Introduction to PCB Industrial Solutions
Printed Circuit Board Industrial Solutions, or PCB-IS for short, refer to the wide range of PCB technologies, processes, materials, and services tailored specifically for industrial applications. Unlike consumer electronics where cost is often the primary driver, industrial PCB solutions prioritize reliability, durability, and performance to withstand harsh operating conditions over extended periods of time.
Industrial PCBs are found in a diverse array of applications including:
- Factory automation and control systems
- Power generation and distribution equipment
- Heavy machinery and vehicles
- Oil and gas exploration and processing
- Medical devices and equipment
- Aerospace and defense systems
- Telecommunications infrastructure
The demanding nature of these industrial environments necessitates PCBs that can tolerate extreme temperatures, vibrations, shocks, moisture, chemicals, and electromagnetic interference (EMI). As a result, industrial PCB design and manufacturing involves specialized materials, enhanced construction techniques, and rigorous testing and quality control measures to ensure the end product meets the required specifications and regulations.
Key Considerations for Industrial PCB Design
Reliability and Durability
The foremost requirement for industrial PCBs is reliable and durable operation, often in mission-critical applications where failure can result in costly downtime, equipment damage, or even safety hazards. Industrial PCB designs must factor in the expected environmental conditions and stresses, such as:
- Wide temperature range (e.g., -40°C to +85°C or higher)
- Thermal cycling and shock
- Vibration and mechanical shock
- Humidity and moisture exposure
- Dust, debris, and chemical contaminants
- Electromagnetic interference (EMI) and radio frequency interference (RFI)
To withstand these challenges, industrial PCBs employ robust design practices, such as:
- Thicker copper traces and dielectric layers for improved mechanical strength
- Larger component pads and holes to reduce stress and improve solderability
- Sufficient spacing between traces to minimize crosstalk and EMI
- Proper grounding and shielding techniques to mitigate electromagnetic interference
- Conformal coating or encapsulation to protect against moisture and contaminants
Material Selection
The choice of PCB materials plays a crucial role in ensuring reliability and performance in industrial environments. Key considerations include:
-
Glass transition temperature (Tg): The temperature at which the PCB substrate softens and deforms. Industrial PCBs often require high Tg materials like polyimide or epoxy resins to withstand elevated temperatures.
-
Coefficient of thermal expansion (CTE): The rate at which the PCB material expands with temperature. Mismatches in CTE between the PCB and components can lead to thermal stresses and failures. Industrial PCBs use materials with closely matched CTEs to minimize this risk.
-
Dielectric constant (Dk) and dissipation factor (Df): These properties affect the PCB’s electrical performance, particularly at high frequencies. Low Dk and Df materials are preferred for high-speed designs to minimize signal distortion and loss.
-
Flame retardancy: Industrial PCBs may be subject to flammability requirements per standards like UL94. Flame-retardant materials such as FR-4 or halogen-free alternatives are commonly used.
Some popular materials for industrial PCBs include:
Material | Tg (°C) | CTE (ppm/°C) | Dk | Df | Flammability |
---|---|---|---|---|---|
FR-4 | 130-140 | 14-16 | 4.5 | 0.02 | UL94 V-0 |
Polyimide | 250-400 | 12-16 | 3.5 | 0.002 | UL94 V-0 |
Rogers 4003 | >280 | 11-14 | 3.38 | 0.0027 | UL94 V-0 |
PTFE | 327 | 88 | 2.1 | 0.0002 | Non-burning |
Component Selection and Placement
Proper component selection and placement are essential for industrial PCB reliability. Key factors to consider include:
- Temperature rating: Components must be rated for the expected operating temperature range, including any additional derating for reliability.
- Package type: Robust packages like through-hole, QFN, or BGA are preferred over fragile leadless packages for better mechanical strength.
- Placement and orientation: Components should be placed to minimize thermal and mechanical stresses, with proper orientation for optimal heat dissipation and stress distribution.
- Stress relief: Techniques like underfill, conformal coating, or strain relief can help mitigate stresses on components.
Industrial PCB Manufacturing Processes
Multilayer PCB Fabrication
Most industrial PCBs are multilayer designs to accommodate higher component density and complex interconnects. The fabrication process involves the following key steps:
- Inner layer printing: Circuit patterns are printed onto individual copper-clad laminates using photolithography.
- Layer lamination: The inner layers are stacked and laminated together with prepreg (pre-impregnated) bonding sheets under heat and pressure.
- Drilling: Holes are drilled through the laminated board for vias and component mounting.
- Plating: The drilled holes are plated with copper to establish electrical connections between layers.
- Outer layer printing: Circuit patterns are printed onto the outer layers using photolithography.
- Etching: Unwanted copper is etched away, leaving the final circuit patterns.
- Solder mask and silkscreen: A protective solder mask is applied, followed by silkscreen legends for component identification.
- Surface finish: A final surface finish, such as HASL, ENIG, or OSP, is applied to protect the exposed copper and enhance solderability.
Specialized Manufacturing Techniques
Industrial PCBs often employ specialized manufacturing techniques to enhance reliability and performance, such as:
- Thicker copper: PCBs with copper weights of 2 oz or more provide better current carrying capacity and mechanical strength.
- Blind and buried vias: These vias connect internal layers without going through the entire board thickness, enabling higher density designs.
- Controlled impedance: Precise control of trace widths and spacing to maintain consistent impedance for high-speed signals.
- Metal core: Using a metal substrate (e.g., aluminum) for better heat dissipation in high-power applications.
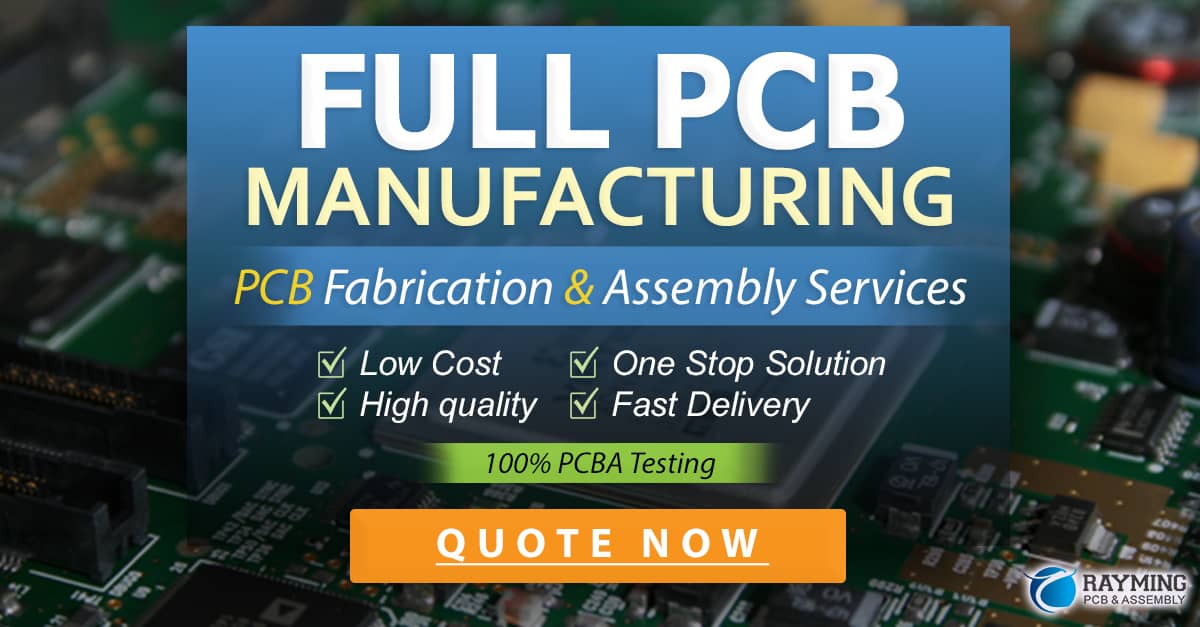
Quality Control and Testing
In-Process Inspection
Industrial PCB manufacturing involves rigorous in-process inspection to catch defects early and ensure consistent quality. Common inspection methods include:
- Automated optical inspection (AOI): Uses cameras and image processing to detect surface defects like shorts, opens, or missing components.
- Automated X-ray inspection (AXI): Uses X-rays to detect internal defects like voids, cracks, or misaligned components.
- Electrical testing: Verifies the electrical continuity and isolation of the PCB using flying probe or bed-of-nails testers.
Environmental Testing
Industrial PCBs undergo extensive environmental testing to validate their reliability and durability under the expected operating conditions. Common tests include:
- Temperature cycling: Subjects the PCB to alternating high and low temperature extremes to simulate thermal stresses.
- Thermal shock: Rapidly transfers the PCB between hot and cold environments to induce thermal shock.
- Vibration and shock: Applies mechanical vibrations or shocks to the PCB to simulate real-world stresses.
- Humidity and moisture resistance: Exposes the PCB to high humidity or moisture to evaluate its resistance to corrosion and degradation.
- Salt spray: Tests the PCB’s resistance to corrosion in a salt-laden atmosphere.
- EMC/EMI: Measures the PCB’s electromagnetic compatibility and immunity to interference.
Standards and Certifications
Industrial PCBs are often subject to various standards and certifications to ensure they meet the required specifications and regulations for their intended application. Some common standards include:
- IPC: The Association Connecting Electronics Industries publishes a wide range of standards for PCB design, fabrication, and assembly, such as IPC-6012 for rigid PCBs and IPC-A-610 for acceptability.
- UL: Underwriters Laboratories provides safety certifications for PCBs, such as UL94 for flammability and UL746E for electrical performance.
- MIL-PRF-31032: The US Department of Defense standard for PCB performance and reliability in military applications.
- NEMA: The National Electrical Manufacturers Association publishes standards for industrial control systems, such as NEMA ICS 61131 for programmable controllers.
- ISO: The International Organization for Standardization publishes quality management standards, such as ISO 9001, which are often required for industrial PCB suppliers.
Future Trends in Industrial PCB Solutions
Advanced Materials
Ongoing research and development in PCB materials aim to address the ever-increasing demands of industrial applications, such as:
- High-temperature materials: New resin systems and laminates that can withstand temperatures above 200°C for use in automotive, aerospace, and oil and gas industries.
- Low-loss materials: Materials with lower dielectric constant and dissipation factor for high-speed digital and RF applications.
- Embedded components: PCBs with passive components (e.g., resistors, capacitors) embedded within the substrate to save space and improve performance.
3D Printing
Additive manufacturing, or 3D printing, is emerging as a potential game-changer for industrial PCB fabrication. Benefits include:
- Rapid prototyping: 3D printing enables faster and cheaper prototyping of complex PCB designs.
- Customization: 3D-printed PCBs can be easily customized for specific applications or form factors.
- Embedded electronics: 3D printing allows the integration of electronic components directly into the PCB structure.
Industry 4.0 and Smart Manufacturing
The rise of Industry 4.0 and smart manufacturing is driving the need for more intelligent and connected industrial PCBs. Key trends include:
- Internet of Things (IoT): PCBs with integrated sensors, wireless connectivity, and edge computing capabilities for IoT applications.
- Predictive maintenance: PCBs with built-in monitoring and diagnostic features to enable predictive maintenance of industrial equipment.
- Cybersecurity: Enhanced security measures for industrial PCBs to protect against cyber threats in connected systems.
FAQ
Q1: What is the difference between industrial and consumer PCBs?
A1: Industrial PCBs are designed for reliability and durability in harsh environments, while consumer PCBs prioritize cost and performance. Industrial PCBs use robust materials, construction techniques, and testing methods to ensure they can withstand extreme temperatures, vibrations, shocks, and other stresses over extended periods of time.
Q2: What are some common materials used in industrial PCBs?
A2: Common materials for industrial PCBs include FR-4, polyimide, Rogers laminates, and PTFE. The choice of material depends on the specific requirements for temperature resistance, dielectric properties, and flammability. High-temperature materials like polyimide are often used in demanding applications.
Q3: Why is component selection important for industrial PCBs?
A3: Proper component selection is crucial for industrial PCB reliability. Components must be rated for the expected operating temperature range and harsh environmental conditions. Robust package types like through-hole or BGA are preferred for better mechanical strength, and placement and orientation should be optimized for heat dissipation and stress distribution.
Q4: What types of testing do industrial PCBs undergo?
A4: Industrial PCBs undergo extensive testing to validate their reliability and performance. Common tests include temperature cycling, thermal shock, vibration and shock, humidity and moisture resistance, salt spray, and EMC/EMI testing. In-process inspection methods like AOI and AXI are also used to catch defects early in the manufacturing process.
Q5: What are some future trends in industrial PCB solutions?
A5: Future trends in industrial PCB solutions include advanced materials like high-temperature and low-loss laminates, 3D printing for rapid prototyping and customization, and the integration of IoT, predictive maintenance, and cybersecurity features for Industry 4.0 and smart manufacturing applications. As industrial systems become more complex and connected, PCBs will need to evolve to meet these new challenges.
Conclusion
PCB Industrial Solutions (PCB-IS) encompass a wide range of technologies, processes, materials, and services tailored for the demanding requirements of industrial applications. From factory automation to aerospace, industrial PCBs must deliver reliable and durable performance in harsh environments over extended periods of time.
Designing and manufacturing industrial PCBs involves careful consideration of factors such as reliability, material selection, component placement, and specialized fabrication techniques. Rigorous testing and quality control measures are employed to ensure the end product meets the required specifications and regulations.
As industrial systems continue to evolve towards Industry 4.0 and smart manufacturing, PCBs will need to integrate advanced features like IoT connectivity, predictive maintenance, and cybersecurity. Ongoing research in materials, 3D printing, and other technologies will drive further innovations in industrial PCB solutions.
By understanding the unique challenges and requirements of industrial applications, PCB designers and manufacturers can develop robust and reliable solutions that meet the needs of this demanding market. With the right expertise and technologies, PCB Industrial Solutions will continue to play a critical role in enabling the next generation of industrial systems and equipment.
0 Comments