Introduction to Programmable Power Supplies
A programmable power supply (PSU) is a versatile tool that allows users to precisely control and adjust the voltage and current output. Unlike traditional fixed-output power supplies, Programmable PSUs offer the flexibility to set and change the output parameters according to the requirements of the connected device or circuit. This makes them essential for various applications, including Electronics Testing, research and development, and industrial automation.
Key Features of Programmable Power Supplies
- Adjustable voltage and current output
- High accuracy and stability
- Remote control and monitoring capabilities
- Overvoltage and overcurrent protection
- Multiple output channels (in some models)
Understanding the Basic Components of a Programmable PSU
To design a programmable power supply schematic circuit, it is essential to understand the basic components and their functions. The following table lists the main components and their roles in a programmable PSU:
Component | Function |
---|---|
Transformer | Steps down the AC input voltage to a lower level suitable for the PSU |
Rectifier | Converts the stepped-down AC voltage to DC Voltage |
Filter Capacitors | Smooths the rectified DC voltage, reducing ripple and noise |
Voltage Regulator | Maintains a constant output voltage despite variations in input voltage or load |
Current Limiter | Protects the PSU and connected devices from excessive current draw |
Microcontroller | Controls and monitors the output voltage and current based on user settings |
User Interface | Allows users to input desired voltage and current values and display output status |
Transformer
The transformer is the first stage in a programmable PSU schematic circuit. Its primary function is to step down the high-voltage AC input (e.g., 120V or 240V) to a lower level suitable for the power supply. The transformer also provides electrical isolation between the input and output, ensuring safety and preventing ground loops.
When selecting a transformer for a programmable PSU, consider the following factors:
- Input voltage range
- Output voltage and current ratings
- Efficiency and regulation
- Size and weight
Rectifier
The rectifier converts the stepped-down AC voltage from the transformer into DC voltage. In most programmable PSU designs, a full-wave bridge rectifier is used due to its efficiency and simplicity. The bridge rectifier consists of four diodes arranged in a bridge configuration, allowing both the positive and negative half-cycles of the AC input to be converted to DC.
Filter Capacitors
After rectification, the DC voltage still contains significant ripple and noise. Filter capacitors are used to smooth the rectified DC voltage, reducing the ripple to an acceptable level. The choice of filter capacitors depends on the desired output voltage and current, as well as the acceptable ripple level.
Factors to consider when selecting filter capacitors:
- Capacitance value
- Voltage rating
- Equivalent series resistance (ESR)
- Ripple current rating
Voltage Regulator
The voltage regulator is responsible for maintaining a constant output voltage despite variations in the input voltage or load. In programmable PSUs, adjustable voltage regulators are used to allow users to set the desired output voltage. The most common types of adjustable voltage regulators are linear regulators and switching regulators.
Linear regulators, such as the LM317, offer simplicity and low noise but are less efficient and generate more heat. Switching regulators, like the Buck Converter, provide higher efficiency and can handle higher power levels but are more complex and may introduce higher noise levels.
Current Limiter
The current limiter protects the PSU and connected devices from excessive current draw. It monitors the output current and limits it to a safe level if the load demands more current than the PSU can safely provide. Current limiting can be implemented using various methods, such as:
- Series resistors
- Current-sensing resistors and transistors
- Dedicated current-limit ICs
Microcontroller
In a programmable PSU, a microcontroller is used to control and monitor the output voltage and current based on user settings. The microcontroller communicates with the user interface, reads the desired voltage and current values, and adjusts the voltage regulator and current limiter accordingly. It also monitors the output parameters and displays them on the user interface.
When selecting a microcontroller for a programmable PSU, consider the following factors:
- Number of input/output pins
- Analog-to-digital converter (ADC) resolution
- Communication interfaces (e.g., UART, I2C, SPI)
- Processing speed and memory
User Interface
The user interface allows users to input the desired voltage and current values and displays the output status. It typically consists of a display (e.g., LCD, OLED) and input devices (e.g., buttons, rotary encoders, touchscreens). The user interface communicates with the microcontroller, sending user settings and receiving output data for display.
When designing the user interface for a programmable PSU, consider the following factors:
- Ease of use and readability
- Input method (buttons, encoders, touchscreen)
- Display type and resolution
- Menu structure and navigation
Designing the Programmable PSU Schematic Circuit
Now that we have covered the basic components of a programmable PSU, let’s dive into the process of designing the schematic circuit.
Step 1: Determine the Input and Output Specifications
Before starting the design, determine the input and output specifications of the programmable PSU. This includes:
- Input voltage range (e.g., 120V or 240V AC)
- Output voltage range (e.g., 0-30V DC)
- Output current range (e.g., 0-5A)
- Output power (e.g., 150W)
Step 2: Select the Transformer
Based on the input voltage range and output power requirements, select an appropriate transformer. Ensure that the transformer’s secondary voltage is higher than the desired maximum output voltage to account for the voltage drops across the rectifier, filter, and regulator.
Step 3: Design the Rectifier and Filter Stage
Choose a suitable rectifier configuration (e.g., full-wave bridge rectifier) and select the diodes based on their forward voltage drop and current rating. Calculate the required filter capacitance based on the desired output voltage, current, and ripple level.
Step 4: Select the Voltage Regulator
Choose an adjustable voltage regulator that meets the output voltage and current requirements. Consider the regulator’s efficiency, Heat Dissipation, and noise performance. Design the necessary feedback and control circuits to adjust the output voltage based on user settings.
Step 5: Implement the Current Limiter
Select a current limiting method (e.g., series resistor, current-sensing resistor and transistor) and design the circuit to limit the output current to a safe level. Ensure that the current limiter can handle the maximum output current and dissipate the necessary power.
Step 6: Select the Microcontroller and Design the Control Circuit
Choose a microcontroller that meets the input/output, processing, and communication requirements of the programmable PSU. Design the necessary circuits to interface the microcontroller with the voltage regulator, current limiter, and user interface. Develop the firmware to control and monitor the output parameters based on user settings.
Step 7: Design the User Interface
Select the display and input devices for the user interface and design the necessary circuits to interface them with the microcontroller. Develop the menu structure and navigation logic for the user interface, ensuring ease of use and readability.
Step 8: Assemble and Test the Programmable PSU
Assemble the programmable PSU schematic circuit on a breadboard or PCB, following best practices for component placement and signal routing. Test the PSU thoroughly, verifying the output voltage and current accuracy, stability, and protection features. Fine-tune the circuit and firmware as necessary to achieve the desired performance.
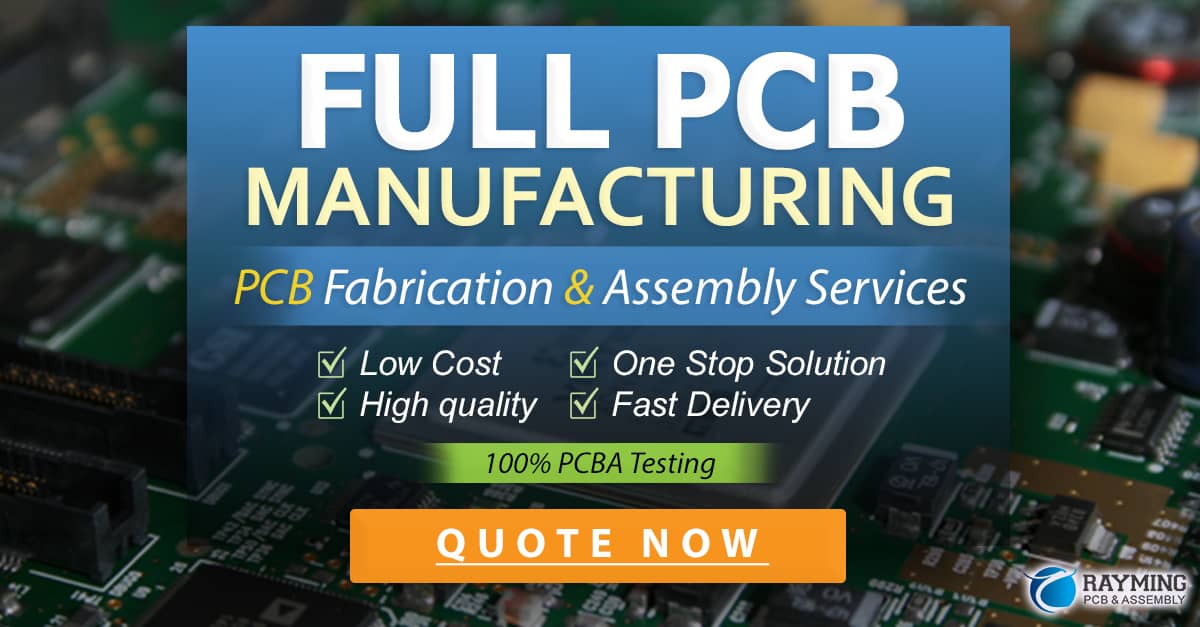
Frequently Asked Questions (FAQ)
-
Q: What is the difference between a linear and switching voltage regulator in a programmable PSU?
A: Linear regulators are simpler and offer lower noise but are less efficient and generate more heat. Switching regulators provide higher efficiency and can handle higher power levels but are more complex and may introduce higher noise levels. -
Q: How do I determine the required filter capacitance for the rectifier stage?
A: The required filter capacitance depends on the desired output voltage, current, and ripple level. You can use the following formula as a starting point:
C = (I_load × t) / (V_ripple)
where C is the capacitance, I_load is the maximum load current, t is the time between charging cycles (1/2f for full-wave rectification, where f is the input frequency), and V_ripple is the maximum allowable ripple voltage. -
Q: What factors should I consider when selecting a microcontroller for a programmable PSU?
A: When selecting a microcontroller, consider the number of input/output pins required, the resolution of the analog-to-digital converter (ADC), the necessary communication interfaces (e.g., UART, I2C, SPI), and the processing speed and memory requirements for your specific application. -
Q: How can I ensure the safety of the programmable PSU and connected devices?
A: To ensure safety, incorporate protection features such as overvoltage and overcurrent protection, short-circuit protection, and thermal shutdown. Use appropriate fuses and circuit breakers, and ensure proper grounding and isolation between the input and output. Follow best practices for PCB design and component selection, and test the PSU thoroughly under various conditions. -
Q: Can I add multiple output channels to a programmable PSU?
A: Yes, you can design a programmable PSU with multiple output channels. To do this, replicate the voltage regulator, current limiter, and control circuits for each channel, and modify the microcontroller firmware and user interface to support multiple outputs. Ensure that the transformer and rectifier stage can handle the total power requirements of all channels.
Conclusion
Designing a programmable power supply schematic circuit requires a thorough understanding of the basic components and their functions. By following the step-by-step process outlined in this article, you can create a reliable and efficient programmable PSU that meets your specific requirements.
Remember to consider factors such as input and output specifications, component selection, protection features, and user interface design when developing your programmable PSU. Always follow best practices for circuit design, PCB layout, and testing to ensure the safety and performance of your power supply.
With a well-designed programmable PSU, you can power and test a wide range of electronic devices and circuits, making it an essential tool for any electronics engineer or hobbyist.
0 Comments