Introduction to PCBs in Renewable Energy
Printed circuit boards (PCBs) play a critical role in the rapidly growing renewable energy industry. PCBs are found in a wide range of renewable energy devices and systems, including:
– Solar panels and solar power inverters
– Wind turbine control systems
– Hydroelectric generators
– Geothermal heat pumps
– Biofuel processing equipment
PCBs help enable the efficient generation, conversion, storage, and distribution of clean, sustainable energy from renewable sources. As the demand for renewable energy continues to grow globally to combat climate change, the PCB manufacturing industry is rising to meet the unique challenges and requirements of renewable energy applications.
Importance of High-Quality PCBs for Renewables
Renewable energy systems often operate in harsh environments and demanding conditions. Solar panels and wind turbines, for example, are exposed to extreme temperatures, humidity, vibration, and weather events. Hydroelectric and geothermal facilities deal with high pressure and corrosive conditions.
To reliably function in these challenging operating environments over a 20+ year lifespan, renewable energy systems require high-quality, durable PCBs. Any failures or defects in the PCBs can cripple renewable energy generation and lead to costly repairs.
High-quality PCBs for renewable energy applications are characterized by:
– Robust, durable construction using high-grade materials
– Precise manufacturing to tight tolerances
– Thorough quality control and testing
– Enhanced protection against moisture, corrosion, and environmental contaminants
– Optimal thermal management to dissipate heat
– Excellent reliability and longevity
By investing in high-quality PCBs from experienced manufacturers, renewable energy OEMs can ensure their products meet strict performance, reliability, and durability requirements. Quality PCBs help renewable energy systems achieve optimal generating efficiency, minimal downtime, and a long operating life—all of which improve the cost-competitiveness and ROI of renewable energy.
PCB Design Considerations for Renewable Energy
Designing PCBs for renewable energy applications requires careful consideration of the unique technical requirements and operating conditions. Some key PCB design factors for renewables include:
Ruggedized Materials
PCBs in renewables must withstand extreme temperatures, humidity, and other environmental stresses. Therefore, it’s important to choose PCB substrate materials and coatings that can handle these exposures.
Polyimide is a popular high-temperature PCB material that offers excellent thermal resistance up to 260°C. For humid environments, PCBs with enhanced moisture barriers or encapsulation are required.
Efficient Layout
The PCB layout and stack-up should be optimized for the specific renewable application. Proper grounding, power and signal routing, and component placement are critical for optimal performance, signal integrity, and thermal management. Experienced PCB layout engineers can ensure an efficient, reliable design.
Optimal Thermal Management
Renewable energy PCBs often deal with high voltages and currents which generate a lot of heat. Overheating can degrade performance, reliability, and lifespan. Therefore, renewable energy PCBs require optimal thermal management.
Techniques such as using wide, heavy copper traces, installing thermal vias and heat sinks, and selecting high-temperature PCB materials can help dissipate heat. Thermal analysis during the design stage can validate the PCB’s thermal performance.
Reliable Connectors
Renewable energy PCBs interface with various other systems, so reliable connectors are critical. High-quality, industrial-grade connectors ensure secure connections that can withstand vibration, shock, and environmental exposure over time. Gold-plated contacts provide the best corrosion resistance and reliability.
EMC Compliance
Renewable energy systems can be a source of electromagnetic interference (EMI) which can disrupt other electronic devices. PCBs play an important role in ensuring electromagnetic compatibility (EMC).
Proper PCB layout techniques such as partitioning, shielding, filtering, and grounding can minimize EMI. PCBs should be designed to meet relevant EMC standards such as FCC Part 15 and CISPR 22.
Testing and Validation
Comprehensive testing and validation during PCB design and manufacturing are crucial for renewable energy applications. This includes:
– Design rule checks (DRC) and layout vs. schematic (LVS) verification
– Signal integrity analysis
– Thermal simulation
– Accelerated life testing
– Environmental testing (temperature, humidity, vibration, etc.)
– Functional testing
Thorough testing helps identify and correct any design issues before mass production, ensuring the PCBs will perform reliably in the field.
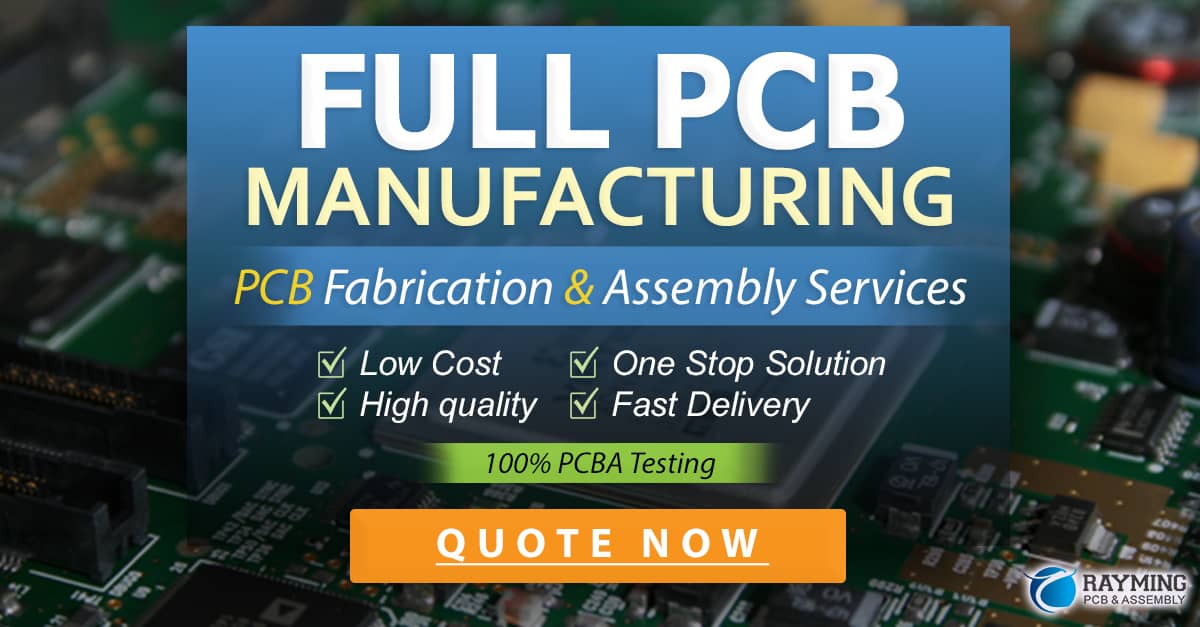
PCB Manufacturing Capabilities for Renewable Energy
Renewable energy PCBs require advanced manufacturing capabilities to meet their demanding specifications and quality requirements. Some key PCB fabrication capabilities for renewables include:
HDI and Microvias
Many renewable energy PCBs have high component density and complex layouts, necessitating HDI (high density interconnect) designs with microvias. Advanced HDI PCB fabrication with precise laser drilling ensures reliable interconnects on dense boards.
Heavy Copper
High-power renewable energy PCBs often require heavy copper traces (up to 20 oz/ft2 or more) to handle large currents. PCB manufacturers must have experience with heavy copper plating and etching processes.
Precision Tolerances
Renewable energy PCBs require tighter fabrication tolerances to ensure optimal performance and reliability. This includes precise trace widths and spacing, hole diameters, and layer registration.
Capability | Typical Tolerance |
---|---|
Trace width/spacing | ± 0.0005 in |
Hole diameter | ± 0.002 in |
Layer registration | ± 0.002 in |
Specialty Materials
PCB fabricators must be able to source and process a variety of specialty materials for renewable energy applications. This includes polyimide, PTFE, ceramic/LTCC substrates, metal-backed PCBs, and thermally conductive dielectrics.
Conformal Coating
Conformal coating is often required on renewable energy PCBs for added protection against moisture, corrosion, and environmental contamination. Parylene, acrylic, urethane, and silicone coatings are common options. The coating must be uniformly applied without impacting component functionality.
Electrical Test
100% electrical test (ET) is critical for renewable energy PCBs to verify the continuity and isolation of all traces, vias, and pads. Flying probe testers or bed-of-nails fixturing provide precise electrical testing and help catch any manufacturing defects.
By partnering with PCB manufacturers who specialize in these advanced capabilities, renewable energy OEMs can ensure they are getting the highest quality, most reliable PCBs for their critical applications.
Choosing the Right PCB Manufacturer for Renewable Energy
Selecting the right PCB manufacturing partner is essential for the success of renewable energy products. Some key factors to consider when choosing a PCB fabricator for renewables include:
Experience with Renewable Energy Applications
It’s important to partner with a PCB manufacturer who has proven experience serving the renewable energy industry. They will understand the unique technical requirements and quality standards for renewable energy PCBs.
Look for a fabricator with a track record of successful renewable energy projects, as evidenced by case studies, customer references, and industry certifications.
Engineering Support
Renewable energy PCBs often require close collaboration between the OEM’s design team and the PCB manufacturer’s engineers. The fabricator should offer experienced PCB design engineers who can provide DFM (design for manufacturability) feedback, recommend materials and stack-ups, and assist with testing and validation.
Accessible, responsive engineering support helps optimize the PCB design, avoid delays, and ensure a smooth transition to manufacturing.
Quality Management System
A robust quality management system (QMS) is essential for ensuring consistent, reliable PCB production. The fabricator should have a well-documented QMS that includes:
– Strict process controls and statistical monitoring
– Thorough inspection and testing procedures
– Continuous improvement initiatives
– Regular audits and management review
Ideally, the QMS should be certified to industry standards such as ISO 9001, AS9100, or IATF 16949. These certifications demonstrate the fabricator’s commitment to quality and ability to meet the rigorous requirements of the renewable energy industry.
U.S. Manufacturing
Using a domestic PCB fabricator offers several advantages for renewable energy OEMs, including:
– Faster lead times and shorter supply chains
– Easier communication and collaboration
– Greater IP protection and security
– Compliance with federal purchasing requirements (e.g. Buy American Act)
U.S.-based PCB manufacturing helps support the domestic renewable energy industry and ensures a secure, resilient supply chain.
Cost-Effectiveness
While high quality and reliability are paramount for renewable energy PCBs, cost is still an important consideration. The PCB fabricator should offer competitive pricing while still meeting all technical and quality requirements.
Lean manufacturing initiatives, automation, and continuous improvement help reduce costs without sacrificing quality. The fabricator should also provide cost reduction suggestions during DFM review to optimize the PCB design for manufacturing efficiency and affordability.
By selecting a PCB manufacturing partner with these capabilities and attributes, renewable energy OEMs can ensure a strong, successful collaboration that advances the growth of clean energy technologies.
FAQ
What are the most common types of PCBs used in renewable energy?
The most common types of PCBs used in renewable energy applications include:
1. High-temperature PCBs (e.g. polyimide)
2. Heavy copper PCBs
3. Metal-backed PCBs (e.g. aluminum or copper core)
4. HDI/microvia PCBs
5. Flexible and rigid-flex PCBs
How can PCB design optimize the performance of renewable energy systems?
PCB design plays a critical role in optimizing renewable energy system performance through:
– Efficient power and signal routing
– Optimal thermal management (e.g. heavy copper, thermal vias, heat sinks)
– Robust protection against environmental stresses (e.g. conformal coating, ruggedized materials)
– High-reliability design (e.g. redundant traces, reliable connectors)
– EMI/EMC control (e.g. shielding, grounding, filtering)
What environmental tests should PCBs undergo for renewable energy applications?
Some key environmental tests for renewable energy PCBs include:
– Thermal cycling and shock
– Temperature/humidity aging
– Highly accelerated life test (HALT)
– Vibration and mechanical shock
– Salt spray and corrosion testing
– Insulation resistance testing
These tests help validate the PCB’s durability and reliability in harsh operating environments.
How does using a domestic PCB fabricator benefit renewable energy OEMs?
Using a U.S.-based PCB fabricator offers several benefits for renewable energy OEMs, such as:
– Faster lead times and delivery
– Easier communication and engineering collaboration
– Greater IP security and trade secret protection
– Compliance with federal purchasing regulations
– Supporting the growth of the domestic renewable energy industry
Domestic sourcing strengthens the renewable energy supply chain and accelerates new product development.
What should renewable energy OEMs look for when selecting a PCB manufacturing partner?
When choosing a PCB fabricator for renewable energy applications, OEMs should look for:
1. Experience with renewable energy applications
2. Strong engineering and technical support
3. Advanced manufacturing capabilities (e.g. HDI, heavy copper, specialty materials)
4. Robust quality management system
5. U.S.-based manufacturing
6. Cost-effectiveness and DFM support
Partnering with the right PCB fabricator is essential for ensuring the performance, reliability, and affordability of renewable energy systems.
Conclusion
PCBs are a critical component of renewable energy systems, enabling efficient and reliable power generation from clean, sustainable sources. By understanding the unique requirements and design considerations for renewable energy PCBs, OEMs can develop high-performance products that accelerate the global transition to renewables.
Partnering with an experienced, high-quality PCB manufacturer is essential for the success of renewable energy products. The right fabricator will provide the advanced capabilities, engineering support, and quality assurance necessary to ensure reliable, cost-effective PCBs.
As the demand for renewable energy continues to grow, PCB manufacturers will play an increasingly important role in supporting the development and deployment of innovative clean energy technologies. By working closely together, renewable energy OEMs and PCB fabricators can create a sustainable future powered by efficient, affordable, and environmentally friendly energy solutions.
0 Comments