Introduction to Polyethylene PCBs
Polyethylene (PE) is a thermoplastic polymer that has gained popularity in recent years as a substrate material for printed circuit boards (PCBs). PE offers several unique properties that make it an attractive choice for certain PCB applications. In this article, we will explore the benefits of polyethylene PCBs, their manufacturing process, and the key players in the PE PCB manufacturing industry.
Advantages of Polyethylene PCBs
Polyethylene PCBs offer several advantages over traditional PCB materials like FR-4:
- Low dielectric constant and dissipation factor
- Excellent chemical resistance
- High flexibility and durability
- Lightweight
- Cost-effective
These properties make PE PCBs ideal for high-frequency applications, flexible electronics, and harsh environments.
Polyethylene PCB Manufacturing Process
Raw Materials
The primary raw material for PE PCBs is high-density polyethylene (HDPE). HDPE is a type of polyethylene with a higher density and tensile strength compared to low-density polyethylene (LDPE). Other materials used in the manufacturing process include copper foil, adhesives, and soldermask.
Substrate Preparation
The first step in manufacturing PE PCBs is preparing the substrate. HDPE sheets are cut to the desired size and thickness. The surface of the HDPE is then treated to improve adhesion with the copper foil. This can be done through plasma treatment, corona discharge, or chemical etching.
Lamination
Once the HDPE substrate is prepared, it is laminated with copper foil using heat and pressure. The copper foil is typically treated with a roughening process to improve adhesion with the HDPE. The lamination process creates a strong bond between the HDPE and copper, ensuring the reliability of the final PCB.
Circuit Patterning
After lamination, the PCB undergoes circuit patterning. This involves applying a photoresist layer to the copper, exposing it to UV light through a photomask, and developing the photoresist to create the desired circuit pattern. The exposed copper is then etched away using a chemical solution, leaving only the desired circuit traces.
Drilling and Plating
Holes are drilled in the PCB for through-hole components and vias. The holes are then plated with copper to create electrical connections between the layers of the PCB. This is typically done using electroless copper plating followed by electrolytic copper plating.
Soldermask and Silkscreen
A soldermask layer is applied to the PCB to protect the copper traces from oxidation and prevent solder bridges during assembly. The soldermask is typically applied using a screen printing process and then cured using UV light. A silkscreen layer is then applied to the PCB to add component labels, logos, and other markings.
Surface Finish
The final step in the PE PCB manufacturing process is applying a surface finish to the exposed copper areas. This is done to prevent oxidation and improve solderability. Common surface finishes for PE PCBs include HASL (hot air solder leveling), ENIG (electroless nickel immersion gold), and OSP (organic solderability preservative).
Key Players in the Polyethylene PCB Manufacturing Industry
Several PCB Manufacturers have specialized in producing polyethylene PCBs. Here are some of the key players in the industry:
Company | Location | Specialization |
---|---|---|
Printed Circuits | USA | High-frequency PE PCBs |
Flexible Circuit Technologies | USA | Flexible PE PCBs |
Cisel | Taiwan | PE PCBs for automotive applications |
FINECS | South Korea | Multi-layer PE PCBs |
Polyonics | USA | PE PCBs for harsh environments |
These companies have invested in specialized equipment and processes to manufacture high-quality polyethylene PCBs for various applications.
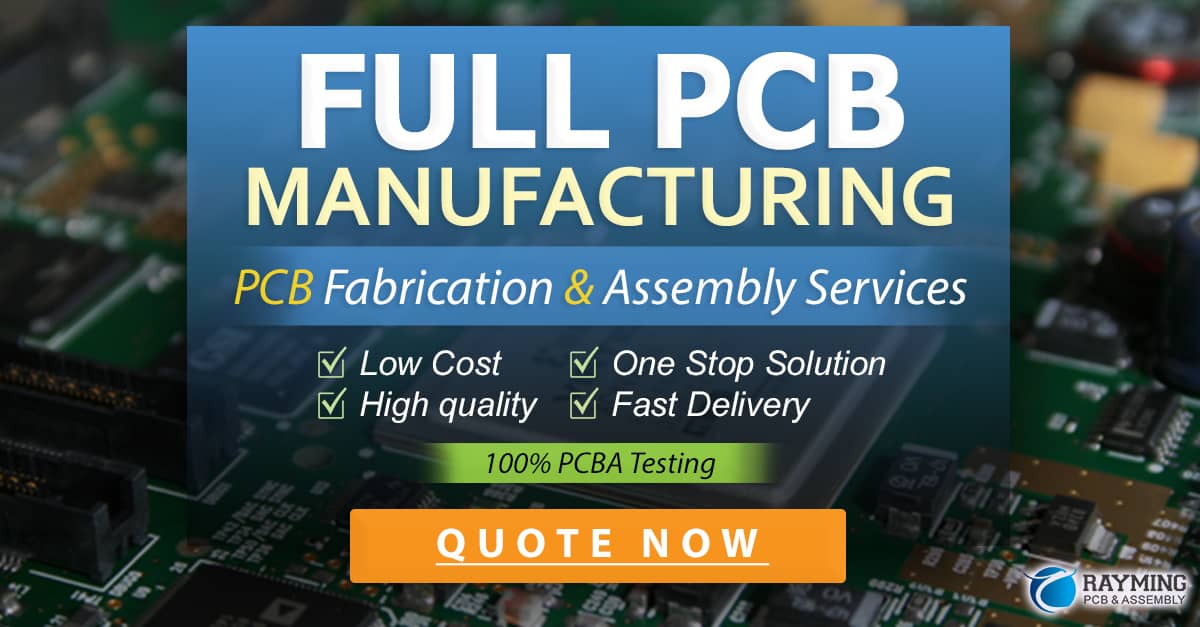
Applications of Polyethylene PCBs
High-Frequency Applications
One of the primary applications of PE PCBs is in high-frequency electronics. The low dielectric constant and dissipation factor of polyethylene make it an excellent substrate for high-frequency PCBs. PE PCBs are commonly used in RF and microwave applications, such as antennas, filters, and amplifiers.
Flexible Electronics
Polyethylene’s flexibility and durability make it an ideal material for flexible electronics. PE PCBs can be bent, twisted, and stretched without damaging the circuit traces. This makes them suitable for wearable electronics, medical devices, and other applications where flexibility is required.
Automotive Electronics
PE PCBs are also finding use in automotive electronics due to their excellent chemical resistance and durability. Polyethylene’s resistance to moisture, oil, and other automotive fluids makes it a reliable choice for under-the-hood electronics. PE PCBs are used in applications such as engine control units, sensors, and power modules.
Industrial and Harsh Environments
Polyethylene’s chemical resistance and durability also make it suitable for use in industrial and harsh environments. PE PCBs can withstand exposure to chemicals, extreme temperatures, and mechanical stress. They are used in applications such as oil and gas exploration, chemical processing, and aerospace.
Challenges and Future Trends
Challenges in PE PCB Manufacturing
Despite the benefits of polyethylene PCBs, there are some challenges in their manufacturing process. One of the main challenges is the lower adhesion strength between polyethylene and copper compared to traditional PCB materials. This can lead to delamination and reliability issues if not properly addressed. PCB manufacturers have developed specialized surface treatments and adhesives to overcome this challenge.
Another challenge is the limited availability of polyethylene materials and processing equipment compared to traditional PCB materials. This can lead to longer lead times and higher costs for PE PCBs. However, as demand for PE PCBs grows, more suppliers and equipment manufacturers are entering the market.
Future Trends in PE PCB Manufacturing
The polyethylene PCB market is expected to grow in the coming years, driven by increasing demand for high-frequency electronics, flexible electronics, and harsh environment applications. Some of the future trends in PE PCB manufacturing include:
- Development of higher-performance polyethylene materials with improved electrical and mechanical properties
- Adoption of advanced manufacturing processes such as 3D printing and laser drilling for faster and more precise PCB fabrication
- Integration of PE PCBs with other advanced materials such as graphene and carbon nanotubes for enhanced functionality
- Expansion of PE PCB applications into new markets such as renewable energy and smart cities
As the PE PCB industry evolves, PCB manufacturers will need to invest in research and development to stay competitive and meet the changing needs of their customers.
FAQs
- Q: What are the main advantages of using polyethylene for PCBs?
A: Polyethylene offers several advantages for PCBs, including low dielectric constant and dissipation factor, excellent chemical resistance, high flexibility and durability, lightweight, and cost-effectiveness.
- Q: What surface finishes are commonly used for polyethylene PCBs?
A: Common surface finishes for PE PCBs include HASL (hot air solder leveling), ENIG (electroless nickel immersion gold), and OSP (organic solderability preservative).
- Q: Can polyethylene PCBs be used for flexible electronics?
A: Yes, polyethylene’s flexibility and durability make it an ideal material for flexible electronics. PE PCBs can be bent, twisted, and stretched without damaging the circuit traces, making them suitable for wearable electronics, medical devices, and other flexible applications.
- Q: Are there any challenges in manufacturing polyethylene PCBs?
A: One of the main challenges in manufacturing PE PCBs is the lower adhesion strength between polyethylene and copper compared to traditional PCB materials. This can lead to delamination and reliability issues if not properly addressed. PCB manufacturers have developed specialized surface treatments and adhesives to overcome this challenge.
- Q: What are some future trends in polyethylene PCB manufacturing?
A: Some future trends in PE PCB manufacturing include the development of higher-performance polyethylene materials, adoption of advanced manufacturing processes such as 3D printing and laser drilling, integration of PE PCBs with other advanced materials such as graphene and carbon nanotubes, and expansion of PE PCB applications into new markets such as renewable energy and smart cities.
Conclusion
Polyethylene PCBs offer unique properties that make them an attractive choice for high-frequency, flexible, and harsh environment applications. Their low dielectric constant, excellent chemical resistance, and durability set them apart from traditional PCB materials. As the demand for advanced electronics continues to grow, the PE PCB market is expected to expand, driving innovation in materials, manufacturing processes, and applications.
PCB manufacturers specializing in polyethylene PCBs are well-positioned to capitalize on this growth by offering high-quality, reliable products that meet the evolving needs of their customers. By staying at the forefront of technology and investing in research and development, these manufacturers can help shape the future of the electronics industry.
0 Comments