Introduction to PCB Manufacturing in China and the US
Printed Circuit Board (PCB) manufacturing is a critical industry that underpins modern electronics. Both China and the United States are major players in the global PCB market, but there are significant differences between the two countries in terms of manufacturing capabilities, costs, quality, and other factors.
In this article, we will provide an in-depth comparison of PCB manufacturing in China and the US. We’ll examine the strengths and weaknesses of each country’s PCB industry, explore the factors that influence manufacturing decisions, and provide insights to help electronics companies make informed choices about where to source their PCBs.
Overview of the Global PCB Market
The global PCB market was valued at approximately $60 billion in 2020 and is projected to reach over $75 billion by 2027, growing at a compound annual growth rate (CAGR) of around 3% during the forecast period (2020-2027).
China is currently the world’s largest PCB manufacturing country, accounting for over 50% of global production. The US is the second-largest PCB producer, with a market share of approximately 5%.
Country | Global PCB Market Share |
---|---|
China | >50% |
US | ~5% |
Others | <45% |
Key Factors Influencing PCB Manufacturing Decisions
When deciding where to manufacture PCBs, electronics companies must consider several key factors:
- Manufacturing capabilities and technology
- Production costs
- Quality and reliability
- Lead times and flexibility
- Intellectual property protection
- Geopolitical factors and trade policies
Let’s examine each of these factors in more detail.
Manufacturing Capabilities and Technology
China has a well-established PCB manufacturing industry with a wide range of capabilities, from basic single-layer boards to complex multi-layer and high-density interconnect (HDI) PCBs. Chinese manufacturers have invested heavily in advanced equipment and technologies to meet the growing demand for sophisticated PCBs used in smartphones, computers, automotive electronics, and other applications.
US PCB Manufacturers also have advanced capabilities but tend to focus more on specialty products such as military/aerospace-grade PCBs, high-frequency PCBs for 5G telecommunications, and other niche applications. Some US companies have shifted their focus to higher-value PCB design, engineering, and Prototyping Services while outsourcing volume production to lower-cost countries like China.
Production Costs
One of the main reasons China has become the world’s PCB manufacturing hub is its lower production costs compared to the US and other developed countries. This is due to several factors:
- Lower labor costs: Average wages for factory workers are much lower in China than in the US.
- Economies of scale: China’s large-scale PCB factories can produce higher volumes at lower unit costs.
- Supply chain efficiencies: China has a well-developed supply chain for PCB raw materials and components, which helps reduce overall production costs.
However, it’s important to note that Chinese labor costs have been rising in recent years, narrowing the gap with US labor costs. Additionally, the US government has introduced tariffs on some Chinese-made PCBs, which can offset some of the cost advantages of manufacturing in China.
Cost Factor | China | US |
---|---|---|
Average factory labor cost | $3-5/hour | $15-25/hour |
PCB tariffs (as of 2021) | 25% | N/A |
Quality and Reliability
Both China and the US have PCB manufacturers capable of producing high-quality boards that meet international standards such as IPC. However, there can be significant variability in quality among Chinese manufacturers, especially at the lower end of the market. Some Chinese PCB factories may cut corners on materials or processes to reduce costs, which can compromise reliability.
US PCB manufacturers generally have a reputation for consistent quality, strict quality control procedures, and adherence to industry standards. They are often the preferred choice for mission-critical applications where reliability is paramount, such as in aerospace, defense, and medical devices.
Lead Times and Flexibility
Chinese PCB manufacturers typically offer shorter lead times than their US counterparts due to their larger production capacity and streamlined operations. Many Chinese factories can produce PCBs in 1-2 weeks, compared to 3-4 weeks or longer for US manufacturers.
However, US manufacturers may offer greater flexibility for small-volume orders, custom designs, and quick-turn prototyping. They are also less likely to impose minimum order quantities (MOQs) than Chinese factories, which can be advantageous for low-volume production runs.
Intellectual Property Protection
Intellectual property (IP) protection is a significant concern for many electronics companies when outsourcing PCB manufacturing. China has historically had a poor record of IP protection, with instances of design theft, counterfeiting, and reverse engineering.
US PCB manufacturers generally offer better IP protection due to stronger legal protections and enforcement in the United States. They are more likely to have secure data handling practices and strict confidentiality agreements in place.
However, it’s worth noting that some Chinese PCB manufacturers have improved their IP protection measures in recent years to attract foreign customers. It’s important to thoroughly vet any potential manufacturing partner and have strong legal agreements in place regardless of location.
Geopolitical Factors and Trade Policies
Geopolitical factors and trade policies can also influence PCB manufacturing decisions. The US-China trade war and tariffs have disrupted supply chains and increased costs for some electronics companies that rely on Chinese PCB manufacturers.
Additionally, concerns about national security and the potential for supply chain disruptions have led some US companies to consider reshoring PCB manufacturing or diversifying their supplier base to reduce dependence on China.
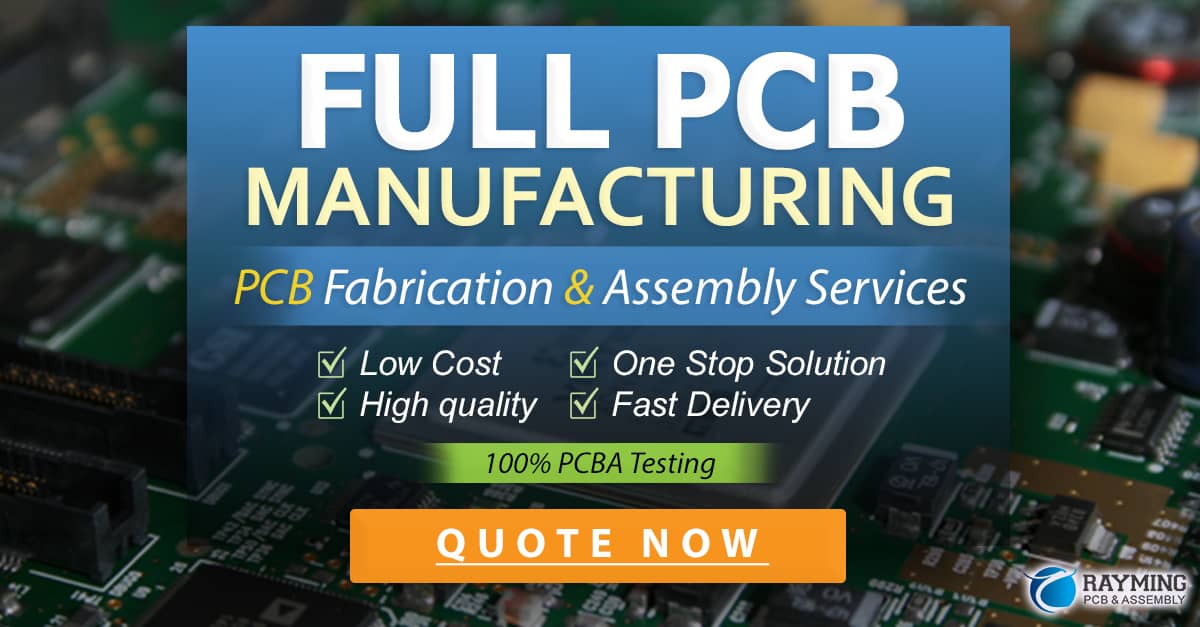
Choosing the Right PCB Manufacturing Partner
Given the complex factors involved, there is no one-size-fits-all answer to whether China or the US is the best choice for PCB manufacturing. The decision depends on each company’s specific needs, priorities, and risk tolerance.
Here are some general guidelines to consider:
- For cost-sensitive, high-volume production, China may be the most attractive option if quality and reliability can be assured through proper vetting and quality control measures.
- For mission-critical applications, specialized technologies, or sensitive IP, US manufacturers may be the safer choice despite potentially higher costs.
- A balanced approach could involve using Chinese manufacturers for lower-cost, standard PCBs while relying on US manufacturers for critical components or prototypes.
Regardless of location, it’s crucial to thoroughly research and vet potential PCB manufacturing partners. Look for manufacturers with a proven track record of quality, reliability, and customer service. Request references, audits, and certifications to ensure they meet your standards.
FAQ
- Are Chinese PCBs always lower quality than US-made PCBs?
-
Not necessarily. While there can be variability in quality among Chinese manufacturers, many are capable of producing high-quality PCBs that meet international standards. The key is to carefully vet potential partners and have strong quality control measures in place.
-
Will tariffs on Chinese PCBs make them more expensive than US-made PCBs?
-
Tariffs have increased the cost of some Chinese-made PCBs, but in many cases, they may still be less expensive than US-made equivalents due to China’s lower labor costs and economies of scale. The specific impact of tariffs depends on the type of PCB and the manufacturing process involved.
-
Is it risky to share sensitive design files with Chinese PCB manufacturers?
-
There are risks associated with sharing IP with any overseas manufacturer, but these can be mitigated through careful partner selection, strong legal agreements, and secure data handling practices. Some Chinese manufacturers have improved their IP protection measures in recent years, but it’s still important to be cautious and protect your company’s interests.
-
How can I ensure consistent quality when working with a Chinese PCB manufacturer?
-
Establish clear quality standards and expectations upfront, and verify that the manufacturer has the necessary certifications and quality control processes in place. Conduct regular audits and inspections, and consider using a third-party quality control service to monitor production. Building a long-term relationship with a trusted manufacturing partner can also help ensure consistent quality over time.
-
Should I consider reshoring PCB manufacturing to the US?
- The decision to reshore depends on your company’s specific needs and priorities. Reshoring can offer advantages such as better IP protection, greater control over quality, and reduced supply chain risks. However, it may also involve higher costs and longer lead times. A thorough cost-benefit analysis and risk assessment can help guide your decision.
Conclusion
The choice between China and the US for PCB manufacturing is a complex one that depends on a variety of factors, including cost, quality, technology, IP protection, and geopolitical considerations. While China offers significant cost advantages and large-scale production capabilities, the US provides benefits in terms of quality, reliability, and IP protection for sensitive applications.
Ultimately, the key to successful PCB manufacturing in either location is careful partner selection, strong quality control measures, and a clear understanding of your company’s specific needs and risk tolerance. By weighing the factors discussed in this article and conducting thorough due diligence, you can make an informed decision that balances cost, quality, and risk to meet your business objectives.
As the global electronics industry continues to evolve, it’s important to stay informed about trends and developments in PCB manufacturing and adapt your strategies accordingly. Whether you choose to work with a Chinese or US manufacturer, or pursue a diversified sourcing approach, the goal should be to build strong, reliable partnerships that can support your company’s long-term success in a competitive and ever-changing market.
0 Comments