Introduction to PCB Assembly
Printed Circuit Board (PCB) assembly is a crucial process in the manufacturing of electronic devices. It involves the placement and soldering of various components onto a PCB to create a functional circuit. In this comprehensive guide, we will delve into the intricacies of the PCB assembly process, covering everything from the basics to advanced techniques.
What is a Printed Circuit Board?
A Printed Circuit Board, or PCB, is a flat board made of insulating material, such as fiberglass or plastic, with conductive tracks etched onto its surface. These tracks, also known as traces, connect the various components of an electronic circuit, allowing electrical signals to flow between them. PCBs are used in a wide range of electronic devices, from smartphones and computers to medical equipment and industrial machinery.
Importance of PCB Assembly
PCB assembly is a critical step in the production of electronic devices. The quality and reliability of the assembled PCB directly impact the performance and longevity of the final product. A well-assembled PCB ensures proper functionality, minimizes the risk of failures, and enhances the overall user experience.
PCB Assembly Process Overview
The PCB assembly process can be broadly divided into three main stages: pre-assembly, assembly, and post-assembly. Each stage involves several steps that must be carried out with precision and care to ensure a high-quality end product.
Pre-Assembly Stage
-
PCB Design and Fabrication: The PCB assembly process begins with the design and fabrication of the PCB itself. This involves creating a schematic diagram of the circuit, designing the PCB layout, and fabricating the board using various methods such as etching, drilling, and plating.
-
Component Selection and Procurement: Once the PCB design is finalized, the next step is to select and procure the necessary components. This includes resistors, capacitors, integrated circuits (ICs), and other electronic components required for the circuit.
-
Solder Paste Stenciling: Before the components are placed on the PCB, a thin layer of solder paste is applied to the pads using a stencil. The stencil ensures that the solder paste is deposited accurately and consistently on the pads.
Assembly Stage
-
Component Placement: The components are then placed onto the PCB using either manual or automated methods. Surface Mount Technology (SMT) is the most common method used for component placement, where the components are placed directly onto the surface of the PCB.
-
Reflow Soldering: After the components are placed, the PCB undergoes reflow soldering. In this process, the PCB is heated in a reflow oven, causing the solder paste to melt and form a permanent bond between the components and the PCB pads.
-
Through-Hole Component Insertion: If the PCB design includes through-hole components, they are inserted into the corresponding holes on the board and soldered in place using a wave soldering machine or manual soldering techniques.
Post-Assembly Stage
-
Inspection and Quality Control: Once the assembly is complete, the PCB undergoes thorough inspection and quality control checks. This includes visual inspection, automated optical inspection (AOI), and electrical testing to ensure that the PCB functions as intended and meets the required specifications.
-
Cleaning and Coating: After inspection, the PCB is cleaned to remove any residual flux or contaminants. If required, a protective coating, such as conformal coating, may be applied to the PCB to protect it from environmental factors like moisture, dust, and corrosion.
-
Packaging and Shipping: Finally, the assembled PCBs are packaged and shipped to the customer or integrated into the final product.
Surface Mount Technology (SMT) Assembly
Surface Mount Technology (SMT) is the most widely used method for PCB assembly. In SMT assembly, the components are placed directly onto the surface of the PCB, as opposed to through-hole assembly, where the component leads are inserted into holes drilled in the board.
Advantages of SMT Assembly
-
Miniaturization: SMT components are smaller than through-hole components, allowing for more compact PCB designs and higher component density.
-
Faster Assembly: SMT assembly is highly automated, enabling faster placement of components and shorter production times compared to through-hole assembly.
-
Cost-Effective: The use of SMT components and automated assembly processes reduces the overall manufacturing costs, making it an economical choice for high-volume production.
SMT Assembly Process
-
Solder Paste Application: A thin layer of solder paste is applied to the PCB pads using a stencil. The stencil ensures precise and consistent application of the solder paste.
-
Component Placement: SMT components are placed onto the PCB using automated pick-and-place machines. These machines use vacuum nozzles to pick up the components from feeders and place them accurately on the solder paste-coated pads.
-
Reflow Soldering: The PCB with the placed components is then passed through a reflow oven. The oven heats the board to a specific temperature profile, melting the solder paste and forming a permanent bond between the components and the PCB pads.
-
Inspection and Testing: After the reflow soldering process, the PCB undergoes visual inspection and automated optical inspection (AOI) to detect any placement errors, solder bridges, or other defects. Electrical testing is also performed to ensure proper functionality.
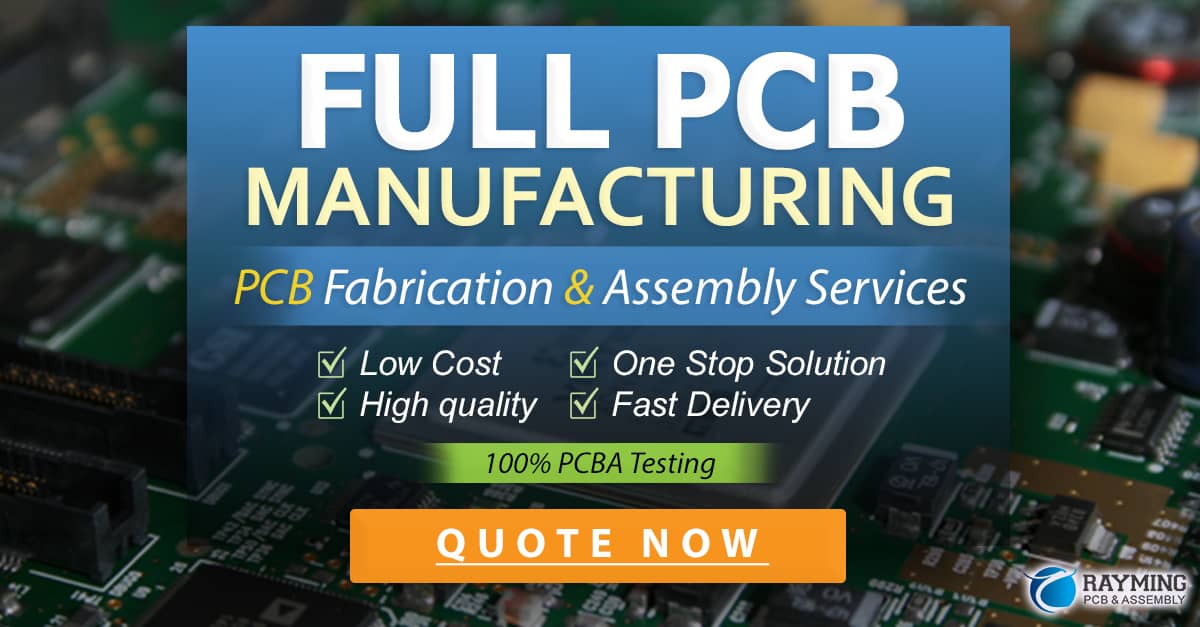
Through-Hole Assembly
Through-hole assembly is a traditional PCB assembly method where the component leads are inserted into holes drilled in the PCB and soldered in place. Although SMT has largely replaced through-hole assembly, it is still used for certain components that are not suitable for SMT, such as large connectors, transformers, and high-power components.
Through-Hole Assembly Process
-
Component Insertion: The leads of the through-hole components are inserted into the corresponding holes on the PCB. This process can be done manually or using automated insertion machines.
-
Wave Soldering: The PCB is then passed over a wave soldering machine, which consists of a molten solder bath. As the PCB moves over the solder wave, the molten solder flows into the holes and around the component leads, creating a strong mechanical and electrical connection.
-
Inspection and Cleaning: After wave soldering, the PCB is inspected for any solder bridges, cold solder joints, or other defects. The board is then cleaned to remove any residual flux or contaminants.
Mixed Technology Assembly
In some cases, a PCB may require both SMT and through-hole components. This is known as mixed technology assembly or hybrid assembly. In mixed technology assembly, the SMT components are typically placed and soldered first, followed by the insertion and soldering of the through-hole components.
Challenges in Mixed Technology Assembly
-
Process Compatibility: Ensuring compatibility between the SMT and through-hole assembly processes can be challenging. The reflow soldering temperature profile must be carefully controlled to prevent damage to the through-hole components.
-
Component Placement Sequence: The placement sequence of SMT and through-hole components must be carefully planned to avoid interference and ensure proper soldering.
-
Inspection and Testing: Mixed technology assemblies require thorough inspection and testing to ensure the proper functioning of both SMT and through-hole components.
Quality Control in PCB Assembly
Quality control is a critical aspect of the PCB assembly process. It ensures that the assembled PCBs meet the required specifications, function as intended, and are free from defects.
Inspection Methods
-
Visual Inspection: Visual inspection is the most basic form of quality control in PCB assembly. Trained operators visually examine the assembled PCBs for any visible defects, such as component misalignment, solder bridges, or damaged components.
-
Automated Optical Inspection (AOI): AOI uses high-resolution cameras and image processing software to automatically detect assembly defects. AOI systems can quickly identify issues such as missing components, incorrect component placement, and solder defects.
-
X-Ray Inspection: X-ray inspection is used to detect defects that are not visible on the surface, such as voids in solder joints, component shorts, and ball grid array (BGA) solder joint defects.
Electrical Testing
-
In-Circuit Testing (ICT): ICT is a type of electrical testing that verifies the proper connectivity and functionality of individual components on the PCB. ICT systems use a bed-of-nails fixture to make contact with the PCB and perform various electrical measurements.
-
Functional Testing: Functional testing involves testing the assembled PCB as a complete system to ensure that it performs as intended. This may include power-on testing, boundary scan testing, and application-specific testing.
Rework and Repair
If defects are found during the inspection and testing processes, the PCBs may require rework or repair. Rework involves the removal and replacement of defective components or the correction of soldering issues. Skilled technicians perform rework using specialized tools and techniques to ensure the integrity of the PCB.
PCB Assembly Challenges and Solutions
PCB assembly can present various challenges that must be addressed to ensure a successful outcome. Some common challenges and their solutions include:
Component Miniaturization
-
Challenge: As electronic devices become smaller and more complex, the components used in PCB assembly are also shrinking in size. This makes handling and placing these components more difficult.
-
Solution: Invest in advanced pick-and-place machines with high precision and the ability to handle small components. Provide training to operators to ensure proper handling and placement techniques.
Thermal Management
-
Challenge: High-power components and dense PCB layouts can generate significant heat, which can affect the performance and reliability of the assembly.
-
Solution: Incorporate thermal management techniques into the PCB design, such as the use of heat sinks, thermal vias, and proper component placement. Use thermally conductive materials and ensure adequate airflow for cooling.
Electrostatic Discharge (ESD) Protection
-
Challenge: Electronic components are sensitive to electrostatic discharge, which can cause damage and lead to device failure.
-
Solution: Implement ESD protection measures throughout the PCB assembly process, including the use of ESD-safe workstations, grounding straps, and static-dissipative materials. Train personnel in ESD prevention and handling procedures.
Moisture Sensitivity
-
Challenge: Some components, particularly those with plastic packages, are sensitive to moisture absorption. Exposure to moisture can cause cracking or delamination during the reflow soldering process.
-
Solution: Follow proper moisture-sensitive device (MSD) handling procedures, including dry storage, moisture barrier bags, and baking prior to assembly. Ensure that the reflow soldering profile is optimized for the specific components and their moisture sensitivity levels.
Future Trends in PCB Assembly
As technology continues to advance, the PCB assembly industry must adapt to new trends and requirements. Some of the future trends in PCB assembly include:
Increased Automation
The use of automated systems, such as advanced pick-and-place machines, robotic soldering, and automated inspection, will continue to grow in PCB assembly. Automation improves efficiency, accuracy, and repeatability while reducing human error and labor costs.
Adoption of Industry 4.0
Industry 4.0, or the fourth industrial revolution, involves the integration of smart technologies, such as the Internet of Things (IoT), artificial intelligence (AI), and machine learning, into manufacturing processes. In PCB assembly, this may include the use of connected machines, real-time data analysis, and predictive maintenance to optimize production and quality control.
Sustainable Manufacturing Practices
As environmental concerns continue to grow, the PCB assembly industry will need to adopt more sustainable manufacturing practices. This may include the use of lead-free solders, recyclable materials, and energy-efficient equipment. Manufacturers will also need to ensure compliance with evolving environmental regulations and standards.
Advanced Materials and Components
The development of new materials and components, such as flexible and stretchable PCBs, embedded components, and advanced packaging techniques, will drive innovation in PCB assembly. Manufacturers will need to stay updated on these advancements and adapt their processes accordingly.
Frequently Asked Questions (FAQ)
-
What is the difference between SMT and through-hole assembly?
SMT (Surface Mount Technology) assembly involves placing components directly onto the surface of the PCB, while through-hole assembly requires inserting component leads into holes drilled in the board and soldering them in place. SMT is more common in modern PCB assembly due to its advantages in miniaturization, faster assembly, and cost-effectiveness. -
What is the purpose of solder paste in PCB assembly?
Solder paste is a mixture of tiny solder particles suspended in a flux medium. It is applied to the PCB pads prior to component placement. The solder paste serves two main purposes: it holds the components in place during the reflow soldering process and forms a permanent electrical and mechanical bond between the components and the PCB pads when heated. -
What is the role of inspection in PCB assembly?
Inspection plays a crucial role in ensuring the quality and reliability of assembled PCBs. Various inspection methods, such as visual inspection, automated optical inspection (AOI), and X-ray inspection, are used to detect defects, component placement errors, and soldering issues. Inspection helps identify and correct problems early in the assembly process, reducing the risk of device failure and improving overall product quality. -
How can thermal management issues be addressed in PCB assembly?
Thermal management issues can be addressed through a combination of PCB design and assembly techniques. This includes the use of heat sinks, thermal vias, and proper component placement to dissipate heat effectively. The selection of thermally conductive materials, such as metal-core PCBs or thermal interface materials, can also help manage heat. Ensuring adequate airflow and using conformal coatings can further enhance the thermal performance of the assembled PCB. -
What are the benefits of automated PCB assembly?
Automated PCB assembly offers several benefits over manual assembly methods. It improves efficiency and throughput by enabling faster placement of components and shorter production times. Automation also enhances accuracy and consistency, reducing the risk of human error and ensuring repeatable results. Additionally, automated systems can handle smaller components and higher component densities, facilitating the production of more complex and miniaturized PCBs.
Conclusion
PCB assembly is a complex and critical process in the manufacturing of electronic devices. By understanding the various stages, techniques, and challenges involved in PCB assembly, manufacturers can optimize their processes to produce high-quality, reliable, and cost-effective products.
From the pre-assembly stage of PCB design and component selection to the assembly processes of SMT and through-hole technology, each step requires precision and attention to detail. Effective quality control measures, including inspection and testing, ensure that assembled PCBs meet the required specifications and perform as intended.
As the electronics industry continues to evolve, PCB assembly must adapt to new trends and technologies. Increased automation, the adoption of Industry 4.0 practices, sustainable manufacturing, and the incorporation of advanced materials and components will shape the future of PCB assembly.
By staying informed about the latest developments and best practices in PCB assembly, manufacturers can remain competitive and deliver innovative, high-quality electronic products to meet the ever-growing demands of the market.
0 Comments