Understanding the Basics of Power PCB Design
Before diving into the specifics, it’s important to grasp the fundamental concepts of power PCB design. A power PCB is a printed circuit board that is specifically designed to handle high currents and voltages, making it an integral component in power electronics systems.
Key Characteristics of Power PCBs
Characteristic | Description |
---|---|
High Current Handling | Power PCBs are designed to handle high currents, typically in the range of several amperes to hundreds of amperes. |
High Voltage Tolerance | These PCBs must withstand high voltages, often ranging from tens of volts to several kilovolts. |
Thermal Management | Efficient heat dissipation is crucial in power PCBs to prevent overheating and ensure reliable operation. |
Mechanical Strength | Power PCBs require robust mechanical design to withstand the stresses associated with high-power applications. |
Applications of Power PCBs
Power PCBs find applications in a wide range of industries and systems, including:
- Power supplies and converters
- Motor drives and controllers
- Renewable energy systems (e.g., solar inverters, wind turbines)
- Automotive electronics
- Industrial automation and control systems
1. Component Selection and Placement
One of the most critical aspects of power PCB design is selecting the right components and placing them strategically on the board. Here are some key considerations:
Choosing the Right Components
- Select components with appropriate voltage and current ratings to ensure they can handle the power requirements of your design.
- Consider the thermal characteristics of the components, such as their maximum junction temperature and thermal resistance.
- Opt for components with low parasitic inductance and capacitance to minimize unwanted effects at high frequencies.
Proper Component Placement
- Place power components, such as MOSFETs, diodes, and capacitors, close to each other to minimize the loop area and reduce parasitic inductance.
- Arrange components in a way that promotes efficient heat dissipation, allowing for adequate airflow and thermal management.
- Keep sensitive components, such as control circuitry, away from high-power components to minimize electromagnetic interference (EMI).
2. Copper Trace Sizing and Routing
The size and routing of copper traces on a power PCB play a crucial role in ensuring reliable power delivery and minimizing losses. Here are some guidelines to follow:
Determining Trace Width
- Calculate the required trace width based on the maximum current carrying capacity and the acceptable temperature rise.
- Use online trace width calculators or refer to industry standards, such as IPC-2221, to determine the appropriate trace width for your design.
- Consider using thicker copper layers (e.g., 2 oz or 4 oz) for high-current traces to improve current handling capacity and heat dissipation.
Trace Routing Techniques
- Route power traces as directly as possible, minimizing the overall trace length to reduce resistance and inductance.
- Avoid sharp corners and abrupt changes in trace direction to prevent current crowding and localized heating.
- Use multiple vias to connect power traces on different layers, ensuring low-resistance connections and improved heat dissipation.
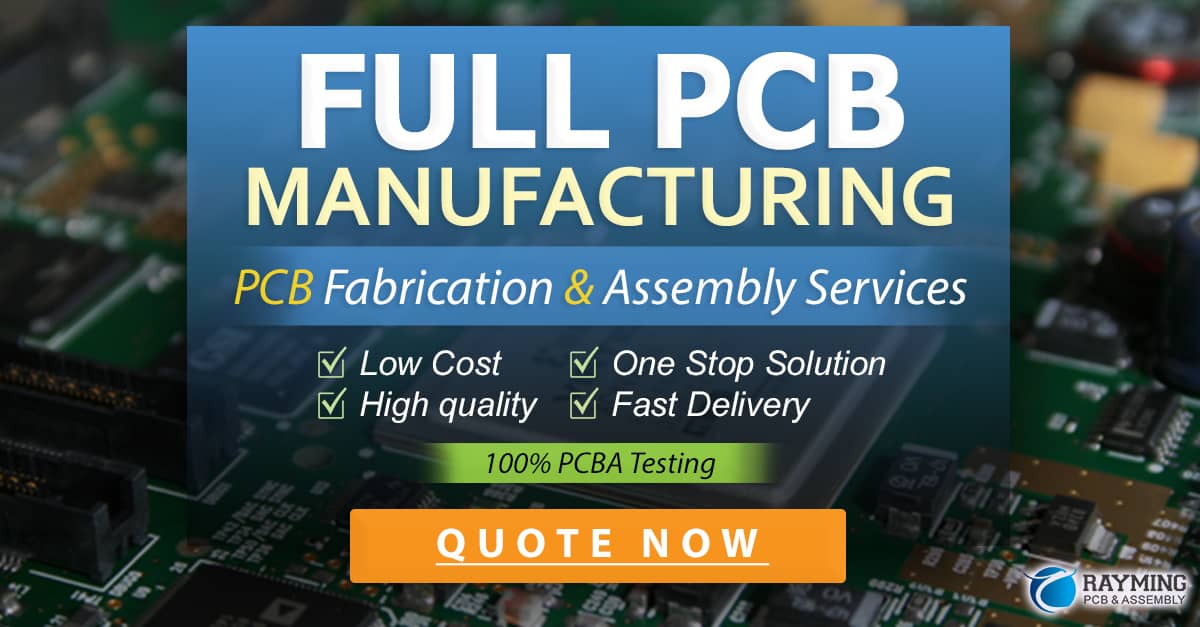
3. Grounding and Power Plane Design
Proper grounding and power plane design are essential for maintaining signal integrity, reducing EMI, and ensuring stable power delivery. Consider the following:
Grounding Strategies
- Implement a solid ground plane on one or more layers of the PCB to provide a low-impedance return path for currents.
- Use separate ground planes for analog and digital circuitry to minimize noise coupling between the two domains.
- Connect ground planes on different layers using multiple vias to ensure low-impedance connections.
Power Plane Design
- Dedicate one or more layers of the PCB to power planes, providing a low-impedance and low-inductance path for power distribution.
- Segment power planes based on different voltage levels or power domains to avoid interference and ensure proper isolation.
- Use appropriate decoupling capacitors near power pins of components to suppress high-frequency noise and stabilize the power supply.
4. Thermal Management Techniques
Effective thermal management is crucial in power PCB design to ensure reliable operation and prevent component failure due to overheating. Here are some techniques to consider:
Heatsinks and Thermal Vias
- Incorporate heatsinks on high-power components, such as MOSFETs and diodes, to dissipate heat efficiently.
- Use thermal vias to create a low-resistance thermal path between components and the heatsink or ground plane.
- Select heatsinks with appropriate thermal resistance and size based on the power dissipation requirements of the components.
PCB Material Selection
- Choose PCB materials with high thermal conductivity, such as aluminum-backed PCBs or metal-core PCBs, to enhance heat dissipation.
- Consider using thermally conductive PCB substrates, such as ceramic or polyimide, for high-temperature applications.
Airflow and Cooling
- Design the PCB layout to promote natural convection or forced airflow, allowing for efficient heat removal.
- Incorporate cooling fans or heatsinks with built-in fans to actively dissipate heat from the PCB and its components.
5. Testing and Verification
Before finalizing your power PCB design, it’s essential to perform thorough testing and verification to ensure its functionality, reliability, and safety. Consider the following:
Prototype Testing
- Fabricate a prototype of your power PCB and perform comprehensive functional testing to verify its operation under various conditions.
- Conduct thermal imaging or temperature measurements to identify hot spots and ensure proper thermal management.
- Test the PCB under different load conditions to validate its performance and identify any potential weaknesses.
Compliance Testing
- Ensure that your power PCB complies with relevant industry standards and regulations, such as UL, IEC, or EN standards.
- Perform electromagnetic compatibility (EMC) testing to verify that your PCB meets the required EMI and electromagnetic susceptibility (EMS) limits.
- Conduct safety tests, such as isolation and dielectric withstand tests, to ensure the PCB can operate safely under the specified voltage and current conditions.
Frequently Asked Questions (FAQ)
-
What is the difference between a power PCB and a regular PCB?
A power PCB is specifically designed to handle high currents and voltages, whereas a regular PCB is designed for lower power applications. Power PCBs have thicker copper traces, larger components, and enhanced thermal management features compared to regular PCBs. -
How do I determine the appropriate trace width for my power PCB?
The appropriate trace width depends on the maximum current carrying capacity and the acceptable temperature rise. You can use online trace width calculators or refer to industry standards, such as IPC-2221, to determine the suitable trace width based on your design requirements. -
What is the purpose of using a ground plane in a power PCB?
A ground plane serves as a low-impedance return path for currents, minimizing noise and ensuring stable power delivery. It also helps in reducing electromagnetic interference (EMI) and improving signal integrity. -
How can I effectively manage heat dissipation in my power PCB?
Effective heat dissipation can be achieved through various techniques, such as using heatsinks on high-power components, incorporating thermal vias to create a low-resistance thermal path, selecting PCB materials with high thermal conductivity, and designing the PCB layout to promote natural convection or forced airflow. -
Why is testing and verification important in power PCB design?
Testing and verification are crucial to ensure the functionality, reliability, and safety of your power PCB. Prototype testing helps identify any design flaws or performance issues, while compliance testing ensures that your PCB meets the required industry standards and regulations for EMC and safety.
Conclusion
Designing a power PCB requires careful consideration of various factors, including component selection and placement, copper trace sizing and routing, grounding and power plane design, thermal management, and testing and verification. By understanding and applying these key principles, beginners can create robust and reliable power PCBs that meet the demands of their specific applications.
Remember to always prioritize safety, adhere to industry standards and best practices, and seek guidance from experienced professionals when needed. With practice and continuous learning, you can master the art of power PCB design and create high-quality, efficient, and reliable power electronics systems.
0 Comments