What Are the Main Steps in PCB Fabrication?
The PCB fabrication process can be broken down into several key steps:
- Design: Creating the circuit schematic and board layout using EDA (electronic design automation) software
- Printing: Printing the circuit pattern onto the copper laminated board
- Etching: Chemically removing unwanted copper to leave behind the desired circuit
- Drilling: Drilling holes for through-hole components and vias
- Plating: Plating and coating the board to prevent oxidation and improve solderability
- Silkscreen: Applying a silkscreen legend to label components, test points, etc.
- Cutting: Cutting the board out into its final shape
- Testing: Testing for proper functioning and identifying defective boards
Each step must be carried out with precision in a controlled environment to produce reliable, high-quality PCBs suitable for the end application.
What Materials Are PCBs Made From?
The based material of a PCB is a thin board made of insulating layers typically consisting of a substrate material laminated with a thin layer of copper foil that forms the conductive circuit pattern. Common substrate materials used include:
Substrate Material | Composition | Typical Applications |
---|---|---|
FR-4 | Fiberglass reinforced epoxy laminate | Most common for general purpose PCBs |
CEM-1 | Composites of cotton paper and epoxy | Low-end consumer electronics |
Polyimide | High-temperature polymer film | Flexible, high-reliability circuits |
PTFE | Polytetrafluoroethylene (Teflon) | High-frequency RF circuits |
Aluminum | Metal-core with thin dielectric layer | High power LED lighting |
The choice of substrate depends on the electrical, mechanical, and environmental requirements of the application. FR-4 fiberglass is the most commonly used due to its durability, affordability, good dielectric properties, and temperature resistance.
What Types of PCBs Are There?
PCBs can be categorized in various ways based on their construction:
- Single-sided: Conductive copper traces on one side of the substrate only
- Double-sided: Conductive traces on both sides of the substrate
- Multi-layer: Three or more conductive copper layers laminated with insulating material in between
They can also be categorized by the type of components they are designed for:
- Through-hole: Uses leaded components that are inserted into drilled holes
- Surface-mount (SMT): Uses leadless components that are soldered directly to pads on the surface of the board
- Mixed: Uses both through-hole and surface-mount components
Additionally, PCBs may be rigid, flexible, or a hybrid combination (rigid-flex) depending on the substrate material used. The vast majority are rigid, but flexible circuits are becoming more common.
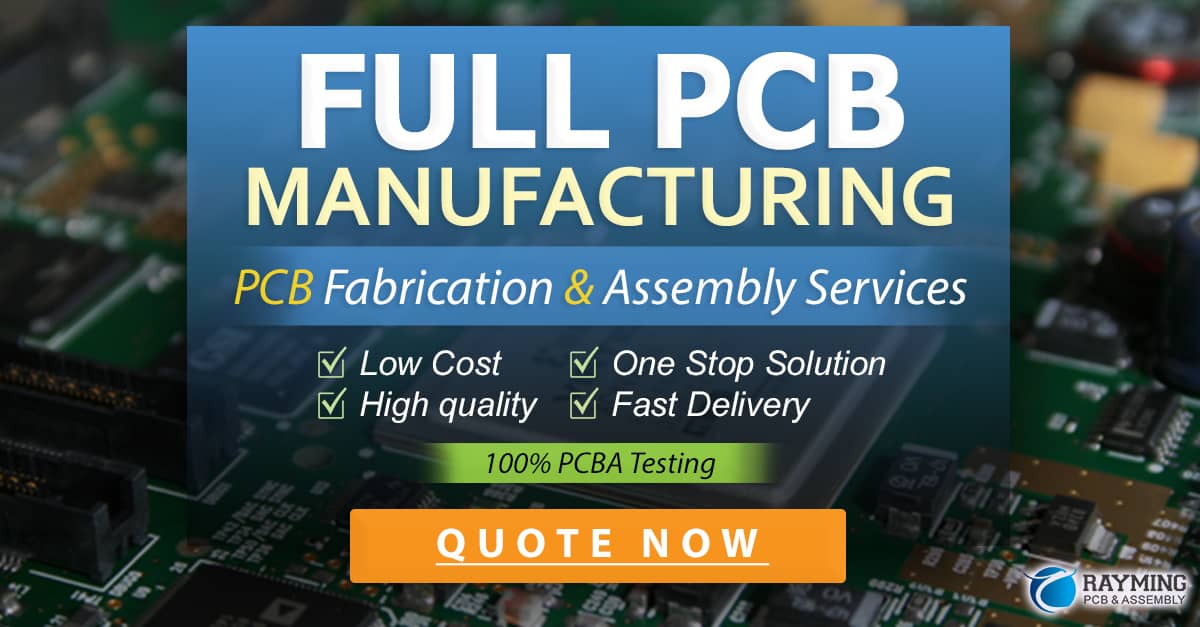
What is Gerber Data and Why Is It Important?
Gerber data is the universal file format used to describe the printed circuit board images for manufacturing. It is a 2D vector image format that describes each layer of the PCB – copper layers, solder mask, legend, drill data, etc.
Example Gerber file extensions and their meanings:
Extension | Layer |
---|---|
.GTO | Top Silkscreen Overlay |
.GTP | Top Paste Mask |
.GTS | Top Solder Mask |
.GTL | Top Copper Layer |
… | |
.GBL | Bottom Copper Layer |
.GBS | Bottom Solder Mask |
.GBP | Bottom Paste Mask |
.GBO | Bottom Silkscreen Overlay |
Proper Gerber files are critical because they tell the PCB manufacturer exactly what to build. They should be carefully checked for errors before being sent for fabrication. Any mistakes in the Gerber data will result in wrongly manufactured boards.
How Are PCBs Actually Manufactured?
The actual manufacturing process for a typical rigid FR-4 PCB goes through the following simplified steps:
- Pre-treat the copper clad laminate to remove oxides and debris
- Print the circuit pattern onto the board using a photoresist
- Expose the photoresist to UV light to harden the resist that remains on the copper
- Chemically etch away the unwanted copper that is not protected by hardened photoresist
- Strip off the hardened photoresist
- Drill holes for vias and through-hole component leads
- Plate copper onto hole barrels to provide electrical connection between layers
- Apply and cure soldermask to cover bare copper
- Apply silkscreen legend using ink or epoxy
- Perform final surface finish (e.g. HASL, ENIG, OSP)
- Route or V-score the board out to final dimensions
- Test the finished boards electrically and visually
- Package the good boards for shipment
Many of these steps may be performed in a different order or repeated multiple times depending on the number of layers and specific design requirements.
What Surface Finishes Are Available for PCBs?
The final step that a bare PCB goes through before shipment is the application of a surface finish to the exposed copper. This is necessary to prevent oxidation and provide a solderable surface when components are attached. The most common surface finishes for PCBs include:
Finish | Composition | Pros | Cons |
---|---|---|---|
HASL | Hot air solder leveling (tin-lead) | Inexpensive, easy to solder | Not always flat, contains lead |
ENIG | Electroless nickel immersion gold | Flat, gold is easy to solder | More expensive |
OSP | Organic solderability preservative | Cheapest finish | Shorter shelf life before oxidation |
Immersion Silver | Thin silver plating | Inexpensive, good solderability | Can tarnish over time |
Immersion Tin | Thin tin plating | Good flatness, lead-free | Prone to tin whiskers |
The choice of finish depends on the soldering process to be used, flatness requirements, cost constraints, lead-free requirements, and expected product lifespan. HASL remains one of the most popular finishes due to low cost, but lead-free HASL and ENIG are becoming more common.
FAQ on PCB Fabrication
What is the typical turnaround time for PCB fabrication?
Turnaround times vary by manufacturer, complexity and quantity of the boards, but typically range from 1-2 days for quick-turn prototypes to 2-3 weeks for larger orders. Expedited production is usually available for an added cost.
What are the most common reasons for PCBs to fail?
Some of the top causes of PCB failure include:
- Poor design: Errors or oversights in the circuit design
- Manufacturing defects: Shorts, opens, inaccurate drilling/routing, contamination
- Component failure: Defective, overstressed, or improperly installed parts
- Environmental damage: Corrosion, overheating, physical damage
- User abuse: Improper use, electrostatic discharge, power surges
Following good DFM (design for manufacturing) practices, using reputable manufacturers, and properly protecting the finished product can help minimize PCB failures.
What are controlled impedance PCBs?
Controlled impedance PCBs are boards that are manufactured to tight tolerances in order to control the impedance of the traces for high-speed signals. This is important to maintain signal integrity and prevent unwanted reflections. Impedance is determined by the width and copper thickness of the trace and the dielectric constant of the substrate.
What is the difference between V-scoring and routing?
Both V-scoring and routing are methods of cutting the finished board out of the panel. V-scoring uses a V-shaped blade to cut part way through the board, allowing it to be easily snapped out. Routing uses a spinning router bit to cut all the way through. V-scoring is faster and less expensive but leaves a slight notch, while routing provides a smooth, flush edge.
How small of features can be fabricated on a PCB?
The minimum feature sizes that can be fabricated depend on the capabilities of the specific manufacturer and the tolerances of the design. In general, most PCB shops can fabricate traces and spaces down to 0.006″ (6 mil) or smaller. High-end shops may be able to do 0.003″ (3 mil). Smaller mechanical drills down to 0.004″ (4 mil) are also possible. The tradeoff is that smaller features are more expensive. It’s best to use the largest feature sizes allowable for your design.
We’ve covered a lot of ground on the topic of PCB fabrication, from the basics of how they’re made to the key considerations and tradeoffs a designer needs to keep in mind. While PCB manufacturing is a complex, multi-step process, having a good working knowledge of it is invaluable for producing reliable, cost-effective electronics. As PCB technologies continue to evolve, designers who understand the fundamentals are well-positioned to take advantage of them in new and innovative applications.
0 Comments