What is PCB Panelization?
PCB panelization is the process of arranging multiple PCB designs on a single panel for manufacturing purposes. This approach allows for the simultaneous production of several PCBs, reducing the overall fabrication time and costs. Panelization is particularly beneficial for high-volume production runs and helps maintain consistency across the manufactured boards.
Benefits of PCB Panelization
- Increased production efficiency
- Reduced manufacturing costs
- Improved consistency and uniformity
- Simplified handling and assembly
- Optimized material usage
Mouse Bites in PCB Panelization
Mouse bites, also known as break-off tabs or perforations, are small, strategically placed holes along the edges of individual PCBs on a panel. These holes are typically arranged in a series, forming a perforated line that allows for easy separation of the individual boards after the manufacturing process is complete.
Advantages of Mouse Bites
- Easy separation of individual PCBs
- Minimal material waste
- Suitable for various PCB shapes and sizes
- Cost-effective for low to medium-volume production
Disadvantages of Mouse Bites
- Visible marks on the edges of the separated PCBs
- Potential for damage during the separation process
- Limited strength of the tabs, which may break prematurely
- Not ideal for thick or high-density PCBs
V-Grooves in PCB Panelization
V-grooves are precision-cut channels along the edges of individual PCBs on a panel. These grooves are typically cut using a specialized tool, such as a V-shaped blade, and extend partially through the thickness of the PCB substrate. V-grooves allow for clean and smooth separation of the individual boards by applying gentle pressure along the grooves.
Advantages of V-Grooves
- Clean and smooth edges after separation
- Reduced risk of damage during the separation process
- Suitable for thick and high-density PCBs
- Improved structural integrity of the individual boards
- Aesthetically pleasing results
Disadvantages of V-Grooves
- Higher tooling costs compared to mouse bites
- Increased material waste due to the removal of the V-shaped channels
- Limited flexibility in PCB shapes and sizes
- Longer setup times for the cutting process
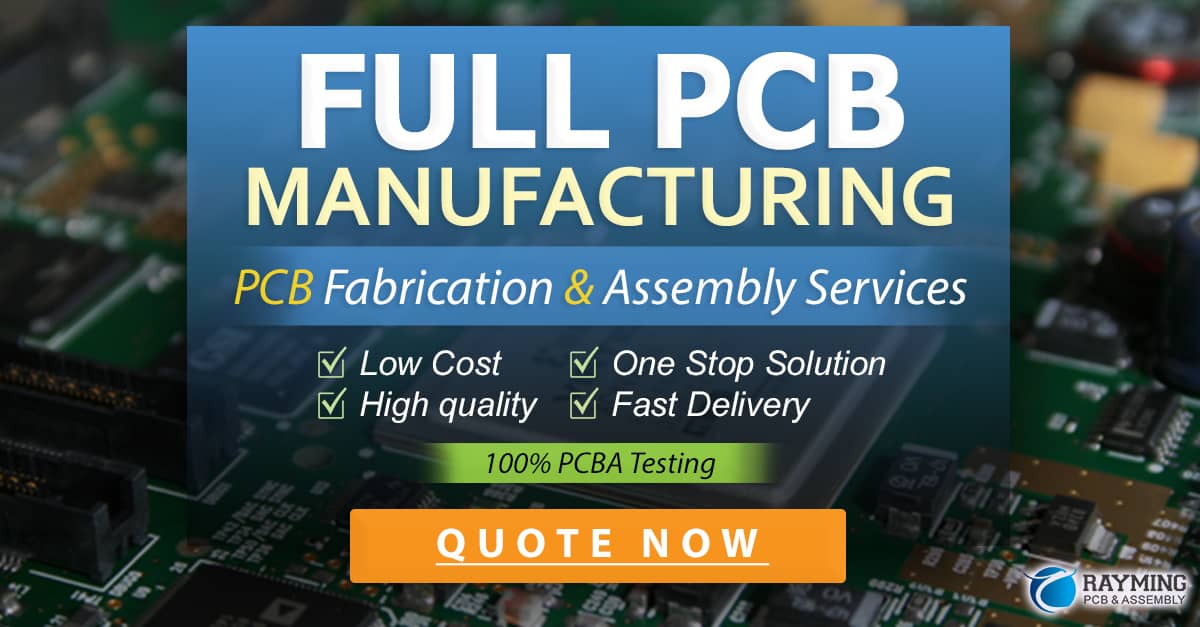
Comparison Table: Mouse Bites vs V-Grooves
Feature | Mouse Bites | V-Grooves |
---|---|---|
Separation Method | Perforations | Precision-cut channels |
Edge Quality | Visible marks | Clean and smooth |
Damage Risk | Higher | Lower |
Material Waste | Minimal | Increased |
Tooling Costs | Lower | Higher |
Suitability for Thick PCBs | Limited | Good |
Flexibility in PCB Shapes | High | Limited |
Choosing Between Mouse Bites and V-Grooves
When deciding between mouse bites and V-grooves for your PCB panelization needs, consider the following factors:
- Production volume and cost constraints
- PCB thickness and density
- Desired edge quality and aesthetics
- Shape and size requirements of the individual PCBs
- Available tooling and manufacturing capabilities
In general, mouse bites are more suitable for low to medium-volume production runs, while V-grooves are preferred for high-volume production and applications that require clean, smooth edges and improved structural integrity.
FAQ
1. Can mouse bites and V-grooves be used together on the same PCB panel?
Yes, it is possible to use a combination of mouse bites and V-grooves on the same PCB panel. This approach can be beneficial when dealing with complex PCB designs or when different separation methods are required for various sections of the panel.
2. How do I determine the appropriate size and spacing of mouse bites?
The size and spacing of mouse bites depend on several factors, including the PCB thickness, material properties, and the required strength of the tabs. Generally, the hole diameter ranges from 0.5mm to 1.5mm, with a spacing of 1mm to 3mm between holes. It is essential to consult with your PCB manufacturer to determine the optimal size and spacing for your specific design.
3. What is the typical depth of a V-groove?
The depth of a V-groove is typically one-third to one-half of the PCB substrate thickness. For example, a 1.6mm thick PCB would have a V-groove depth of approximately 0.5mm to 0.8mm. The exact depth may vary based on the specific requirements of the PCB design and the manufacturability constraints.
4. How does the choice of panelization method affect the assembly process?
The choice of panelization method can impact the assembly process in several ways. Mouse bites may leave visible marks on the edges of the PCBs, which can be a cosmetic concern in some applications. V-grooves, on the other hand, provide clean and smooth edges, which can be advantageous for certain assembly processes or end-use requirements. Additionally, the structural integrity of the individual PCBs can be affected by the panelization method, which may influence the handling and assembly procedures.
5. Are there any alternative panelization methods besides mouse bites and V-grooves?
Yes, there are other panelization methods available, such as scoring, routing, and snap-apart. Scoring involves creating shallow grooves on the surface of the PCB panel, while routing uses a milling tool to cut through the panel. Snap-apart panelization uses specially designed snap-off rails that allow for easy separation of the individual PCBs. Each method has its own advantages and disadvantages, and the choice depends on the specific requirements of the PCB design and manufacturing process.
Conclusion
PCB panelization is an essential aspect of PCB manufacturing, and the choice between mouse bites and V-grooves depends on various factors such as production volume, PCB thickness, desired edge quality, and cost constraints. Mouse bites offer a cost-effective solution for low to medium-volume production, while V-grooves provide clean, smooth edges and improved structural integrity for high-volume production and applications with specific aesthetic requirements.
By understanding the differences between these two panelization methods and considering the specific needs of your PCB design, you can make an informed decision that optimizes your manufacturing process and ensures the best possible results for your end product.
0 Comments