Introduction to Rigid-flex PCBs
Rigid-Flex PCBs are a unique type of printed circuit board that combines the benefits of both rigid and flexible substrates. This innovative technology allows for the creation of highly compact, lightweight, and reliable electronic devices that can withstand harsh environments and repeated flexing. RAYPCB, a leading PCB manufacturer, offers comprehensive rigid-flex PCB services to meet the growing demands of various industries, including aerospace, medical, automotive, and consumer electronics.
What are Rigid-Flex PCBs?
Rigid-flex PCBs are a type of circuit board that consists of both rigid and flexible layers laminated together. The rigid layers provide structural support and house the majority of the components, while the flexible layers allow for bending and folding, enabling 3D packaging and improved connectivity between different sections of the device.
Benefits of Rigid-Flex PCBs
- Space Savings: Rigid-flex PCBs enable more compact packaging, reducing the overall size and weight of electronic devices.
- Enhanced Reliability: The elimination of connectors and wires between rigid sections improves signal integrity and reduces the risk of mechanical failures.
- Improved Flexibility: The flexible layers allow for bending and folding, enabling 3D packaging and greater design freedom.
- Cost Reduction: Rigid-flex PCBs can simplify assembly processes and reduce the number of components, leading to lower production costs.
RAYPCB’s Rigid-Flex PCB Manufacturing Capabilities
Materials and Layup Options
RAYPCB offers a wide range of materials and layup options to meet the specific requirements of different applications. Some of the commonly used materials include:
Material | Description | Applications |
---|---|---|
Polyimide (PI) | High temperature resistance, excellent mechanical properties | Aerospace, military, medical |
Polyester (PET) | Lower cost, good electrical properties | Consumer electronics, automotive |
Flexible Copper Clad Laminate (FCCL) | Copper foil bonded to a flexible dielectric material | High-density interconnects, wearables |
RAYPCB’s experienced engineers can assist in selecting the most suitable materials and layup configuration for your project, taking into account factors such as bend radius, flexing cycles, and environmental conditions.
Design and Simulation Services
To ensure the optimal performance and reliability of rigid-flex PCBs, RAYPCB offers comprehensive design and simulation services. Their team of skilled designers uses advanced software tools to create high-quality layouts, considering signal integrity, thermal management, and mechanical stress analysis. Some of the key design considerations include:
- Bend Radius: Ensuring that the minimum bend radius is maintained to prevent damage to the flexible layers.
- Coverlay Placement: Proper placement of coverlay to protect the flexible circuits and prevent delamination.
- Stiffener Design: Incorporating stiffeners to support the rigid sections and improve the overall mechanical stability.
RAYPCB also provides simulation services to validate the design before manufacturing, minimizing the risk of costly redesigns and ensuring a smooth transition to production.
Manufacturing Process
RAYPCB employs state-of-the-art manufacturing processes to produce high-quality rigid-flex PCBs. The typical manufacturing steps include:
- Material Preparation: Cutting and laminating the flexible and rigid substrates.
- Drilling and Plating: Creating via holes and plating them with copper to establish electrical connections between layers.
- Patterning: Applying and developing the photoresist, followed by etching to create the desired circuit patterns.
- Lamination: Bonding the flexible and rigid layers together using heat and pressure.
- Surface Finishing: Applying a protective surface finish, such as ENIG or HASL, to improve solderability and corrosion resistance.
- Cutting and Forming: Cutting the panel into individual boards and forming them into the desired shape.
Throughout the manufacturing process, RAYPCB implements strict quality control measures to ensure that the rigid-flex PCBs meet the highest standards of reliability and performance.
Applications of Rigid-Flex PCBs
Rigid-flex PCBs find applications in a wide range of industries, thanks to their unique combination of flexibility, reliability, and space-saving properties. Some of the key application areas include:
Aerospace and Defense
In the aerospace and defense sector, rigid-flex PCBs are used in avionics, satellite systems, and military equipment. Their ability to withstand harsh environments, vibrations, and extreme temperatures makes them ideal for these demanding applications. Examples include:
- Missile guidance systems
- Cockpit displays and control panels
- Radar and communication equipment
Medical Devices
Rigid-flex PCBs are increasingly used in medical devices, where miniaturization, reliability, and biocompatibility are crucial. Some common applications include:
- Implantable devices, such as pacemakers and neurostimulators
- Wearable monitoring devices, such as ECG patches and glucose sensors
- Surgical instruments and endoscopes
Automotive Electronics
The automotive industry relies on rigid-flex PCBs for various electronic systems, as they offer improved reliability and space savings compared to traditional Wire Harnesses. Applications include:
- Engine control units (ECUs)
- Infotainment systems
- Advanced driver assistance systems (ADAS)
Consumer Electronics
Rigid-flex PCBs are widely used in consumer electronics, where compact packaging and high-density interconnects are essential. Examples include:
- Smartphones and tablets
- Wearable devices, such as smartwatches and fitness trackers
- Virtual reality and augmented reality headsets
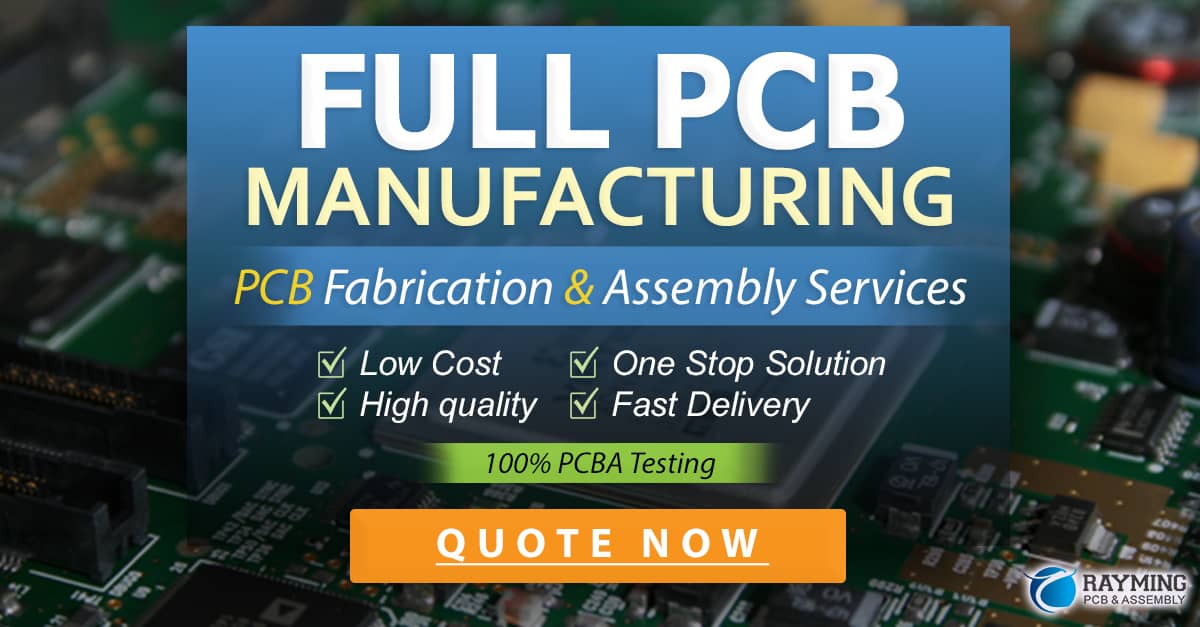
RAYPCB’s Value-Added Services
In addition to their core rigid-flex PCB manufacturing capabilities, RAYPCB offers a range of value-added services to support customers throughout the product development lifecycle.
Prototyping and Low-Volume Production
RAYPCB provides rapid prototyping services to help customers validate their designs and bring products to market faster. Their quick-turn prototyping capabilities include:
- 24-hour and 48-hour rush services
- Flexible minimum order quantities (MOQs)
- Dedicated support from experienced engineers
For low-volume production runs, RAYPCB offers competitive pricing and lead times, making them an ideal partner for startups and small businesses.
Assembly and Box Build Services
To streamline the production process and reduce time-to-market, RAYPCB provides turnkey assembly and box build services. Their state-of-the-art facilities are equipped with advanced surface mount technology (SMT) lines and automated optical inspection (AOI) systems, ensuring high-quality and efficient assembly. Services include:
- Component sourcing and procurement
- SMT and through-hole assembly
- Functional testing and burn-in
- Final packaging and shipping
By leveraging RAYPCB’s assembly and box build services, customers can benefit from a single-source solution that reduces costs, minimizes supply chain risks, and improves overall product quality.
Engineering Support and Consulting
RAYPCB’s team of experienced engineers provides comprehensive support and consulting services to help customers optimize their rigid-flex PCB designs. They can assist with:
- Material selection and stackup design
- Signal integrity analysis and simulation
- Thermal management and mechanical stress analysis
- Design for manufacturing (DFM) and design for assembly (DFA) recommendations
By collaborating closely with customers, RAYPCB’s engineers can identify potential issues early in the design phase, reducing the risk of costly redesigns and ensuring a smooth transition to manufacturing.
Frequently Asked Questions (FAQ)
-
What is the minimum bend radius for rigid-flex PCBs?
The minimum bend radius depends on the thickness and material of the flexible layers. As a general rule, the minimum bend radius should be at least 6 times the thickness of the flexible layer to prevent damage and ensure long-term reliability. -
Can rigid-flex PCBs be used in high-temperature environments?
Yes, rigid-flex PCBs can be designed to withstand high temperatures by selecting appropriate materials, such as polyimide (PI), which has a high glass transition temperature (Tg) and excellent thermal stability. -
How do I choose the right material for my rigid-flex PCB?
The choice of material depends on several factors, including the application requirements, operating environment, and budget. RAYPCB’s engineers can help you select the most suitable material based on your specific needs, considering factors such as flexibility, temperature resistance, and electrical properties. -
What are the advantages of using rigid-flex PCBs over traditional wire harnesses?
Rigid-flex PCBs offer several advantages over traditional wire harnesses, including improved reliability, reduced weight and space, and simplified assembly processes. They also provide better signal integrity and eliminate the need for connectors, which are common points of failure in wire harnesses. -
How long does it take to manufacture rigid-flex PCBs?
The lead time for rigid-flex PCBs depends on the complexity of the design, the materials used, and the order quantity. RAYPCB offers standard lead times of 2-3 weeks for most rigid-flex PCB orders, with expedited options available for urgent projects.
Conclusion
Rigid-flex PCBs are a cutting-edge technology that enables the creation of highly compact, reliable, and flexible electronic devices. With their unique combination of rigid and flexible layers, rigid-flex PCBs offer numerous benefits, including space savings, improved signal integrity, and greater design freedom. RAYPCB, as a leading PCB manufacturer, provides comprehensive rigid-flex PCB services, from design and simulation to manufacturing and assembly, helping customers bring their innovative products to market faster and more efficiently. By partnering with RAYPCB, companies across various industries can leverage the power of rigid-flex PCBs to create the next generation of electronic devices that are smaller, smarter, and more reliable than ever before.
0 Comments