What are Castellated Pads?
Castellated pads, also known as castellated holes or castellations, are a type of surface mount technology (SMT) used in printed circuit board (PCB) design. These pads are essentially plated through-holes (PTHs) that are cut in half along the edge of the PCB, creating a series of semi-circular pads that resemble the battlements of a castle, hence the name “castellated.”
Castellated pads offer several advantages over traditional SMT pads:
- They allow for easy and secure connection between PCBs in a stack or between a module and a main board.
- They provide a larger surface area for soldering, resulting in a stronger mechanical and electrical connection.
- They enable better visual inspection of solder joints, making it easier to identify and correct any issues.
How are Castellated Pads Manufactured?
The process of creating castellated pads involves several steps:
- Designing the PCB layout with castellated pads along the desired edges.
- Drilling holes at the edge of the PCB where the castellated pads will be located.
- Plating the holes with copper to create a conductive surface.
- Cutting the PCB along the center of the holes, creating the semi-circular castellated pads.
This process can be performed using standard PCB manufacturing techniques, making it a cost-effective solution for many applications.
Applications of Castellated Pads
Castellated pads find use in a wide range of electronics applications, particularly in situations where a secure and reliable connection between PCBs or modules is required.
System-on-Module (SoM) and Computer-on-Module (CoM)
One of the most common applications of castellated pads is in System-on-Module (SoM) and Computer-on-Module (CoM) designs. These compact, self-contained modules integrate a complete computer system, including a processor, memory, and input/output interfaces, onto a single PCB.
Castellated pads along the edges of the module allow it to be easily soldered onto a carrier board, which provides additional functionality and connectivity. This modular approach offers several benefits:
- Simplified design and development, as the complex computing functions are contained within the module.
- Reduced time-to-market, as pre-designed modules can be quickly integrated into a final product.
- Increased flexibility, as different modules can be interchanged to meet specific requirements.
Some popular examples of SoM and CoM formats that utilize castellated pads include:
- Raspberry Pi Compute Module
- NVIDIA Jetson modules
- Arduino Industrial 101
- BeagleBone Black Wireless
Expansion Boards and Shields
Castellated pads are also commonly used in expansion boards and shields for development platforms like Arduino and Raspberry Pi. These boards can be stacked on top of the main board, providing additional features such as sensors, displays, or communication interfaces.
The castellated pads along the edges of the expansion board align with corresponding header pins on the main board, allowing for a secure and reliable connection. This stacking capability enables users to easily customize and extend the functionality of their development boards without the need for complex wiring or soldering.
High-Density Interconnects
In applications where a high density of interconnects is required between PCBs, castellated pads can provide a space-saving solution. By using castellated pads along the edges of the boards, designers can achieve a greater number of connections within a smaller footprint compared to traditional header pins or connectors.
This is particularly useful in compact electronic devices such as smartphones, wearables, and Internet of Things (IoT) sensors, where space is at a premium.
Designing with Castellated Pads
When designing a PCB with castellated pads, there are several factors to consider to ensure optimal performance and reliability.
Pad Dimensions
The size and spacing of castellated pads should be carefully chosen based on the requirements of the application. Some key dimensions to consider include:
- Pad diameter: The diameter of the plated through-hole that forms the castellated pad. A larger diameter provides a greater surface area for soldering but may reduce the number of pads that can fit along the edge of the PCB.
- Pad pitch: The distance between the centers of adjacent pads. A smaller pitch allows for more pads to be placed along the edge but may make soldering more challenging.
- Pad length: The length of the castellated pad, measured from the edge of the PCB to the inner edge of the pad. A longer pad provides more surface area for soldering but may reduce the mechanical strength of the PCB edge.
The table below shows some common dimensions for castellated pads:
Pad Diameter (mm) | Pad Pitch (mm) | Pad Length (mm) |
---|---|---|
0.5 | 1.0 | 0.75 |
0.8 | 1.27 | 1.0 |
1.0 | 1.5 | 1.25 |
1.2 | 2.0 | 1.5 |
Solder Mask and Paste
To ensure proper soldering of castellated pads, it is important to design the solder mask and paste layers correctly.
The solder mask should be opened around the castellated pads to expose the copper surface for soldering. The opening should be slightly larger than the pad diameter to allow for proper solder flow and to prevent solder bridging between adjacent pads.
The solder paste layer should be designed to deposit the appropriate amount of solder paste onto the castellated pads. The paste should be applied in a controlled manner to prevent excessive or insufficient solder volume, which can lead to poor solder joint quality.
Mechanical Considerations
Castellated pads can impact the mechanical strength and stability of a PCB, particularly along the edges where the pads are located. To mitigate these issues, designers should consider the following:
- Reinforce the PCB edges with additional material, such as a thicker copper or a stiffener, to prevent bending or cracking.
- Avoid placing castellated pads too close to the corners of the PCB, where stress concentrations can occur.
- Use a sufficient number of castellated pads to distribute the mechanical load evenly along the edge of the PCB.
By carefully considering these mechanical factors, designers can create PCBs with castellated pads that are both electrically and mechanically robust.
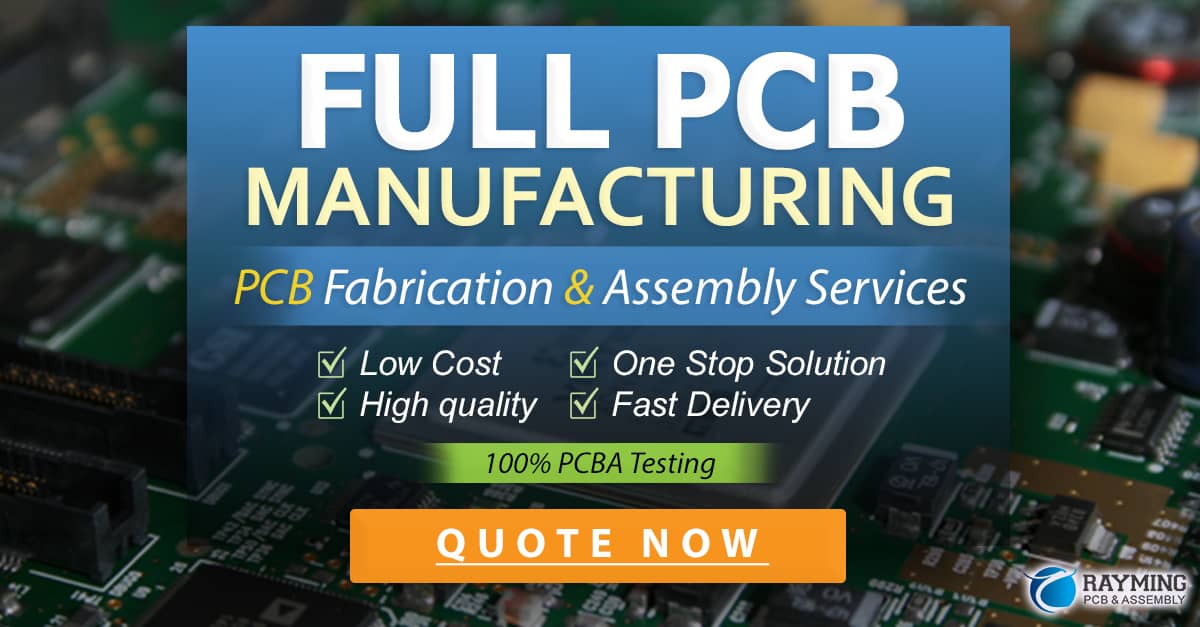
Frequently Asked Questions (FAQ)
1. Can castellated pads be used with through-hole components?
No, castellated pads are designed specifically for surface mount components and are not compatible with through-hole components. Through-hole components require full plated through-holes that extend through the entire thickness of the PCB.
2. Are castellated pads suitable for high-current applications?
Castellated pads can be used in high-current applications, but designers must ensure that the pads are sized appropriately to handle the required current. Larger pad diameters and longer pad lengths can help to increase the current-carrying capacity of the pads.
3. Can castellated pads be used on both sides of a PCB?
Yes, castellated pads can be placed on both sides of a PCB, allowing for even greater connectivity density. However, designers must ensure that the pads on opposite sides are properly aligned and that there is sufficient clearance between the pads and other components on the board.
4. How do castellated pads impact signal integrity?
Castellated pads can have an impact on signal integrity, particularly at high frequencies. The discontinuity created by the semi-circular pad can cause reflections and impedance mismatches, leading to signal degradation. To minimize these effects, designers should carefully choose the pad dimensions and spacing and use appropriate signal routing techniques, such as impedance matching and ground shielding.
5. Can castellated pads be repaired if damaged?
Castellated pads can be repaired if damaged, but the process can be challenging and time-consuming. If a castellated pad is damaged during assembly or handling, it may be possible to repair it using specialized soldering techniques, such as wire bonding or conductive epoxy. However, in some cases, the entire PCB may need to be replaced if the damage is severe or if multiple pads are affected.
Conclusion
Castellated pads offer a versatile and reliable solution for connecting PCBs and modules in a wide range of electronics applications. By providing a secure mechanical and electrical connection, castellated pads enable designers to create modular, expandable, and high-density systems that are both robust and flexible.
When designing with castellated pads, it is important to carefully consider factors such as pad dimensions, solder mask and paste, and mechanical reinforcement to ensure optimal performance and reliability. By following best practices and leveraging the advantages of castellated pads, designers can create innovative and efficient electronic products that meet the demands of today’s fast-paced and ever-evolving market.
0 Comments