Introduction to PCBA Testing
Printed Circuit Board Assembly (PCBA) is a crucial process in the manufacturing of electronic devices. To ensure the quality and reliability of the final product, various test and inspection methods are employed at different stages of the PCBA process. These methods help identify defects, ensure proper functionality, and maintain the overall quality of the assembled PCBs.
In this article, we will explore several PCBA test and inspection methods, their importance, and how they contribute to the production of high-quality electronic devices.
Visual Inspection
Manual Visual Inspection
Manual visual inspection is the most basic and essential method of PCBA testing. Skilled operators visually inspect the assembled PCBs for any obvious defects, such as:
- Solder bridges
- Cold solder joints
- Misaligned components
- Incorrect component placement
- Damaged components
While manual visual inspection is simple and cost-effective, it is prone to human error and may not detect subtle defects.
Automated Optical Inspection (AOI)
Automated Optical Inspection (AOI) is a more advanced form of visual inspection that uses high-resolution cameras and image processing software to detect defects on the assembled PCBs. AOI systems can identify various defects, including:
- Solder defects (bridges, insufficient solder, etc.)
- Component placement errors
- Missing or incorrect components
- Polarity issues
- Trace and pad defects
AOI systems offer several advantages over manual inspection, such as:
- Higher speed and throughput
- Improved accuracy and consistency
- Ability to detect smaller and more subtle defects
- Reduced human error and fatigue
Electrical Testing
In-Circuit Testing (ICT)
In-Circuit Testing (ICT) is a method that verifies the electrical connectivity and functionality of individual components on the assembled PCB. ICT systems use a bed-of-nails fixture that makes contact with specific test points on the PCB, allowing the system to:
- Measure component values (resistors, capacitors, inductors, etc.)
- Test for short circuits and open circuits
- Verify the presence and orientation of components
- Perform functional tests on individual components
ICT is an essential test method for detecting defects that may not be visible during visual inspection, ensuring the proper functionality of the assembled PCBs.
Flying Probe Testing
Flying Probe Testing is an alternative to ICT that uses movable test probes instead of a fixed bed-of-nails fixture. The probes move across the PCB, making contact with test points and performing electrical measurements. Flying Probe Testing offers several advantages, such as:
- Flexibility in testing different PCB designs
- No need for custom test fixtures
- Ability to test both sides of the PCB
- Reduced setup time and cost
However, Flying Probe Testing is generally slower than ICT and may not be suitable for high-volume production.
Boundary Scan Testing (BST)
Boundary Scan Testing (BST) is a method that verifies the functionality of digital components and their interconnections on the assembled PCB. BST relies on a built-in test architecture called Joint Test Action Group (JTAG), which is implemented in many digital components, such as microprocessors, FPGAs, and ASICs.
BST allows for:
- Testing the interconnections between digital components
- Verifying the functionality of individual components
- Programming and debugging of components
- Detecting faults such as short circuits, open circuits, and stuck-at faults
BST is particularly useful for testing complex digital circuits and high-density PCBs, where physical access to test points may be limited.
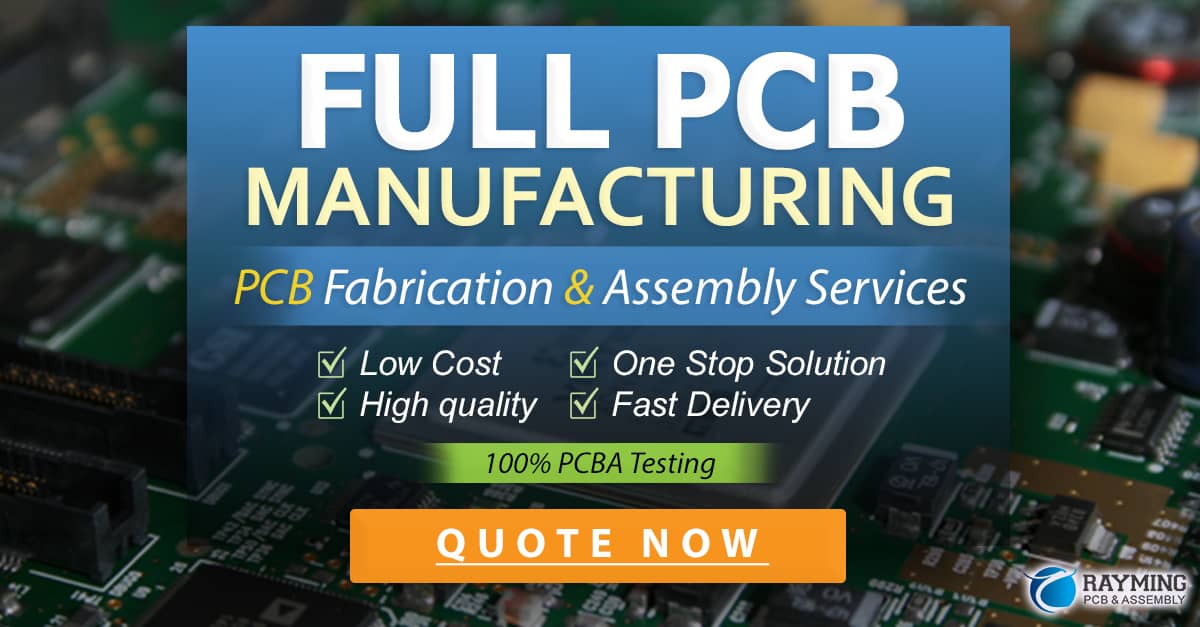
X-Ray Inspection
X-Ray Inspection is a non-destructive testing method that uses X-rays to examine the internal structure of the assembled PCBs. This method is particularly useful for inspecting:
- Ball Grid Array (BGA) and other area array packages
- Flip-chip devices
- Solder joints under components
- Voids, cracks, and other defects in solder joints
X-Ray Inspection systems can be either 2D or 3D, with 3D systems providing more detailed and accurate images of the internal structure of the PCBs.
Functional Testing
Functional Testing is a method that verifies the overall functionality and performance of the assembled PCBs under real-world operating conditions. This testing method involves:
- Powering up the PCB
- Applying input signals
- Measuring output signals
- Verifying the PCB’s functionality against its specifications
Functional Testing is typically performed after the PCB has passed all other test and inspection methods, ensuring that the final product meets the desired performance and quality standards.
Importance of PCBA Testing
PCBA testing is essential for ensuring the quality, reliability, and functionality of electronic devices. By employing various test and inspection methods, manufacturers can:
- Detect and correct defects early in the production process
- Reduce the risk of product failures and recalls
- Improve product quality and customer satisfaction
- Minimize production costs by catching defects before final assembly
- Ensure compliance with industry standards and regulations
Conclusion
In conclusion, PCBA testing is a critical aspect of the electronic device manufacturing process. By implementing a combination of visual inspection, electrical testing, X-ray inspection, and functional testing methods, manufacturers can ensure the production of high-quality, reliable, and functionally sound electronic devices.
Frequently Asked Questions (FAQ)
1. What is the difference between ICT and Flying Probe Testing?
In-Circuit Testing (ICT) uses a fixed bed-of-nails fixture to make contact with test points on the PCB, while Flying Probe Testing uses movable test probes. ICT is faster and more suitable for high-volume production, while Flying Probe Testing offers more flexibility in testing different PCB designs.
2. Can X-Ray Inspection detect all types of defects?
X-Ray Inspection is particularly useful for detecting defects in area array packages, flip-chip devices, and solder joints under components. However, it may not detect all types of defects, such as surface-level defects or functional issues.
3. Is Functional Testing necessary if the PCB has passed all other test and inspection methods?
Yes, Functional Testing is necessary to verify the overall functionality and performance of the assembled PCBs under real-world operating conditions. It ensures that the final product meets the desired performance and quality standards.
4. How does PCBA testing help reduce production costs?
PCBA testing helps reduce production costs by catching defects early in the production process, before final assembly. This minimizes the risk of product failures and recalls, which can be costly to manufacturers.
5. What role does PCBA testing play in ensuring compliance with industry standards and regulations?
PCBA testing helps ensure that electronic devices meet industry standards and regulations by verifying their quality, reliability, and functionality. Compliance with these standards is essential for market acceptance and customer satisfaction.
Test Method | Defects Detected | Advantages | Limitations |
---|---|---|---|
Manual Visual Inspection | Obvious defects (solder bridges, misaligned components, etc.) | Simple and cost-effective | Prone to human error, may not detect subtle defects |
Automated Optical Inspection (AOI) | Solder defects, component placement errors, trace and pad defects | High speed, improved accuracy, detects subtle defects | Cannot detect internal or functional defects |
In-Circuit Testing (ICT) | Component values, short circuits, open circuits, component functionality | Detects defects not visible during visual inspection | Requires custom test fixtures, limited to accessible test points |
Flying Probe Testing | Similar to ICT | Flexibility in testing different PCB designs, reduced setup time and cost | Slower than ICT, may not be suitable for high-volume production |
Boundary Scan Testing (BST) | Interconnections between digital components, component functionality | Useful for testing complex digital circuits and high-density PCBs | Limited to digital components with JTAG support |
X-Ray Inspection | BGA and area array packages, flip-chip devices, solder joint defects | Non-destructive, inspects internal structure of PCBs | May not detect surface-level or functional defects |
Functional Testing | Overall functionality and performance of assembled PCBs | Verifies PCB functionality under real-world operating conditions | Performed after all other test and inspection methods |
0 Comments