What is PCB X-Ray Inspection?
PCB X-ray inspection is a non-destructive testing method that utilizes X-ray technology to examine the internal structure of an assembled printed circuit board. By passing X-rays through the PCB, manufacturers can create detailed images of the board’s components, solder joints, and other critical features. These images allow for the detection of defects and anomalies that may not be visible to the naked eye or through other inspection methods.
How PCB X-ray Inspection Works
The process of PCB X-ray inspection involves placing the assembled PCB into an X-ray inspection machine. The machine then generates X-rays, which pass through the PCB and are captured by a detector on the opposite side. As the X-rays pass through the various materials on the PCB, they are absorbed or transmitted based on the material’s density and thickness. This results in a grayscale image that represents the internal structure of the PCB.
The X-ray images are then analyzed by trained operators or advanced software algorithms to identify any defects or anomalies. These may include:
- Component placement errors
- Solder joint defects (e.g., voids, bridges, insufficient solder)
- Broken or damaged components
- Foreign object debris (FOD)
- Internal structural issues (e.g., delamination, cracks)
The Importance of PCB X-ray Inspection in PCBA
PCB X-ray inspection plays a vital role in ensuring the quality and reliability of assembled printed circuit boards. By detecting and addressing potential issues early in the manufacturing process, manufacturers can prevent costly rework, reduce product failures, and improve overall customer satisfaction.
1. Identifying Hidden Defects
One of the primary benefits of PCB X-ray inspection is its ability to detect hidden defects that may not be visible through other inspection methods. For example, ball grid array (BGA) packages and other high-density components can obscure solder joints, making it difficult to assess their quality through visual inspection alone. X-ray inspection allows manufacturers to examine these hidden areas and identify any potential issues.
2. Ensuring Proper Component Placement
Proper component placement is critical to the functionality and reliability of an assembled PCB. PCB X-ray inspection can verify that components are placed in the correct locations and orientations, helping to prevent issues related to incorrect component placement.
3. Detecting Solder Joint Defects
Solder joint defects, such as voids, bridges, and insufficient solder, can compromise the electrical and mechanical integrity of an assembled PCB. PCB X-ray inspection can detect these defects, allowing manufacturers to address them before the board is shipped to the customer.
4. Compliance with Industry Standards
Many industries, such as aerospace, automotive, and medical, have strict quality control requirements for PCBAs. PCB X-ray inspection helps manufacturers meet these standards by providing objective evidence of the board’s internal quality.
PCB X-ray Inspection Techniques
There are several PCB X-ray inspection techniques available, each with its own advantages and limitations. The choice of technique depends on factors such as the complexity of the board, the types of components used, and the specific defects being targeted.
2D X-ray Inspection
2D X-ray inspection is the most basic and widely used technique in PCB X-ray inspection. It involves capturing a single, two-dimensional image of the PCB from a fixed angle. This technique is suitable for detecting gross defects, such as missing components or large solder voids, but may not provide sufficient detail for more subtle issues.
Oblique View X-ray Inspection
Oblique view X-ray inspection involves capturing multiple images of the PCB from different angles, typically ranging from 30° to 60°. By combining these images, manufacturers can create a more comprehensive view of the board’s internal structure, making it easier to detect defects that may be hidden in a single 2D image.
Computed Tomography (CT) X-ray Inspection
Computed tomography (CT) X-ray inspection is an advanced technique that involves capturing a series of X-ray images as the PCB rotates 360°. These images are then processed by software to create a detailed, three-dimensional reconstruction of the board’s internal structure. CT X-ray inspection is particularly useful for examining complex, multi-layered PCBs and identifying defects that may be difficult to detect using other methods.
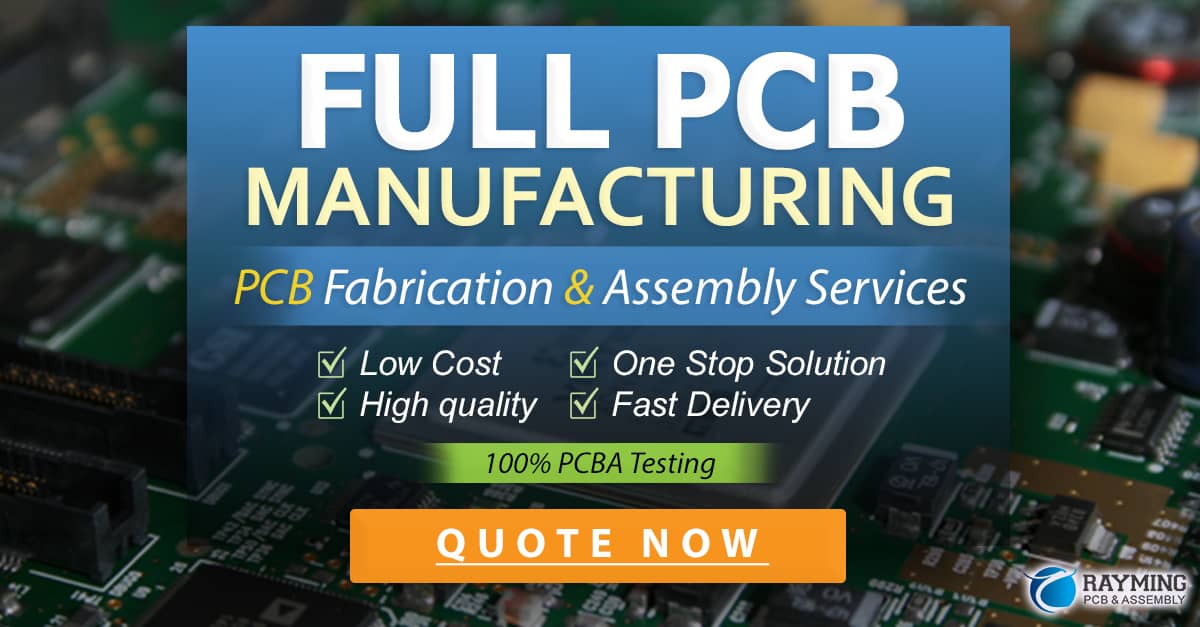
Automated vs. Manual PCB X-ray Inspection
PCB X-ray inspection can be performed manually by trained operators or automatically using advanced software algorithms. Each approach has its own advantages and limitations.
Manual PCB X-ray Inspection
Manual PCB X-ray inspection relies on the expertise and experience of trained operators to identify defects and anomalies in X-ray images. This approach allows for a more nuanced and context-aware analysis of the board’s internal structure, as operators can draw on their knowledge of the specific PCB design and manufacturing process.
However, manual inspection can be time-consuming and subject to human error, particularly when dealing with large volumes of boards or complex designs.
Automated PCB X-ray Inspection
Automated PCB X-ray inspection uses advanced software algorithms to analyze X-ray images and identify defects and anomalies. This approach offers several advantages over manual inspection, including:
- Increased speed and throughput
- Improved consistency and repeatability
- Reduced labor costs
- Ability to detect subtle defects that may be missed by human operators
However, automated inspection may require significant upfront investment in software and hardware, as well as ongoing maintenance and updates to keep pace with evolving PCB designs and manufacturing processes.
Integrating PCB X-ray Inspection into the PCBA Process
To maximize the benefits of PCB X-ray inspection, it is important to integrate it effectively into the overall PCBA process. This involves considering factors such as:
- Inspection frequency: Determining how often X-ray inspection should be performed (e.g., every board, batch sampling)
- Inspection points: Identifying the most appropriate stages in the manufacturing process to perform X-ray inspection (e.g., after solder reflow, final assembly)
- Defect classification and reporting: Establishing clear criteria for classifying and reporting defects identified through X-ray inspection
- Corrective action: Implementing a process for addressing identified defects and preventing their recurrence
By carefully planning and executing PCB X-ray inspection, manufacturers can ensure that it delivers maximum value in terms of quality control and process improvement.
The Future of PCB X-ray Inspection
As PCB designs continue to increase in complexity and miniaturization, the importance of PCB X-ray inspection is only set to grow. Emerging technologies and trends, such as advanced packaging techniques (e.g., 3D packaging, system-in-package) and the use of new materials (e.g., high-density interconnect substrates), will present new challenges and opportunities for X-ray inspection.
To keep pace with these developments, manufacturers will need to invest in advanced X-ray inspection equipment and software, as well as the training and development of skilled operators. Additionally, the integration of artificial intelligence (AI) and machine learning (ML) techniques into automated X-ray inspection systems promises to further enhance defect detection capabilities and streamline the inspection process.
Frequently Asked Questions (FAQ)
1. What types of defects can PCB X-ray inspection detect?
PCB X-ray inspection can detect a wide range of defects, including component placement errors, solder joint defects (e.g., voids, bridges, insufficient solder), broken or damaged components, foreign object debris (FOD), and internal structural issues (e.g., delamination, cracks).
2. Is PCB X-ray inspection suitable for all types of PCBs?
While PCB X-ray inspection is generally applicable to most types of PCBs, it is particularly valuable for boards with high-density components, such as ball grid arrays (BGAs) and chip-scale packages (CSPs), as well as multi-layered boards with complex internal structures.
3. How does PCB X-ray inspection compare to other inspection methods, such as automated optical inspection (AOI)?
PCB X-ray inspection offers several advantages over other inspection methods, such as its ability to detect hidden defects and examine the internal structure of the board. However, it is often used in conjunction with other methods, such as AOI, to provide a comprehensive quality control solution.
4. Can PCB X-ray inspection be used for rework and repair?
Yes, PCB X-ray inspection can be used to guide rework and repair efforts by providing detailed images of the board’s internal structure and helping to pinpoint the location and nature of defects.
5. What factors should be considered when selecting a PCB X-ray inspection system?
When selecting a PCB X-ray inspection system, manufacturers should consider factors such as the system’s resolution and magnification capabilities, the types of X-ray techniques supported (e.g., 2D, oblique view, CT), the speed and throughput of the system, and the ease of integration with existing manufacturing processes and software systems.
Conclusion
PCB X-ray inspection is a critical component of quality control in printed circuit board assembly (PCBA). By providing detailed, non-destructive imaging of a board’s internal structure, X-ray inspection helps manufacturers identify and address potential defects and anomalies that could compromise the functionality and reliability of the final product.
As PCB designs continue to evolve and increase in complexity, the importance of PCB X-ray inspection will only continue to grow. By investing in advanced X-ray inspection technologies and integrating them effectively into the PCBA process, manufacturers can ensure that they are well-positioned to meet the quality and reliability demands of their customers, both now and in the future.
Inspection Method | Advantages | Limitations |
---|---|---|
2D X-ray Inspection | – Simple and widely used – Suitable for detecting gross defects |
– Limited detail for subtle defects – May miss defects hidden in a single 2D image |
Oblique View X-ray Inspection | – Provides a more comprehensive view of the board’s internal structure – Can detect defects hidden in a single 2D image |
– Requires capturing multiple images from different angles – May still miss some subtle defects |
Computed Tomography (CT) X-ray Inspection | – Creates a detailed 3D reconstruction of the board’s internal structure – Useful for examining complex, multi-layered PCBs – Can identify defects difficult to detect using other methods |
– Requires specialized equipment and software – Can be time-consuming and resource-intensive |
Table 1: Comparison of PCB X-ray Inspection Techniques
In conclusion, PCB X-ray inspection is an essential tool for ensuring the quality and reliability of printed circuit board assemblies. By understanding the importance of X-ray inspection, the various techniques available, and how to effectively integrate it into the PCBA process, manufacturers can optimize their quality control efforts and deliver products that meet the highest standards of performance and durability.
0 Comments