Understanding the Importance of PCB Material Selection
The choice of PCB materials directly impacts the performance, durability, and manufacturability of your electronic device. Different materials possess unique properties that affect signal integrity, thermal management, mechanical strength, and environmental resistance. By selecting the appropriate materials for your PCB, you can:
- Ensure reliable performance under various operating conditions
- Minimize signal loss and interference
- Enhance thermal dissipation and prevent overheating
- Improve mechanical stability and durability
- Optimize manufacturability and cost-effectiveness
Factors to Consider When Selecting PCB Materials
To make an informed decision when choosing PCB materials, consider the following key factors:
Electrical Properties
The electrical properties of PCB materials determine how well they can handle signal transmission and maintain signal integrity. The two primary electrical properties to consider are:
-
Dielectric Constant (Dk): The dielectric constant measures the material’s ability to store electrical energy. A lower Dk value is desirable for high-speed applications to minimize signal delay and maintain signal integrity.
-
Dissipation Factor (Df): The dissipation factor represents the amount of energy lost as heat when an electrical signal passes through the material. A lower Df value is preferred to minimize signal loss and maintain signal quality.
Thermal Properties
Thermal management is critical in PCB design to ensure reliable performance and prevent component failure due to overheating. The two main thermal properties to consider are:
-
Thermal Conductivity: This property measures the material’s ability to conduct heat away from heat-generating components. Higher thermal conductivity is desirable for better heat dissipation.
-
Glass Transition Temperature (Tg): The glass transition temperature is the point at which the material transitions from a rigid, glassy state to a softer, rubbery state. A higher Tg value is preferred for applications that require high-temperature stability.
Mechanical Properties
The mechanical properties of PCB materials determine their ability to withstand physical stress and maintain structural integrity. The key mechanical properties to consider include:
-
Flexural Strength: This property measures the material’s ability to resist bending and maintain its shape under stress. Higher flexural strength is desirable for applications that require mechanical stability.
-
Coefficient of Thermal Expansion (CTE): CTE represents the material’s dimensional change in response to temperature variations. A lower CTE value is preferred to minimize stress on components and prevent warping or delamination.
Environmental Resistance
PCBs may be exposed to various environmental conditions, such as humidity, chemical exposure, and extreme temperatures. Consider the following environmental factors when selecting PCB materials:
-
Moisture Absorption: Some materials absorb moisture from the environment, which can lead to dimensional changes and decreased performance. Lower moisture absorption is preferred for applications exposed to high humidity.
-
Chemical Resistance: If your PCB will be exposed to harsh chemicals, choose materials that can withstand these substances without degradation.
-
Temperature Range: Consider the expected operating temperature range of your device and select materials that can maintain their properties within that range.
Commonly Used PCB Materials
Now that we’ve discussed the factors to consider when selecting PCB materials, let’s explore some of the most commonly used materials in the industry.
FR-4
FR-4 is the most widely used PCB material, known for its balanced properties and cost-effectiveness. It is a composite material made of woven fiberglass cloth impregnated with an epoxy resin. FR-4 offers good electrical insulation, mechanical strength, and thermal stability, making it suitable for a wide range of applications.
Property | Value |
---|---|
Dielectric Constant (Dk) | 4.2 – 4.5 |
Dissipation Factor (Df) | 0.02 |
Thermal Conductivity | 0.3 W/mK |
Glass Transition Temperature (Tg) | 130°C – 140°C |
Flexural Strength | 480 MPa |
Coefficient of Thermal Expansion (CTE) | 14 ppm/°C |
High-Frequency Laminates
For high-speed and high-frequency applications, such as RF and microwave devices, specialized laminates are used to minimize signal loss and maintain signal integrity. These materials typically have lower dielectric constant and dissipation factor values compared to FR-4. Some common high-frequency laminates include:
-
Rogers RO4000 Series: These hydrocarbon ceramic laminates offer excellent high-frequency performance and low loss, making them suitable for applications up to 40 GHz.
-
PTFE (Polytetrafluoroethylene): PTFE-based laminates, such as Rogers RT/duroid, provide low dielectric constant and dissipation factor, as well as good thermal stability, making them ideal for microwave and millimeter-wave applications.
Material | Dielectric Constant (Dk) | Dissipation Factor (Df) | Thermal Conductivity | Glass Transition Temperature (Tg) |
---|---|---|---|---|
Rogers RO4350B | 3.48 | 0.0037 | 0.62 W/mK | >280°C |
Rogers RT/duroid 5880 | 2.20 | 0.0009 | 0.20 W/mK | N/A |
Metal Core PCBs
For applications that require enhanced thermal management, such as high-power LED lighting and automotive electronics, metal core PCBs (MCPCBs) are often used. MCPCBs feature a metal substrate, typically aluminum, which provides excellent thermal conductivity and helps dissipate heat more efficiently than traditional FR-4 laminates.
Property | Value |
---|---|
Thermal Conductivity | 1.0 – 3.0 W/mK |
Dielectric Constant (Dk) | 4.0 – 5.0 |
Dissipation Factor (Df) | 0.02 |
Coefficient of Thermal Expansion (CTE) | 12 – 18 ppm/°C |
Flexible PCBs
Flexible PCBs are used in applications that require conformity to non-planar surfaces or repeated flexing. These PCBs are made using flexible substrate materials, such as polyimide or polyester. Flexible PCBs offer the following advantages:
- Increased design freedom and space savings
- Improved reliability and shock resistance
- Reduced assembly time and costs
Material | Dielectric Constant (Dk) | Dissipation Factor (Df) | Tensile Strength | Elongation at Break |
---|---|---|---|---|
Polyimide | 3.5 | 0.002 | 231 MPa | 72% |
Polyester | 3.2 | 0.005 | 138 MPa | 150% |
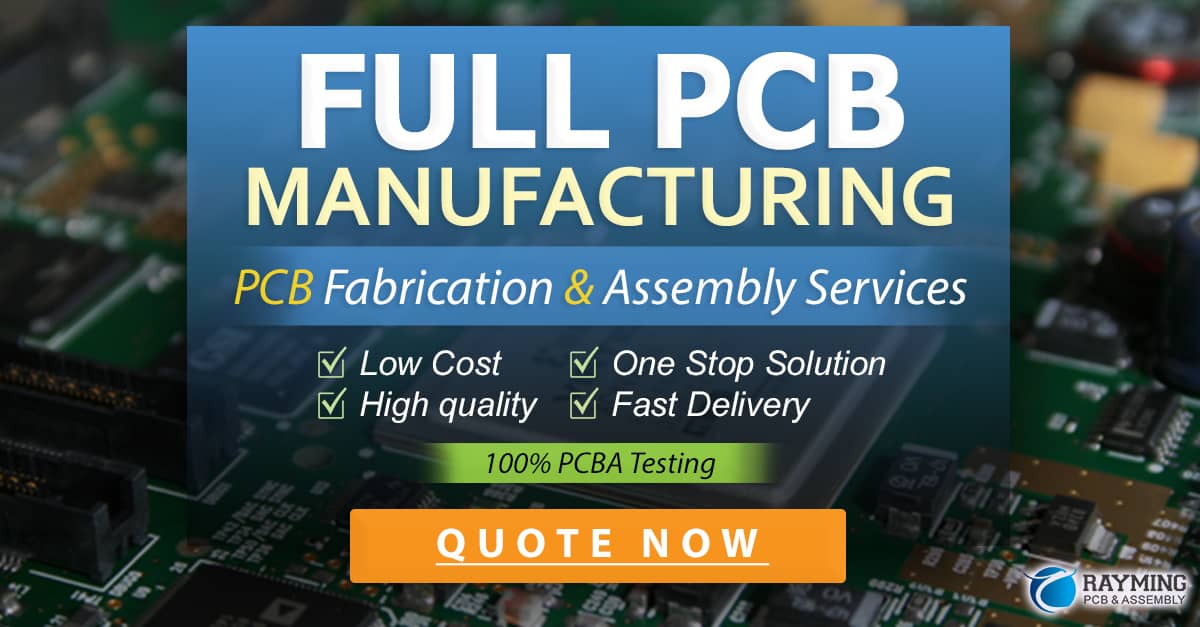
Frequently Asked Questions (FAQ)
- How do I choose between FR-4 and high-frequency laminates?
-
If your application involves high-speed or high-frequency signals, such as RF or microwave devices, high-frequency laminates like Rogers RO4000 series or PTFE-based materials are recommended for their lower dielectric constant and dissipation factor. For general-purpose applications, FR-4 is a cost-effective and suitable choice.
-
When should I consider using metal core PCBs?
-
Metal core PCBs are ideal for applications that generate significant heat, such as high-power LED lighting, automotive electronics, and power converters. The metal substrate, typically aluminum, provides excellent thermal conductivity and helps dissipate heat more efficiently, ensuring reliable performance and preventing component failure due to overheating.
-
Can I use flexible PCBs in all applications?
-
Flexible PCBs are best suited for applications that require conformity to non-planar surfaces, repeated flexing, or space-saving designs. However, they may not be the optimal choice for all applications due to their higher cost compared to rigid PCBs. Consider using flexible PCBs when the benefits of increased design freedom, improved reliability, and reduced assembly time outweigh the additional cost.
-
How do I select the right PCB material for high-temperature applications?
-
For high-temperature applications, choose PCB materials with a high glass transition temperature (Tg) to ensure stability and reliability at elevated temperatures. Materials like polyimide, which has a Tg of over 250°C, or high-temperature FR-4 variants with Tg values around 170°C, are suitable options. Additionally, consider the thermal conductivity of the material to facilitate heat dissipation.
-
What should I consider when selecting PCB materials for aerospace or military applications?
- Aerospace and military applications often require PCBs to withstand harsh environmental conditions, such as extreme temperatures, vibrations, and exposure to chemicals. Choose PCB materials that meet the specific requirements of your application, such as high-temperature resistance, low outgassing, and compliance with industry standards like IPC-6012 (Aerospace and Defense) or MIL-P-50884 (Military). Materials like polyimide, PTFE, and specialized FR-4 variants are commonly used in these demanding applications.
Conclusion
Selecting the right PCB materials is a critical step in designing and manufacturing reliable and high-performance electronic devices. By considering factors such as electrical properties, thermal management, mechanical stability, and environmental resistance, you can make an informed decision that meets the specific requirements of your application.
This guide has provided an overview of the most commonly used PCB materials, including FR-4, high-frequency laminates, metal core PCBs, and flexible PCBs, along with their key properties and suitable applications. By understanding the strengths and limitations of each material, you can optimize your PCB design for performance, reliability, and cost-effectiveness.
Remember to consult with your PCB manufacturer and material suppliers to discuss your specific project requirements and gain further insights into the best material choices for your application. With the right PCB materials and a well-designed layout, you can ensure the success of your electronic device and bring your innovative ideas to life.
0 Comments