What is Solder?
Solder is a metal alloy used to join two or more metal surfaces together. It is typically composed of tin and lead, although lead-free solder alloys are becoming increasingly common due to health and environmental concerns. Solder melts at a relatively low temperature, allowing it to flow into the joint between the metal surfaces, creating a strong electrical and mechanical bond when it cools and solidifies.
Types of Solder
There are two main types of solder: leaded and lead-free.
-
Leaded Solder: Traditionally, solder was composed of a mixture of tin and lead. The most common ratio was 60% tin and 40% lead (Sn60/Pb40). Leaded solder has a lower melting point and is easier to work with compared to lead-free solder. However, due to health and environmental concerns, the use of leaded solder has been restricted in many countries.
-
Lead-Free Solder: Lead-free solder alloys have been developed to replace leaded solder. These alloys typically contain tin, silver, and copper (SAC alloys). The most common lead-free solder alloy is Sn96.5/Ag3.0/Cu0.5 (SAC305). Lead-free solder has a higher melting point and requires more precise temperature control during the soldering process.
Solder Type | Composition | Melting Point |
---|---|---|
Leaded | Sn60/Pb40 | 183-190°C |
Lead-Free | SAC305 | 217-220°C |
Solder Forms
Solder is available in various forms to suit different soldering applications:
Wire Solder
Wire solder is the most common form of solder used in electronics assembly. It consists of a solder alloy core surrounded by a flux coating. The flux helps to remove oxides from the metal surfaces and promotes the flow of the molten solder. Wire solder is available in different diameters, alloy compositions, and flux types to suit various soldering needs.
Solder Paste
Solder paste is a mixture of tiny solder particles suspended in a flux medium. It is used in surface mount technology (SMT) assembly, where it is applied to the pads on a printed circuit board (PCB) using a stencil or syringe. The components are then placed on the pads, and the entire assembly is heated in a reflow oven, melting the solder particles and creating the solder joints.
Solder Bar
Solder bars are large, solid pieces of solder alloy used in wave soldering machines. In wave soldering, the PCB is passed over a molten wave of solder, which creates the solder joints on the bottom side of the board. Solder bars are melted in the wave soldering machine to maintain the solder wave.
Solder Preforms
Solder preforms are precisely shaped pieces of solder designed for specific applications. They can be in the form of rings, discs, or custom shapes. Solder preforms are often used in automated assembly processes, where they are placed on the components or PCB before the soldering process.
Flux in Soldering
Flux is a chemical compound used in soldering to remove oxides from the metal surfaces, prevent oxidation during the soldering process, and promote the flow of the molten solder. There are three main types of flux:
-
Rosin Flux: Rosin flux is a natural, non-corrosive flux derived from pine resin. It is available in various activity levels, ranging from mild (R) to activated (RA) and highly activated (RSA). Rosin flux is suitable for most electronics soldering applications and can be easily cleaned with solvents.
-
Water-Soluble Flux: Water-soluble flux is a more aggressive, inorganic acid flux that provides excellent oxide removal. It requires thorough cleaning after soldering, as the flux residues are corrosive and can cause long-term reliability issues if left on the assembly.
-
No-Clean Flux: No-clean flux is a mild, rosin-based flux that leaves minimal, non-corrosive residues after soldering. These residues do not require cleaning, making no-clean flux popular in applications where post-soldering cleaning is not feasible or desirable.
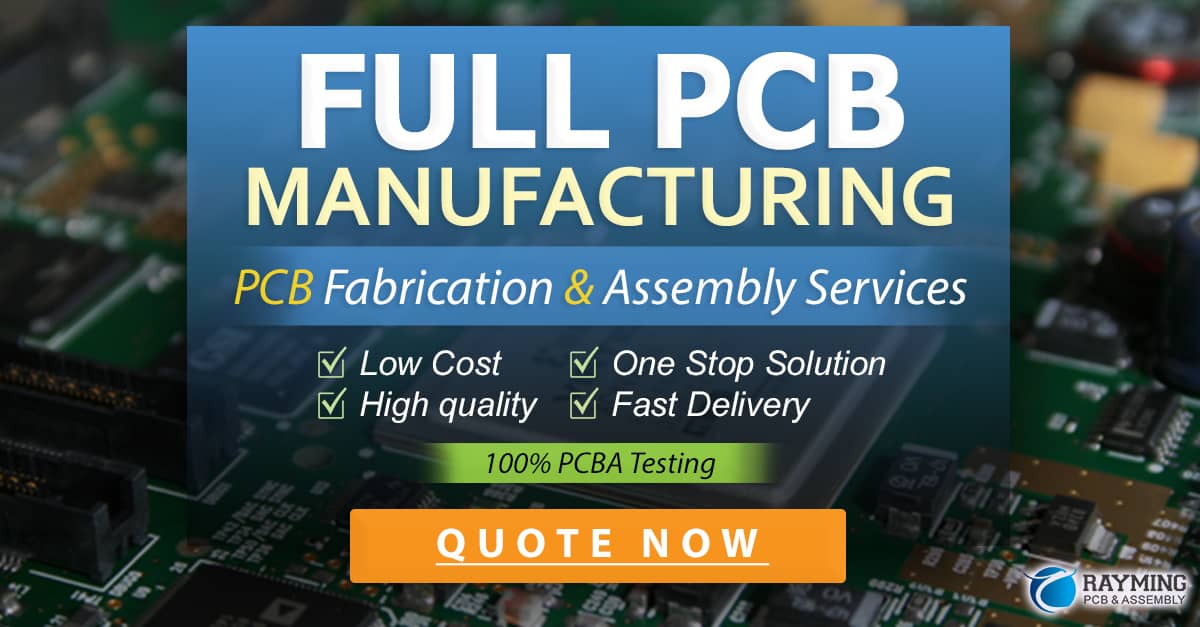
Soldering Techniques
There are several soldering techniques used in electronics assembly, depending on the components, PCB design, and production volume:
Hand Soldering
Hand soldering is a manual technique where a soldering iron is used to heat the solder and the components, creating the solder joint. This technique is suitable for low-volume production, prototyping, and repair work. Proper technique, temperature control, and tip maintenance are essential for achieving reliable solder joints.
Wave Soldering
Wave soldering is an automated process used for through-hole component assembly. The PCB is passed over a molten wave of solder, which creates the solder joints on the bottom side of the board. Wave soldering is suitable for high-volume production and provides a reliable and efficient way to solder through-hole components.
Reflow Soldering
Reflow soldering is an automated process used for surface mount component assembly. Solder paste is applied to the pads on the PCB, and the components are placed on the pads. The entire assembly is then heated in a reflow oven, melting the solder particles and creating the solder joints. Reflow soldering is suitable for high-volume production and provides a reliable and efficient way to solder surface mount components.
Selective Soldering
Selective soldering is an automated process used for soldering specific areas or components on a PCB. It combines the advantages of hand soldering and wave soldering, allowing for precise control over the soldering process. Selective soldering is suitable for mixed-technology assemblies, where both through-hole and surface mount components are present.
Soldering Safety and Best Practices
Soldering involves high temperatures and exposure to chemicals, so it is essential to follow safety guidelines and best practices:
-
Ventilation: Always solder in a well-ventilated area to avoid inhaling flux fumes and solder particles. Use a fume extractor or work under a ventilated hood if possible.
-
Eye and Skin Protection: Wear safety glasses to protect your eyes from solder splashes and flux fumes. Avoid skin contact with molten solder and flux by wearing protective gloves.
-
Temperature Control: Use the appropriate soldering iron temperature for the solder alloy and components being soldered. Excessive temperature can damage components and cause poor solder joint quality.
-
Tip Maintenance: Keep the soldering iron tip clean and tinned with solder to ensure optimal heat transfer and prevent oxidation. Use a damp sponge or brass wool to clean the tip periodically.
-
Flux Selection: Choose the appropriate flux type for the soldering application, considering the cleaning requirements and the potential for corrosion.
-
Cleaning: Clean the soldered assembly thoroughly if using water-soluble or corrosive fluxes to prevent long-term reliability issues.
-
Proper Technique: Use the correct soldering technique for the components and PCB design, ensuring adequate heat transfer and avoiding bridging or cold solder joints.
Frequently Asked Questions (FAQ)
-
What is the difference between leaded and lead-free solder?
Leaded solder contains a mixture of tin and lead, typically in a 60/40 ratio. Lead-free solder, on the other hand, is composed of tin, silver, and copper (SAC alloys). Lead-free solder has a higher melting point and requires more precise temperature control during soldering. -
Why is lead-free solder preferred over leaded solder?
Lead-free solder is preferred due to health and environmental concerns. Lead is a toxic substance that can cause harm to human health and the environment. Many countries have restricted or banned the use of leaded solder in electronics manufacturing. -
What is the purpose of flux in soldering?
Flux is used in soldering to remove oxides from the metal surfaces, prevent oxidation during the soldering process, and promote the flow of the molten solder. It helps to ensure a strong and reliable solder joint. -
Can I mix different types of solder?
Mixing different types of solder is not recommended, as it can lead to compatibility issues and poor solder joint quality. It is best to use the same type of solder throughout an assembly to ensure consistent performance. -
How do I choose the right soldering iron temperature?
The appropriate soldering iron temperature depends on the solder alloy and the components being soldered. Generally, leaded solder requires a lower temperature (around 300-350°C) compared to lead-free solder (around 350-400°C). Always refer to the solder manufacturer’s recommendations and the component datasheets for specific temperature guidelines.
In conclusion, understanding solder products, their forms, and the various soldering techniques is essential for achieving reliable and high-quality solder joints in electronics assembly. By selecting the appropriate solder alloy, flux, and soldering method, and following safety guidelines and best practices, you can ensure the long-term performance and reliability of your electronic devices.
0 Comments