Understanding PCB Thickness
PCB thickness is typically measured in either millimeters (mm) or mils (thousandths of an inch). The most common PCB thickness standards are:
Thickness (mm) | Thickness (mils) |
---|---|
0.4 | 15.75 |
0.6 | 23.62 |
0.8 | 31.50 |
1.0 | 39.37 |
1.2 | 47.24 |
1.6 | 62.99 |
2.0 | 78.74 |
Factors Influencing PCB Thickness Choice
Several factors can influence the choice of PCB thickness, including:
-
Application requirements: The intended use of the PCB can dictate its thickness. For example, thicker boards are often used in high-power applications or when greater mechanical strength is needed.
-
Layer count: As the number of layers in a PCB increases, the overall thickness of the board also increases. Each additional layer adds to the thickness of the PCB.
-
Component size and weight: The size and weight of the components mounted on the PCB can affect the required thickness. Heavier components may necessitate a thicker board for improved support.
-
Manufacturing constraints: PCB Manufacturers have limitations on the minimum and maximum thicknesses they can produce. It is essential to consult with the manufacturer to ensure the desired thickness is achievable.
Standard PCB Thicknesses
0.4mm (15.75 mils)
0.4mm PCBs are the thinnest standard option and are suitable for compact, lightweight devices. They are commonly used in applications such as:
- Mobile phones
- Wearable electronics
- Flexible circuits
However, 0.4mm PCBs have limitations in terms of layer count and the size of components they can support.
0.6mm (23.62 mils)
0.6mm PCBs offer a balance between thickness and flexibility. They are used in a wide range of applications, including:
- Consumer electronics
- Automotive electronics
- Industrial control systems
0.6mm PCBs can support a moderate layer count and component size.
0.8mm (31.50 mils)
0.8mm PCBs are a popular choice for many electronic devices due to their increased mechanical strength and ability to support more layers and larger components compared to thinner options. Applications include:
- Computers and peripherals
- Telecommunications equipment
- Medical devices
1.0mm (39.37 mils)
1.0mm PCBs provide a robust solution for applications that require higher layer counts or larger components. They are used in:
- Servers and networking equipment
- Power electronics
- Aerospace and defense systems
1.2mm (47.24 mils) and Above
PCBs with thicknesses of 1.2mm and above are used in specialized applications that demand exceptional mechanical strength or high power handling capability. Examples include:
- High-power LED lighting
- Electric vehicle power electronics
- Industrial motor drives
Designing PCBs with Optimal Thickness
When designing a PCB, it is crucial to select an appropriate thickness based on the specific requirements of the application. Consider the following factors:
Layer Stack-Up
The number of layers in a PCB directly affects its thickness. Work with your PCB manufacturer to develop an optimal layer stack-up that meets your design requirements while minimizing thickness.
Copper Weight
The copper weight, or thickness, of the conductive layers in a PCB also contributes to the overall board thickness. Thicker copper layers are used for high-current applications but can increase the overall PCB thickness.
Dielectric Material
The choice of dielectric material between layers can impact the PCB’s thickness and electrical properties. Some high-performance dielectric materials allow for thinner PCBs while maintaining good electrical characteristics.
Tolerance and Variance
PCB manufacturers specify tolerances for board thickness, which can vary depending on the manufacturing process and materials used. It is essential to understand these tolerances and design your PCB accordingly.
Prototyping and Testing
Before finalizing your PCB design, it is recommended to produce prototypes and test them under real-world conditions. This can help identify any issues related to PCB thickness, such as mechanical strength or signal integrity problems.
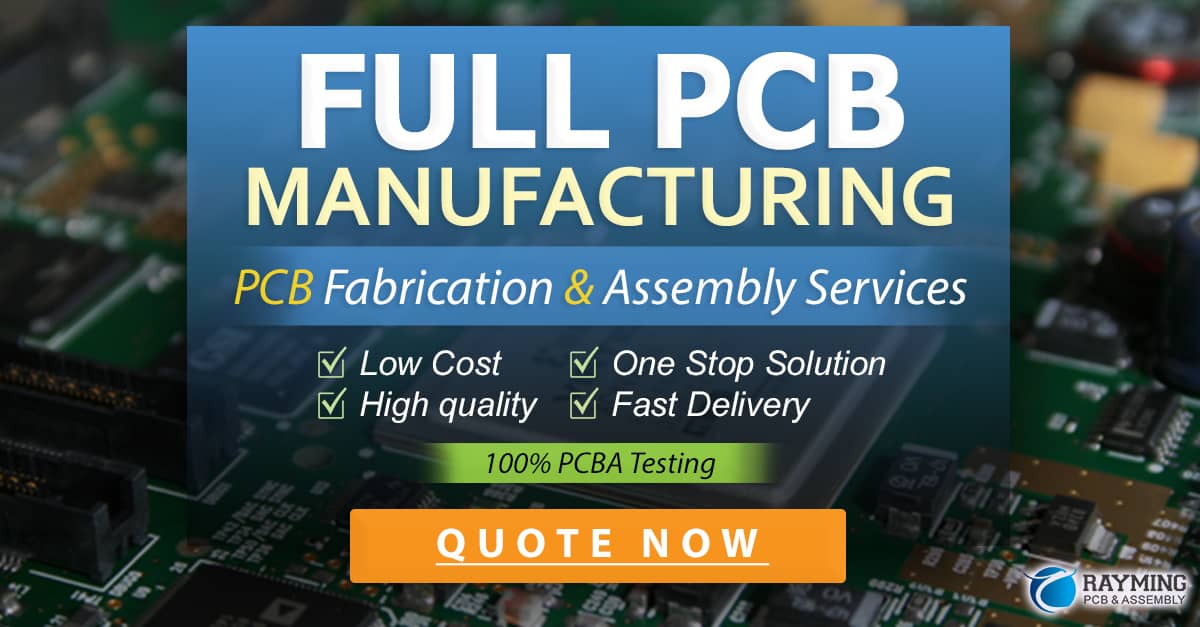
FAQ
1. What is the most common PCB thickness?
The most common PCB thickness is 1.6mm (62.99 mils). This thickness provides a good balance between mechanical strength, layer count support, and ease of manufacturing.
2. Can I use a thinner PCB to save space in my design?
Yes, thinner PCBs can be used to save space in compact designs. However, it is important to consider the limitations of thinner boards, such as reduced layer count and component size support. Always consult with your PCB manufacturer to ensure your design is feasible.
3. How does PCB thickness affect signal integrity?
PCB thickness can affect signal integrity in several ways. Thinner PCBs may be more susceptible to signal crosstalk and electromagnetic interference (EMI). Additionally, the dielectric thickness between layers can impact the Characteristic Impedance of transmission lines. Careful design and simulation can help mitigate these issues.
4. Are thicker PCBs always better?
Not necessarily. While thicker PCBs offer increased mechanical strength and support for higher layer counts, they may not be the optimal choice for every application. Thicker PCBs can increase the overall size and weight of the device, and may also have higher manufacturing costs.
5. Can I mix different thicknesses in the same PCB?
In some cases, it is possible to design a PCB with varying thicknesses in different regions of the board. This is known as a “stepped” or “cavity” PCB. However, this approach adds complexity to the manufacturing process and may increase costs. It is essential to work closely with your PCB manufacturer if considering a stepped PCB design.
Conclusion
PCB thickness is a critical specification that impacts the mechanical, electrical, and manufacturing aspects of a PCB design. By understanding the standard PCB thicknesses, factors that influence thickness selection, and design considerations, engineers can create PCBs that are optimized for their specific applications. Always collaborate with your PCB manufacturer to ensure your design is manufacturable and meets your performance requirements.
0 Comments