Introduction to PCB Surface Finish and Intermetallic Layers
Printed Circuit Boards (PCBs) are essential components in modern electronic devices, providing a platform for connecting and integrating various electronic components. The reliability and longevity of PCBs heavily depend on the protection of the copper layer, which is susceptible to oxidation and corrosion. To address this issue, PCB manufacturers employ surface finishes, which act as an intermetallic layer between the copper and the environment, enhancing the PCB’s durability and performance.
In this article, we will delve into the world of PCB surface finishes, focusing on the role of intermetallic layers in protecting the copper layer. We will explore the various types of surface finishes, their properties, and their applications in different industries. Additionally, we will discuss the manufacturing processes involved in applying these finishes and the factors to consider when selecting the appropriate finish for a specific project.
The Importance of Protecting the Copper Layer
Copper’s Vulnerability to Oxidation and Corrosion
Copper is the primary material used for creating conductive traces on PCBs due to its excellent electrical conductivity and relatively low cost. However, copper is prone to oxidation and corrosion when exposed to air and moisture. Over time, the formation of copper oxide on the surface can lead to reduced conductivity, compromising the performance and reliability of the PCB.
Moreover, corrosion can cause the copper traces to deteriorate, leading to open circuits and short circuits, which can ultimately result in device failure. To mitigate these issues, PCB manufacturers apply surface finishes that act as a barrier between the copper and the environment, protecting the copper layer from oxidation and corrosion.
The Role of Intermetallic Layers
An intermetallic layer is a thin layer of metal alloy that forms between the copper layer and the surface finish. This layer serves several crucial functions in protecting the copper layer and ensuring the overall reliability of the PCB:
-
Barrier against oxidation and corrosion: The intermetallic layer acts as a physical barrier, preventing oxygen and moisture from reaching the copper layer. This protection helps maintain the copper’s conductivity and structural integrity over time.
-
Improved solderability: Many surface finishes, such as Electroless Nickel Immersion Gold (ENIG) and Immersion Silver (IAg), enhance the solderability of the PCB. The intermetallic layer provides a surface that facilitates the formation of a strong and reliable solder joint during the assembly process.
-
Enhanced mechanical properties: The intermetallic layer can improve the mechanical properties of the PCB, such as hardness and wear resistance. This is particularly important for PCBs that are subjected to frequent handling or operate in harsh environments.
-
Compatibility with various components: Different surface finishes offer compatibility with a wide range of electronic components, such as through-hole and surface-mount devices. The intermetallic layer ensures a stable and reliable connection between the components and the PCB.
Common Types of PCB Surface Finishes
There are several types of PCB surface finishes available, each with its unique properties and advantages. The choice of surface finish depends on factors such as the application, environmental conditions, cost, and manufacturing requirements. Some of the most common PCB surface finishes include:
1. Electroless Nickel Immersion Gold (ENIG)
ENIG is a popular surface finish that consists of a layer of electroless nickel (typically 3-6 μm thick) followed by a thin layer of immersion gold (0.05-0.2 μm). The nickel layer acts as a barrier against copper diffusion, while the gold layer provides excellent solderability and corrosion resistance. ENIG is suitable for a wide range of applications, including high-frequency and high-reliability devices.
Advantages:
– Excellent solderability
– Good corrosion resistance
– Suitable for fine-pitch components
– Compatibility with lead-free soldering processes
Disadvantages:
– Higher cost compared to other finishes
– Potential for “black pad” syndrome due to improper plating processes
2. Immersion Silver (IAg)
IAg is a cost-effective surface finish that involves the deposition of a thin layer of silver (0.1-0.3 μm) directly onto the copper layer. Silver provides good solderability and conductivity, making it suitable for high-frequency applications. However, IAg is more prone to oxidation and tarnishing compared to ENIG.
Advantages:
– Cost-effective
– Good solderability
– Suitable for high-frequency applications
– Compatibility with lead-free soldering processes
Disadvantages:
– Limited shelf life due to silver tarnishing
– Not suitable for environments with high levels of sulfur or chlorine
3. Organic Solderability Preservative (OSP)
OSP is a thin, organic coating applied directly onto the copper layer. It acts as a temporary protective layer, preventing oxidation and maintaining solderability until the PCB is assembled. OSP is a cost-effective option for PCBs with a short shelf life and is commonly used in consumer electronics.
Advantages:
– Cost-effective
– Easy to apply and remove
– Suitable for fine-pitch components
– Compatibility with lead-free soldering processes
Disadvantages:
– Limited shelf life (typically 6-12 months)
– Not suitable for multiple reflow cycles
– Potential for inconsistent coating thickness
4. Hot Air Solder Leveling (HASL)
HASL is a traditional surface finish that involves dipping the PCB in molten solder and then using hot air to remove excess solder, creating a flat surface. HASL provides excellent solderability and is compatible with a wide range of components. However, it may not be suitable for fine-pitch components due to the inconsistent surface flatness.
Advantages:
– Excellent solderability
– Cost-effective
– Compatibility with a wide range of components
– Good shelf life
Disadvantages:
– Inconsistent surface flatness
– Not suitable for fine-pitch components
– Potential for thermal shock during the dipping process
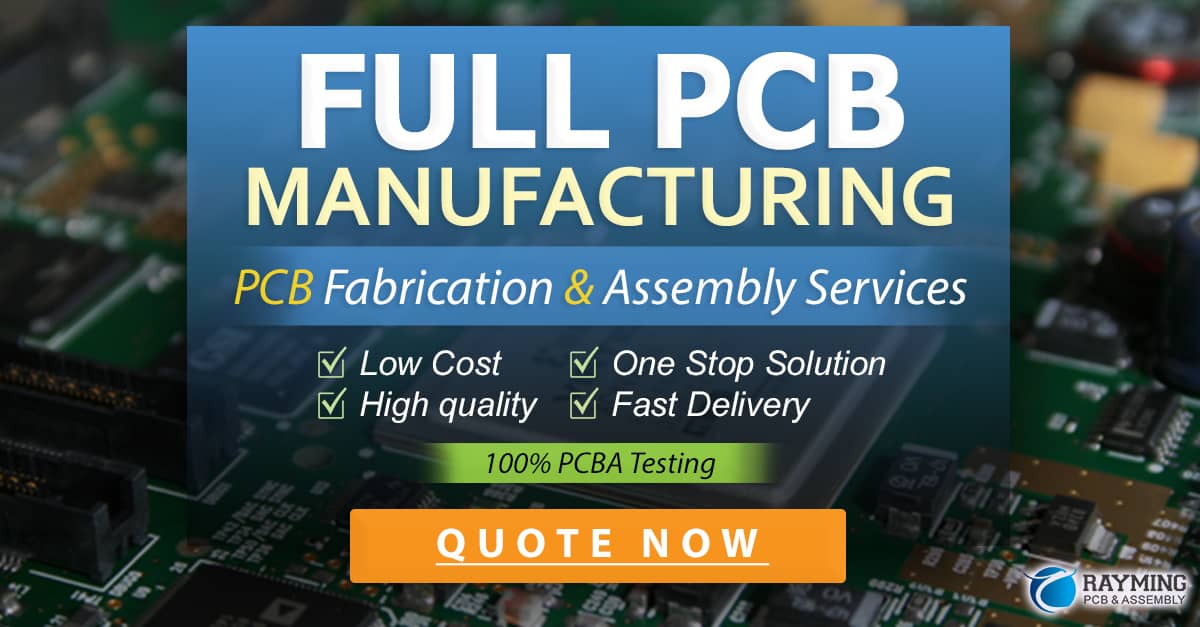
Comparison of PCB Surface Finishes
Surface Finish | Solderability | Shelf Life | Cost | Fine-Pitch Compatibility | Lead-Free Compatibility |
---|---|---|---|---|---|
ENIG | Excellent | Excellent | High | Yes | Yes |
IAg | Good | Limited | Low | Yes | Yes |
OSP | Good | Limited | Low | Yes | Yes |
HASL | Excellent | Good | Low | No | Yes |
Manufacturing Process of PCB Surface Finishes
The manufacturing process of PCB surface finishes involves several steps, which may vary depending on the specific finish being applied. The general steps include:
-
Cleaning: The PCB is thoroughly cleaned to remove any contaminants or oxides from the copper surface. This step is crucial for ensuring proper adhesion of the surface finish.
-
Micro-etching: A mild etching solution is used to remove a thin layer of copper, creating a uniform and clean surface for the subsequent plating processes.
-
Plating: The specific plating process depends on the chosen surface finish. For example, ENIG involves the electroless deposition of nickel followed by the immersion deposition of gold. IAg and OSP involve the direct immersion of the PCB in the respective plating solutions.
-
Rinsing and drying: After plating, the PCB is rinsed with deionized water to remove any residual plating solution and then dried using hot air or nitrogen.
-
Inspection: The finished PCB undergoes a visual inspection to ensure the surface finish is uniform and free from defects. Electrical tests may also be performed to verify the conductivity and solderability of the finish.
Factors to Consider When Choosing a PCB Surface Finish
When selecting a PCB surface finish for a specific project, several factors should be considered:
-
Application requirements: The choice of surface finish should be based on the specific requirements of the application, such as operating environment, expected lifespan, and performance demands.
-
Component compatibility: Different surface finishes offer varying levels of compatibility with different types of components. It is essential to choose a finish that is compatible with the components used in the PCB Assembly.
-
Cost: The cost of the surface finish can vary significantly, with ENIG being the most expensive and OSP being the least expensive. The choice of finish should balance the project’s budget with the required performance and reliability.
-
Manufacturing capabilities: The availability of the necessary equipment and expertise for applying a specific surface finish should be considered. Some finishes, such as ENIG, require specialized plating equipment and strict process control.
-
Environmental regulations: Certain surface finishes, such as HASL, may contain lead, which is restricted by environmental regulations such as RoHS. It is crucial to choose a finish that complies with the relevant regulations in the target market.
Conclusion
PCB surface finishes play a critical role in protecting the copper layer and ensuring the reliability and longevity of electronic devices. The intermetallic layer formed between the copper and the surface finish acts as a barrier against oxidation and corrosion, enhances solderability, and improves the mechanical properties of the PCB.
The choice of surface finish depends on various factors, including the application requirements, component compatibility, cost, manufacturing capabilities, and environmental regulations. By understanding the properties and advantages of different surface finishes, PCB designers and manufacturers can make informed decisions to optimize the performance and reliability of their products.
As technology advances and new materials emerge, the development of innovative PCB surface finishes will continue to shape the future of the electronics industry. By staying up-to-date with the latest advancements and best practices, manufacturers can ensure their PCBs meet the ever-increasing demands of modern electronic devices.
Frequently Asked Questions (FAQ)
-
What is the purpose of a PCB surface finish?
A PCB surface finish serves to protect the copper layer from oxidation and corrosion, enhance solderability, and improve the mechanical properties of the PCB. The surface finish acts as an intermetallic layer between the copper and the environment, ensuring the reliability and longevity of the electronic device. -
What are the most common types of PCB surface finishes?
The most common types of PCB surface finishes include Electroless Nickel Immersion Gold (ENIG), Immersion Silver (IAg), Organic Solderability Preservative (OSP), and Hot Air Solder Leveling (HASL). Each finish has its unique properties, advantages, and limitations, making them suitable for different applications and manufacturing requirements. -
How does the choice of surface finish affect the performance of a PCB?
The choice of surface finish can significantly impact the performance of a PCB. Different finishes offer varying levels of protection against oxidation and corrosion, solderability, and compatibility with different types of components. Selecting the appropriate finish based on the application requirements, environmental conditions, and manufacturing capabilities is crucial for ensuring the optimal performance and reliability of the PCB. -
What factors should be considered when choosing a PCB surface finish?
When choosing a PCB surface finish, several factors should be considered, including the application requirements, component compatibility, cost, manufacturing capabilities, and environmental regulations. It is essential to balance these factors to select a finish that meets the specific needs of the project while ensuring compliance with relevant standards and regulations. -
How does the manufacturing process differ for various PCB surface finishes?
The manufacturing process for PCB surface finishes involves several steps, including cleaning, micro-etching, plating, rinsing, drying, and inspection. However, the specific plating process varies depending on the chosen surface finish. For example, ENIG involves the electroless deposition of nickel followed by the immersion deposition of gold, while IAg and OSP involve the direct immersion of the PCB in the respective plating solutions. The availability of specialized equipment and expertise for applying a specific surface finish should be considered when making a selection.
0 Comments