What is PCB Soldering?
PCB soldering is the process of joining electronic components to a printed circuit board (PCB) using a molten metal alloy called solder. The solder forms a strong electrical and mechanical bond between the component leads and the PCB pads, ensuring a reliable connection and proper functioning of the electronic circuit.
Types of Soldering
There are two main types of soldering used in PCB Assembly:
- Through-hole soldering
- Surface-mount soldering
Through-hole Soldering
Through-hole soldering involves inserting component leads through pre-drilled holes in the PCB and soldering them to the pads on the opposite side of the board. This method is often used for larger components, such as connectors, switches, and some types of resistors and capacitors.
Surface-mount Soldering
Surface-mount soldering, also known as SMT (Surface-mount Technology) soldering, involves attaching components directly to the surface of the PCB without using through-holes. SMT components are smaller and have flat leads or terminals that are soldered to the PCB pads. This method allows for higher component density and is widely used in modern electronics manufacturing.
Tools and Materials for PCB Soldering
To achieve successful PCB soldering, you’ll need the right tools and materials. Here’s a list of essential items:
- Soldering iron
- Soldering iron tips
- Solder
- Flux
- Solder wick
- Tweezers
- Side cutters
- Magnifying glass or microscope
- Isopropyl alcohol and cleaning wipes
- ESD-safe mat and wrist strap
Soldering Iron
A soldering iron is the most essential tool for PCB soldering. It consists of a heated metal tip that melts the solder, allowing it to flow onto the component leads and PCB pads. When choosing a soldering iron, consider the following factors:
- Wattage: A higher wattage iron heats up faster and maintains a more stable temperature, but it may be overkill for smaller components. A 30-60 watt iron is suitable for most PCB soldering tasks.
- Temperature control: Adjustable temperature control allows you to set the optimal temperature for different types of solder and components.
- Tip size and shape: Select a tip size and shape that matches the size of the components and pads you’ll be soldering.
Solder
Solder is a metal alloy that melts at a relatively low temperature and forms a strong bond between the component leads and PCB pads. The most common types of solder used in electronics are:
- Lead-based solder: Typically a 60/40 tin-lead alloy, which melts at around 188°C (370°F). However, due to environmental and health concerns, lead-based solder is being phased out in many countries.
- Lead-free solder: Usually a tin-silver-copper (SAC) alloy, such as SAC305, which melts at a slightly higher temperature of around 217°C (423°F). Lead-free solder is becoming the standard in electronics manufacturing.
Solder is available in various diameters, with thinner diameters (e.g., 0.5mm or 0.8mm) being more suitable for smaller components and SMT soldering, while thicker diameters (e.g., 1.0mm or 1.2mm) are better for larger components and through-hole soldering.
Flux
Flux is a chemical compound that helps to remove oxides and impurities from the surfaces being soldered, promoting better solder flow and adhesion. There are two main types of flux:
- Rosin flux: A natural or synthetic resin-based flux that is available in various activator levels (mild, activated, and highly activated). Rosin flux is the most common type used in electronics soldering.
- Water-soluble flux: A more aggressive flux that requires cleaning with water after soldering. Water-soluble flux is less common in electronics soldering but may be used in some industrial applications.
Many solders come with a flux core, which eliminates the need for separate flux application in most cases. However, additional flux may be necessary for more challenging soldering tasks or when working with older or oxidized components and PCBs.
PCB Soldering Techniques
Now that you have the necessary tools and materials, let’s explore the various techniques used in PCB soldering.
Through-hole Soldering Technique
- Prepare the components by bending the leads at a 90-degree angle to fit through the PCB holes.
- Insert the component leads through the corresponding holes in the PCB.
- Bend the leads slightly outward on the opposite side of the PCB to hold the component in place.
- Apply a small amount of solder to the tip of the soldering iron.
- Touch the soldering iron tip to the PCB pad and the component lead simultaneously, allowing the solder to melt and flow around the joint.
- Remove the soldering iron and let the solder joint cool and solidify.
- Trim the excess component leads with side cutters.
Surface-mount Soldering Techniques
Hand Soldering SMT Components
- Apply a small amount of solder to one of the PCB pads.
- Using tweezers, place the SMT component onto the PCB, aligning its leads with the pads.
- While holding the component in place with the tweezers, touch the soldering iron tip to the lead and the solder on the pad, allowing the solder to melt and flow around the joint.
- Remove the soldering iron and let the solder joint cool and solidify.
- Repeat the process for the remaining leads.
Reflow Soldering SMT Components
- Apply solder paste (a mixture of solder particles and flux) to the PCB pads using a stencil or syringe.
- Place the SMT components onto the PCB, aligning their leads with the pads.
- Place the PCB in a reflow oven or use a hot air rework station to heat the board and components, following a specific temperature profile.
- The solder paste melts and flows around the joints, forming a strong bond as it cools and solidifies.
Inspection and Cleaning
After soldering, it’s essential to inspect the solder joints for quality and clean the PCB to remove any flux residue.
- Use a magnifying glass or microscope to visually inspect the solder joints for proper fillets, no bridges or cold joints.
- Clean the PCB with isopropyl alcohol and a lint-free wipe to remove flux residue, which can cause corrosion over time.
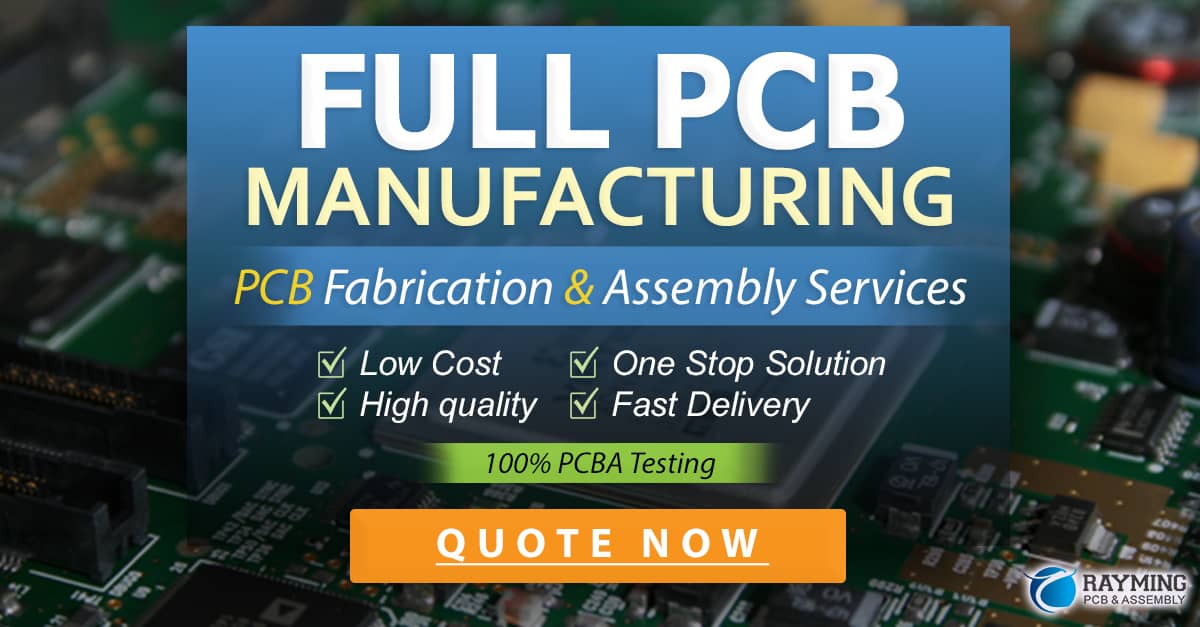
Common PCB Soldering Problems and Solutions
Even with the best techniques, problems can arise during PCB soldering. Here are some common issues and their solutions:
Cold Joints
A cold joint occurs when the solder fails to melt and flow properly, resulting in a weak and unreliable connection.
Causes:
– Insufficient heat
– Dirty or oxidized surfaces
– Inadequate flux
– Improper soldering technique
Solutions:
– Ensure the soldering iron is set to the correct temperature.
– Clean the component leads and PCB pads before soldering.
– Use fresh solder and additional flux if needed.
– Practice proper soldering techniques, ensuring the iron tip is in contact with both the lead and pad simultaneously.
Solder Bridges
A solder bridge is an unintended connection between two or more solder joints, caused by excess solder.
Causes:
– Applying too much solder
– Holding the soldering iron on the joint for too long
– Insufficient spacing between pads or leads
Solutions:
– Use solder wick to remove the excess solder and break the bridge.
– Apply the appropriate amount of solder and avoid overheating the joint.
– Ensure proper spacing between components and pads during PCB design and assembly.
Lifted Pads
A lifted pad occurs when the copper pad separates from the PCB substrate during soldering.
Causes:
– Excessive heat or prolonged contact with the soldering iron
– Improper handling or stress on the component leads
– Poor PCB design or manufacturing quality
Solutions:
– Avoid overheating the pads and limit soldering iron contact time.
– Handle components and PCBs gently, avoiding excessive force or bending.
– Ensure PCBs are designed and manufactured to industry standards, with proper pad size and adhesion.
Conclusion
PCB soldering is a valuable skill that requires practice, patience, and attention to detail. By understanding the basics of soldering, using the right tools and materials, and following proper techniques, you can achieve reliable and high-quality solder joints. Remember to work in a well-ventilated area, wear protective gear, and always prioritize safety when soldering.
Frequently Asked Questions (FAQ)
-
What is the difference between lead-based and lead-free solder?
Lead-based solder contains a 60/40 tin-lead alloy, while lead-free solder typically consists of a tin-silver-copper (SAC) alloy. Lead-free solder has a slightly higher melting point and requires more precise temperature control during soldering. -
How often should I replace my soldering iron tip?
Soldering iron tips should be replaced when they become worn, pitted, or excessively oxidized. The lifespan of a tip depends on factors such as usage frequency, soldering temperature, and proper maintenance. On average, a well-maintained tip can last several months to a year. -
Can I use the same soldering techniques for both through-hole and surface-mount components?
While the basic principles of soldering apply to both through-hole and surface-mount components, the techniques differ slightly. Through-hole soldering involves inserting component leads through holes in the PCB, while surface-mount soldering requires placing components directly onto the PCB pads. Surface-mount soldering often requires a steadier hand and more precise control due to the smaller size of components and pads. -
How can I prevent static damage to sensitive electronic components during soldering?
To prevent electrostatic discharge (ESD) damage, always use an ESD-safe mat and wear an ESD wrist strap when handling sensitive components. Additionally, avoid touching component leads or PCB pads directly, and use ESD-safe tweezers or vacuum picks when handling components. -
What should I do if I accidentally create a solder bridge between two pads?
If you create a solder bridge, use solder wick (also known as Desoldering Braid) to remove the excess solder. Place the solder wick over the bridge and apply the soldering iron tip to the wick, allowing the excess solder to be absorbed into the wick. Repeat the process until the bridge is removed, and then clean the area with isopropyl alcohol.
Soldering Type | Characteristics | Advantages | Disadvantages |
---|---|---|---|
Through-hole | – Components have long leads – Inserted through holes in PCB – Soldered on the opposite side of PCB |
– Stronger mechanical connection – Easier to solder for beginners – Suitable for larger components |
– Requires more PCB space – Slower assembly process – Limited component density |
Surface-mount | – Components have short leads or terminals – Placed directly onto PCB pads – Soldered on the same side of PCB |
– Higher component density – Faster assembly process – Smaller PCB size |
– Requires more precise soldering skills – Smaller components can be challenging to handle – More susceptible to thermal stress |
0 Comments