What is an SMT Chip?
SMT stands for Surface Mount Technology. An SMT chip, also known as a surface mount device (SMD), is an electronic component that is designed to be mounted directly onto the surface of a printed circuit board (PCB). Unlike through-hole components that require leads to be inserted into holes drilled in the PCB, SMT components are soldered onto pads or lands on the surface of the board.
SMT chips come in various package types and sizes, such as:
Package Type | Description |
---|---|
QFP | Quad Flat Package, a rectangular package with leads on 4 sides |
QFN | Quad Flat No-leads, similar to QFP but without leads |
BGA | Ball Grid Array, a package with solder balls arranged in a grid |
CSP | Chip Scale Package, a small package with a size close to the die |
The use of SMT components has revolutionized the electronics manufacturing industry by enabling the production of smaller, lighter, and more densely populated PCBs. SMT assembly is also faster and more automated compared to through-hole assembly, resulting in lower manufacturing costs.
What is Terminal Lifting?
Terminal lifting, also known as pad lifting or land lifting, is a defect that can occur during the SMT assembly process. It happens when the pad or land on the PCB separates from the board, causing the solder joint to break and the component to lose electrical and mechanical connection.
Terminal lifting can be caused by various factors, such as:
- Poor PCB design or fabrication
- Improper solder paste application
- Incorrect reflow profile
- Mechanical stress during handling or testing
Terminal lifting is a serious defect that can lead to intermittent or complete failure of the electronic device. It is especially problematic for SMT chips with fine-pitch leads or small pads, as they are more susceptible to lifting due to their size and spacing.
How to Prevent Terminal Lifting
Preventing terminal lifting requires careful attention to the design, fabrication, and assembly processes. Here are some best practices to minimize the risk of terminal lifting:
PCB Design
- Use appropriate pad sizes and shapes for the specific component package
- Provide adequate support for the pads with vias and copper pour
- Avoid placing pads too close to the edge of the board or other features
- Use solder mask to prevent solder bridging and improve adhesion
PCB Fabrication
- Use high-quality base materials and copper foils
- Ensure proper etching and plating of the pads
- Apply solder mask evenly and with good registration
- Clean the PCB thoroughly before assembly
SMT Assembly
- Use solder paste with the correct composition and viscosity for the specific component and PCB
- Apply solder paste using a stencil with the appropriate aperture sizes and shapes
- Control the reflow profile to achieve proper wetting and avoid overheating
- Handle the PCB and components carefully to avoid mechanical stress
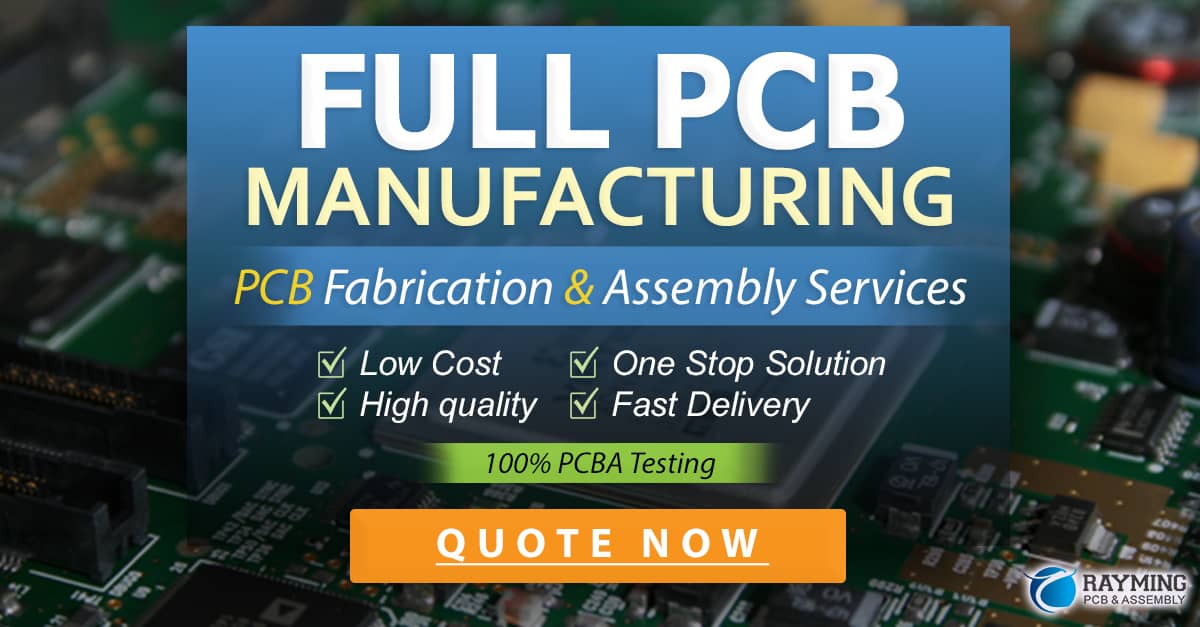
How to Detect Terminal Lifting
Terminal lifting can be difficult to detect visually, especially for small or hidden components. Here are some methods to detect terminal lifting:
Visual Inspection
- Use a magnifying lens or microscope to examine the solder joints for signs of lifting, such as cracks, gaps, or discoloration
- Look for components that are tilted, shifted, or missing
- Check for solder bridging or excessive solder on the pads
X-Ray Inspection
- Use X-ray imaging to see through the component and inspect the solder joints
- Look for voids, cracks, or insufficient solder coverage
- Compare the X-ray image to a reference image of a good solder joint
Electrical Testing
- Use in-circuit testing (ICT) or flying probe testing to verify the electrical continuity and resistance of the solder joints
- Apply mechanical stress to the board while monitoring for intermittent or open circuits
- Use boundary scan testing to detect opens, shorts, and other defects on boards with JTAG-compliant components
How to Repair Terminal Lifting
If terminal lifting is detected, it may be possible to repair the defect depending on the severity and location of the lifting. Here are some methods to repair terminal lifting:
Manual Soldering
- Use a fine-tip soldering iron and flux to reflow the solder joint and reattach the pad to the board
- Be careful not to apply too much heat or pressure, as this can cause further damage
- Clean the repaired joint thoroughly to remove any flux residue
Epoxy Bonding
- Use a conductive epoxy to bond the lifted pad back to the board
- Apply the epoxy carefully to avoid shorting adjacent pads or components
- Allow the epoxy to cure fully before testing the joint
Pad Replacement
- If the pad is severely damaged or missing, it may be necessary to replace it with a new pad
- Use a sharp knife or milling machine to remove the old pad and expose the underlying copper
- Apply a new pad using a conductive adhesive or solder paste
- Reflow the solder joint to attach the component to the new pad
FAQ
What are the most common causes of terminal lifting?
The most common causes of terminal lifting are:
- Poor PCB design or fabrication, such as inadequate pad support or incorrect etching
- Improper solder paste application, such as insufficient or excessive solder volume
- Incorrect reflow profile, such as overheating or insufficient wetting
- Mechanical stress during handling or testing, such as bending or twisting the board
Can terminal lifting be prevented entirely?
While it may not be possible to prevent terminal lifting entirely, following best practices in PCB design, fabrication, and assembly can significantly reduce the risk of this defect occurring. Proper process control and quality assurance measures are essential to minimizing the incidence of terminal lifting.
Is it always necessary to repair terminal lifting?
The decision to repair terminal lifting depends on the severity and impact of the defect. Minor lifting that does not affect the electrical or mechanical integrity of the solder joint may be acceptable in some cases. However, severe lifting that causes intermittent or complete failure of the device must be repaired to ensure reliability and performance.
Can terminal lifting occur in through-hole components?
While terminal lifting is more common in SMT components due to their smaller size and spacing, it can also occur in through-hole components. Through-hole pads can lift from the board due to poor plating, mechanical stress, or thermal cycling. However, through-hole components are generally more robust and less susceptible to lifting compared to SMT components.
How can I improve my PCB design to prevent terminal lifting?
To improve your PCB design and prevent terminal lifting, consider the following tips:
- Use appropriate pad sizes and shapes for the specific component package
- Provide adequate support for the pads with vias and copper pour
- Avoid placing pads too close to the edge of the board or other features
- Use solder mask to prevent solder bridging and improve adhesion
- Follow the manufacturer’s recommendations for pad layout and design rules
By following these guidelines and working closely with your PCB fabricator and assembly provider, you can create PCBs that are more resistant to terminal lifting and other defects.
0 Comments