solder flow more easily over the joint.
Flux comes in several forms including liquid, paste, and solid. The most common types used in electronics soldering are rosin-based fluxes which are available in various activity levels.
Types of Soldering Flux
Flux Type | Composition | Characteristics |
---|---|---|
Rosin | Pine tree sap | Mildly activated, non-corrosive, removes oxides |
Water-Soluble | Organic acids | Highly activated, corrosive, removes oxides |
No-Clean | Rosin + solvents | Mildly activated, leaves clear residue |
Why is Soldering Flux Important?
Soldering flux serves several critical functions in the soldering process:
-
Cleaning: Flux cleans the metal surfaces of oxides, dirt, and other contaminants that can prevent solder from bonding properly.
-
Protection: Flux coats the cleaned metal surfaces to prevent re-oxidation during the soldering process.
-
Improved Wetting: Flux lowers the surface tension of molten solder, allowing it to flow and spread more easily over the joint surfaces.
-
Heat Transfer: Some fluxes help transfer heat from the soldering iron to the joint, enabling the solder to melt and flow more efficiently.
Without flux, soldered joints would be prone to defects like poor wetting, voids, cold joints, and weak connections. Using the right type and amount of flux is key to creating strong, reliable solder joints.
How to Choose the Right Soldering Flux
Selecting the appropriate soldering flux depends on several factors:
Base Metals
Consider what metals you are soldering. Different fluxes work better with certain metals.
- Rosin fluxes work well with copper, brass, and solder-plated surfaces common in electronics.
- Stainless steel and cast iron require active fluxes to remove tough oxides.
- Aluminum needs special fluxes to disrupt its oxide layer.
Soldering Temperature
The soldering temperature influences flux selection. Higher temperatures call for more active fluxes to prevent oxidation. Lower temperature soldering, like that used for electronics, can use milder rosin fluxes.
Cleaning Requirements
Some fluxes, like rosin-based no-clean fluxes, are designed to be left on boards after soldering. If you need to clean off flux residue, a water-soluble flux may be easier to remove. Always defer to the recommendations for the product and process.
Activity Level
Flux activity refers to its ability to remove oxides. Increased activity usually comes with higher corrosivity and cleaning requirements. Use the lowest activity flux that yields good results for your application.
Activity Level | Flux Type | Base Metals | Residue/Cleaning |
---|---|---|---|
Low | Rosin (R) | Copper, solder, clean metals | Non-corrosive, optional cleaning |
Moderate | Rosin Activated (RMA) | Copper, brass, nickel | Slightly corrosive, cleaning recommended |
High | Water-Soluble | Stainless steel, cast iron, aluminum | Corrosive, requires cleaning |
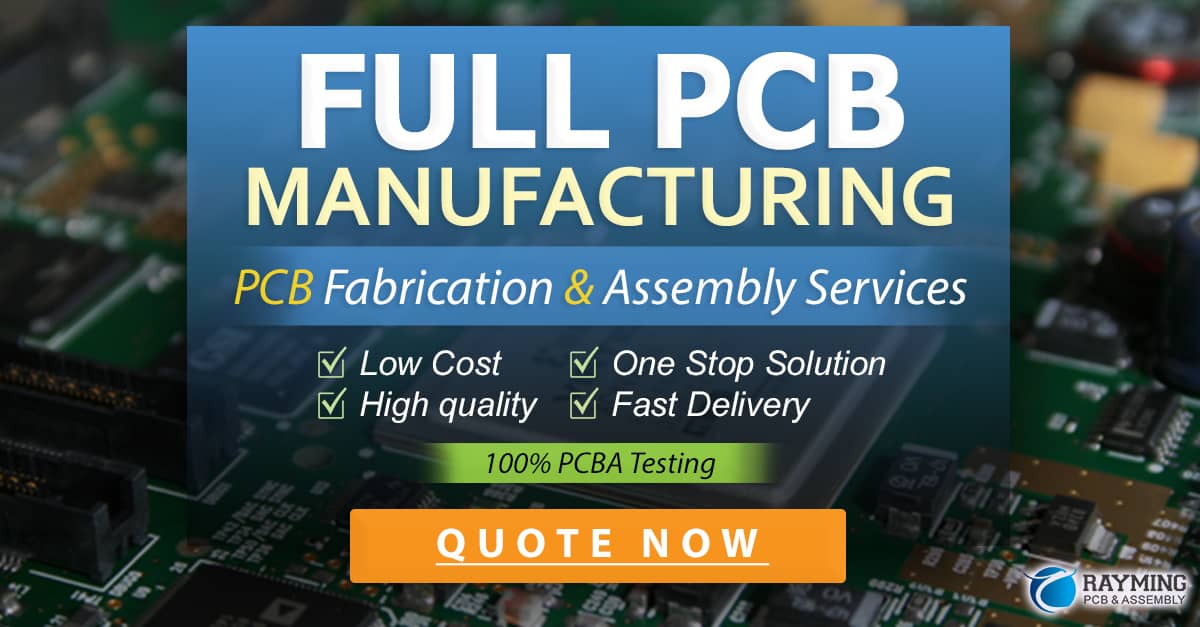
How to Apply Soldering Flux
Proper flux application is important for achieving good soldering results. Too little flux can lead to poor wetting and wicking. Too much flux can cause bridging, spatter, and excessive residue. Here are some tips:
-
Clean surfaces first to remove dirt, oils, and oxides. Flux works best on freshly cleaned metals.
-
Apply a thin, even layer of flux to the surfaces to be soldered. You can use a brush, swab, syringe, or flux pen depending on the form of flux.
-
Avoid touching fluxed areas with your skin as oils can contaminate the surface. Use tweezers or gloves if needed.
-
Apply heat and solder to the joint. The flux should melt and activate, cleaning the surfaces as the solder flows. If needed, add a bit more flux during soldering.
-
Clean flux residue after soldering if required for your flux type. Isopropyl alcohol or commercial Flux Removers can be used.
With practice, you’ll get a feel for the right amount of flux to apply for your specific soldering jobs. When in doubt, start with less and add more as needed – it’s easier than removing excess!
Soldering Flux Safety
While soldering flux is essential to the process, it’s important to handle it safely. Some key precautions:
-
Always work in a well-ventilated area when soldering to avoid breathing flux fumes. Use a fume extractor if soldering frequently.
-
Avoid skin contact with flux. Some fluxes can cause irritation or allergic reactions. Wear gloves and safety glasses.
-
Never eat or drink while handling flux. Wash hands thoroughly after soldering.
-
Keep flux containers closed when not in use to avoid contamination and spills.
-
Dispose of used flux and flux-contaminated materials per local regulations. Some fluxes contain lead or other hazardous materials.
By using appropriate protective equipment and safe handling practices, you can minimize the risks associated with soldering flux use.
FAQ
What’s the difference between flux and solder paste?
Solder paste is a mixture of powdered solder and flux. It’s used primarily for surface-mount soldering. Flux is a separate component used for through-hole and other manual soldering processes.
Can I solder without using flux?
While you may be able to solder without flux on pristine surfaces, flux is recommended to ensure proper cleaning, wetting, and joint strength, especially when working with oxidized or contaminated metals.
How long does flux last?
Shelf life depends on flux type and storage conditions. Most fluxes last 1-2 years if kept sealed and stored between 40-90°F. Water-soluble fluxes may have shorter lifespans due to evaporation. Always check expiration dates.
What happens if I use too much flux?
Excessive flux can cause solder bridging, spatter, and leave heavy residues that may be difficult to clean. It’s best to use a minimal amount of flux that still yields good results.
Is soldering flux toxic?
Some fluxes contain chemicals that can be harmful if inhaled or ingested in large amounts. Always use proper ventilation, avoid skin contact, and wash hands after handling flux. Consult safety data sheets for specific flux products.
Soldering flux is a key component in electronics soldering that ensures strong, reliable joints. By understanding the types, selection criteria, application tips, and safety precautions for flux, you’ll be well on your way to successful soldering. As with any skill, using flux effectively takes practice – but with the right techniques, you’ll be creating perfect solder joints in no time!
0 Comments