What is Solderability Testing?
Solderability testing is a crucial process in the manufacturing of printed circuit boards (PCBs) to ensure the reliability and quality of the final product. It involves evaluating the ability of component leads, pins, and PCB Pads to be effectively wetted by molten solder during the assembly process. Solderability testing helps identify potential issues that may lead to poor solder joints, which can cause electronic failures and decrease the overall reliability of the PCB.
Importance of Solderability Testing
Solderability testing is essential for several reasons:
- Quality Assurance: It ensures that the components and PCB pads can form reliable solder joints, reducing the risk of defects and failures.
- Cost Reduction: By identifying solderability issues early in the manufacturing process, costly rework and repairs can be avoided.
- Compliance: Solderability testing helps manufacturers meet industry standards and customer requirements for quality and reliability.
Types of Solderability Tests
There are various methods used to assess the solderability of components and PCBs. Some of the most common solderability tests include:
1. Wetting Balance Test
The wetting balance test, also known as the dip and look test, is a quantitative method to evaluate the solderability of component leads or PCB pads. In this test, the component lead or PCB coupon is dipped into a bath of molten solder for a specified time and then withdrawn. The wetting force, which is the force exerted by the molten solder on the lead or pad, is measured and recorded.
Wetting Balance Test Procedure
- Prepare the component lead or PCB coupon for testing.
- Set the appropriate testing parameters, such as solder temperature, dipping depth, and dwell time.
- Dip the lead or coupon into the molten solder bath.
- Measure and record the wetting force using a wetting balance tester.
- Analyze the results and compare them to the specified requirements.
2. Meniscograph Test
The meniscograph test is another quantitative method for evaluating solderability. It measures the wetting force and wetting time of a component lead or PCB pad when it comes in contact with molten solder. The test is performed using a meniscograph machine, which records the wetting force over time.
Meniscograph Test Procedure
- Prepare the component lead or PCB coupon for testing.
- Set the appropriate testing parameters, such as solder temperature and dwell time.
- Place the lead or coupon on the meniscograph machine’s test platform.
- Bring the lead or coupon into contact with the molten solder.
- Record the wetting force and wetting time using the meniscograph machine.
- Analyze the results and compare them to the specified requirements.
3. Spread Test
The spread test is a qualitative method for assessing the solderability of component leads or PCB pads. In this test, a small amount of solder paste is applied to the lead or pad, and then the component is heated to the solder’s melting temperature. The extent of solder spread on the lead or pad is visually inspected and evaluated.
Spread Test Procedure
- Prepare the component lead or PCB coupon for testing.
- Apply a small amount of solder paste to the lead or pad.
- Place the component on a hotplate or reflow oven.
- Heat the component to the solder’s melting temperature.
- Visually inspect the solder spread on the lead or pad.
- Evaluate the results based on the specified criteria, such as percentage of area covered by solder.
Factors Affecting Solderability
Several factors can influence the solderability of components and PCBs, including:
-
Surface Finish: The type and quality of the surface finish on component leads and PCB pads can impact solderability. Common surface finishes include hot air solder leveling (HASL), immersion silver, immersion tin, and electroless nickel immersion gold (ENIG).
-
Storage Conditions: Improper storage of components and PCBs can lead to oxidation and contamination of the surfaces, which can degrade solderability. It is essential to store components and PCBs in a controlled environment with appropriate temperature, humidity, and packaging.
-
Aging: Over time, the solderability of components and PCBs can deteriorate due to oxidation and other chemical changes. Solderability testing should be performed periodically to ensure that the components and PCBs remain within acceptable limits.
-
Solder Alloy: The composition of the solder alloy used in the assembly process can affect solderability. Different solder alloys have varying wetting characteristics and melting temperatures, which can impact the formation of reliable solder joints.
-
Flux: The type and quality of the flux used during soldering can influence solderability. Flux helps remove oxides and contaminants from the surfaces, promoting better wetting and solder joint formation.
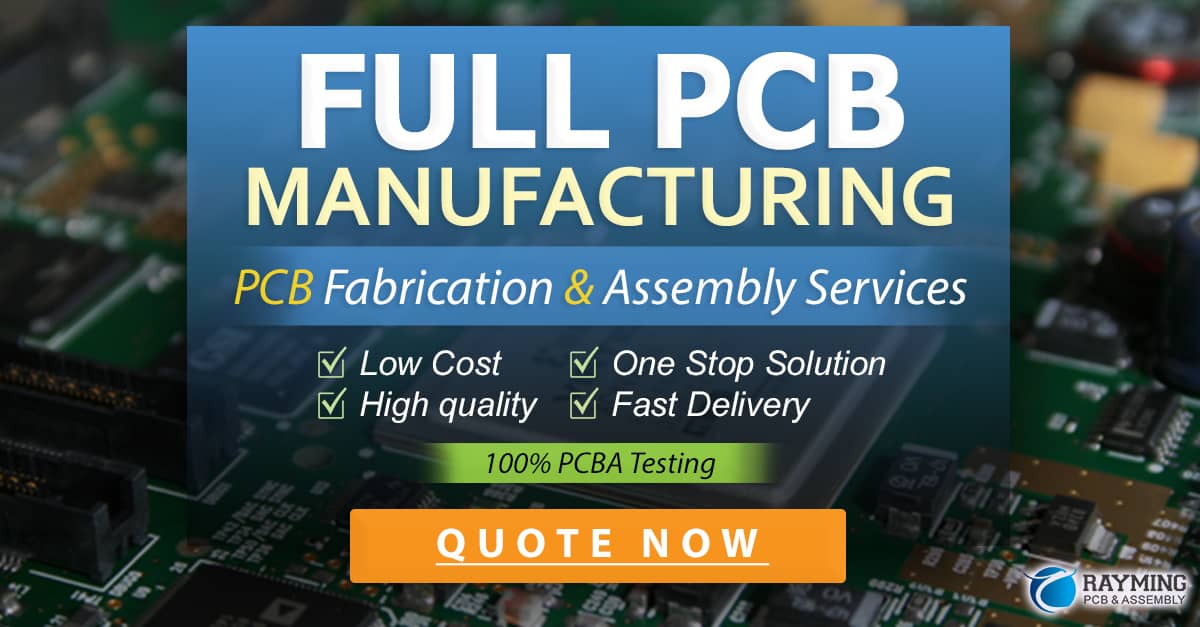
Solderability Test Standards
Several industry standards provide guidelines and requirements for solderability testing, including:
- IPC J-STD-002: Solderability Tests for Component Leads, Terminations, Lugs, Terminals, and Wires
- IPC J-STD-003: Solderability Tests for Printed Boards
- MIL-STD-883: Test Method Standard, Microcircuits
- EIA-364: Electrical Connector/Socket Test Procedures Including Environmental Classifications
These standards specify the test methods, procedures, and acceptance criteria for solderability testing of various electronic components and PCBs.
Interpreting Solderability Test Results
Interpreting the results of solderability tests is crucial for making informed decisions about the quality and reliability of components and PCBs. The following table provides an overview of typical solderability test results and their implications:
Test Result | Interpretation | Implications |
---|---|---|
Good Wetting | The solder readily wets the surface, forming a uniform and continuous solder coating. | The component or PCB is likely to form reliable solder joints during the assembly process. |
Poor Wetting | The solder does not wet the surface adequately, resulting in incomplete or discontinuous solder coverage. | The component or PCB may experience soldering difficulties and potentially form weak or defective solder joints. |
Non-Wetting | The solder does not wet the surface at all, forming beads or droplets instead of a continuous coating. | The component or PCB is likely to fail during the assembly process and may require rework or replacement. |
It is essential to compare the solderability test results to the specified requirements and industry standards to determine whether the components or PCBs meet the necessary criteria for reliable soldering.
Solderability Testing Equipment
Various equipment is used to perform solderability tests, depending on the specific test method employed. Some common solderability testing equipment includes:
-
Wetting Balance Tester: Used for the wetting balance test, this equipment measures the wetting force of a component lead or PCB pad when dipped into molten solder.
-
Meniscograph Machine: Employed for the meniscograph test, this machine records the wetting force and wetting time of a component lead or PCB pad when brought into contact with molten solder.
-
Dipping Pot: A container used to hold molten solder for the wetting balance and meniscograph tests. The dipping pot maintains the solder at a constant temperature and ensures a consistent testing environment.
-
Hotplate or Reflow Oven: Used for the spread test, a hotplate or reflow oven is employed to heat the component and melt the solder paste applied to the lead or pad.
-
Microscope: A microscope is often used to visually inspect the solder spread and wetting characteristics of component leads and PCB pads during the spread test.
Frequently Asked Questions (FAQ)
-
What is the purpose of solderability testing?
Solderability testing is performed to evaluate the ability of component leads, pins, and PCB pads to be effectively wetted by molten solder during the assembly process. It helps ensure the formation of reliable solder joints and identifies potential issues that may lead to defects or failures. -
How often should solderability testing be performed?
The frequency of solderability testing depends on various factors, such as the component type, storage conditions, and industry requirements. Typically, solderability testing is performed on incoming components, before assembly, and periodically during the product’s life cycle to monitor any changes in solderability. -
What are the consequences of poor solderability?
Poor solderability can lead to several issues, including: - Difficulty in forming reliable solder joints during the assembly process
- Increased risk of defects and failures in the final product
- Reduced product reliability and performance
-
Increased rework and repair costs
-
Can solderability be improved if a component fails the test?
In some cases, solderability can be improved through various methods, such as: - Cleaning the component leads or PCB pads to remove oxides and contaminants
- Applying a fresh surface finish to the leads or pads
-
Using a more active flux during the soldering process
However, if the solderability issues are severe or the component has been damaged, replacement may be necessary. -
Are there any environmental concerns associated with solderability testing?
Yes, solderability testing involves the use of molten solder, which may contain lead or other hazardous substances. Proper safety measures, such as ventilation and personal protective equipment, should be employed to minimize exposure to harmful fumes and materials. Additionally, the disposal of used solder and cleaning solutions should be done in accordance with local environmental regulations.
Conclusion
Solderability testing is a vital process in the manufacturing of PCBs and electronic assemblies. It ensures that components and PCBs can form reliable solder joints, minimizing the risk of defects and failures in the final product. By understanding the different types of solderability tests, factors affecting solderability, and industry standards, manufacturers can effectively evaluate and control the quality of their components and PCBs.
Implementing a robust solderability testing program, along with proper storage and handling practices, can lead to improved product reliability, reduced rework and repair costs, and increased customer satisfaction. As the electronics industry continues to evolve, staying up-to-date with the latest solderability testing methods and requirements will be essential for maintaining a competitive edge in the market.
0 Comments