Introduction to PCB Materials
Printed Circuit Boards (PCBs) are the backbone of modern electronics, providing a reliable and efficient means of interconnecting electronic components. The choice of PCB material plays a crucial role in determining the performance, reliability, and cost of the final product. In this comprehensive article, we will explore the various types of PCB materials, their properties, and their applications, helping you make an informed decision when selecting the right substrate for your circuit board.
Types of PCB Materials
FR-4
FR-4 is the most commonly used PCB material, consisting of a woven fiberglass fabric impregnated with an epoxy resin. It offers a good balance of mechanical, electrical, and thermal properties, making it suitable for a wide range of applications.
Advantages of FR-4
- Low cost
- Good mechanical strength
- Excellent electrical insulation
- Flame retardant
Disadvantages of FR-4
- Limited high-frequency performance
- Higher dielectric constant compared to other materials
- Prone to moisture absorption
Rogers
Rogers materials are high-performance substrates designed for demanding RF and microwave applications. They offer superior electrical properties, such as low dielectric constant and low loss tangent, enabling higher signal integrity and reduced signal loss.
Advantages of Rogers Materials
- Excellent high-frequency performance
- Low dielectric constant and loss tangent
- Stable electrical properties over a wide temperature range
- Low moisture absorption
Disadvantages of Rogers Materials
- Higher cost compared to FR-4
- More challenging to process and fabricate
- Limited availability and longer lead times
Polyimide
Polyimide is a high-temperature resistant polymer that offers excellent thermal stability and mechanical strength. It is commonly used in applications that require operation in harsh environments or exposure to high temperatures.
Advantages of Polyimide
- High temperature resistance (up to 400°C)
- Excellent mechanical strength and flexibility
- Good chemical resistance
- Low moisture absorption
Disadvantages of Polyimide
- Higher cost compared to FR-4
- More challenging to process and fabricate
- Limited high-frequency performance
PTFE (Teflon)
PTFE, also known as Teflon, is a low-loss dielectric material that offers excellent electrical properties, particularly at high frequencies. It is commonly used in RF and microwave applications that demand the lowest possible signal loss.
Advantages of PTFE
- Lowest dielectric constant and loss tangent among PCB materials
- Excellent high-frequency performance
- High temperature resistance
- Low moisture absorption
Disadvantages of PTFE
- High cost compared to other materials
- Difficult to process and fabricate
- Limited mechanical strength
Comparing PCB Material Properties
Property | FR-4 | Rogers | Polyimide | PTFE |
---|---|---|---|---|
Dielectric Constant | 4.5 | 2.2-10.2 | 3.5 | 2.1 |
Loss Tangent | 0.02 | 0.0009-0.003 | 0.002 | 0.0002 |
Thermal Conductivity (W/mK) | 0.3 | 0.6-1.0 | 0.2 | 0.2 |
Tg (°C) | 130-140 | 280-315 | 360-410 | 327 |
Moisture Absorption (%) | 0.1-0.2 | 0.02-0.1 | 0.4-0.8 | <0.01 |
Relative Cost | Low | High | Medium | High |
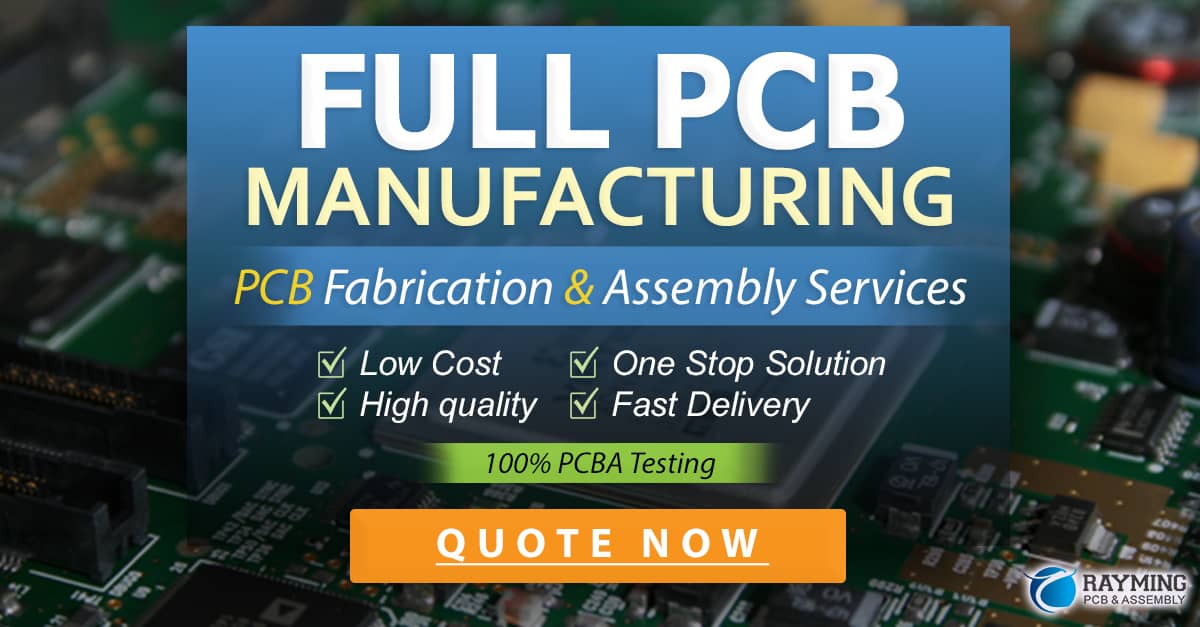
Selecting the Right PCB Material
When choosing a PCB material for your circuit board, consider the following factors:
-
Frequency of operation: For high-frequency applications, such as RF and microwave circuits, low-loss materials like Rogers or PTFE are preferred.
-
Environmental conditions: If your PCB will be exposed to high temperatures or harsh environments, consider using polyimide or other high-temperature resistant materials.
-
Cost: FR-4 is the most cost-effective option for general-purpose applications, while specialized materials like Rogers or PTFE come at a higher price point.
-
Manufacturing considerations: Some materials, such as polyimide and PTFE, may require specialized processing techniques and equipment, which can impact the manufacturing cost and lead time.
-
Mechanical requirements: Consider the required mechanical strength, flexibility, and dimensional stability of your PCB when selecting a material.
PCB Material and Signal Integrity
The choice of PCB material can significantly impact signal integrity, particularly at high frequencies. The two key properties that affect signal integrity are the dielectric constant (Dk) and the loss tangent (Df).
Dielectric Constant (Dk)
The dielectric constant is a measure of a material’s ability to store electrical energy. A lower Dk value means that the material has a lower capacitance, which results in faster signal propagation and reduced signal distortion. Materials with low Dk values, such as Rogers and PTFE, are preferred for high-frequency applications.
Loss Tangent (Df)
The loss tangent is a measure of a material’s ability to dissipate electrical energy as heat. A lower Df value indicates that the material has lower dielectric losses, resulting in reduced signal attenuation and improved signal integrity. Materials with low Df values, such as Rogers and PTFE, are ideal for applications that require minimal signal loss.
PCB Material and Thermal Management
Thermal management is another critical aspect to consider when selecting a PCB material. The thermal conductivity of the material determines its ability to dissipate heat generated by electronic components.
Thermal Conductivity
Thermal conductivity is a measure of a material’s ability to conduct heat. Materials with higher thermal conductivity, such as Rogers, can efficiently transfer heat away from components, preventing overheating and improving the overall reliability of the PCB.
Coefficient of Thermal Expansion (CTE)
The coefficient of thermal expansion (CTE) is a measure of how much a material expands or contracts with changes in temperature. A mismatch in CTE between the PCB material and the components can lead to mechanical stress and potential reliability issues. It is essential to choose a material with a CTE that closely matches that of the components to minimize thermal stress.
Frequently Asked Questions (FAQ)
-
What is the most common PCB material?
FR-4 is the most common PCB material, used in a wide range of general-purpose applications. -
Which PCB material is best for high-frequency applications?
Rogers materials and PTFE (Teflon) are the best choices for high-frequency applications due to their low dielectric constant and loss tangent. -
Can I use FR-4 for high-temperature applications?
While FR-4 can withstand temperatures up to 130-140°C, it is not recommended for high-temperature applications. Polyimide is a better choice for applications that require operation at higher temperatures. -
What is the most cost-effective PCB material?
FR-4 is the most cost-effective PCB material, offering a good balance of properties at a lower price point compared to specialized materials like Rogers or PTFE. -
How does the choice of PCB material affect signal integrity?
The dielectric constant (Dk) and loss tangent (Df) of the PCB material have a significant impact on signal integrity. Materials with lower Dk and Df values, such as Rogers and PTFE, offer better signal integrity and are preferred for high-frequency applications.
Conclusion
Selecting the right PCB material is crucial for ensuring the performance, reliability, and cost-effectiveness of your circuit board. By understanding the properties and characteristics of different materials, such as FR-4, Rogers, polyimide, and PTFE, you can make an informed decision based on your specific application requirements.
Consider factors such as frequency of operation, environmental conditions, cost, manufacturing considerations, and mechanical requirements when choosing a PCB material. Additionally, pay attention to the material’s impact on signal integrity and thermal management to optimize the performance and reliability of your PCB.
By carefully evaluating your needs and selecting the appropriate PCB material, you can create a high-quality circuit board that meets your performance and reliability goals while staying within your budget constraints.
0 Comments