A printed circuit board (PCB) transformer is a type of transformer constructed directly on a printed circuit board using conductive traces as windings instead of wires. PCB transformers provide galvanic isolation, voltage step-up or step-down, and other transforming functions in a compact footprint that integrates directly into modern electronic devices.
Key Characteristics of PCB Transformers
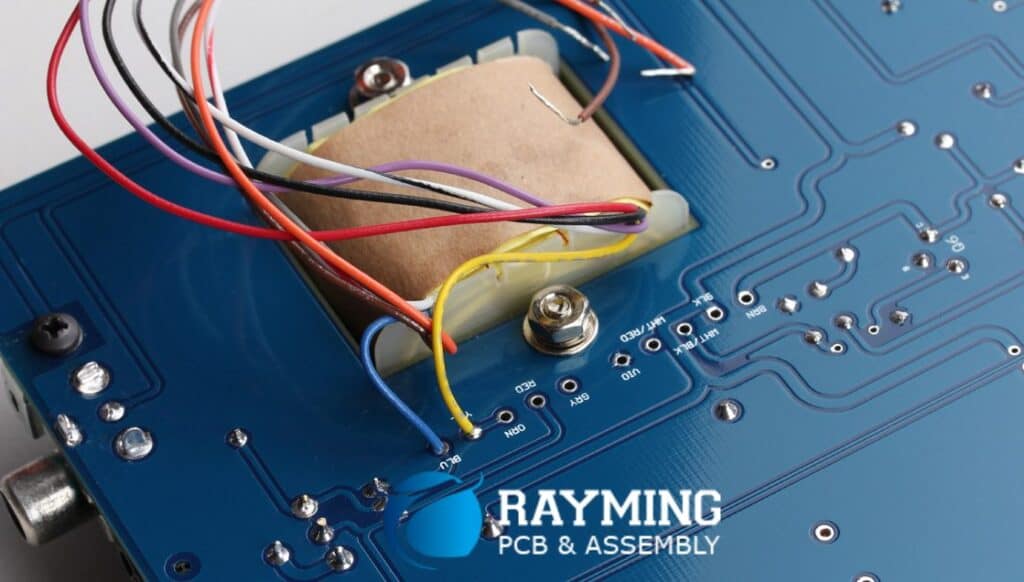
PCB transformers offer several advantages compared to traditional wire-wound versions:
Compact Size
Etching winding traces onto the PCB substrate creates a low profile transformer ideal for space-constrained applications like mobile devices. Heights under 3mm are common.
Light Weight
Without heavy cores or wire windings, PCB transformer weight ranges from a few grams to under one ounce even for multilayer designs.
Inherent PCB Integration
Monolithic construction directly on the PCB facilitates placement close to powered circuits requiring transformation, saving space versus discrete components on standoffs.
Flexibility
Designer control over winding geometries from oval, circular and rectangular to complex irregular shapes allows great flexibility to utilize available board space.
Reliability
Robust epoxy-glass PCB substrates protect against environmental factors and mechanical stresses while eliminating connections prone to failure.
Economical
Automated PCB etching enables high volume, low cost production compared to manual winding and assembly using discrete wires and bobbins.
How PCB Transformers Work
PCB transformers leverage principles of electromagnetic induction in the same manner as wire-wound versions. Alternating current in a primary winding creates a fluctuating magnetic field picked up by an isolated secondary winding. This mutually induced voltage can be adjusted up or down per the windings’ calibrated number of turns.
Planar Magnetics
In PCB transformers, the windings comprise etched copper traces on layers stacked to create a transformer lying flat on the board surface. The layered arrangement defines the inductive coupling between primary and secondary.
Magnetic Core
While some PCB transformers rely solely on air for flux conduction, most encapsulate an iron-powdered ferrite core within winding openings to control and channel magnetic fields for enhanced inductance.
Insulating Layers
Dielectric laminates separating winding layers provide turn-to-turn and primary-to-secondary insulation up to thousands of volts while minimizing parasitic capacitance.
PCB Transformer Construction
Modern PCB transformers leverage advanced PCB materials and processing capabilities for precision construction.
Windings
Fine line traces etched on copper layers form accurately calibrated windings with the number of turns set by the designer. Controlled geometries also tune self-capacitance and leakage inductance behavior.
Magnetic Core
Ferrites fabricated in thin sheets or beads are precisely placed in alignment with winding openings to channel magnetic flux. Some cores feature openings to allow winding traces to pass through for stronger coupling.
Dielectrics
Thin insulative laminates like FR4 or polyimides separate winding layers, providing turn isolation and insulation strength up to thousands of volts in compact form factors.
Vias
Plated through holes efficiently interconnect traces across layers in multilayer designs, allowing precise series and parallel connections to form transformer winding turns and taps.
Solder Pads
Solderable contacts along the perimeter or underside enable convenient PCB mounting for through-hole or surface-mount installations.
PCB Transformer Types and Applications
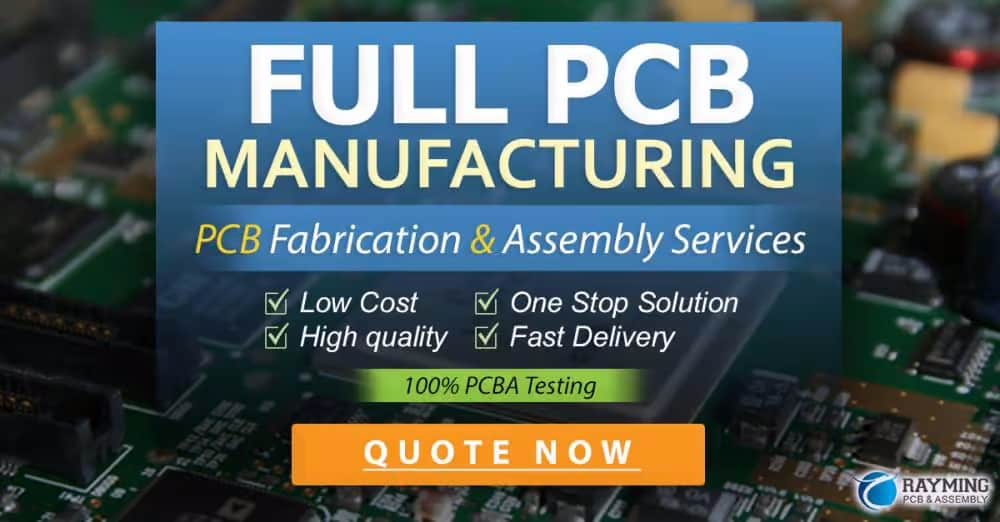
PCB transformers support diverse application requirements across electronics:
Signal or Low Power Transformers
Small signal transformers with lower power handling step voltages up or down while isolating different device areas. Applications include audio circuits, USB & Ethernet interfaces, vehicle cameras, etc.
High Frequency RF Transformers
Specially designed RF transformers built into antennas, amplifiers, mixers and other radio circuits provide impedance matching and balanced signals.
Gate Drive Transformers
These provide isolated power and signals to rapidly switch high-power transistors on and off in converter and inverter applications.
DC-DC Converter Transformers
Step-down transformers help convert direct current voltages to lower isolated levels for powering downstream switch-mode supply circuitry.
EMI Filtering Transformers
Common mode choke transformers suppress electromagnetic interference noise propagating between devices and power lines.
High Voltage Flyback Transformers
These produce very high secondary voltages – often in the 10’s of kV range – to drive applications like cathode ray tubes or ionizers, while avoiding direct human contact with hazardous potentials.
High Power Density Transformers
Custom designs maximize power handling and minimizes size/weight for highly compact transformation up to several hundred watts to support miniaturized devices and portability.
Benefits of Using a PCB Transformer
Reasons to consider integrating a PCB transformer versus traditional wire-wound versions include:
Size Reduction
Etched construction collapses conventional bobbins and cores into a low height component measured in millimeters rather than centimeters. Ideal for ever-shrinking products.
Lower Mass
Lack of heavy wire windings or bulky bobbins creates a lightweight transformer option weighing just a few grams – a fraction of comparable off-board versions.
Cost Efficiency
Economies of scale apply to PCB production. Precision etching also eliminates manual winding labor and related variability while boosting reliability.
Simplified Assembly
Monolithic PCB construction avoids installing and connecting separate transformer components. Automated SMT pickup and placement integrates easily onto PCBs.
Enhanced Reliability
Robust epoxy-glass substrates protect against stress, shock and vibration. Eliminating wired connections also removes failure points.
Design Flexibility Windings can take on any shape to match surrounding board geometries. Multiple secondary taps enable flexible output configurations from a single device.
Performance gains
Careful layout optimizes magnetic coupling while minimizing inter-winding capacitance for wide bandwidth and efficiency. Small form factors also operate at higher frequencies.
For today’s electronics, PCB integration and miniaturization provides higher performance in less space at lower costs.
PCB Transformer Design Considerations
Realizing the benefits of on-board transformation requires careful design for intended functionality:
Output Power Determine voltage, current and power level needs to drive downstream circuitry, factoring in some safety margin. This guides physical size parameters.
Input Voltage
The excitation voltage that will power the primary winding impacts heat dissipation and clearance constraints. Wide input ranges require compensation.
Turns Ratio Choose the windings ratio to scale input voltage up or down per application requirements. Step-down ratios over 10:1 are common for switchers.
Efficiency Design for targeted efficiency by sizing core materials to operating frequencies and setting conductor widths/spacings to manage skin effects.
Thermal Management Power levels dictate dissipated heat budgets. Max temperatures inform construction materials, copper weights, and cooling provisions if necessary.
Insulation Withstand Voltages Safety needs based on isolation type (functional, basic, supplementary, reinforced) set dielectric layer quantities and quality to achieve insulation ratings.
Environment
Parameters like production soldering profiles, operating temperatures, humidity exposure levels etc. guide material selections like substrate class and ferrite composition.
Standards Settings aligned to application standards like Telcordia, DO-160, IPC etc. ensure properly derated designs meeting reliability metrics for industry qualification.
Manufacturing Processes for PCB Transformers
Specialized manufacturing techniques enable quality and precision PCB transformer fabrication.
Winding Etch Patterning – Photolithography and accurate etched copper removal creates precision winding geometries calibrated to yield specific self-inductances.
Layer Stacking & Registration – Careful alignment of substrate cores and pre-preg dielectric layers prevent winding short circuits while ensuring consistency.
Core Placement – Robotic pick-and-place equipment positions ferrite core pieces into winding openings with tight positional tolerances.
Auto-Insertion – Surface mount contacts get reliably inserted along the exterior edges to simplify downstream PCB mounting.
Solder Reflow Integration – Reflow soldering attaches transformer onto final PCB without damaging heat-sensitive ferrite cores.
Conformal Coating – Protective coatings prevent environmental contamination that could degrade dielectric isolation over product lifetime.
HiPot Testing – Automated equipment verifies insulation voltage withstand ratings meet target design specifications.
These fabrication processes enable reliable construction of sensitive, high-quality PCB transformers in industrial volumes.
Performance Testing PCB Transformers
To validate designs and reliability, PCB transformers undergo various qualification tests:
Winding Resistance – Validates trace conductivities match intended resistivity to minimize loss.
Insulation Resistance – Confirms dielectric layers provide required isolation up to hi-pot test voltages ratings.
Inductance – Quantifies designed self-inductance values to transforming requirements.
DC Resistance – Ensures low DCR meeting efficiency targets and thermal rise limits.
Hipot – Verifies insulation level compliance for regulatory safety approvals.
Turns Ratio – Assesses precision winding traces achieve targeted step-up or step-down ratios.
Leakage Inductance – Measures unwanted coupling between windings causing energy losses.
Once characterized, statistical process controls maintain parameters within acceptable guard bands.
Industry Standards for PCB Transformers
To ensure safety, reliability and performance for end applications, PCB transformers may require certification to industry standards like:
- IEC/EN 62368-1 – Audio/video, information and communication technology equipment safety requirements
- IEC 60950-1 – Information technology equipment safety
- IEC 60601 – Medical electrical equipment safety
- J-STD-020 – Soldering standards for electrical connections
- IPC-A-610 – Acceptability for electronic assemblies
- Telcordia GR-468/NEBS – Telecom equipment environment/safety
- IEC60068 – Environmental stress testing
- RTCA/DO-160 – Environmental conditions for airborne equipment
Compliance demonstrates transformers are qualified for safety and reliability within their intended operating environments. This qualifies them for deployment into customer end products.
Future PCB Transformer Trends
Advancing PCB materials science and demand for higher power densities drive ongoing innovation, including:
Miniaturization
Continual efforts to condense converters, inverters, isolators etc. apply pressure for still smaller, lower profile planar transformers. Expect widths under 10mm and sub 2mm heights.
Higher Frequency/Efficiency Wide bandgap semiconductors enable megahertz switching frequencies catering to more integrated, efficient voltage transformation footprints.
Embedded Actives
Transformers may co-package complementary active components like integrated circuits or control components, transforming entire functional modules.
Additive Mfg
Emerging multi-metal additive printing could enable fabrication of entire PCB transformers with windings, cores and contacts in a single process step.
Integrated Cooling
Thermal management techniques like patterned copper heat sinks or cooling vias help dissipate heat from high power density PCB transformers.
Already displacing conventional transformers in many applications, expect ongoing PCB transformer enhancements meeting the ever-increasing demands of modern electronics.
Frequently Asked Questions
How are number of winding turns determined in a PCB transformer?
Primary and secondary PCB transformer winding turns comprise conductive circuit traces on layers stacked through the thickness of the assembly. Each complete etched loop on a layer counts as one turn. The number of turns determines the transformer power transfer ratio. Tight tolerances on trace geometries etched using photolithography ensures precision turn ratios.
What dielectric materials separate PCB transformer windings?
Transformer winding layers require excellent electrical insulation to prevent shorting while also enabling high magnetic permeability. Common dielectric materials integrated during PCB transformer fabrication include polyimides like DuPont Kapton, epoxy resin-impregnated fiberglass composites like FR4, and various ceramic-filled formulations. Electrical, environmental, thermal and mechanical properties are all considered during material selection.
How are PCB transformer winding layers interconnected?
In multilayer designs, winding traces across various layers get connected through vertical plated vias drilled through the PCB structure. These enable winding continuity as traces route through needed layers. Careful staggering and spacing prevent unintended connections between unrelated traces. Additional connection pads etched on exterior layers allow transformer integration onto application circuit boards through soldering.
How is magnetic flux channeled in a PCB transformer?
While some PCB transformer geometries leverage only air core designs, most encapsulate specifically shaped ferrite cores within the winding aperture to control flux flows. The ferrite intensifies magnetization levels. Cores typically comprise thin sheets or beads of manganese-zinc or nickel-zinc ferritic materials placed in alignment with etched winding patterns during transformer assembly. Some feature center posts for windings to pass through. Proper core sizing balances inductance versus efficiency for the operating environment.
What construction approaches maximize PCB transformer reliability?
Careful material selection matches dielectric properties and copper weights suitable for operating voltages and temperatures. Precise photolithographic winding etching combined with properly calibrated automated core placement ensures dimensional consistency. Conformal coatings protect against environmental contaminants while high pot testing validates voltage isolation margins. These careful fabrication controls support transformer longevity over extreme conditions. Statistical process controls then maintain parameters within acceptable guard bands. The result is millions of hours mean time between failure rates.
0 Comments