What is a Cable Assembly?
A cable assembly is a group of cables or wires that are bundled together and terminated with connectors on one or both ends. These assemblies are designed to transmit electrical signals or power between two points in an electrical system. Cable assemblies can be custom-made to suit specific applications and are often used in industries such as telecommunications, automotive, aerospace, and consumer electronics.
Components of a Cable Assembly
A typical cable assembly consists of the following components:
- Cables or wires
- Connectors
- Strain relief
- Shielding (optional)
- Labeling or marking
Types of Cable Assemblies
There are several types of cable assemblies, each designed for specific applications or environments:
- Ribbon cable assemblies
- Coaxial cable assemblies
- Multi-conductor cable assemblies
- Flat cable assemblies
- Twisted pair cable assemblies
Applications of Cable Assemblies
Cable assemblies are used in a wide range of applications, including:
- Data transmission
- Power distribution
- Signal transmission
- Telecommunications
- Automotive systems
- Aerospace systems
- Medical devices
What is a Wire Harness?
A wire harness, also known as a wiring harness or wiring loom, is a collection of wires, cables, and connectors that are bundled together to transmit electrical signals or power throughout a system. Wire harnesses are designed to simplify the installation and maintenance of complex electrical systems by organizing and routing wires in a logical manner. They are commonly used in industries such as automotive, aerospace, and heavy equipment manufacturing.
Components of a Wire Harness
A typical wire harness consists of the following components:
- Wires
- Connectors
- Terminals
- Splices
- Protective covering (e.g., tape, conduit, or braiding)
- Labeling or marking
Types of Wire Harnesses
Wire harnesses can be categorized based on their application or the method of construction:
- Main wire harnesses
- Engine wire harnesses
- Chassis wire harnesses
- Braided wire harnesses
- Taped wire harnesses
Applications of Wire Harnesses
Wire harnesses are used in various applications, including:
- Automotive systems (e.g., engine, chassis, and interior)
- Aerospace systems
- Heavy equipment
- Industrial machinery
- Appliances
- Medical devices
Cable Assembly vs Wire Harness: Key Differences
While cable assemblies and wire harnesses serve similar purposes, there are several key differences between the two:
Characteristic | Cable Assembly | Wire Harness |
---|---|---|
Purpose | Transmit signals or power between two points | Distribute signals or power throughout a system |
Construction | Bundled cables or wires with connectors on one or both ends | Bundled wires, cables, and connectors organized and routed throughout a system |
Flexibility | Less flexible due to thicker cables and more robust construction | More flexible and able to conform to tight spaces |
Complexity | Generally less complex than wire harnesses | Can be highly complex, with numerous branches and connections |
Customization | Often custom-made for specific applications | Typically custom-designed for a specific system or vehicle |
Environment | Can be designed for various environments, including harsh conditions | Often designed for specific environmental conditions (e.g., temperature, vibration, and moisture) |
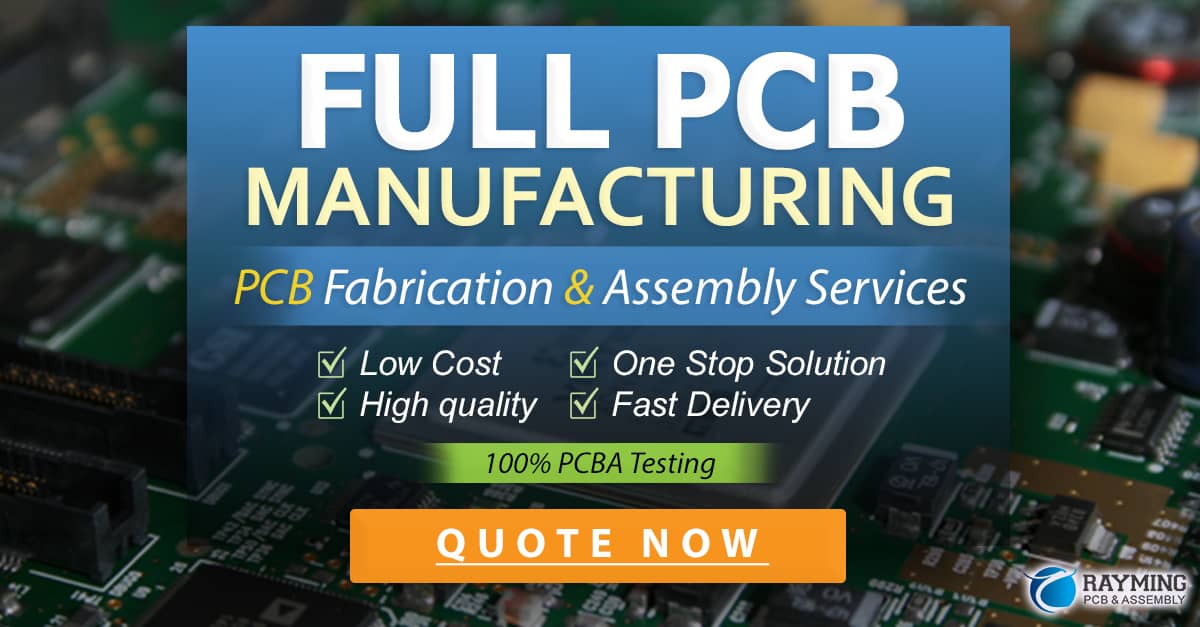
Choosing Between a Cable Assembly and Wire Harness
When deciding between a cable assembly and a wire harness, consider the following factors:
- Application requirements
- Signal or power transmission needs
- Environmental conditions
- Space constraints
- Complexity of the system
- Cost and lead time
In general, cable assemblies are better suited for point-to-point signal or power transmission, while wire harnesses are ideal for distributing signals or power throughout a complex system. However, the specific requirements of your application will ultimately dictate the best choice.
Best Practices for Designing and Manufacturing Cable Assemblies and Wire Harnesses
To ensure the optimal performance and reliability of your cable assemblies or wire harnesses, consider the following best practices:
- Clearly define requirements and specifications
- Choose appropriate materials and components
- Use reliable suppliers and manufacturers
- Implement proper labeling and marking
- Conduct thorough testing and quality control
- Consider serviceability and maintenance
FAQ
-
Q: Can a cable assembly be used in place of a wire harness?
A: While cable assemblies and wire harnesses serve similar purposes, they are not always interchangeable. The choice between the two depends on the specific requirements of your application, such as signal or power transmission needs, environmental conditions, and system complexity. -
Q: How do I choose the right connectors for my cable assembly or wire harness?
A: When selecting connectors, consider factors such as the number of contacts, current rating, voltage rating, environmental resistance, and mating cycles. Consult with your supplier or manufacturer to ensure that you choose connectors that meet your application’s requirements. -
Q: What is the difference between a braided wire harness and a taped wire harness?
A: A braided wire harness uses a braided protective covering to bundle and protect the wires, while a taped wire harness uses tape to hold the wires together. Braided wire harnesses offer better abrasion resistance and durability, while taped wire harnesses are generally less expensive and easier to assemble. -
Q: How can I ensure the reliability of my cable assembly or wire harness?
A: To ensure reliability, use high-quality materials and components, follow best practices for design and manufacturing, and conduct thorough testing and quality control. Additionally, consider factors such as environmental conditions, vibration, and temperature when designing your assembly or harness. -
Q: What is the typical lead time for custom cable assemblies or wire harnesses?
A: Lead times for custom cable assemblies or wire harnesses can vary depending on the complexity of the design, the availability of materials and components, and the manufacturer’s production schedule. Generally, lead times can range from a few weeks to several months. Consult with your supplier or manufacturer to obtain a specific lead time for your project.
Conclusion
Cable assemblies and wire harnesses are essential components in various electrical systems, serving to transmit signals and power efficiently and reliably. While they share some similarities, there are distinct differences between the two in terms of construction, flexibility, complexity, and application. Understanding these differences is crucial for making the right choice when designing or manufacturing electrical systems.
By considering factors such as application requirements, environmental conditions, and system complexity, you can determine whether a cable assembly or wire harness is the best fit for your needs. Following best practices for design and manufacturing, and working with reliable suppliers and manufacturers, will help ensure the optimal performance and reliability of your cable assemblies or wire harnesses.
As technology continues to advance, the demand for high-quality, custom-designed cable assemblies and wire harnesses will only continue to grow. By staying informed about the latest developments and trends in this field, you can make informed decisions and stay ahead of the competition.
0 Comments